Le procédé de moulage par injection est une méthode de fabrication très efficace qui permet de produire en grande quantité des pièces en plastique de forme complexe.Il consiste à faire fondre la matière plastique, à l'injecter dans un moule de presse Les moules de presse sont des moules dans lesquels les pièces sont pressées sous haute pression, refroidies pour se solidifier, puis éjectées du produit fini.Ce procédé est largement utilisé dans l'industrie pour sa précision, sa répétabilité et sa capacité à produire des dessins complexes.Vous trouverez ci-dessous une explication détaillée, étape par étape, du processus de moulage par injection.
Points clés expliqués :
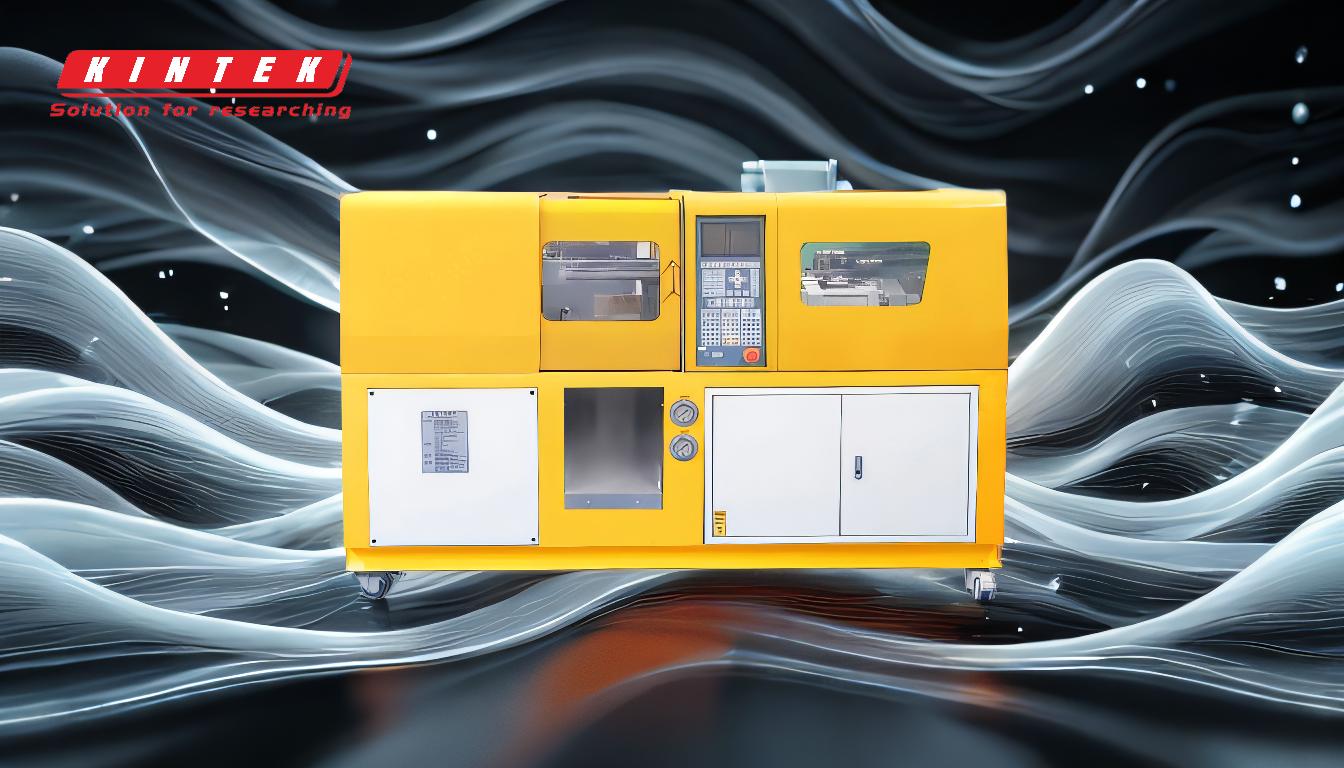
-
Préparation et alimentation des matériaux
- Les boulettes ou granulés de plastique sont introduits dans la trémie de la machine de moulage par injection.
- La matière est ensuite acheminée dans le cylindre, où elle est chauffée et mélangée par une vis rotative.
- La vis assure une fusion et une homogénéisation uniformes de la matière plastique.
-
Fusion et plastification
- À l'intérieur du tonneau, la matière plastique est chauffée jusqu'à son point de fusion, ce qui la transforme en un état fondu.
- La vis continue de mélanger et de comprimer le plastique fondu, garantissant une viscosité et une température constantes.
- Cette étape est essentielle pour obtenir des pièces moulées de haute qualité.
-
Injection dans la cavité du moule
- Une fois que le plastique est entièrement fondu, la vis se déplace vers l'avant, agissant comme un piston pour injecter le matériau fondu dans la cavité du moule.
- Une pression élevée est appliquée pour s'assurer que le matériau remplit chaque détail du moule, y compris les géométries complexes.
- Le moule est maintenu fermé par une unité de serrage pour résister à la pression d'injection.
-
Refroidissement et solidification
- Une fois la cavité du moule remplie, le plastique fondu commence à refroidir et à se solidifier, prenant ainsi la forme du moule.
- Le temps de refroidissement dépend des propriétés du matériau, de l'épaisseur de la pièce et de la conception du moule.
