Les revêtements PVD (Physical Vapor Deposition) sont réputés pour leur durabilité exceptionnelle et leur résistance à l'usure, à la corrosion et à l'écaillage.Ces revêtements se lient au niveau moléculaire avec le substrat, créant une couche solide et fine très résistante aux forces extérieures.En raison de leur dureté, de leur résistance à l'usure et de leur faible coefficient de frottement, les revêtements PVD sont moins susceptibles de s'écailler que les revêtements traditionnels.Leur capacité à résister à des environnements difficiles, notamment à des températures élevées et à des conditions corrosives, renforce encore leur durabilité.Bien qu'aucun revêtement ne soit totalement à l'abri des dommages, les revêtements PVD comptent parmi les options les plus durables disponibles, ce qui les rend idéaux pour les applications exigeantes dans des secteurs tels que l'automobile, l'aérospatiale et la médecine.
Explication des points clés :
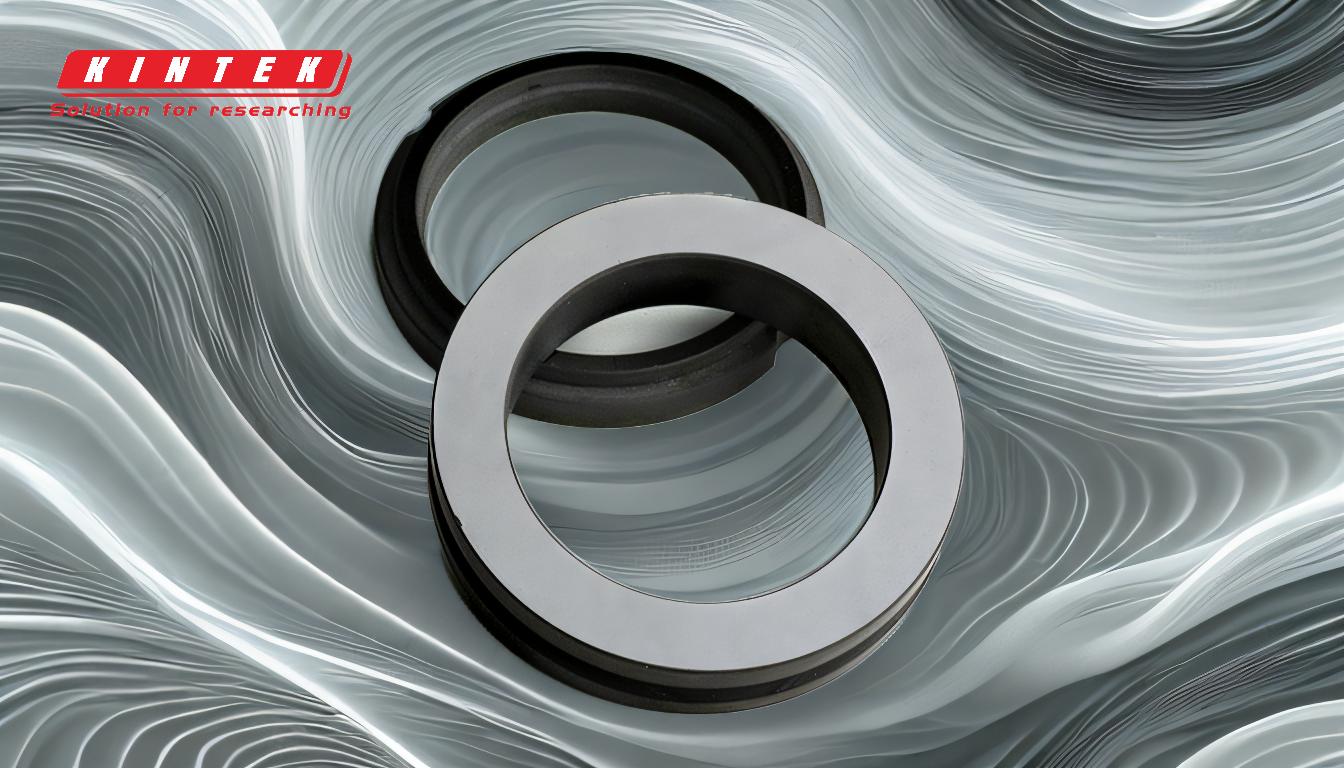
-
Liaison moléculaire et adhésion
- Les revêtements PVD forment une liaison moléculaire avec le substrat, créant ainsi un lien solide et durable.
