La pulvérisation cathodique, bien qu'elle soit une technique de dépôt de couches minces largement utilisée, présente plusieurs limites qui peuvent avoir un impact sur son efficacité, sa qualité et son applicabilité. Ces limites comprennent les défis posés par les matériaux isolants, la contamination potentielle des films, les vitesses de dépôt plus faibles et les difficultés de contrôle des paramètres du processus. En outre, des problèmes tels que le chauffage du substrat, l'arc électrique et l'empoisonnement de la cible compliquent encore le processus. Des techniques avancées telles que la pulvérisation magnétron ont été développées pour atténuer certains de ces problèmes, mais la pulvérisation à courant continu reste confrontée à des difficultés inhérentes qui limitent son efficacité dans certaines applications.
Explication des points clés :
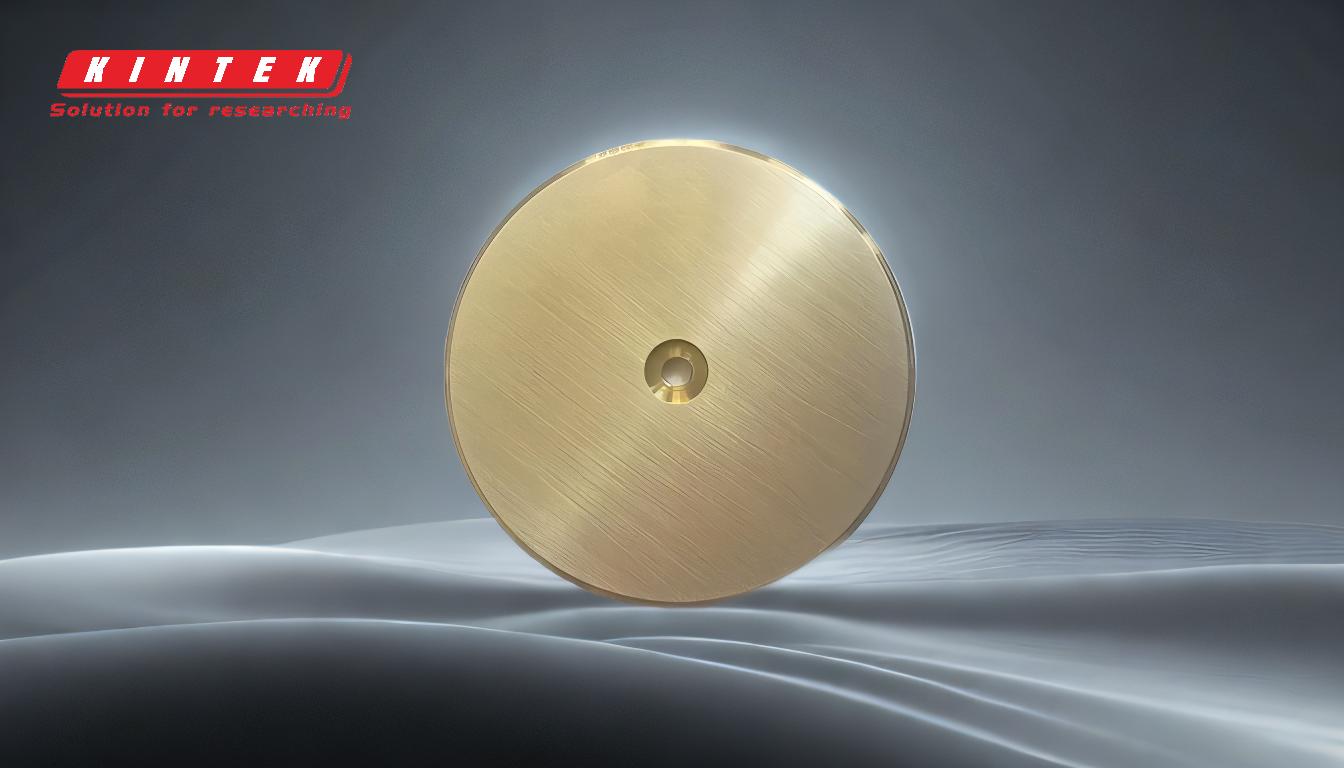
-
Défis liés aux matériaux isolants:
- Accumulation de charges: Les matériaux diélectriques non conducteurs peuvent accumuler des charges au fil du temps, ce qui entraîne la formation d'arcs ou l'empoisonnement de la cible. Cela perturbe le processus de pulvérisation et peut l'interrompre complètement.
