Les réacteurs discontinus, bien que polyvalents et largement utilisés en laboratoire et dans le cadre d'une production à petite échelle, présentent plusieurs inconvénients importants.Il s'agit notamment des coûts de main-d'œuvre élevés, des difficultés liées à l'augmentation de la production, des longs temps morts pendant les opérations, de l'instrumentation limitée, de la qualité irrégulière des produits et des risques de sécurité tels que les explosions.En outre, les réacteurs discontinus sont généralement mieux adaptés aux réactions homogènes, ce qui limite leur applicabilité aux processus industriels plus complexes.Ces inconvénients les rendent moins efficaces et moins rentables que les réacteurs à flux continu, qui offrent des rendements plus élevés, un meilleur contrôle et des coûts de fabrication plus faibles.
Explication des principaux points :
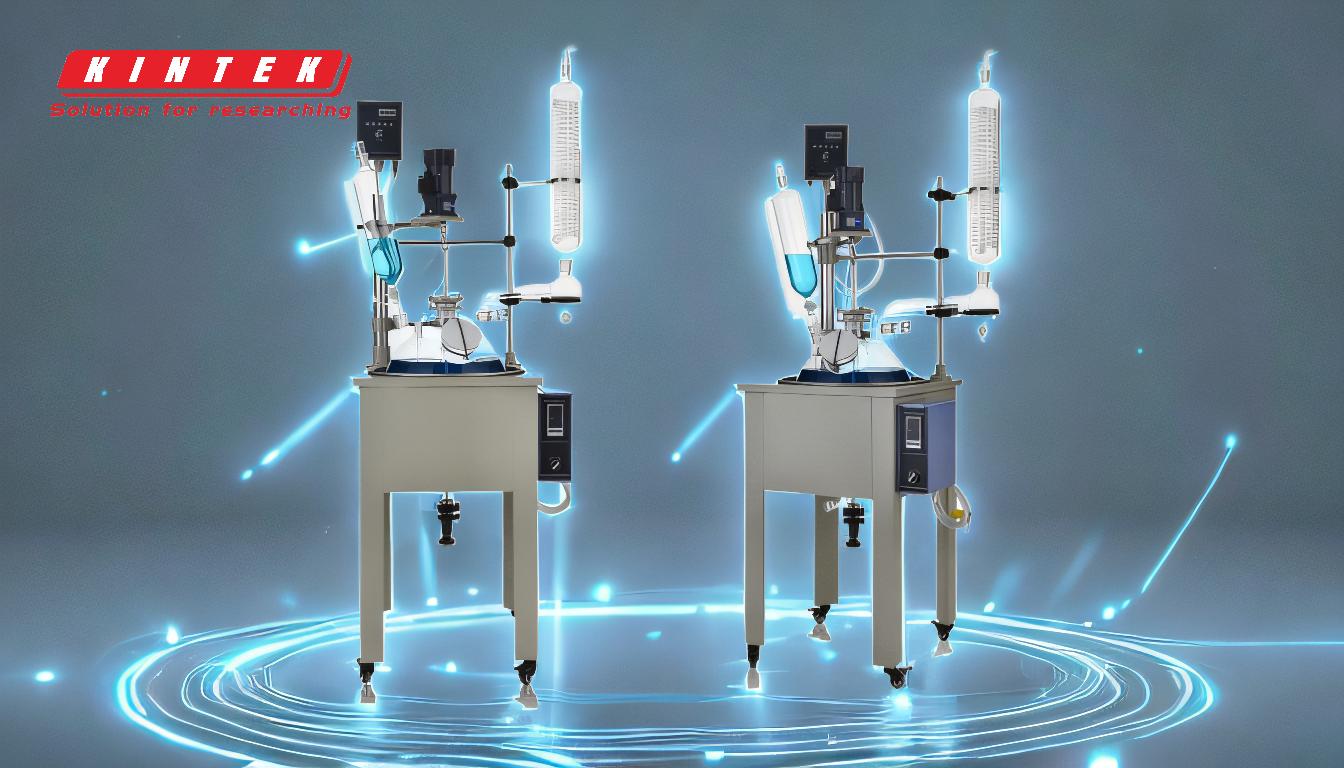
-
Coûts de main-d'œuvre élevés par unité de production
- Les réacteurs discontinus nécessitent une intervention manuelle importante pour des tâches telles que le chargement, le déchargement et le nettoyage.Cela augmente les coûts de main-d'œuvre, surtout par rapport aux réacteurs à flux continu, qui sont plus automatisés et nécessitent moins de surveillance humaine.
- La nature répétitive des procédés discontinus est également source d'inefficacité, car les travailleurs doivent effectuer les mêmes tâches plusieurs fois pour chaque lot.
-
Difficulté à maintenir une production à grande échelle
- Les réacteurs discontinus ne sont pas bien adaptés à la production industrielle à grande échelle en raison de leur capacité limitée et de la nécessité de cycles de démarrage et d'arrêt fréquents.
- L'augmentation de la production avec des réacteurs discontinus implique souvent l'utilisation de plusieurs réacteurs, ce qui augmente les coûts et la complexité.Les réacteurs à flux continu, en revanche, sont conçus pour la production de gros volumes et peuvent fonctionner en continu sans interruption.
