Le rendement de pulvérisation est un paramètre critique dans les processus de pulvérisation, représentant le nombre moyen d'atomes éjectés d'un matériau cible par ion incident. Il est influencé par des facteurs tels que l'énergie de l'ion, les masses de l'ion et de l'atome cible, l'angle d'incidence de l'ion et l'énergie de liaison de la surface du matériau cible. Pour les matériaux cristallins, l'orientation des axes cristallins par rapport à la surface joue également un rôle. Il est essentiel de comprendre le rendement de la pulvérisation pour optimiser les processus de dépôt par pulvérisation, car il a un impact direct sur les taux de dépôt et la qualité des films. Cette explication se penche sur les facteurs clés qui affectent le rendement de la pulvérisation et leurs implications.
Explication des points clés :
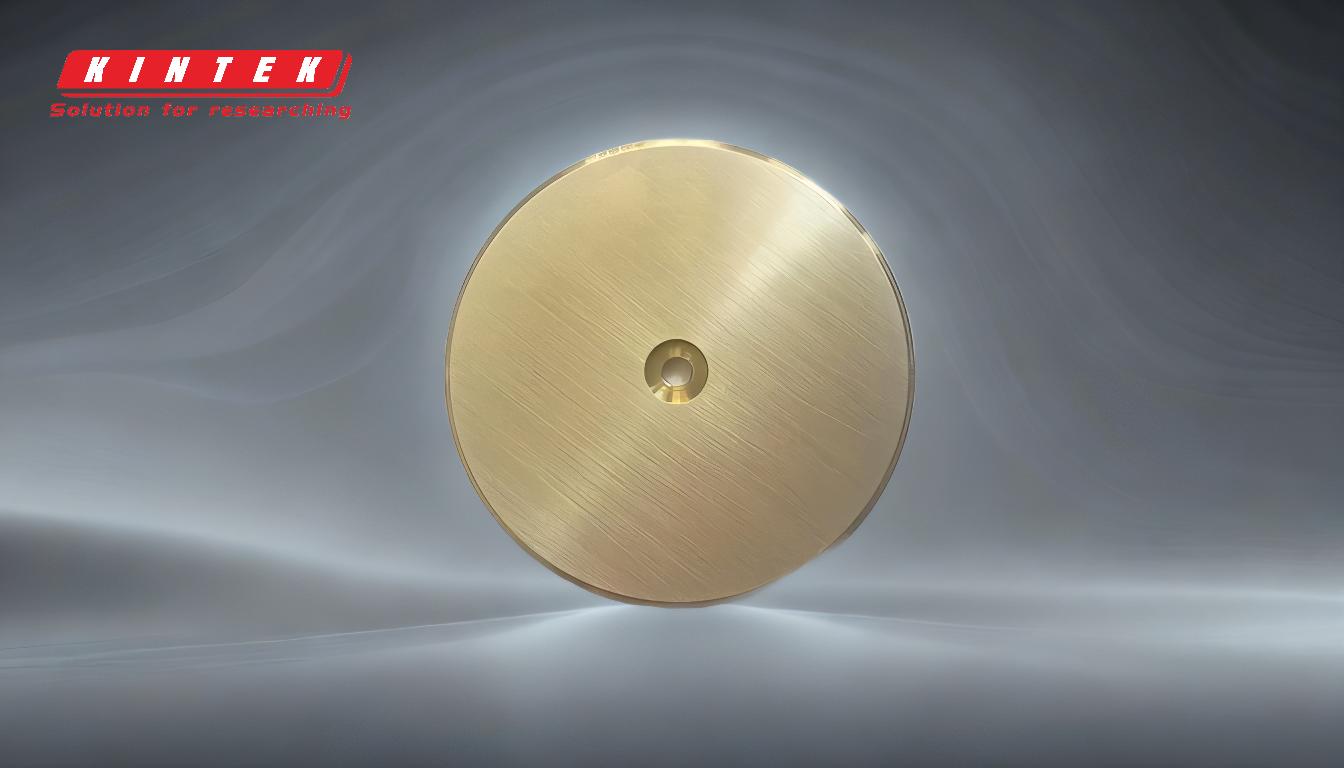
-
Définition du rendement de pulvérisation:
- Le rendement de pulvérisation est défini comme le nombre moyen d'atomes éjectés d'un matériau cible par ion incident. Il s'agit d'une mesure quantitative de l'efficacité du processus de pulvérisation.
