Le dépôt physique en phase vapeur (PVD) et le dépôt chimique en phase vapeur (CVD) sont deux techniques de revêtement de couches minces très répandues qui permettent de déposer des couches de matériaux sur des substrats afin d'en améliorer les propriétés.L'épaisseur de ces revêtements varie en fonction de l'application, les revêtements PVD étant généralement compris entre 0,25 et 5 microns et les revêtements CVD étant généralement plus épais, de 5 à 10 microns.Ces épaisseurs sont soigneusement choisies pour garantir que les revêtements apportent les avantages fonctionnels souhaités sans altérer les spécifications des pièces sous-jacentes.Il est essentiel de comprendre les plages d'épaisseur des revêtements PVD et CVD pour sélectionner la méthode de revêtement appropriée pour des applications spécifiques, que ce soit à des fins décoratives, d'améliorations fonctionnelles ou de mesures de protection.
Explication des points clés :
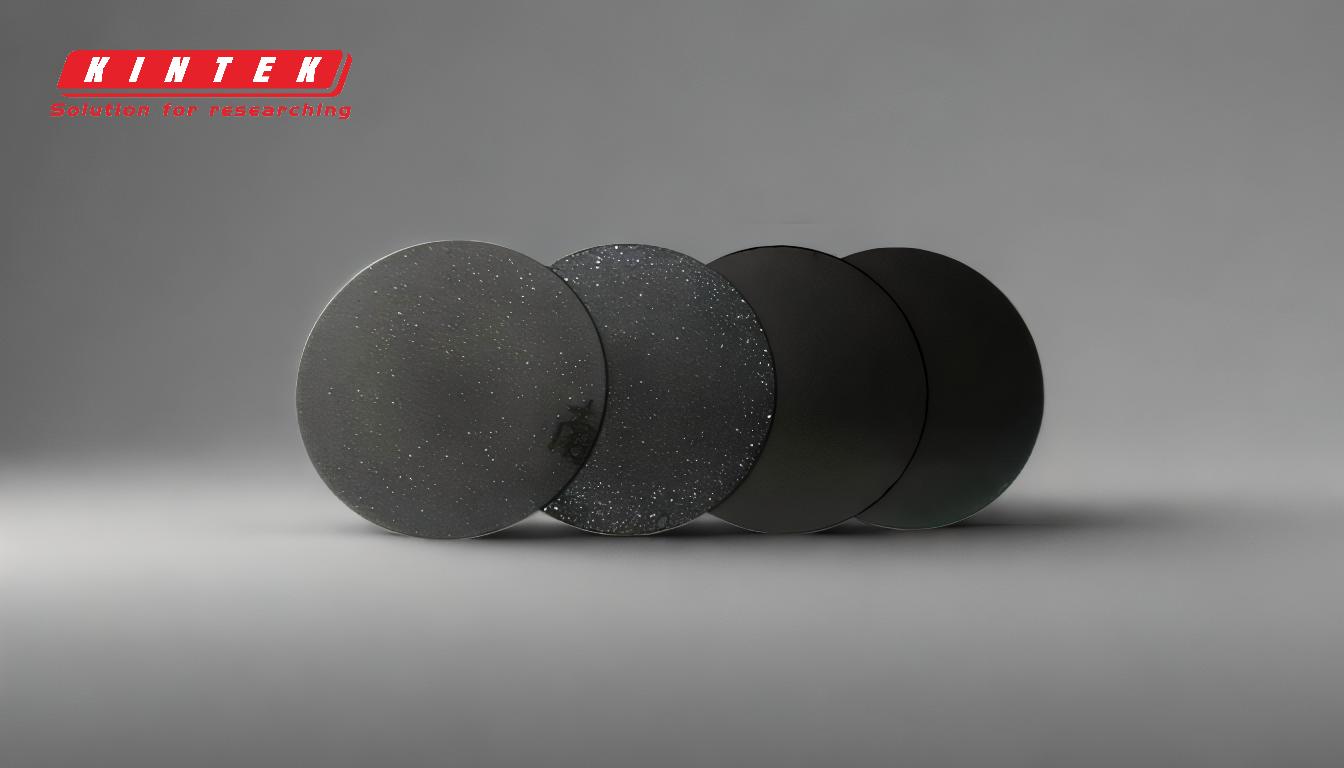
-
Épaisseur du revêtement PVD :
- Les revêtements PVD sont des films minces, dont l'épaisseur est généralement comprise entre 0,25 à 5 microns d'épaisseur.
