Les revêtements PVD (Physical Vapor Deposition) sont constitués d'une variété d'éléments et de composés, conçus pour répondre à des exigences de performance spécifiques.Ces revêtements combinent généralement des métaux tels que le titane, le zirconium, l'aluminium et l'or avec des éléments non métalliques tels que l'azote, l'oxygène, le carbone et le silicium.Les composés qui en résultent, tels que les nitrures, les oxydes, les carbures et le carbone de type diamant (DLC), offrent des propriétés améliorées telles que la dureté, la résistance à l'usure et la résistance à la corrosion.Le choix des ingrédients dépend de l'application, les revêtements spécialisés étant utilisés dans des secteurs tels que l'aérospatiale, l'automobile et l'électronique.Le procédé PVD consiste à vaporiser un matériau cible solide, qui se condense ensuite sur un substrat pour former un revêtement mince et durable.
Explication des points clés :
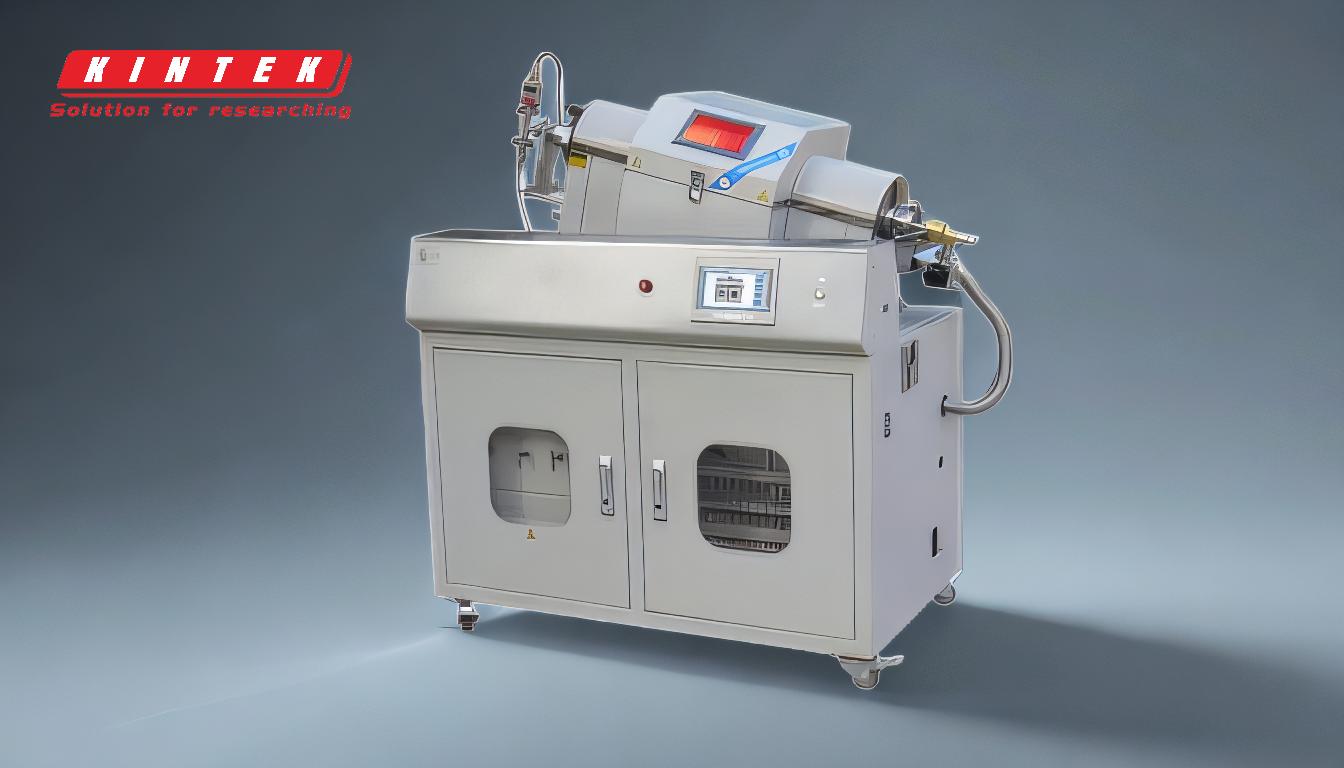
-
Principaux ingrédients des revêtements PVD:
- Métaux:Les métaux couramment utilisés sont le titane, le zirconium, l'aluminium, l'acier inoxydable, le cuivre et l'or.Ces métaux constituent la base du revêtement et contribuent à des propriétés telles que la dureté et la conductivité.
- Éléments non métalliques:L'azote, l'oxygène, le carbone et le silicium sont fréquemment combinés avec des métaux pour créer des composés tels que les nitrures (par exemple, le nitrure de titane), les oxydes, les carbures et les siliciures.
