L'oxyde de zirconium (zircone) se fritte généralement à des températures élevées allant de 1400°C à 1600°C, la plupart des processus se déroulant à des températures plus proches de 1500°C à 1550°C. Cette plage de températures est essentielle pour obtenir la dureté, la densité et la résistance souhaitées du produit final. Le frittage à ces températures transforme la zircone d'une structure monoclinique en une structure polytétragonale, ce qui améliore considérablement ses propriétés mécaniques. Cependant, tout écart par rapport à cette plage optimale, même de 150°C, peut entraîner une réduction de la résistance en raison de la croissance des grains. Des fours de frittage à haute température spécialisés sont nécessaires pour ce processus, car les fours à porcelaine standard ne peuvent pas atteindre ces températures.
Explication des points clés :
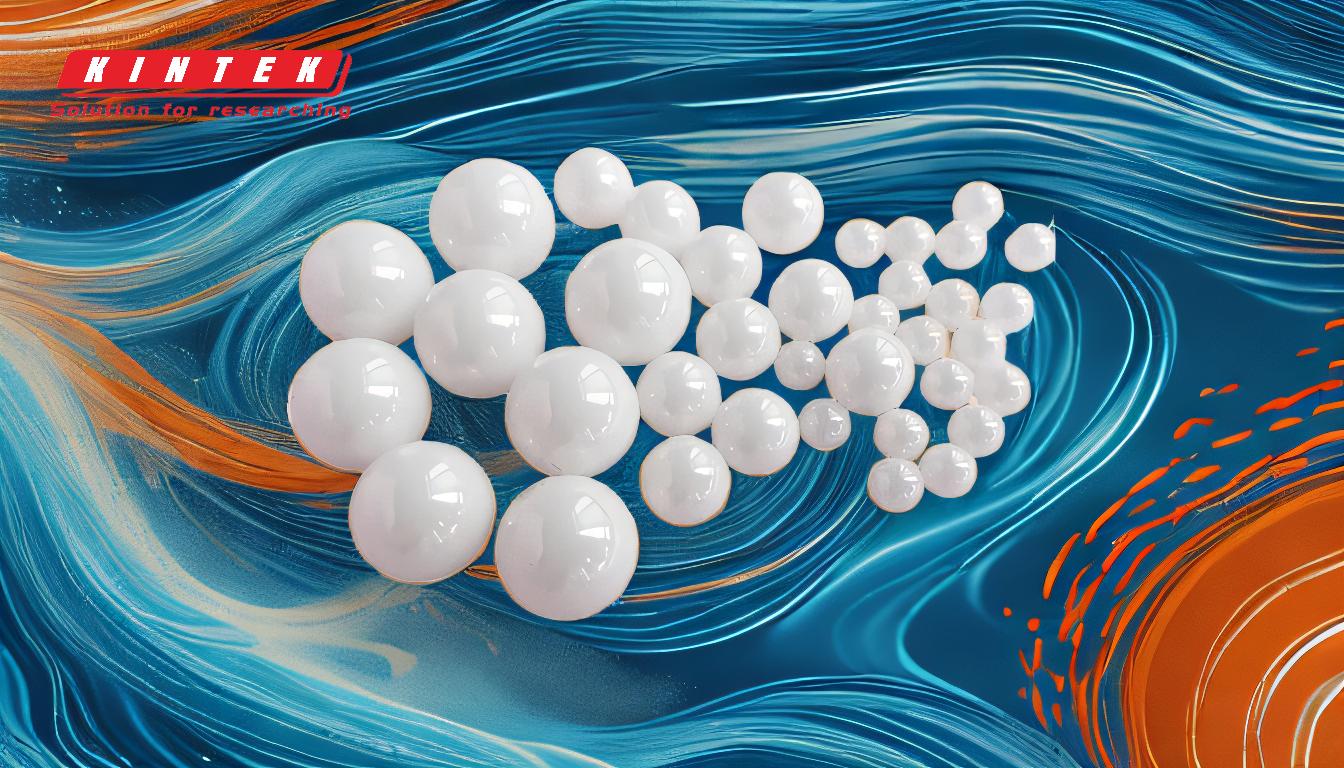
-
Plage de température optimale de frittage:
- La zircone sintérise efficacement entre 1400°C et 1600°C la plupart des processus visent à 1500°C à 1550°C .
- Cette gamme assure la transformation d'une structure cristalline monoclinique en une structure cristalline polytétragonale, ce qui est essentiel pour obtenir une densité et une résistance élevées.
- Le frittage à ces températures permet à la zircone d'atteindre près de 99% de sa densité maximale théorique .
-
Impact de la température sur la résistance:
- Cuisson de la zircone à 1500°C à 1550°C produit une force maximale, avec des valeurs autour de 1280 MPa .
-
Si l'on s'écarte de cette fourchette en
±150°C
peut réduire considérablement la résistance :
- Au 1600°C , la force diminue jusqu'à environ 980 MPa .
- Au 1700°C , la résistance diminue encore pour atteindre environ 600 MPa .
- Cette réduction de la résistance est attribuée à une croissance excessive du grain à des températures plus élevées.
-
Taux de montée en température:
- Une vitesse de montée en température lente de 4°C à 10°C par minute est recommandée pendant le frittage.
- Ce chauffage contrôlé assure une densification uniforme et minimise les contraintes internes, qui pourraient sinon entraîner des défauts dans le produit final.
-
Exigences en matière de four:
- Spécialisé fours de frittage à haute température sont nécessaires pour traiter la zircone.
- Les fours à porcelaine standard, généralement utilisés pour la cuisson d'infiltration du verre, ne peuvent pas atteindre les températures élevées requises pour le frittage de la zircone.
-
Transformation structurelle:
- La transformation de la zircone monoclinique en zircone polytétragonale se produit à 1100°C à 1200°C .
- Cependant, pour obtenir une densification complète et des propriétés mécaniques optimales, il faut fritter à des températures plus élevées ( 1400°C à 1600°C ).
-
Considérations pratiques pour les acheteurs:
- Lors du choix d'un four de frittage, il convient de s'assurer qu'il peut maintenir en permanence les températures dans les limites de la zone de frittage 1500°C à 1550°C gamme.
- Vérifiez la précision et l'uniformité de la température du four, car de petits écarts peuvent avoir une incidence sur la résistance du produit final.
- Envisagez des appareils de chauffage avec des taux de montée en température programmables pour atteindre les valeurs recommandées 4°C à 10°C par minute profil de chauffage.
En respectant ces lignes directrices, les acheteurs peuvent garantir la production de composants en zircone de haute qualité avec des propriétés mécaniques optimales.
Tableau récapitulatif :
Facteur clé | Détails |
---|---|
Plage de frittage optimale | 1400°C-1600°C (objectif 1500°C-1550°C) |
Résistance à 1500°C-1550°C | ~1280 MPa |
Réduction de la résistance à 1600°C | ~980 MPa |
Réduction de la résistance à 1700°C | ~600 MPa |
Taux de montée en température | 4°C-10°C par minute |
Type de four | Four de frittage spécialisé à haute température (les fours à porcelaine standard ne suffisent pas) |
Densité atteinte | ~99% du maximum théorique |
Transformation structurelle | Monoclinique à polytétragonal à 1100°C-1200°C |
Assurez-vous que votre processus de frittage de la zircone est conforme aux normes de l'industrie contactez nos experts dès aujourd'hui pour des solutions sur mesure !