Les revêtements en carbone de type diamant (DLC) sont largement reconnus pour leurs excellentes propriétés, telles qu'une dureté élevée, une faible friction et une résistance à l'usure.Cependant, ils présentent également plusieurs inconvénients qui peuvent limiter leur applicabilité dans certains scénarios.Il s'agit notamment des défis liés aux processus de dépôt, à la compatibilité des matériaux et aux performances dans des conditions spécifiques.Il est essentiel de comprendre ces limites pour prendre des décisions éclairées lorsque l'on envisage d'utiliser des revêtements DLC pour diverses applications.
Explication des points clés :
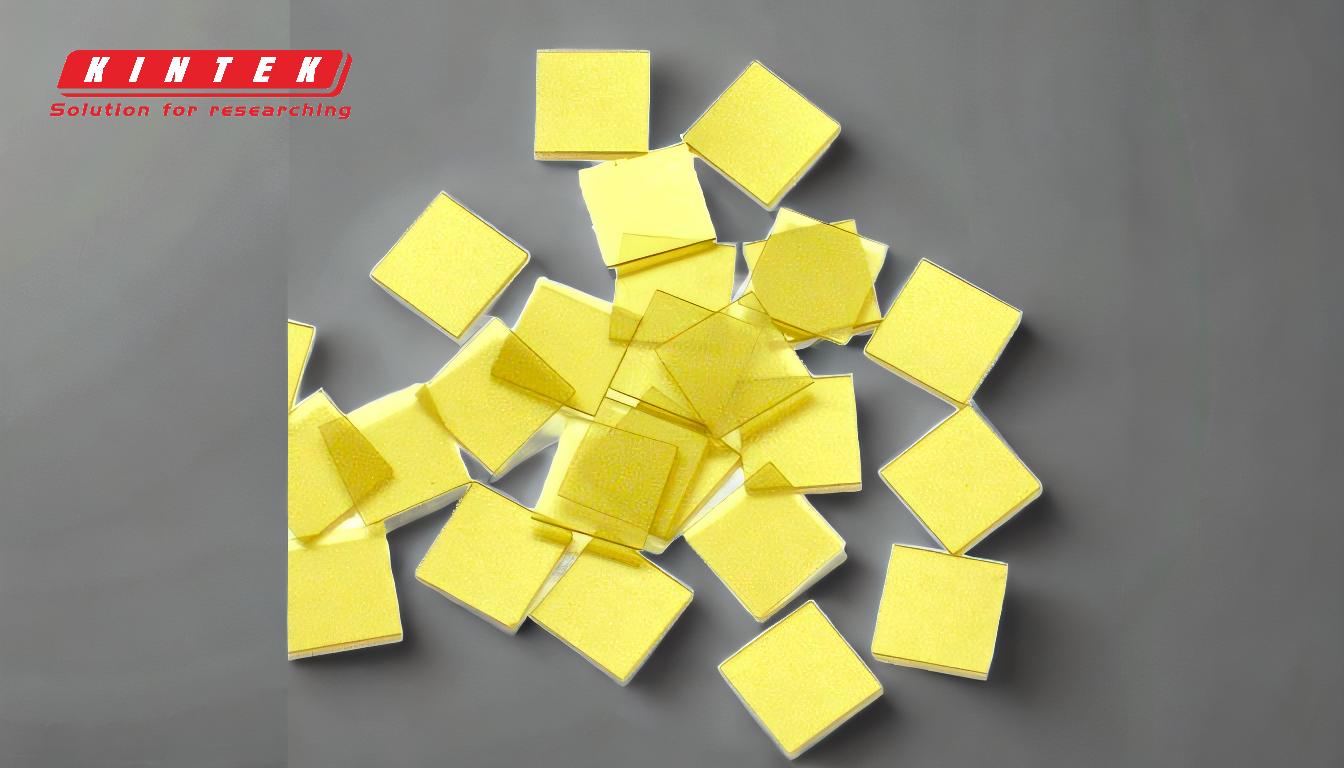
-
Limites du processus de dépôt:
- Températures de traitement élevées:Les revêtements DLC, en particulier ceux appliqués par dépôt chimique en phase vapeur (CVD), nécessitent souvent des températures de traitement élevées (800-1000 °C).Cela limite leur utilisation aux matériaux qui peuvent supporter une telle chaleur, comme le carbure cémenté.De nombreux matériaux, en particulier les polymères et certains métaux, ne peuvent supporter ces températures, ce qui limite la gamme d'applications.
- Difficultés de masquage:Les revêtements CVD sont difficiles à masquer, ce qui donne souvent un revêtement "tout ou rien".Cela signifie que le revêtement sélectif de zones spécifiques est difficile, ce qui peut constituer un inconvénient important lorsque seules certaines parties d'un composant doivent être revêtues.
- Contraintes de taille:La taille des pièces pouvant être revêtues est limitée par la capacité de la chambre de réaction.Les composants complexes ou de grande taille peuvent devoir être divisés en pièces plus petites, ce qui complique le processus et augmente les coûts.