-
L'épaisseur exacte dépend de l'application :
- Les applications décoratives (par exemple, les feuilles d'acier inoxydable) peuvent nécessiter des revêtements plus fins, de l'ordre de 0,30 micron .
- Les applications fonctionnelles (par exemple, amélioration de la résistance à l'usure ou de la dureté) nécessitent souvent des revêtements plus épais, allant de 2 à 5 microns .
- Les revêtements PVD sont connus pour leur précision et leur capacité à respecter les spécifications des pièces techniques en raison de leur faible épaisseur.
-
Épaisseur du revêtement CVD :
- Les revêtements CVD sont généralement plus épais que les revêtements PVD. 5 à 10 microns .
- L'épaisseur accrue des revêtements CVD les rend appropriés pour les applications nécessitant une durabilité, une stabilité thermique ou une résistance chimique accrues.
- Les revêtements CVD sont formés par une réaction chimique à la surface du substrat, ce qui permet de déposer des couches plus épaisses et plus uniformes que les revêtements PVD.
-
Comparaison de l'épaisseur des revêtements PVD et CVD :
- Les revêtements PVD sont plus fins (0,25-5 microns) et sont souvent utilisés lorsqu'un contrôle précis de l'épaisseur du revêtement est nécessaire, comme dans les applications décoratives ou fonctionnelles de haute précision.
- Les revêtements CVD sont plus épais (5-10 microns) et sont préférés pour les applications où la durabilité et la résistance aux environnements difficiles sont essentielles, comme dans les outils industriels ou les composants à haute température.
-
Facteurs influençant l'épaisseur du revêtement :
- Exigences d'application : L'utilisation prévue de la pièce revêtue (par exemple, décorative, fonctionnelle ou protectrice) détermine l'épaisseur optimale du revêtement.
- Matériau du support : Le matériau revêtu peut influencer l'épaisseur et l'adhérence du revêtement.
- Paramètres du processus de revêtement : Des variables telles que la température, la pression et le temps de dépôt peuvent affecter l'épaisseur et la qualité du revêtement.
-
Implications pratiques de l'épaisseur du revêtement :
- Revêtements PVD minces (0,25-2 microns) : Idéal pour les applications où une interférence minimale avec les dimensions du substrat est requise, comme dans l'ingénierie de précision ou les finitions décoratives.
- Revêtements PVD plus épais (2-5 microns) : Ils offrent une résistance à l'usure et une durabilité accrues, ce qui les rend adaptés à des applications fonctionnelles telles que les outils de coupe ou les composants automobiles.
- Revêtements CVD (5-10 microns) : Ils offrent une protection supérieure contre les conditions extrêmes, telles que les températures élevées ou les environnements corrosifs, ce qui les rend adaptés aux applications industrielles et aérospatiales.
-
Contexte réel :
-
Pour mettre l'épaisseur en perspective :
- 1 micron = 0,001 millimètre .
- A globule rouge est d'environ 8 microns de diamètre.
- A cheveu humain est d'environ 80 microns de diamètre.
- Cette comparaison met en évidence la faible épaisseur des revêtements PVD et CVD, malgré leur impact significatif sur les performances et la longévité des pièces revêtues.
-
Pour mettre l'épaisseur en perspective :
En comprenant les plages d'épaisseur et les applications des revêtements PVD et CVD, les acheteurs et les ingénieurs peuvent prendre des décisions éclairées sur la méthode de revêtement la mieux adaptée à leurs besoins spécifiques.Que l'objectif soit d'améliorer l'esthétique, la fonctionnalité ou la protection, le choix entre PVD et CVD dépendra de l'épaisseur de revêtement souhaitée et des exigences opérationnelles de la pièce revêtue.
Tableau récapitulatif :
Type de revêtement | Gamme d'épaisseur | Applications principales |
---|---|---|
PVD | 0,25-5 microns | Décoratif, fonctionnel, mécanique de précision |
CVD | 5-10 microns | Durabilité, stabilité thermique, outils industriels |
Vous avez besoin d'aide pour sélectionner le bon revêtement pour votre application ? Contactez nos experts dès aujourd'hui !