Les réacteurs discontinus et les réacteurs semi-liquides sont tous deux largement utilisés dans les processus chimiques et industriels, mais ils diffèrent considérablement dans leur fonctionnement, leur conception et leurs applications.Les réacteurs discontinus consistent à charger tous les réactifs en même temps, à laisser la réaction se dérouler pendant une période déterminée, puis à retirer les produits.Les réacteurs semi-batch, quant à eux, combinent des éléments des réacteurs discontinus et continus, où un réactif est chargé initialement et un autre est ajouté progressivement au cours de la réaction.Cette différence de fonctionnement entraîne des variations en termes de contrôle, d'efficacité et d'adéquation à des applications spécifiques.Nous examinons ci-dessous en détail les principales différences entre ces deux types de réacteurs.
Explication des points clés :
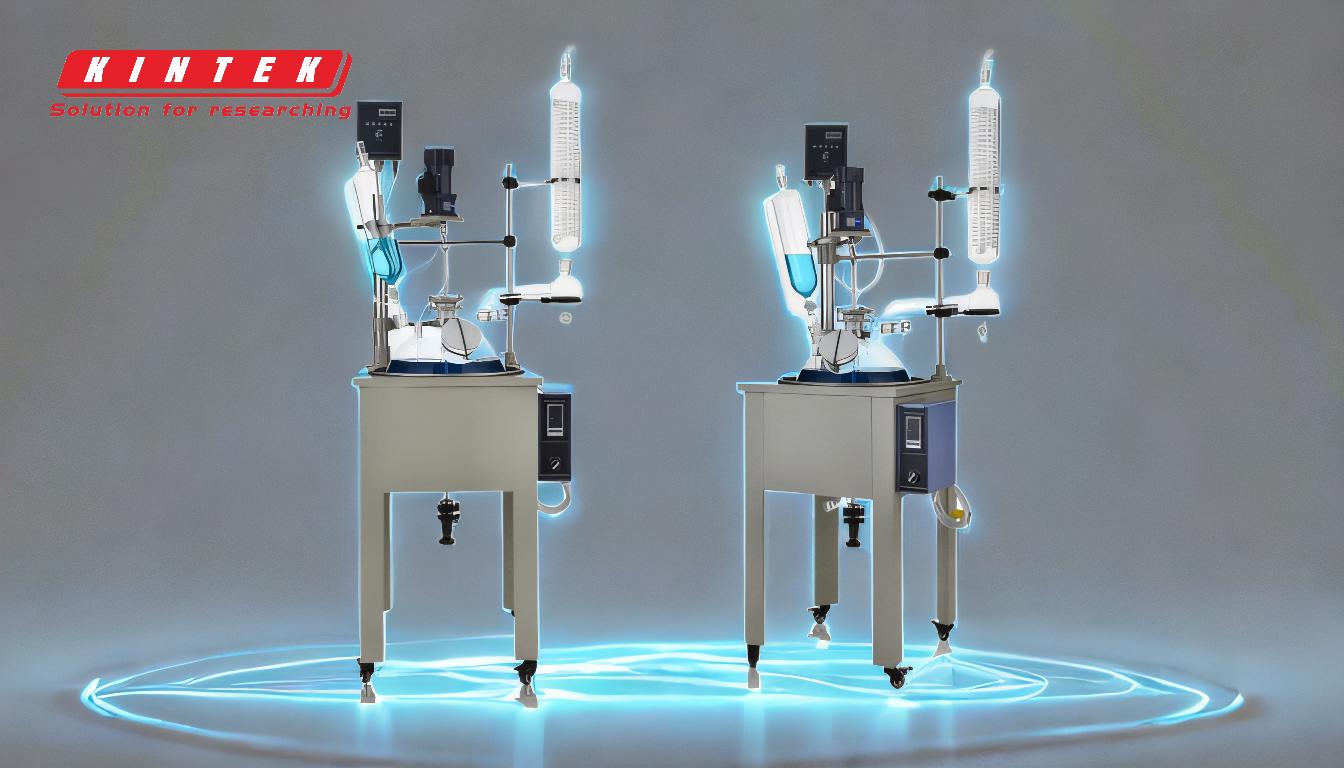
-
Mécanisme opérationnel:
-
Réacteur discontinu:Dans un réacteur discontinu, tous les réactifs, catalyseurs et composants nécessaires sont ajoutés au réacteur au début.Le réacteur est ensuite scellé et la réaction se déroule pendant une durée prédéterminée, souvent avec chauffage ou refroidissement.Une fois la réaction terminée, les produits sont éliminés et le réacteur est nettoyé pour le lot suivant.
- Exemple :Une réaction peut consister à mélanger des réactifs et à les chauffer à 50°C pendant 5 heures avant d'extraire le produit final.
-
Réacteur semi-batch:Un réacteur semi-batch fonctionne en chargeant initialement un réactif, puis en introduisant progressivement un second réactif au cours de la réaction.Cela permet de mieux contrôler la cinétique de la réaction et la production de chaleur, car le taux d'ajout peut être ajusté en fonction de la progression de la réaction.
- Exemple :Dans une réaction gaz-liquide, le liquide peut être chargé en premier et le gaz est lentement introduit dans le réacteur.
