Les revêtements PVD (Physical Vapor Deposition) sont en effet très résistants à la corrosion, ce qui les rend adaptés aux applications exigeantes où la durabilité est essentielle.Ces revêtements créent une couche mince, dure et durable qui adhère fortement au substrat, renforçant ainsi sa résistance à la corrosion, à l'oxydation et à l'usure.Le procédé consiste à vaporiser un matériau cible sous vide et à le déposer sur le substrat, ce qui permet d'obtenir un revêtement pur et durable.Les revêtements PVD, tels que le nitrure de zirconium (ZrN), ont démontré des performances exceptionnelles lors d'essais de résistance à la corrosion, y compris les essais au brouillard salin neutre et les essais CASS.Leur dureté, leur finesse et leur forte adhérence les rendent idéaux pour les environnements difficiles, y compris les zones côtières.
Explication des points clés :
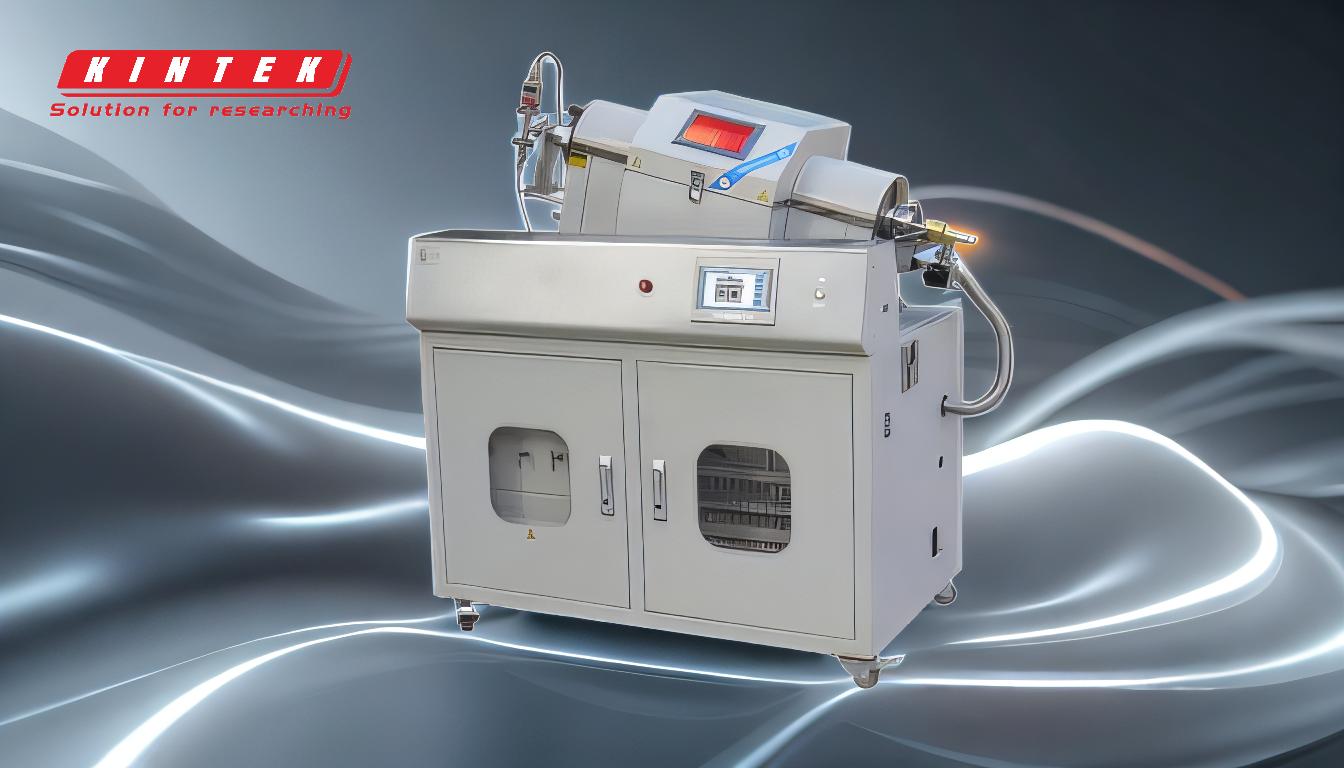
-
Résistance à la corrosion des revêtements PVD:
- Les revêtements PVD sont très résistants à la corrosion et à l'oxydation.Ils forment une couche protectrice qui protège le substrat des facteurs environnementaux qui provoquent la rouille, le ternissement ou la dégradation.