- Ce paramètre est crucial pour le dépôt par pulvérisation cathodique, car il influence directement la vitesse de dépôt et la qualité du film déposé.
-
Facteurs influençant le rendement de la pulvérisation:
- Énergie ionique: L'énergie des ions incidents est un facteur essentiel. Dans la gamme d'énergie de 10 à 5000 eV, le rendement de la pulvérisation augmente avec l'énergie de l'ion. Les ions plus énergétiques transfèrent plus d'énergie cinétique aux atomes de la cible, ce qui augmente la probabilité d'éjection.
- Masse des ions et des atomes cibles: Les masses des ions incidents et des atomes cibles affectent le rendement de la pulvérisation. Des ions ou des atomes cibles plus lourds peuvent conduire à des rendements de pulvérisation plus élevés en raison d'un transfert de quantité de mouvement plus efficace lors des collisions.
- Angle d'incidence des ions: L'angle sous lequel les ions frappent la surface de la cible influe sur le rendement de la pulvérisation. En général, les angles obliques (non perpendiculaires) peuvent améliorer le rendement en raison d'un transfert d'énergie plus efficace.
- Énergie de liaison de la surface: L'énergie de liaison des atomes dans le matériau cible joue un rôle important. Les matériaux dont l'énergie de liaison de surface est faible ont tendance à avoir un rendement de pulvérisation plus élevé, car les atomes sont plus facilement éjectés.
- Structure cristalline: Pour les matériaux cristallins, l'orientation des axes cristallins par rapport à la surface peut affecter le rendement de pulvérisation. Certaines orientations peuvent faciliter l'éjection des atomes.
-
Implications pour le dépôt par pulvérisation:
- Taux de dépôt: Des rendements de pulvérisation plus élevés conduisent à des taux de dépôt plus élevés, ce qui est bénéfique pour une production de film efficace.
- Qualité du film: L'énergie et la direction des particules éjectées influencent la qualité du film déposé. Des conditions de pulvérisation optimales peuvent améliorer l'uniformité et l'adhérence du film.
- Optimisation du processus: La compréhension et le contrôle des facteurs affectant le rendement de la pulvérisation permettent d'optimiser les processus de pulvérisation, ce qui conduit à un meilleur contrôle des propriétés du film et de l'efficacité du processus.
-
Considérations pratiques:
- Source d'énergie: Le type de source d'énergie (DC ou RF) utilisé pour la pulvérisation affecte le rendement de la pulvérisation. La pulvérisation RF peut être plus efficace pour les matériaux isolants, tandis que la pulvérisation DC est généralement utilisée pour les matériaux conducteurs.
- Pression de la chambre: La pression dans la chambre de pulvérisation peut influencer le rendement de la pulvérisation et la distribution des particules éjectées. Un réglage optimal de la pression peut améliorer la couverture et la qualité du film.
- Compatibilité des matériaux: Des matériaux cibles et des conditions de pulvérisation différents nécessitent des approches adaptées pour obtenir les rendements de pulvérisation et les caractéristiques de film souhaités.
En résumé, le rendement de pulvérisation est un paramètre fondamental dans les processus de pulvérisation, influencé par l'énergie et la masse des ions, l'angle d'incidence, l'énergie de liaison de la surface et la structure cristalline. Il est essentiel de comprendre ces facteurs pour optimiser les processus de dépôt par pulvérisation cathodique et garantir une production de films efficace et de haute qualité.
Tableau récapitulatif :
Facteur | Impact sur le rendement de la pulvérisation |
---|---|
Énergie ionique | Augmente avec une énergie d'ion plus élevée (10-5000 eV). |
Masse des ions et de la cible | Des ions/atomes cibles plus lourds augmentent le rendement grâce à un transfert efficace de la quantité de mouvement. |
Angle d'incidence des ions | Les angles obliques améliorent le rendement en optimisant le transfert d'énergie. |
Énergie de liaison de la surface | Une énergie de liaison plus faible augmente le rendement en facilitant l'éjection des atomes. |
Structure cristalline | L'orientation du cristal affecte le rendement ; certaines orientations facilitent l'éjection des atomes. |
Optimisez votre processus de pulvérisation dès aujourd'hui. contactez nos experts pour des solutions sur mesure !