- Un refroidissement adéquat est essentiel pour éviter les défauts tels que le gauchissement ou les marques d'enfoncement.
-
Ouverture du moule et éjection
- Une fois la pièce solidifiée, le moule s'ouvre et des broches d'éjection poussent le produit fini hors de la cavité du moule.
- La pièce éjectée est alors récupérée pour être transformée ou emballée.
- Le moule se referme et le cycle se répète pour la pièce suivante.
-
Post-traitement (si nécessaire)
- Certaines pièces peuvent nécessiter des étapes supplémentaires telles que l'ébarbage, la peinture ou l'assemblage.
- Ces étapes permettent de s'assurer que le produit final répond aux spécifications et aux normes de qualité souhaitées.
Explication détaillée :
-
Préparation et alimentation des matériaux
Le processus commence par la sélection de la matière plastique appropriée, qui se présente généralement sous la forme de pastilles ou de granulés.Ces matières sont chargées dans la trémie, qui les introduit dans le cylindre de la machine de moulage par injection.Le cylindre est équipé d'une vis rotative qui transporte la matière vers l'avant tout en la chauffant à la température requise.Cette étape permet de s'assurer que le matériau est prêt pour la phase suivante de fusion et de plastification. -
Fusion et plastification
À l'intérieur du cylindre, la matière plastique est soumise à la chaleur et au cisaillement mécanique de la vis.La combinaison de la chaleur et de la friction fait fondre le plastique, le transformant en un fluide visqueux.La conception de la vis assure un mélange complet, éliminant toute incohérence dans le matériau.Cette étape est cruciale car la qualité du plastique fondu influe directement sur les propriétés du produit final, telles que la résistance, l'état de surface et la précision dimensionnelle. -
Injection dans la cavité du moule
Une fois le plastique entièrement fondu, la phase d'injection commence.La vis se déplace vers l'avant, agissant comme un piston pour injecter le matériau fondu dans la cavité du moule.Le moule est conçu avec précision pour créer la forme souhaitée de la pièce.Une pression élevée est appliquée pendant l'injection pour garantir que le matériau remplit toutes les zones du moule, y compris les détails fins et les sections minces.L'unité de fermeture maintient le moule hermétiquement fermé pour résister à la forte pression d'injection, évitant ainsi toute fuite ou déformation. -
Refroidissement et solidification
Une fois la cavité du moule remplie, la phase de refroidissement commence.Le plastique fondu commence à refroidir et à se solidifier, prenant la forme du moule.Le temps de refroidissement est un facteur critique dans le processus de moulage par injection, car il détermine la durée du cycle et affecte la qualité de la pièce.Un refroidissement adéquat garantit que la pièce se solidifie uniformément, minimisant ainsi les défauts tels que le gauchissement, les marques d'enfoncement ou les contraintes internes.Le système de refroidissement à l'intérieur du moule, qui utilise souvent des canaux d'eau, permet de réguler la température et d'accélérer le processus. -
Ouverture du moule et éjection
Une fois la pièce suffisamment refroidie et solidifiée, le moule s'ouvre et le produit fini est éjecté.Des broches ou des plaques d'éjection sont utilisées pour pousser la pièce hors de la cavité du moule.Le moule se referme ensuite et le cycle se répète pour la pièce suivante.Cette étape exige de la précision pour que la pièce soit éjectée sans dommage et que le moule soit prêt pour l'injection suivante. -
Post-traitement (si nécessaire)
En fonction de l'application, certaines pièces peuvent nécessiter des étapes de post-traitement supplémentaires.Il peut s'agir de rogner l'excès de matière (flash), de peindre ou de revêtir à des fins esthétiques, ou d'assembler plusieurs composants.Le post-traitement permet de s'assurer que le produit final répond aux spécifications et aux normes de qualité requises.
Conclusion :
Le procédé de moulage par injection est une méthode polyvalente et efficace pour produire des pièces en plastique de haute qualité à géométrie complexe.En suivant les étapes de préparation des matériaux, de fusion, d'injection, de refroidissement, d'éjection et de post-traitement, les fabricants peuvent obtenir des résultats cohérents et précis.Ce processus est largement utilisé dans toutes les industries en raison de sa capacité à produire de grandes quantités de pièces avec un minimum de déchets et une grande répétabilité.
Tableau récapitulatif :
Étape | Description de l'étape |
---|---|
1.Préparation des matériaux | Les granulés de plastique sont introduits dans la trémie, chauffés et mélangés dans le tonneau. |
2.Fusion et plastification | La matière est fondue et homogénéisée par la vis pour obtenir une viscosité constante. |
3.Injection dans le moule | Le plastique fondu est injecté sous haute pression dans la cavité du moule. |
4.Refroidissement et solidification | Le plastique se refroidit et se solidifie pour prendre la forme souhaitée. |
5.Ouverture du moule et éjection | Le moule s'ouvre et les broches d'éjection poussent la pièce finie. |
6.Post-traitement | Des étapes supplémentaires, telles que l'ébarbage ou la peinture, peuvent être nécessaires pour obtenir la qualité finale. |
Prêt à optimiser votre processus de fabrication ? Contactez-nous dès aujourd'hui pour en savoir plus sur les solutions de moulage par injection. pour en savoir plus sur les solutions de moulage par injection !