Le revêtement PVD (Physical Vapor Deposition) est une technique de traitement de surface polyvalente et avancée qui consiste à déposer de fines couches de matériaux, atome par atome, sur un substrat.Les matériaux utilisés pour les revêtements PVD sont divers et adaptés à des applications spécifiques, offrant des propriétés améliorées telles que la dureté, la résistance à l'usure, la résistance à la corrosion et l'attrait esthétique.Les matériaux courants comprennent des métaux tels que le titane, le zirconium et le chrome, ainsi que des céramiques telles que le nitrure de titane (TiN), le nitrure de chrome (CrN) et le carbone de type diamant (DLC).Ces matériaux sont choisis en fonction des caractéristiques de performance souhaitées et du type de substrat à revêtir.Les revêtements PVD sont largement utilisés dans des secteurs allant de l'automobile à l'aérospatiale en passant par le médical et l'outillage, afin d'assurer la durabilité et la longévité des produits.
Explication des principaux points :
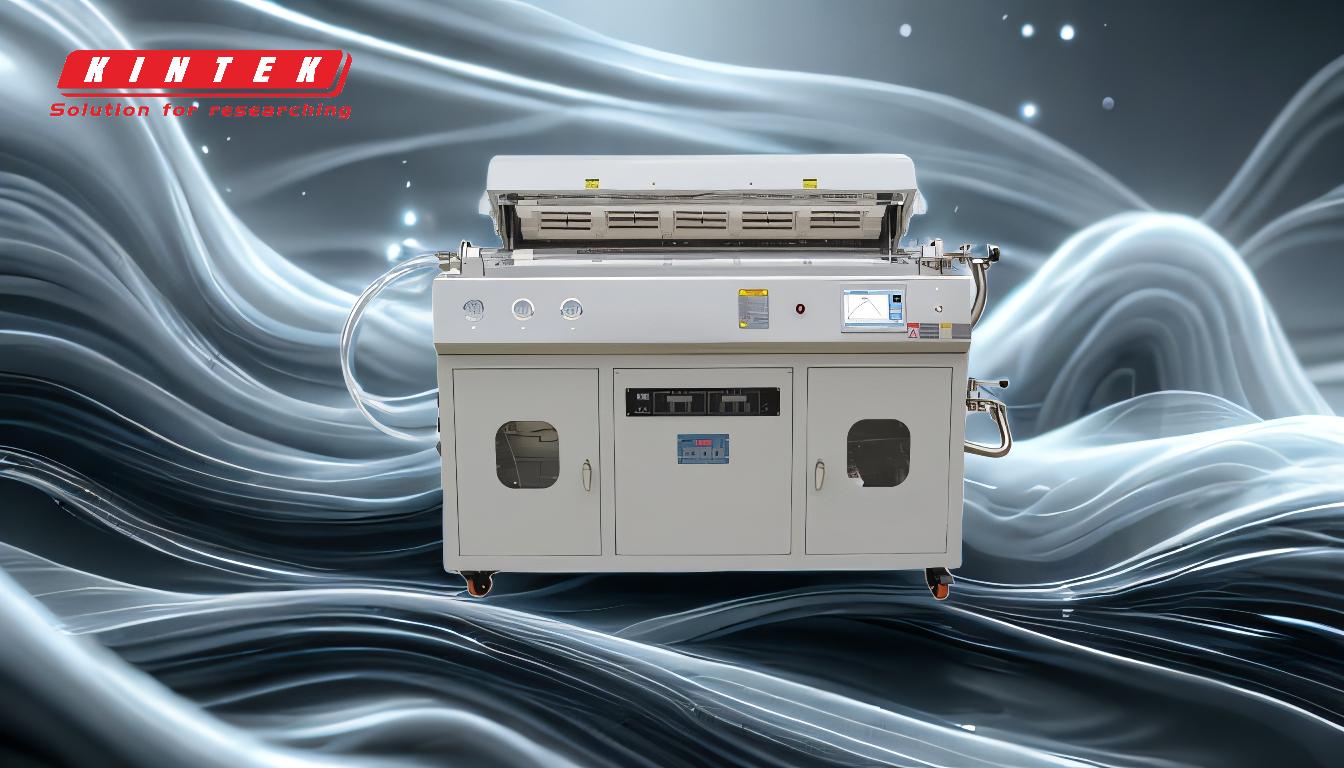
-
Matériaux utilisés pour le revêtement PVD:
-
Les revêtements PVD utilisent une variété de matériaux, y compris des métaux, des céramiques et des composés spécialisés.Parmi les exemples les plus courants, on peut citer
- Nitrure de titane (TiN):Connu pour son aspect doré, sa grande dureté et son excellente résistance à l'usure, le TiN est largement utilisé dans les outils de coupe, les moules et les applications décoratives.
- Nitrure de chrome (CrN):Il offre une résistance supérieure à la corrosion et est souvent utilisé dans les matrices de moulage de plastique et les instruments médicaux.
