Un insert en fonderie est un composant, souvent en acier ou dans un autre matériau durable, qui est placé dans la cavité d'un moule pour créer des caractéristiques ou des formes spécifiques dans la pièce moulée finale. Ces inserts sont utilisés pour améliorer la fonctionnalité, la durabilité ou la complexité du produit moulé. Ils sont particulièrement utiles dans le moulage sous pression, où la précision et la répétabilité sont essentielles. En incorporant des inserts, les fabricants peuvent réaliser des conceptions complexes, améliorer la résistance des pièces ou intégrer des matériaux supplémentaires sans modifier l'ensemble de la structure du moule.
Explication des points clés :
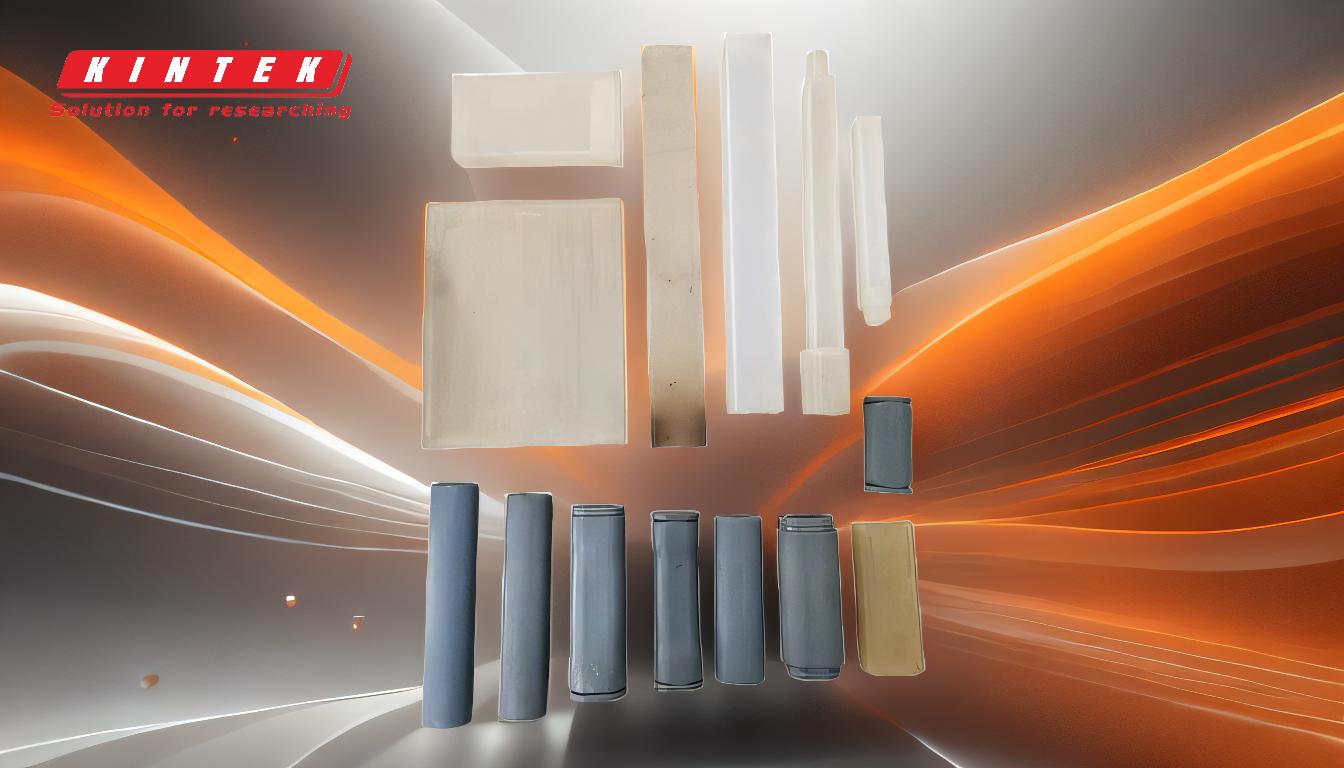
-
Définition d'un insert de moulage:
- Un insert de coulée est une pièce de matériau séparée, généralement en acier, qui est placée dans une cavité de moule avant le début du processus de coulée.