- La finesse des revêtements PVD (0,5 à 5 microns) ne compromet pas leur efficacité.Au contraire, leur extrême finesse les rend difficiles à enlever, ce qui garantit une protection à long terme.
-
Durabilité et dureté:
- Les revêtements PVD sont quatre fois plus durs que le chrome, ce qui les rend très résistants aux rayures et durables.Cette dureté contribue à leur capacité à résister à des conditions difficiles, y compris à des environnements corrosifs.
- La dureté du revêtement est un facteur essentiel de sa durabilité.Par exemple, un revêtement TiN (nitrure de titane) peut augmenter la limite de fatigue et l'endurance d'un substrat tel que l'alliage Ti-6Al-4V.
-
Adhésion et longévité:
- Les revêtements PVD adhèrent fortement au substrat, même en le pénétrant légèrement.Cette forte adhérence garantit que le revêtement reste intact pendant de longues périodes, augmentant ainsi la durée de vie du produit jusqu'à dix fois dans certains cas.
- Le processus de recuit utilisé pour le revêtement PVD garantit que la couche est exempte d'impuretés, ce qui améliore encore sa durabilité et sa résistance à l'usure et à la corrosion.
-
Performance dans les tests de corrosion:
- Les revêtements PVD, tels que le nitrure de zirconium (ZrN), ont démontré des performances exceptionnelles lors d'essais de corrosion normalisés.Par exemple, ils ont dépassé les 1200 heures d'essais au brouillard salin neutre (ASTM B117) et plus de 150 heures d'essais CASS, qui sont des mesures rigoureuses de la résistance à la corrosion.
- Ces résultats mettent en évidence la pertinence des revêtements PVD pour les applications exposées à des environnements corrosifs, tels que les environnements marins ou côtiers.
-
Applications dans des environnements difficiles:
- Les revêtements PVD sont idéaux pour les projets exposés à des environnements difficiles, notamment ceux situés près de la côte, où l'eau salée et l'humidité peuvent accélérer la corrosion.
- Leur capacité à reproduire la finition d'origine des matériaux avec un minimum d'effort les rend polyvalents pour les applications fonctionnelles et esthétiques.
-
Processus et pureté:
- Le procédé PVD consiste à vaporiser un matériau cible sous vide et à le déposer sur le substrat.Cela permet d'obtenir un revêtement pur, exempt d'impuretés, ce qui améliore sa durabilité et sa résistance à la corrosion.
- Ce procédé permet de contrôler avec précision les propriétés du revêtement, notamment l'épaisseur, la dureté et l'adhérence, ce qui garantit des performances optimales pour des applications spécifiques.
En résumé, les revêtements PVD sont très résistants à la corrosion en raison de leur dureté, de leur forte adhérence et de leur pureté.Leurs performances lors d'essais de corrosion rigoureux et leur adaptation aux environnements difficiles en font un excellent choix pour les applications nécessitant une durabilité et une protection durables contre la corrosion.
Tableau récapitulatif :
Caractéristique | Détails |
---|---|
Résistance à la corrosion | Très résistant à la rouille, au ternissement et à l'oxydation ; idéal pour les environnements difficiles. |
Dureté | 4x plus dur que le chrome ; résistant aux rayures et durable. |
Adhésion | Adhère fortement aux substrats, augmentant la longévité jusqu'à 10 fois. |
Performance dans les tests | Dépasse 1200 heures dans les tests de brouillard salin neutre et 150 heures dans les tests CASS. |
Applications | Convient aux environnements marins, côtiers et autres environnements corrosifs. |
Procédé | Revêtements purs, sans impuretés, obtenus par vaporisation sous vide, garantissant la durabilité. |
Améliorez la durabilité de votre projet avec les revêtements PVD. contactez nos experts dès aujourd'hui !