- Matériaux spécialisés:Des matériaux tels que le carbone de type diamant (DLC), le graphite et les composés à base de molybdène sont utilisés pour des applications spécifiques nécessitant une durabilité extrême ou une faible friction.
-
Composés de revêtement PVD courants:
- Revêtements à base de titane:Le nitrure de titane (TiN) est l'un des revêtements PVD les plus utilisés, connu pour sa couleur dorée et son excellente résistance à l'usure.
- Revêtements à base de zirconium:Le nitrure de zirconium (ZrN) offre une grande dureté et une grande résistance à la corrosion. Il est souvent utilisé dans des applications médicales et décoratives.
- Revêtements à base d'aluminium:L'oxyde d'aluminium (Al₂O₃) offre une excellente isolation thermique et électrique, ce qui le rend adapté à l'électronique.
- Carbone semblable à un diamant (DLC):Les revêtements DLC sont appréciés pour leur dureté, leur faible friction et leur biocompatibilité. Ils sont souvent utilisés dans les industries automobile et médicale.
- Or et autres métaux précieux:Les revêtements d'or sont utilisés dans l'électronique aérospatiale pour leur excellente conductivité et leur résistance à la corrosion.
-
Personnalisation pour des applications spécifiques:
-
Les revêtements PVD sont hautement personnalisables, ce qui permet de combiner différents éléments pour obtenir les propriétés souhaitées.C'est le cas, par exemple, dans le domaine de l'aérospatiale :
- Aérospatiale:Les revêtements à base d'or et de titane sont utilisés pour leur conductivité et leur résistance aux environnements extrêmes.
- Automobile:Les revêtements DLC et de nitrure de titane sont appliqués aux composants des moteurs pour les rendre plus résistants à l'usure et réduire les frottements.
- Médical:Les revêtements de nitrure de zirconium et de DLC sont utilisés pour leur biocompatibilité et leur durabilité dans les outils chirurgicaux et les implants.
-
Les revêtements PVD sont hautement personnalisables, ce qui permet de combiner différents éléments pour obtenir les propriétés souhaitées.C'est le cas, par exemple, dans le domaine de l'aérospatiale :
-
Processus de revêtement PVD:
- Le procédé PVD consiste à vaporiser un matériau cible solide (par exemple, du titane ou de l'or) dans une chambre à vide.Le matériau vaporisé se condense ensuite sur le substrat, formant un revêtement mince et uniforme.Ce procédé permet un contrôle précis de la composition et de l'épaisseur du revêtement.
-
Supports pour les revêtements PVD:
-
Les revêtements PVD peuvent être appliqués sur une large gamme de substrats, notamment :
- les métaux:Acier inoxydable, aluminium et titane.
- Plastiques et Nylon:Utilisé dans des applications décoratives et fonctionnelles.
- Céramique et verre:Souvent revêtus pour améliorer la durabilité et les propriétés optiques.
-
Les revêtements PVD peuvent être appliqués sur une large gamme de substrats, notamment :
-
Avantages des revêtements PVD:
- Durabilité:Les revêtements PVD sont très résistants à l'usure, à la corrosion et à l'oxydation.
- Polyvalence:La possibilité de combiner différents matériaux permet d'élaborer des solutions sur mesure pour diverses industries.
- Esthétique:Les revêtements tels que le nitrure de titane et l'or offrent des finitions attrayantes pour les applications décoratives.
En comprenant les ingrédients et les propriétés des revêtements PVD, les acheteurs peuvent sélectionner les matériaux les mieux adaptés à leurs besoins spécifiques, garantissant ainsi des performances optimales et la longévité des composants revêtus.
Tableau récapitulatif :
Catégorie | Exemples de projets | Propriétés |
---|---|---|
Métaux de base | Titane, Zirconium, Aluminium, Or, Acier inoxydable, Cuivre | Dureté, conductivité, résistance à la corrosion |
Éléments non métalliques | Azote, oxygène, carbone, silicium | Forme des nitrures, des oxydes, des carbures, des siliciures |
Matériaux spécialisés | Composés de carbone semblable au diamant (DLC), de graphite et de molybdène | Durabilité extrême, faible frottement |
Composés courants | Nitrure de titane (TiN), nitrure de zirconium (ZrN), oxyde d'aluminium (Al₂O₃) | Résistance à l'usure, résistance à la corrosion, isolation thermique |
Applications | Aérospatiale, automobile, électronique, médical | Conductivité, biocompatibilité, durabilité, esthétique |
Prêt à améliorer vos composants avec des revêtements PVD ? Contactez nos experts dès aujourd'hui pour des solutions sur mesure !