Les revêtements PVD (Physical Vapor Deposition) sont très efficaces pour prévenir la rouille grâce à leurs excellentes propriétés de résistance à la corrosion.Ces revêtements sont largement utilisés dans des secteurs tels que l'aérospatiale, l'automobile et les appareils médicaux, car ils forment une fine couche durable qui protège le matériau sous-jacent des facteurs environnementaux tels que l'humidité et l'oxydation.Les revêtements PVD, tels que le nitrure de zirconium (ZrN), ont démontré une résistance exceptionnelle à la corrosion, dépassant les 1200 heures dans les tests de brouillard salin neutre (ASTM B117) et plus de 150 heures dans les tests CASS.La finesse des revêtements PVD, de 0,5 à 5 microns, ne compromet pas leur efficacité, car ils sont très adhérents et difficiles à enlever.En outre, les revêtements PVD peuvent reproduire la finition d'origine des matériaux, ce qui les rend à la fois fonctionnels et esthétiques.Dans l'ensemble, les revêtements PVD constituent une solution fiable pour la prévention de la rouille et prolongent considérablement la durée de vie des produits.
Explication des points clés :
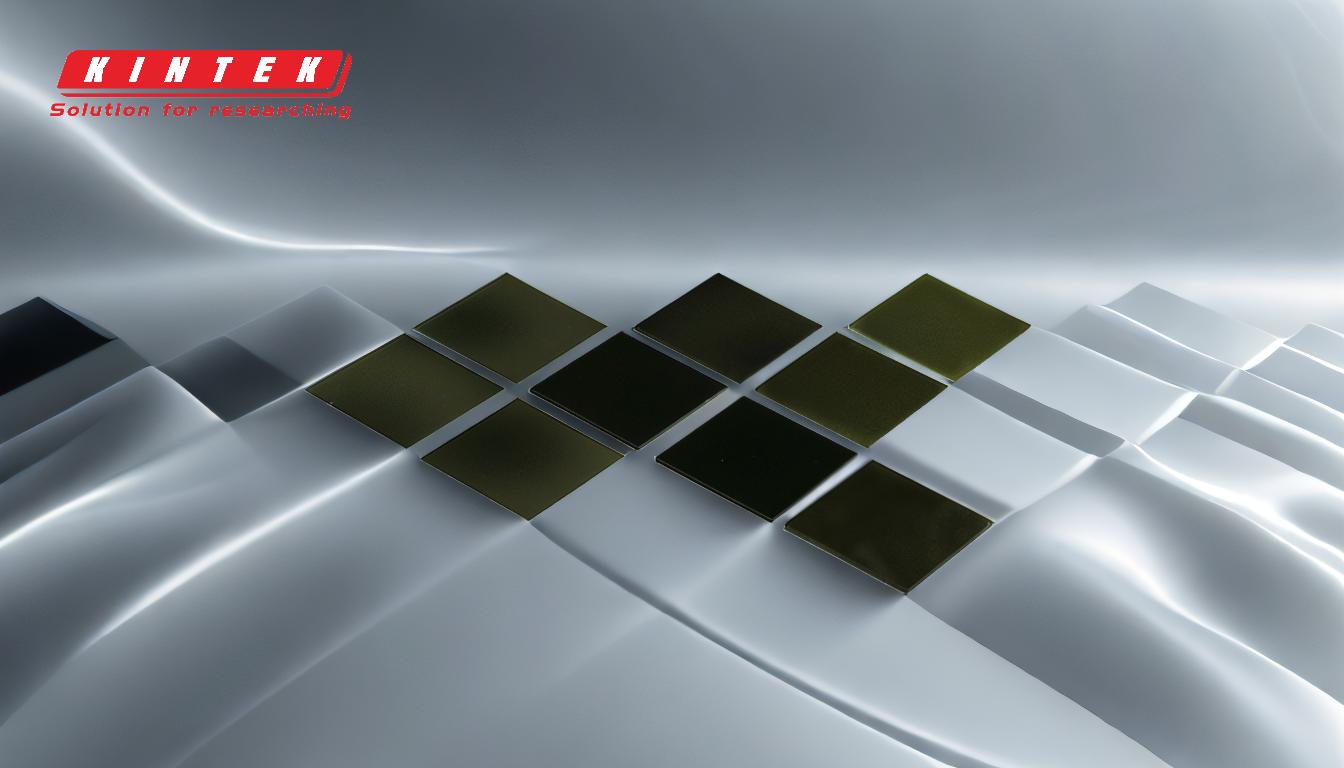
-
Résistance à la corrosion des revêtements PVD
- Les revêtements PVD sont spécialement conçus pour résister à la corrosion et à l'oxydation, ce qui les rend très efficaces pour prévenir la rouille.