- Il est conçu pour créer des caractéristiques, des formes ou des fonctionnalités spécifiques dans la pièce moulée finale.
-
Objectif de l'utilisation d'inserts:
- Complexité et précision: Les inserts permettent de créer des caractéristiques complexes et précises qu'il serait difficile, voire impossible, de réaliser avec un moule standard.
- Durabilité accrue: Les inserts peuvent être fabriqués dans des matériaux plus durables que le matériau de base du moule, ce qui augmente la durée de vie du moule et la qualité des pièces moulées.
- Intégration des matériaux: Les inserts permettent l'intégration de différents matériaux dans une seule pièce moulée, ce qui peut s'avérer crucial pour les applications nécessitant des propriétés de matériaux spécifiques dans certaines zones.
-
Types d'inserts:
- Inserts en acier: Couramment utilisés en raison de leur solidité et de leur durabilité, en particulier pour le moulage sous pression.
- Plaquettes en céramique: Utilisées dans les applications nécessitant une résistance thermique élevée ou une isolation électrique.
- Plaquettes composites: Ils peuvent combiner les avantages de différents matériaux, tels que la résistance et la légèreté.
-
Placement et conception des inserts:
- Placement de précision: Les inserts doivent être placés avec précision dans l'empreinte du moule pour que la caractéristique souhaitée soit formée avec exactitude dans la pièce finale.
- Considérations relatives à la conception: La conception de l'insert doit tenir compte de facteurs tels que la dilatation thermique, la compatibilité des matériaux et la facilité de retrait ou de remplacement.
-
Avantages de l'utilisation des inserts:
- Efficacité des coûts: L'utilisation d'inserts permet aux fabricants d'éviter des modifications complexes et coûteuses des moules.
- Souplesse: Les inserts offrent une grande souplesse de conception, ce qui permet d'apporter rapidement des modifications ou des mises à jour au moule sans temps d'arrêt important.
- Amélioration de la qualité des pièces: Les inserts permettent d'obtenir des pièces de meilleure qualité, avec de meilleurs états de surface et des dimensions plus précises.
-
Défis et considérations:
- Compatibilité des matériaux: Il est essentiel de s'assurer que le matériau de l'insert est compatible avec le matériau et le procédé de coulée pour éviter les défauts ou les défaillances.
- Gestion thermique: Les inserts doivent pouvoir résister aux conditions thermiques du processus de moulage sans se dégrader ni causer de problèmes dans la pièce finale.
- Maintenance et remplacement: Les inserts peuvent nécessiter un entretien ou un remplacement régulier, en particulier dans les environnements de production à haut volume.
En comprenant ces points clés, un acheteur d'équipement ou de consommables peut prendre des décisions éclairées sur l'utilisation d'inserts dans ses processus de moulage, en s'assurant qu'il obtient les résultats souhaités en termes de qualité des pièces, de rentabilité et de flexibilité de la production.
Tableau récapitulatif :
Aspect clé | Détails |
---|---|
Définition | Pièce de matériau séparée placée dans un moule pour créer des caractéristiques spécifiques. |
Objectif | Atteindre la complexité, la précision, la durabilité et l'intégration des matériaux. |
Types d'inserts | Inserts en acier, en céramique et en composite. |
Avantages | Rentabilité, souplesse de conception et amélioration de la qualité des pièces. |
Défis | Compatibilité des matériaux, gestion thermique et maintenance. |
Prêt à optimiser votre processus de moulage avec des inserts ? Contactez nous dès aujourd'hui pour obtenir des conseils d'experts !