Lorsque les céramiques, en particulier les argiles, sont cuites dans un four, le carbone et les composés organiques qu'elles contiennent subissent un processus appelé oxydation, au cours duquel ils brûlent.Cette combustion est essentielle pour éviter les défauts dans le produit final, tels que le gonflement ou la décoloration, qui peuvent survenir si le carbone n'est pas entièrement éliminé.Le processus consiste à chauffer le matériau à des températures élevées, généralement entre 500°C et 900°C, où le carbone réagit avec l'oxygène pour former du dioxyde de carbone et d'autres gaz, qui sont ensuite évacués hors du four.Après la cuisson, le matériau est refroidi et traité, souvent par broyage et granulation, avant d'être emballé pour le transport.
Explication des principaux points :
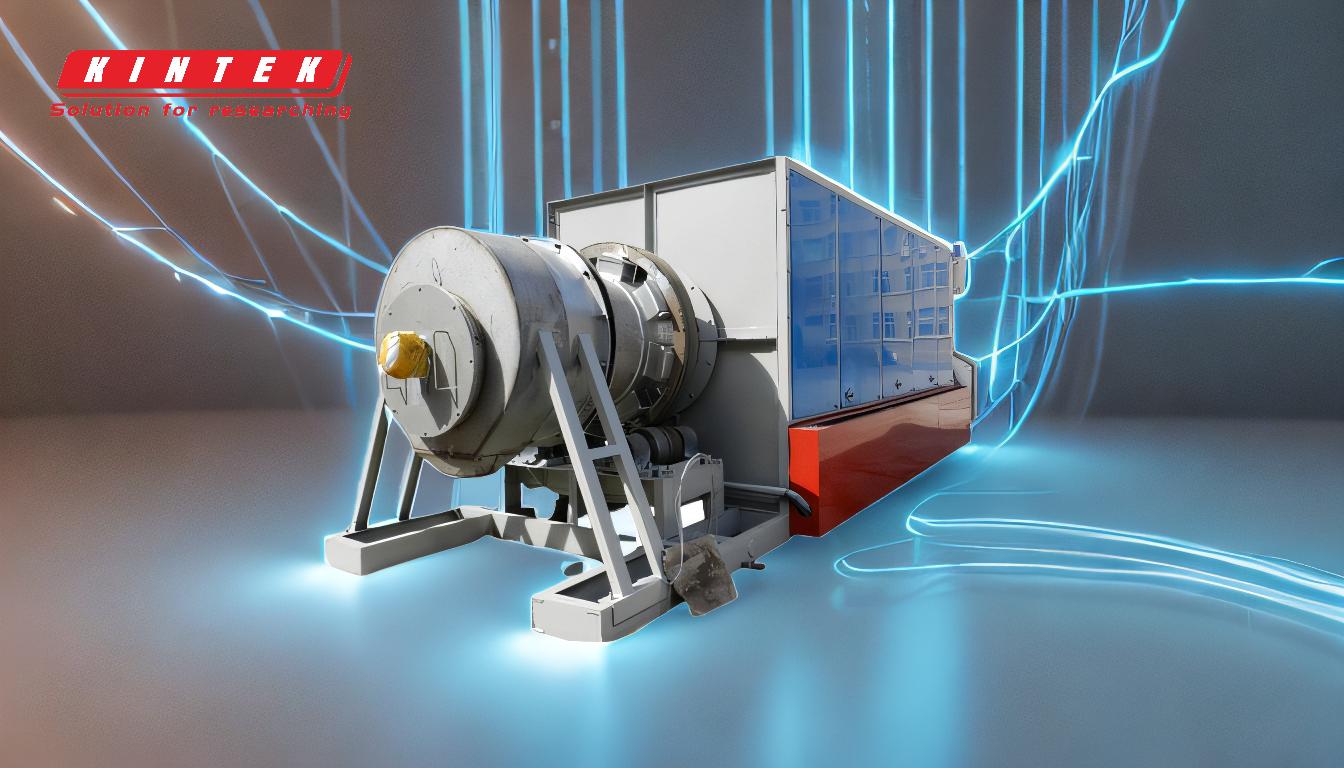
-
Présence de carbone dans les céramiques :
- Les matériaux céramiques, en particulier les argiles, contiennent naturellement du carbone et des composés organiques.Ceux-ci peuvent provenir de la décomposition de matières végétales et animales dans le sol où l'argile est formée.