-
Épaisseur du revêtement et problèmes de contrainte:
- Revêtements épais et contraintes de traction:Les revêtements DLC, notamment ceux appliqués par CVD, peuvent être relativement épais (10-20 μm).Pendant le refroidissement, ces revêtements épais peuvent générer des contraintes de traction, entraînant de fines fissures.Ces fissures peuvent se propager sous l'effet d'un impact externe, entraînant le décollement du revêtement.Les revêtements DLC sont donc moins adaptés aux applications impliquant des processus de coupe interrompus, tels que le fraisage, où le revêtement est plus susceptible de s'abîmer.
- Défis en matière d'adhérence:L'adhésion des revêtements DLC à certains substrats peut être problématique, en particulier si le matériau du substrat n'est pas compatible avec les températures élevées ou si la préparation de la surface est inadéquate.Une mauvaise adhérence peut entraîner une délamination et une réduction des performances du revêtement.
-
Limites de performance dans des conditions spécifiques:
- Processus de coupe interrompus:Les revêtements DLC ne sont pas idéaux pour les processus de coupe interrompue tels que le fraisage.Les impacts répétés et les cycles thermiques de ces processus peuvent exacerber la formation de fissures et entraîner une défaillance du revêtement.Cela limite leur utilisation dans certaines applications d'usinage où d'autres revêtements pourraient être plus performants.
- Teneur en hydrogène et stabilité:Certains revêtements DLC contiennent de l'hydrogène, ce qui peut affecter leur stabilité et leurs performances, en particulier à des températures élevées.Les revêtements DLC hydrogénés peuvent se dégrader ou perdre leurs propriétés lorsqu'ils sont exposés à des températures élevées, ce qui limite leur utilisation dans les applications à haute température.
-
Coût et complexité:
- Coût élevé du dépôt:L'équipement et les procédés requis pour déposer des revêtements DLC, en particulier par CVD, sont complexes et coûteux.Cela peut rendre le coût des revêtements DLC prohibitif pour certaines applications, en particulier lorsqu'on les compare à d'autres revêtements.
- Complexité du processus:La nécessité de températures élevées, d'équipements spécialisés et d'un contrôle précis des paramètres de dépôt ajoute à la complexité du processus.Cela peut augmenter le temps et les coûts de production, ce qui rend les revêtements DLC moins intéressants pour les applications à haut volume ou à faible coût.
-
Compatibilité des matériaux et gamme d'applications:
- Compatibilité limitée avec les substrats:Les revêtements DLC ne sont pas universellement compatibles avec tous les matériaux.Par exemple, ils peuvent ne pas bien adhérer à certains métaux ou polymères, ce qui limite leur utilisation dans les applications où ces matériaux sont prédominants.
- Gamme d'applications restreinte:En raison des limitations mentionnées ci-dessus, les revêtements DLC sont souvent limités à des applications spécifiques où leurs propriétés uniques, telles qu'une faible friction et une grande résistance à l'usure, sont essentielles.Dans d'autres cas, d'autres revêtements peuvent être plus appropriés.
En résumé, si les revêtements DLC offrent des avantages significatifs en termes de dureté, de réduction du frottement et de résistance à l'usure, ils présentent également des inconvénients notables.Il s'agit notamment des défis liés au processus de dépôt, à l'épaisseur et à la contrainte du revêtement, aux performances dans des conditions spécifiques, au coût et à la compatibilité des matériaux.Il est essentiel de comprendre ces limites pour sélectionner le revêtement approprié pour une application donnée et garantir une performance et une durabilité optimales.
Tableau récapitulatif :
Inconvénient | Description |
---|---|
Températures de traitement élevées | Nécessite 800-1000 °C, ce qui limite l'utilisation aux matériaux résistants à la chaleur. |
Difficultés de masquage | Le revêtement sélectif est un défi ; il en résulte souvent une application "tout ou rien". |
Contraintes de taille | Limitée par la taille de la chambre de réaction, ce qui complique les composants complexes ou de grande taille. |
Revêtements épais et contraintes de traction | Les revêtements épais (10-20 μm) peuvent se fissurer sous l'effet de la contrainte, ce qui entraîne un décollement. |
Problèmes d'adhérence | Une mauvaise adhérence à certains substrats peut entraîner une délamination. |
Processus de coupe interrompus | Pas idéal pour le fraisage en raison de la formation de fissures sous l'effet d'impacts répétés. |
Teneur en hydrogène et stabilité | Les revêtements hydrogénés peuvent se dégrader à des températures élevées. |
Coût élevé du dépôt | Des équipements complexes et coûteux augmentent les coûts globaux. |
Compatibilité limitée avec les substrats | La compatibilité avec tous les matériaux n'est pas universelle, ce qui limite le champ d'application. |
Vous avez besoin d'aide pour choisir le bon revêtement pour votre application ? Contactez nos experts dès aujourd'hui !