- Ce mécanisme de liaison garantit que le revêtement adhère étroitement à la surface, ce qui le rend résistant à l'écaillage, même sous l'effet d'une contrainte mécanique ou d'un impact.
-
Dureté et résistance à l'usure
- Les revêtements PVD sont connus pour leur grande dureté, qui dépasse souvent celle des revêtements traditionnels.
- La dureté du revêtement contribue à sa capacité à résister à l'usure, à l'abrasion et à l'écaillage, même dans des environnements soumis à de fortes contraintes.
-
Couche mince et durable
- Les revêtements PVD sont extrêmement fins, de l'ordre de 0,5 à 5 microns.
- Malgré leur finesse, ces revêtements sont très durables et difficiles à enlever, ce qui réduit encore le risque d'écaillage.
-
Résistance à la corrosion et à l'oxydation
- L'environnement sous vide pendant le processus PVD élimine la contamination et empêche l'oxydation, ce qui donne un revêtement très résistant à la corrosion et à la dégradation de l'environnement.
- Cette résistance améliore la durabilité et la longévité globales du revêtement, réduisant le risque d'écaillage au fil du temps.
-
Applications dans des industries exigeantes
- Les revêtements PVD sont largement utilisés dans des secteurs tels que l'automobile, l'aérospatiale et la médecine, où la durabilité et la résistance à l'usure sont essentielles.
- Leur capacité à résister aux conditions difficiles et aux contraintes mécaniques les rend moins susceptibles de s'écailler que d'autres revêtements.
-
Comparaison avec les revêtements traditionnels
- Contrairement aux finitions traditionnelles, les revêtements PVD sont nettement plus durs et plus résistants à l'usure et à la corrosion.
- Cette durabilité supérieure les rend moins susceptibles de s'écailler, même lorsqu'ils sont soumis à une manipulation brutale ou à des conditions extrêmes.
-
Performance dans le monde réel
- Il a été démontré que les revêtements PVD améliorent la limite de fatigue et l'endurance des matériaux, tels que l'alliage Ti-6Al-4V, dans des proportions significatives.
- Ces améliorations de performance démontrent en outre la capacité du revêtement à résister aux dommages, y compris à l'écaillage, dans des conditions réelles.
En résumé, bien qu'aucun revêtement ne soit totalement à l'abri des dommages, les revêtements PVD comptent parmi les options les plus durables et les plus résistantes à l'écaillage.Leur liaison moléculaire, leur dureté, leur finesse et leur résistance à la corrosion et à l'usure en font un excellent choix pour les applications où la durabilité et la longévité sont primordiales.
Tableau récapitulatif :
Caractéristique principale | Description |
---|---|
Liaison moléculaire | Forme une liaison moléculaire forte avec le substrat, réduisant ainsi les risques d'écaillage. |
Dureté et résistance à l'usure | Dépasse les revêtements traditionnels, offrant une résistance supérieure à l'usure et à l'abrasion. |
Couche fine et durable | Extrêmement fine (0,5-5 microns) et pourtant très durable, elle minimise l'écaillage. |
Résistance à la corrosion | Résiste à la corrosion et à l'oxydation, améliorant ainsi la longévité dans les environnements difficiles. |
Applications industrielles | Largement utilisé dans les secteurs de l'automobile, de l'aérospatiale et de la médecine pour sa durabilité et ses performances. |
Performance dans le monde réel | Améliore les limites de fatigue et l'endurance, réduisant les dommages dans des conditions extrêmes. |
Vous souhaitez améliorer la durabilité de vos matériaux à l'aide de revêtements PVD ? Contactez nous dès aujourd'hui pour en savoir plus !