Le dépôt physique en phase vapeur (PVD) et le dépôt chimique en phase vapeur (CVD) sont deux techniques de premier plan utilisées pour déposer des couches minces sur des substrats, mais elles diffèrent considérablement en termes de processus, de matériaux et d'applications. Le dépôt en phase vapeur s'appuie sur des moyens physiques, tels que la vaporisation d'un matériau solide et sa condensation sur un substrat, ce qui permet d'obtenir des revêtements durables et résistants aux températures élevées. Le dépôt en phase vapeur (CVD), quant à lui, implique des réactions chimiques entre des précurseurs gazeux et le substrat, ce qui permet de déposer des couches plus épaisses et plus rugueuses sur une plus large gamme de matériaux. Le choix entre PVD et CVD dépend de facteurs tels que les propriétés souhaitées du revêtement, la compatibilité du substrat et les exigences de l'application.
Explication des points clés :
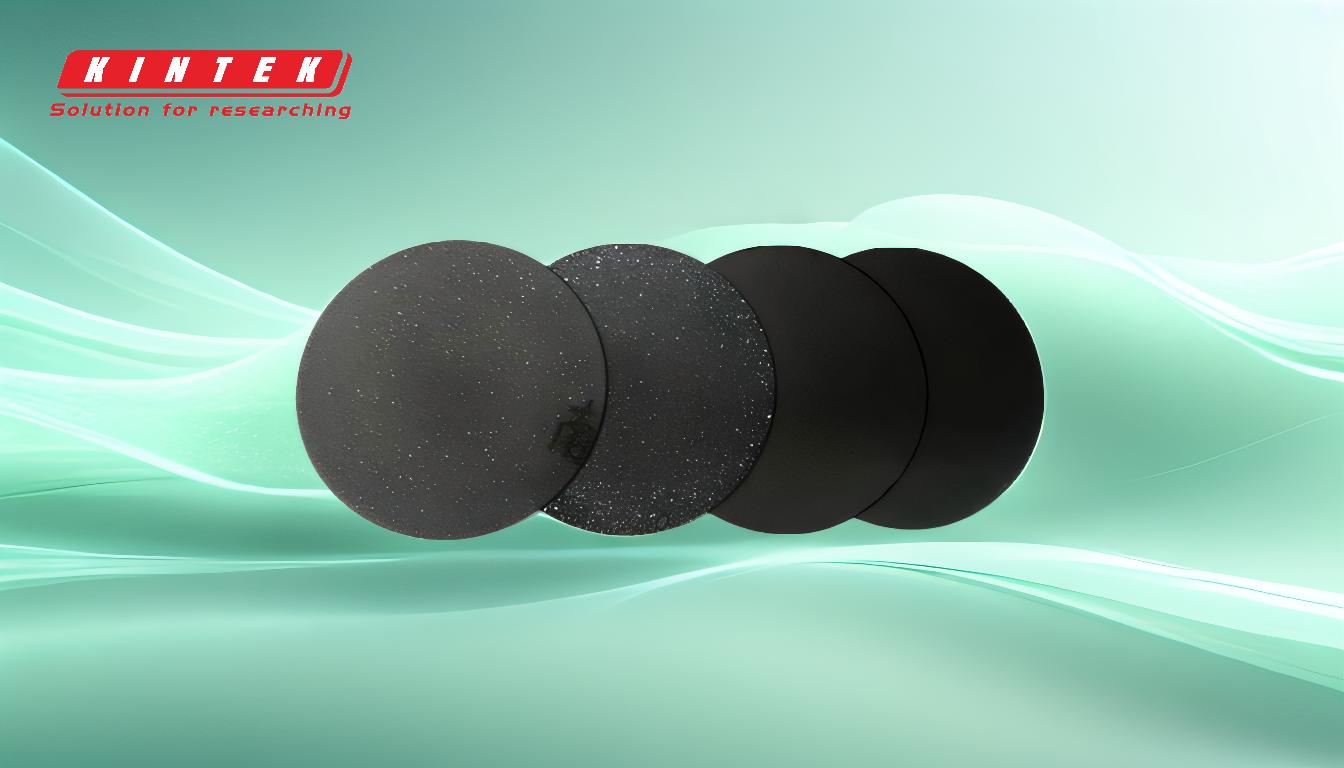
-
Mécanisme du processus:
- PVD: Il utilise des réactions physiques pour convertir un matériau solide en vapeur, qui se condense ensuite sur le substrat pour former un film mince. Ce processus n'implique aucune modification chimique du matériau.