-
La nécessité de brûler le carbone :
- Au cours du processus de cuisson dans un four, il est essentiel de brûler le carbone et les composés organiques.S'ils ne sont pas éliminés, ils peuvent entraîner des défauts dans les produits céramiques, tels que des boursouflures, des noyaux noirs ou des décolorations, qui compromettent l'intégrité structurelle et la qualité esthétique du produit final.
-
Processus d'oxydation :
- La combustion du carbone s'effectue par un processus d'oxydation.Il s'agit de chauffer le matériau céramique à des températures généralement comprises entre 500°C et 900°C.À ces températures, le carbone réagit avec l'oxygène présent dans l'atmosphère du four pour former du dioxyde de carbone (CO₂) et d'autres sous-produits gazeux.
- Le processus d'oxydation est soigneusement contrôlé afin d'assurer une combustion complète des matières carbonées.Une oxydation insuffisante peut laisser des résidus de carbone, ce qui entraîne les défauts susmentionnés.
-
Complications pendant la cuisson :
- La combustion du carbone et des composés organiques peut entraîner des complications pendant la cuisson.Il s'agit notamment de la libération de gaz qui peuvent provoquer des boursouflures ou des trous d'épingle dans le corps de la céramique s'ils ne sont pas correctement ventilés.En outre, une oxydation rapide peut entraîner un choc thermique, susceptible de fissurer les pièces en céramique.
-
Traitement post-cuisson :
- Une fois que le carbone a été brûlé et que la céramique a été cuite, le matériau est refroidi.Ce processus de refroidissement doit être contrôlé afin d'éviter toute contrainte thermique susceptible de provoquer des fissures.
- Une fois refroidi, le matériau peut subir d'autres traitements, tels que le broyage pour obtenir la taille de particule souhaitée, la granulation pour faciliter la manipulation et l'ensachage pour le transport.Le matériau est ainsi prêt pour sa prochaine utilisation ou pour la distribution.
-
Importance du contrôle de la température :
- La température à laquelle le carbone brûle est essentielle.Si la température du four est trop basse, le carbone risque de ne pas brûler complètement, ce qui entraînera des défauts.Inversement, une température trop élevée peut entraîner d'autres problèmes, tels que la surcuisson, qui peut affaiblir la structure de la céramique.
- Les opérateurs de four doivent surveiller et contrôler attentivement la température tout au long du cycle de cuisson afin d'obtenir des résultats optimaux.
-
Considérations environnementales :
- Le dégagement de dioxyde de carbone et d'autres gaz au cours du processus de cuisson a des répercussions sur l'environnement.Les fours modernes sont souvent équipés de systèmes de capture et de traitement de ces émissions afin de minimiser leur impact sur l'environnement.
- La combustion efficace du carbone contribue également à réduire l'empreinte carbone globale du processus de fabrication de la céramique.
En résumé, la combustion du carbone dans un four est une étape critique du processus de fabrication de la céramique.Elle implique un processus d'oxydation soigneusement contrôlé pour garantir l'élimination complète du carbone et des composés organiques, évitant ainsi les défauts dans le produit final.Le contrôle de la température, la ventilation et le traitement post-cuisson sont essentiels pour obtenir des céramiques de haute qualité.En outre, les considérations environnementales jouent un rôle dans la gestion des émissions produites au cours de ce processus.
Tableau récapitulatif :
Aspect clé | Détails |
---|---|
Présence de carbone | Les céramiques, en particulier les argiles, contiennent du carbone provenant de la matière organique décomposée. |
Nécessité de brûler le carbone | Prévient les défauts tels que le gonflement, la décoloration et la formation de noyaux noirs. |
Processus d'oxydation | Le carbone réagit avec l'oxygène à 500°C-900°C pour former du CO₂, assurant ainsi la combustion. |
Complications pendant la cuisson | Le dégagement de gaz peut provoquer des boursouflures ou des fissures s'il n'est pas correctement ventilé. |
Traitement post-combustion | Le refroidissement, le broyage, la granulation et l'emballage garantissent la disponibilité des matériaux. |
Contrôle de la température | Il est essentiel d'éviter la sous-cuisson ou la surcuisson, qui peuvent affaiblir les céramiques. |
Impact sur l'environnement | Les émissions sont gérées de manière à réduire l'empreinte carbone de la production de céramique. |
Garantissez des céramiques de haute qualité grâce à des solutions de cuisson expertes. contactez-nous dès aujourd'hui pour plus d'informations !