- Ils forment une barrière protectrice qui protège le matériau sous-jacent des facteurs environnementaux tels que l'humidité, le sel et les produits chimiques.
- Par exemple, les revêtements en nitrure de zirconium (ZrN) ont été testés pour résister à plus de 1 200 heures de brouillard salin neutre (ASTM B117), qui est une mesure standard de la résistance à la corrosion.
-
Une couche fine mais durable
- Les revêtements PVD sont extrêmement fins, de l'ordre de 0,5 à 5 microns, mais leur finesse ne compromet pas leurs capacités de protection.
- Les revêtements sont très adhérents, c'est-à-dire qu'ils se lient fortement au substrat, ce qui les rend difficiles à enlever et garantit une protection durable.
- Malgré leur finesse, les revêtements PVD peuvent reproduire la finition d'origine des matériaux, en préservant à la fois la fonctionnalité et l'esthétique.
-
Applications dans les environnements sujets à la rouille
- Les revêtements PVD sont utilisés dans les industries où la prévention de la rouille est essentielle, telles que l'automobile (roues, pistons, etc.), l'aérospatiale et les appareils médicaux.
- Ils sont également appliqués aux outils et équipements exposés à des conditions difficiles, tels que les outils de coupe, les matrices et les moules, où la résistance à la corrosion est essentielle à la longévité.
- La capacité des revêtements PVD à résister à des conditions extrêmes, telles que le brouillard salin et les environnements acides, les rend idéaux pour les applications marines, industrielles et extérieures.
-
Des performances supérieures à celles des méthodes traditionnelles
- Les revêtements PVD constituent une alternative plus écologique aux méthodes traditionnelles telles que le chromage, car ils ne produisent pas de substances toxiques lors de l'application.
- Ils offrent une meilleure résistance à la corrosion et une plus grande durabilité que la galvanoplastie, comme en témoignent leurs performances lors de tests normalisés tels que le CASS (Copper-Accelerated Acetic Acid-Salt Spray).
- La durée de vie accrue des produits revêtus par PVD (jusqu'à 25 ans dans certains cas) souligne leur efficacité dans la prévention de la rouille et d'autres formes de dégradation.
-
Compatibilité avec de nombreux matériaux
- Les revêtements PVD peuvent être appliqués sur une large gamme de substrats, y compris les métaux, les polymères et les céramiques, ce qui les rend polyvalents pour diverses applications.
- Les propriétés du revêtement peuvent être adaptées aux besoins spécifiques du substrat, ce qui garantit une protection optimale contre la rouille et d'autres formes de corrosion.
- Par exemple, des revêtements tels que le nitrure de titane (TiN) offrent non seulement une résistance à la corrosion, mais améliorent également la dureté et la résistance à l'usure du matériau.
-
Rentabilité à long terme
- En prévenant la rouille et en prolongeant la durée de vie des produits, les revêtements PVD réduisent la nécessité de remplacements et d'entretiens fréquents, ce qui permet de réaliser des économies à long terme.
- Leur durabilité et leur résistance à l'usure en font une solution rentable pour les industries qui ont besoin de matériaux de haute performance.
- La capacité à reproduire la finition d'origine des matériaux réduit également la nécessité de recourir à des processus de finition supplémentaires, ce qui permet de réduire encore les coûts.
En conclusion, les revêtements PVD constituent un excellent choix pour prévenir la rouille en raison de leur résistance supérieure à la corrosion, de leur durabilité et de leur polyvalence.Leur nature fine mais très adhérente garantit une protection durable, tandis que leur compatibilité avec divers substrats et applications en fait une solution pratique pour les industries qui ont besoin de prévenir la rouille.
Tableau récapitulatif :
Caractéristique | Détails |
---|---|
Résistance à la corrosion | Résiste à plus de 1200 heures d'essais au brouillard salin neutre (ASTM B117). |
Épaisseur | 0,5 à 5 microns, très adhérent et durable. |
Applications | Automobile, aérospatiale, appareils médicaux, marine et équipements industriels. |
Compatibilité des matériaux | Métaux, polymères, céramiques - sur mesure pour une protection optimale. |
Rentabilité | Réduit les coûts d'entretien et de remplacement, prolonge la durée de vie des produits. |
Protégez vos produits de la rouille avec les revêtements PVD- contactez-nous dès aujourd'hui pour en savoir plus !