- MCV: Elle repose sur des réactions chimiques entre des précurseurs gazeux et la surface du substrat. La réaction produit un film solide, souvent accompagné de sous-produits tels que des gaz ou des liquides.
-
État des matériaux:
- PVD: Utilise des matériaux de revêtement solides qui sont vaporisés et déposés sur le substrat.
- MCV: Les matériaux de revêtement gazeux réagissent chimiquement avec le substrat pour former la couche souhaitée.
-
Exigences en matière de température:
- PVD: Fonctionne à des températures relativement basses, généralement entre 250°C et 450°C, ce qui le rend adapté aux substrats sensibles à la température.
- MCV: Nécessite des températures plus élevées, allant de 450°C à 1050°C, ce qui peut limiter son utilisation avec certains matériaux, mais permet de déposer des revêtements plus épais et plus robustes.
-
Caractéristiques du revêtement:
- PVD: Produit des revêtements minces, lisses et très durables avec une excellente adhérence et une résistance aux températures élevées et à l'usure.
- MCV: Permet d'obtenir des revêtements plus épais et plus rugueux qui peuvent être appliqués à une plus grande variété de matériaux, y compris des formes complexes et des surfaces internes.
-
Adéquation de l'application:
- PVD: Idéal pour les applications nécessitant une grande précision, une durabilité et une résistance aux conditions extrêmes, telles que les outils de coupe, les appareils médicaux et les composants aérospatiaux.
- MCV: Convient aux applications nécessitant des revêtements uniformes sur des géométries complexes, telles que les dispositifs à semi-conducteurs, les composants optiques et les revêtements de protection pour les outils industriels.
-
Avantages et limites:
-
Avantages du dépôt en phase vapeur (PVD):
- Grande durabilité et résistance à l'usure.
- Excellente adhérence et finition de surface lisse.
- Le traitement à basse température réduit les dommages au substrat.
-
Limites du PVD:
- Limité au dépôt en ligne de mire, ce qui rend difficile le revêtement de géométries complexes.
- Produit généralement des revêtements plus fins que le dépôt en phase vapeur (CVD).
-
Avantages de la MCV:
- Peut revêtir uniformément des formes complexes et des surfaces internes.
- Permet d'obtenir des revêtements plus épais et plus conformes.
- Compatible avec une plus large gamme de matériaux.
-
Limites des MCV:
- Des températures plus élevées peuvent endommager les substrats sensibles à la température.
- Les sous-produits chimiques peuvent nécessiter une manipulation et une élimination supplémentaires.
-
Avantages du dépôt en phase vapeur (PVD):
-
Applications industrielles:
- PVD: Couramment utilisé dans les industries nécessitant des revêtements de haute performance, telles que l'automobile (composants de moteurs), l'aérospatiale (pales de turbines) et la médecine (instruments chirurgicaux).
- MCV: Largement appliqué dans la fabrication des semi-conducteurs (circuits intégrés), l'optique (revêtements antireflets) et les revêtements résistants à l'usure pour les outils industriels.
En comprenant ces différences clés, les acheteurs d'équipements et de consommables peuvent prendre des décisions éclairées en fonction des exigences spécifiques de leurs applications, telles que l'épaisseur du revêtement, la compatibilité avec le substrat et les conditions environnementales.
Tableau récapitulatif :
Aspect | PVD | MCV |
---|---|---|
Mécanisme du processus | Vaporisation et condensation physiques des matériaux solides. | Réactions chimiques entre les précurseurs gazeux et le substrat. |
État des matériaux | Matériaux solides vaporisés et déposés. | Les matières gazeuses réagissent chimiquement pour former des films solides. |
Plage de température | 250°C à 450°C (plus bas, adapté aux substrats sensibles). | 450°C à 1050°C (plus élevé, permet d'obtenir des revêtements plus épais). |
Caractéristiques du revêtement | Mince, lisse, durable et résistant à l'usure. | Plus épais, plus rugueux et applicable aux géométries complexes. |
Applications | Outils de coupe, dispositifs médicaux, composants aérospatiaux. | Dispositifs à semi-conducteurs, composants optiques, outils industriels. |
Avantages | Grande durabilité, finition lisse, traitement à basse température. | Revêtements uniformes sur des formes complexes, films plus épais, plus grande compatibilité avec les matériaux. |
Limites | Dépôt en ligne de mire, revêtements plus fins. | Températures élevées, sous-produits chimiques. |
Besoin d'aide pour choisir entre PVD et CVD pour votre application ? Contactez nos experts dès aujourd'hui pour un accompagnement personnalisé !