- Arcs électriques et dommages au niveau de l'alimentation: L'accumulation de charges peut provoquer de petits et de macro-arcades, qui non seulement endommagent l'alimentation électrique, mais entraînent également une élimination inégale des atomes du matériau cible.
-
Contamination des films:
- Diffusion des impuretés: Au cours du processus de pulvérisation, les impuretés provenant des matériaux sources peuvent se diffuser dans le film, ce qui entraîne une contamination.
- Contraintes de température de fusion: La sélection des matériaux de revêtement est limitée par leur température de fusion, ce qui peut restreindre la gamme des matériaux qui peuvent être efficacement pulvérisés.
-
Des taux de dépôt plus faibles:
- Densité du plasma: La pulvérisation DC présente généralement des densités de plasma plus faibles que les techniques plus avancées telles que la pulvérisation magnétron à impulsion de haute puissance (HIPIMS), ce qui se traduit par des taux de dépôt plus faibles.
- Densité du gaz: Les densités de gaz plus élevées dans la pulvérisation cathodique contribuent également à réduire les taux de dépôt.
-
Contrôle des processus et sensibilité des paramètres:
- Sensibilité des paramètres: Le contrôle précis des paramètres du processus, tels que la pression du gaz, la distance cible-substrat et la tension, est crucial pour obtenir des résultats optimaux. De petits écarts peuvent avoir un impact significatif sur la qualité du film déposé.
- Pressions de fonctionnement élevées: Les procédés traditionnels de pulvérisation nécessitent souvent des pressions de fonctionnement élevées, ce qui peut affecter la qualité et l'efficacité du dépôt de couches minces.
-
Chauffage du substrat:
- Effets thermiques: Le processus de pulvérisation peut provoquer un échauffement important du substrat, ce qui n'est pas forcément souhaitable pour les matériaux ou les applications sensibles à la température.
-
Exigences en matière de système de refroidissement:
- Coûts de l'énergie: La nécessité d'un système de refroidissement pour gérer le chauffage du substrat diminue le taux de production et augmente les coûts énergétiques, ce qui rend le processus moins efficace et plus coûteux.
-
Contamination de la chambre:
- Revêtements non conducteurs: La pulvérisation de matériaux diélectriques peut recouvrir les parois de la chambre à vide d'un matériau non conducteur, piégeant les charges électriques et entraînant des arcs électriques et d'autres problèmes de qualité.
-
Questions de blindage et de perméation:
- Joints en élastomère: La perméation à travers les joints en élastomère et les problèmes liés au blindage peuvent compliquer davantage le processus de pulvérisation, en affectant la qualité globale du film déposé.
En résumé, si la pulvérisation cathodique est une technique précieuse pour le dépôt de couches minces, elle n'est pas sans limites. Ces défis nécessitent un examen minutieux des paramètres du processus, de la sélection des matériaux et de l'utilisation de techniques avancées pour atténuer certains des problèmes inhérents. Il est essentiel de comprendre ces limites pour optimiser le processus de pulvérisation et obtenir des couches minces de haute qualité.
Tableau récapitulatif :
Limitation | Principaux défis |
---|---|
Matériaux isolants | Accumulation de charges, formation d'arcs électriques et dommages à l'alimentation électrique |
Contamination des films | Diffusion d'impuretés, contraintes liées à la température de fusion |
Des taux de dépôt plus faibles | Faible densité de plasma, forte densité de gaz |
Contrôle des processus | Sensibilité des paramètres, pressions de fonctionnement élevées |
Chauffage du substrat | Effets thermiques sur les matériaux sensibles à la température |
Exigences en matière de système de refroidissement | Augmentation des coûts énergétiques et réduction des taux de production |
Contamination de la chambre | Revêtements non conducteurs entraînant des arcs électriques et des problèmes de qualité |
Blindage et perméation | Complications liées à la perméation et au blindage des joints en élastomère |
Besoin d'aide pour optimiser votre processus de dépôt de couches minces ? Contactez nos experts dès aujourd'hui pour des solutions sur mesure !