- Nitrure de zirconium (ZrN):Il donne une couleur dorée et est utilisé à des fins décoratives et pour des revêtements résistants à l'usure.
- Carbone de type diamant (DLC):Connu pour sa dureté exceptionnelle et sa faible friction, le DLC est utilisé dans les composants automobiles et les outils de haute performance.
-
Les revêtements PVD utilisent une variété de matériaux, y compris des métaux, des céramiques et des composés spécialisés.Parmi les exemples les plus courants, on peut citer
-
Supports adaptés au revêtement PVD:
-
Les revêtements PVD peuvent être appliqués sur une large gamme de substrats, y compris :
- Familles d'acier:Les aciers fortement alliés tels que les aciers rapides et les aciers inoxydables sont couramment revêtus en raison de leur compatibilité avec les procédés PVD.
- Métaux non ferreux:Les matériaux tels que le cuivre, l'aluminium et leurs alliages peuvent également être revêtus, ce qui améliore leur durabilité et leurs performances.
- Métaux chromés ou nickelés:Ces matériaux conviennent au revêtement PVD, mais le laiton non galvanisé ou les matériaux galvanisés ne sont pas recommandés en raison de leur incompatibilité avec les procédés sous vide.
-
Les revêtements PVD peuvent être appliqués sur une large gamme de substrats, y compris :
-
Applications des revêtements PVD:
-
Les revêtements PVD sont utilisés dans diverses industries pour améliorer les performances et la durée de vie des produits.Les principales applications sont les suivantes
- l'automobile:Revêtement de pièces automobiles telles que les roues et les pistons pour améliorer la durabilité et la résistance à l'usure et à la corrosion.
- Médical:Revêtement d'outils chirurgicaux pour améliorer leur longévité et leur résistance aux processus de stérilisation.
- Outillage:Revêtement de forets et de moules pour augmenter leur dureté et leur résistance à l'usure.
- Aérospatiale:Utilisation de revêtements spécialisés comme le graphite et le titane pour des composants de haute performance.
-
Les revêtements PVD sont utilisés dans diverses industries pour améliorer les performances et la durée de vie des produits.Les principales applications sont les suivantes
-
Avantages des revêtements PVD:
-
Les revêtements PVD offrent plusieurs avantages par rapport aux méthodes de placage traditionnelles :
- Durabilité accrue:Les produits revêtus de PVD peuvent durer jusqu'à dix fois plus longtemps que les produits non revêtus, certains pouvant même durer plus de 25 ans.
- Respect de l'environnement:Le dépôt en phase vapeur (PVD) est une alternative plus écologique au chromage, car il ne produit pas de substances toxiques.
- Polyvalence:La large gamme de matériaux et de substrats permet au dépôt en phase vapeur (PVD) de s'adapter à diverses applications.
-
Les revêtements PVD offrent plusieurs avantages par rapport aux méthodes de placage traditionnelles :
-
Techniques de revêtement PVD:
-
Les deux principales techniques utilisées pour le revêtement PVD sont les suivantes :
- l'évaporation:Le matériau de revêtement est vaporisé puis déposé sur le substrat.
- Pulvérisation:Des ions à grande vitesse sont utilisés pour libérer les atomes du matériau source, qui sont ensuite déposés sur le substrat.
-
Les deux principales techniques utilisées pour le revêtement PVD sont les suivantes :
-
Revêtements PVD spécialisés:
- Pour des applications spécifiques, des revêtements uniques tels que les carbures, les nitrures, les siliciures et les borures sont utilisés.Ces revêtements sont conçus pour répondre aux exigences de secteurs tels que l'aérospatiale et l'automobile.
En comprenant les matériaux et les techniques utilisés dans les revêtements PVD, les acheteurs peuvent prendre des décisions éclairées sur les meilleurs revêtements pour leurs besoins spécifiques, garantissant ainsi l'amélioration des performances et de la longévité de leurs produits.
Tableau récapitulatif :
Matériau | Propriétés | Applications |
---|---|---|
Nitrure de titane (TiN) | Dureté élevée, résistance à l'usure, aspect doré | Outils de coupe, moules, applications décoratives |
Nitrure de chrome (CrN) | Résistance supérieure à la corrosion | Matrices de moulage en plastique, instruments médicaux |
Nitrure de zirconium (ZrN) | Couleur dorée, résistance à l'usure | Décorations, revêtements résistants à l'usure |
Carbone de type diamant (DLC) | Dureté exceptionnelle, faible frottement | Composants automobiles, outils de haute performance |
Métaux (titane, zirconium, chrome) | Durabilité accrue, résistance à la corrosion | Industries automobile, aérospatiale, médicale et de l'outillage |
Vous avez besoin du revêtement PVD idéal pour votre application ? Contactez nos experts dès aujourd'hui pour trouver la meilleure solution !