Les revêtements PVD (Physical Vapor Deposition) sont connus pour leur grande dureté, qui se situe généralement entre 1500 HV (dureté Vickers) et 4500 HV, selon le type de revêtement, le matériau du substrat et la méthode PVD utilisée.À titre de comparaison, les aciers au carbone ont une dureté d'environ 250 HV, tandis que les aciers nitrurés ou nickelés/chromés ont une dureté comprise entre 600 HV et 1000 HV.Les revêtements PVD, tels que le TiN (nitrure de titane), sont particulièrement appréciés pour leur capacité à améliorer la résistance à l'usure, la résistance à la corrosion et la durabilité.Dans certains cas, des revêtements spécialisés comme le DLC (Diamond-Like Carbon) peuvent atteindre des valeurs de dureté allant jusqu'à 9000 HV.La dureté des revêtements PVD est un facteur essentiel de leur performance, ce qui les rend appropriés pour des applications exigeantes dans des industries telles que l'automobile, l'aérospatiale et le médical.
Explication des points clés :
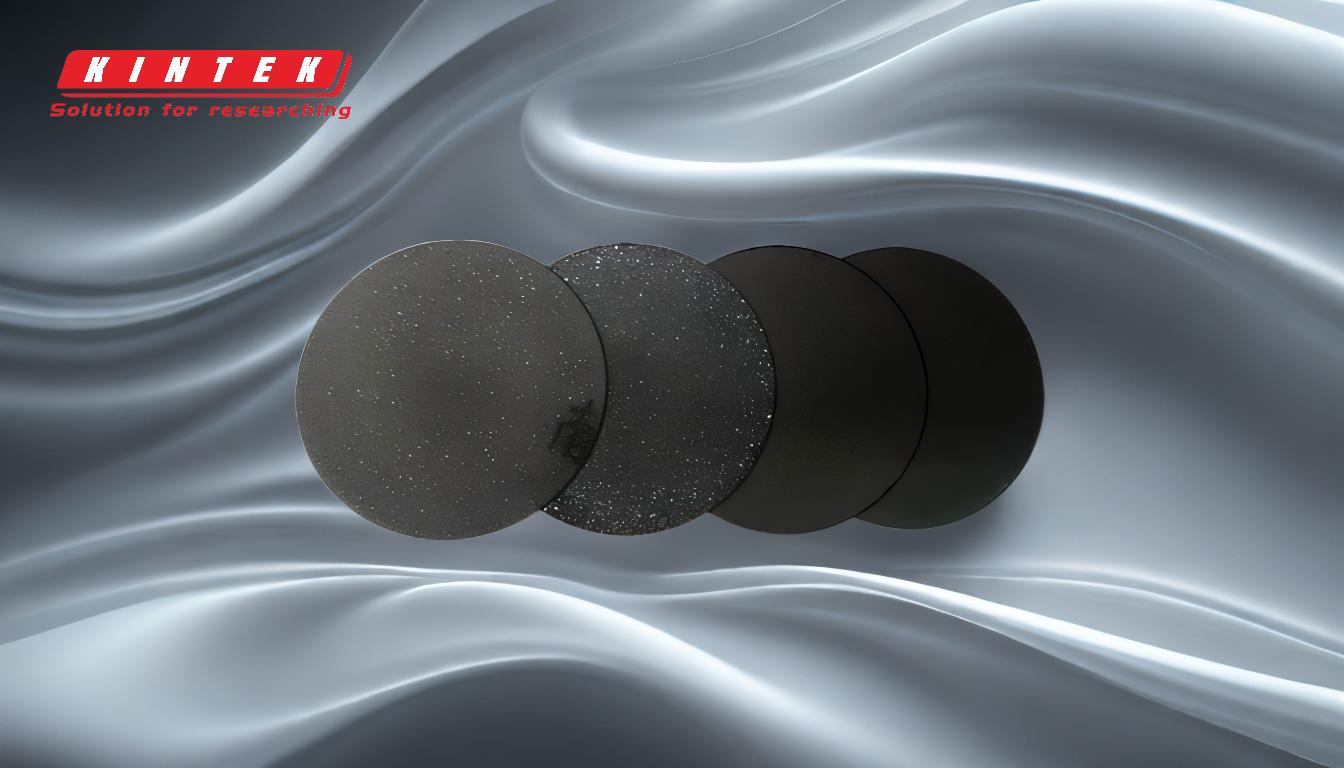
-
Gamme de dureté des revêtements PVD:
- Les revêtements PVD ont généralement une dureté comprise entre 1500 HV à 4500 HV en fonction du matériau de revêtement et du processus spécifiques.