-
Réacteur discontinu:Dans un réacteur discontinu, tous les réactifs, catalyseurs et composants nécessaires sont ajoutés au réacteur au début.Le réacteur est ensuite scellé et la réaction se déroule pendant une durée prédéterminée, souvent avec chauffage ou refroidissement.Une fois la réaction terminée, les produits sont éliminés et le réacteur est nettoyé pour le lot suivant.
-
Contrôle et flexibilité:
- Réacteur discontinu:Les réacteurs discontinus offrent un contrôle limité une fois que la réaction a commencé, car tous les réactifs sont présents dès le début.Cela peut entraîner des difficultés dans la gestion des réactions exothermiques ou des réactions à cinétique complexe.
- Réacteur semi-batch:Les réacteurs semi-batch permettent de mieux contrôler le processus de réaction.En ajoutant progressivement un réactif, les opérateurs peuvent gérer plus efficacement le dégagement de chaleur, les taux de réaction et la formation du produit.Les réacteurs semi-batch sont donc idéaux pour les réactions fortement exothermiques ou nécessitant un contrôle précis.
-
Les applications:
- Réacteur discontinu:Les réacteurs discontinus sont polyvalents et largement utilisés dans des secteurs tels que l'industrie pharmaceutique, l'industrie alimentaire et les produits chimiques spécialisés.Ils conviennent à la production à petite échelle, à la recherche et au développement, où la flexibilité et l'adaptabilité sont plus importantes qu'un débit élevé.
- Réacteur semi-batch:Les réacteurs semi-batch sont particulièrement utiles dans les laboratoires et les procédés impliquant des réactions gaz-liquide ou liquide-liquide.Ils sont également utilisés dans les industries où l'ajout contrôlé de réactifs est nécessaire pour obtenir la qualité ou la sécurité souhaitée du produit.
-
Efficacité et évolutivité:
- Réacteur discontinu:Les réacteurs discontinus sont moins efficaces pour la production à grande échelle en raison des temps d'arrêt entre les lots pour le chargement, la réaction et le nettoyage.Cependant, ils sont faciles à adapter à des volumes de production différents.
- Réacteur semi-batch:Les réacteurs semi-batch offrent une meilleure efficacité pour certains procédés, car l'ajout contrôlé de réactifs peut réduire les déchets et améliorer les rendements.Toutefois, ils peuvent nécessiter des équipements et des systèmes de surveillance plus complexes que les réacteurs discontinus.
-
Conception et complexité:
- Réacteur discontinu:Les réacteurs discontinus sont de conception relativement simple et ne nécessitent que peu de modifications pour les différentes applications.Ils sont souvent choisis pour leur facilité d'utilisation et leur faible coût initial.
- Réacteur semi-batch:Les réacteurs semi-batch sont plus complexes, car ils nécessitent des systèmes pour l'ajout contrôlé de réactifs et la surveillance des paramètres de réaction.Cette complexité peut augmenter l'investissement initial, mais elle peut être justifiée par l'amélioration du contrôle du processus et de la qualité du produit.
-
Considérations relatives à la sécurité:
- Réacteur discontinu:Dans les réacteurs discontinus, les problèmes de sécurité sont liés à la présence simultanée de tous les réactifs, ce qui peut entraîner une production rapide de chaleur ou une augmentation de la pression dans les réactions exothermiques.
- Réacteur semi-batch:Les réacteurs semi-batch atténuent certains risques pour la sécurité en permettant l'ajout progressif de réactifs, ce qui permet de gérer plus efficacement la chaleur et la pression.Ils sont donc plus sûrs pour les réactions à forte libération d'énergie.
En résumé, le choix entre les réacteurs discontinus et les réacteurs semi-liquides dépend des exigences spécifiques du procédé, notamment des besoins en matière de contrôle, de sécurité, d'efficacité et d'évolutivité.Les réacteurs discontinus sont idéaux pour les applications simples et polyvalentes, tandis que les réacteurs semi-larges excellent dans les procédés nécessitant un contrôle précis et l'ajout progressif de réactifs.
Tableau récapitulatif :
Aspect | Réacteur discontinu | Réacteur semi-batch |
---|---|---|
Fonctionnement | Tous les réactifs sont chargés en même temps ; la réaction se déroule sur une période déterminée. | Un seul réactif est chargé au départ ; un deuxième réactif est ajouté progressivement au cours de la réaction. |
Contrôle | Contrôle limité une fois que la réaction a commencé. | Meilleur contrôle de la cinétique de la réaction et du dégagement de chaleur. |
Applications | Produits pharmaceutiques, transformation des aliments, produits chimiques spécialisés. | Réactions gaz-liquide, laboratoires, procédés d'addition contrôlée. |
Efficacité | Moins efficace pour la production à grande échelle en raison des temps d'arrêt. | Plus efficace pour certains processus avec une réduction des déchets et une amélioration des rendements. |
Complexité de la conception | Conception simple, faible coût initial. | Plus complexe, nécessite un ajout contrôlé et des systèmes de surveillance. |
Sécurité | Risque plus élevé d'accumulation rapide de chaleur/pression dans les réactions exothermiques. | Plus sûr grâce à l'ajout progressif de réactifs et à une meilleure gestion de la chaleur et de la pression. |
Vous avez besoin d'aide pour choisir le bon réacteur pour votre procédé ? Contactez nos experts dès aujourd'hui !