-
Longs temps morts pendant le chargement et le déchargement
- Dans les réacteurs discontinus, une grande partie du cycle de production est consacrée à des tâches non productives, telles que le chargement des réactifs, le chauffage ou le refroidissement du système et le déchargement des produits.
- Ces temps morts réduisent l'efficacité globale et le débit, ce qui rend les réacteurs discontinus moins adaptés aux processus de production sensibles au temps ou à forte demande.
-
Manque d'instrumentation et de contrôle
- Les réacteurs discontinus sont souvent dépourvus d'instruments et de systèmes de contrôle avancés, ce qui rend difficile la surveillance et l'optimisation des conditions de réaction en temps réel.
- Cela peut entraîner des incohérences dans la qualité du produit et réduire la fiabilité du processus, car les opérateurs ont moins de contrôle sur les variables telles que la température, la pression et le mélange.
-
Qualité et homogénéité médiocres des produits
- En raison de l'absence de contrôle précis et de la variabilité inhérente entre les lots, les réacteurs discontinus produisent souvent des produits de qualité irrégulière.
- Cette situation est particulièrement problématique dans les industries où l'uniformité des produits est essentielle, comme les produits pharmaceutiques ou les produits chimiques spécialisés.
-
Risques d'explosion pendant la vidange
- Les réacteurs discontinus peuvent présenter des risques pour la sécurité, en particulier pendant la phase de vidange, lorsque les réactifs résiduels ou les sous-produits peuvent réagir de manière imprévisible.
- La conception des réacteurs discontinus n'est pas optimisée pour faire face à de puissantes explosions, ce qui les rend moins sûrs que les réacteurs à flux continu, qui sont conçus pour gérer plus efficacement les conditions de haute pression et de haute température.
-
Applicabilité limitée aux réactions homogènes
- Les réacteurs discontinus conviennent principalement aux réactions homogènes, dans lesquelles les réactifs et les produits se trouvent dans une seule phase (liquide ou gazeuse, par exemple).
- Ils sont moins efficaces pour les réactions hétérogènes, qui impliquent plusieurs phases (par exemple, solide-liquide ou gaz-liquide), ce qui limite encore leur polyvalence dans les applications industrielles.
-
Coûts de fabrication et d'exploitation plus élevés
- Si les réacteurs discontinus permettent d'économiser sur les coûts de fabrication initiaux en raison de leur conception plus simple, leurs inefficacités opérationnelles et leurs besoins en main-d'œuvre plus importants se traduisent souvent par des coûts plus élevés à long terme.
- Les réacteurs à flux continu, malgré leur investissement initial plus élevé, offrent des coûts de fabrication plus faibles et des ratios valeur/résultat (VTO) plus élevés au fil du temps.
-
Incapacité à atteindre des conditions d'équilibre
- Les réacteurs discontinus n'atteignent pas un état stable, ce qui signifie que les conditions de réaction (par exemple, la température, la pression et la concentration) changent au fil du temps.
- Il est donc difficile de contrôler et d'optimiser la réaction, ce qui entraîne des inefficacités potentielles et des rendements de produits sous-optimaux.
-
Conception et technologie dépassées
- Les réacteurs discontinus n'ont connu que des changements minimes dans leur conception au fil du temps, s'appuyant sur des méthodes traditionnelles qui ne bénéficient pas des avancées observées dans les réacteurs à flux continu.
- Cela limite leur capacité à rivaliser avec les technologies modernes des réacteurs, qui offrent de meilleures performances, des rendements plus élevés et des caractéristiques de sécurité améliorées.
En résumé, si les réacteurs discontinus sont simples et polyvalents, leurs inconvénients - coûts de main-d'œuvre élevés, faible évolutivité, risques pour la sécurité et qualité inégale des produits - les rendent moins adaptés aux applications industrielles modernes.Les réacteurs à flux continu, avec leur technologie avancée et leur efficacité supérieure, sont de plus en plus privilégiés pour les processus de production à grande échelle et à forte demande.
Tableau récapitulatif :
Inconvénient | Description |
---|---|
Coûts de main-d'œuvre élevés | Nécessite une intervention manuelle importante, ce qui augmente les coûts d'exploitation. |
Faible évolutivité | Pas idéal pour la production à grande échelle en raison des cycles fréquents de démarrage et d'arrêt. |
Longs temps morts | Les tâches non productives telles que la charge et la décharge réduisent l'efficacité. |
Instrumentation limitée | L'absence de surveillance et de contrôle en temps réel entraîne des résultats incohérents. |
Qualité inégale des produits | La variabilité entre les lots affecte l'uniformité du produit. |
Risques pour la sécurité | Risques d'explosion lors de la vidange en raison de réactions imprévisibles. |
Limité aux réactions homogènes | Moins efficace pour les réactions complexes et multiphases. |
Coûts d'exploitation plus élevés | Les inefficacités à long terme l'emportent sur les économies initiales. |
Pas de conditions stables | Les conditions de réaction changent au fil du temps, ce qui rend l'optimisation difficile. |
Technologie dépassée | Ne bénéficie pas des avancées des réacteurs à flux continu modernes. |
Découvrez comment les réacteurs à flux continu peuvent résoudre vos problèmes de production. contactez-nous dès aujourd'hui !