- A titre de référence, 900 HV correspond à 67 HRC (Rockwell C) ce qui est nettement plus dur que de nombreux matériaux courants tels que l'acier au carbone (250 HV) ou les aciers nitrurés (600-1000 HV).
- Les revêtements spécialisés, tels que DLC (Diamond-Like Carbon) peut atteindre des valeurs de dureté encore plus élevées, jusqu'à 9000 HV .
-
Facteurs influençant la dureté:
-
La dureté des revêtements PVD dépend de plusieurs facteurs :
- Matériau du revêtement:Les différents matériaux (par exemple, TiN, TiCN, CrN, DLC) ont des niveaux de dureté variables.
- Matériau du substrat:Le matériau sous-jacent peut influencer les propriétés du revêtement.Par exemple, les revêtements TiN sur l'alliage Ti-6Al-4V améliorent les limites de fatigue et l'endurance.
- Méthode PVD:Le procédé PVD spécifique (par exemple, pulvérisation cathodique, évaporation à l'arc) et les compétences de l'opérateur peuvent influer sur la dureté du revêtement.
- Épaisseur:Les revêtements PVD sont très fins (0,5-5 microns), mais leur dureté est optimisée pour la performance.
-
La dureté des revêtements PVD dépend de plusieurs facteurs :
-
Comparaison avec d'autres matériaux:
- Aciers au carbone:Ont généralement une dureté d'environ 250 HV (25 HRC) .
- Aciers nitrurés ou nickelés/chromés:Plage entre 600 HV et 1000 HV .
- Revêtements PVD:Au 1500-4500 HV Les revêtements PVD sont nettement plus durs, ce qui les rend idéaux pour les applications nécessitant une résistance à l'usure et une durabilité élevées.
-
Applications et avantages:
- Les revêtements PVD sont largement utilisés dans des secteurs tels que l'automobile, l'aérospatiale et le secteur médical en raison de leur grande dureté, de leur résistance à l'usure et à la corrosion.
- Ils offrent également un faible frottement et un aspect esthétique amélioré Ils conviennent donc aussi bien à des fins fonctionnelles que décoratives.
-
Dureté et résistance à l'usure:
- Si une dureté élevée est généralement associée à une une meilleure résistance à l'usure il n'y a pas de relation directe entre les deux.Des valeurs de dureté supérieures au seuil optimal peuvent indiquer décarburation ce qui peut réduire les performances.
- Les revêtements PVD permettent de trouver un équilibre entre la dureté et d'autres propriétés comme la ténacité et l'adhérence pour garantir une durabilité à long terme.
-
Revêtements spécialisés:
- Revêtements DLC:Ils font partie des revêtements PVD les plus durs, avec des valeurs de dureté atteignant jusqu'à 9000 HV .Ils sont particulièrement appréciés pour leur faible frottement et une excellente résistance à l'usure .
- Revêtements TiN:Couramment utilisés pour leur aspect aspect doré et une dureté élevée, ils sont idéaux pour les outils de coupe, les moules et les applications décoratives.
-
Mesure de la dureté:
- La dureté est généralement mesurée à l'aide de la méthode dureté Vickers (HV) qui convient aux revêtements minces.À titre de comparaison, Rockwell C (HRC) est également utilisé, 900 HV équivalant à 67 HRC.
-
Dureté et résistance à la corrosion optimales:
- Les revêtements PVD permettent d'atteindre un niveau de dureté optimal qui améliore leur résistance à la résistance à la corrosion .Une dureté excessive peut conduire à la formation de phases dures, ce qui peut compromettre les performances.
En résumé, la dureté des revêtements PVD est une propriété essentielle qui leur confère une grande durabilité et les rend aptes à des applications exigeantes.Leur dureté varie de 1500 HV à 4500 HV, les revêtements spécialisés comme le DLC pouvant atteindre 9000 HV.Cette dureté exceptionnelle, associée à une résistance à l'usure et à la corrosion et à un faible frottement, rend les revêtements PVD inestimables dans diverses industries.
Tableau récapitulatif :
Aspect | Détails |
---|---|
Plage de dureté | 1500-4500 HV (jusqu'à 9000 HV pour les revêtements DLC) |
Matériaux de comparaison | Acier au carbone : 250 HV ; aciers nitrurés : 600-1000 HV |
Principaux avantages | Résistance élevée à l'usure et à la corrosion, faible frottement et durabilité |
Applications | Automobile, aérospatiale, applications médicales et décoratives |
Revêtements spécialisés | TiN (nitrure de titane), DLC (Diamond-Like Carbon) |
Mesures | Dureté Vickers (HV) ; 900 HV = 67 HRC |
Découvrez comment les revêtements PVD peuvent améliorer les performances de vos matériaux. contactez nos experts dès aujourd'hui !