Les revêtements par dépôt physique en phase vapeur (PVD) sont largement utilisés dans toutes les industries pour leur capacité à améliorer la durabilité, les performances et l'apparence de divers matériaux.Les revêtements PVD sont fins, durs et très adhérents, ce qui les rend adaptés aux applications dans les dispositifs médicaux, les composants automobiles, etc.Le revêtement PVD le plus courant pour les dispositifs médicaux est le nitrure de titane (TiN), connu pour sa dureté et sa couleur or.D'autres revêtements comme le nitrure d'aluminium et de titane (AlTiN) et le nitrure de chrome (CrN) offrent des propriétés spécifiques adaptées à différents besoins.Les procédés PVD, tels que la pulvérisation cathodique et l'évaporation thermique, sont utilisés pour déposer ces revêtements, ce qui permet un contrôle précis de l'épaisseur et des propriétés.
Explication des points clés :
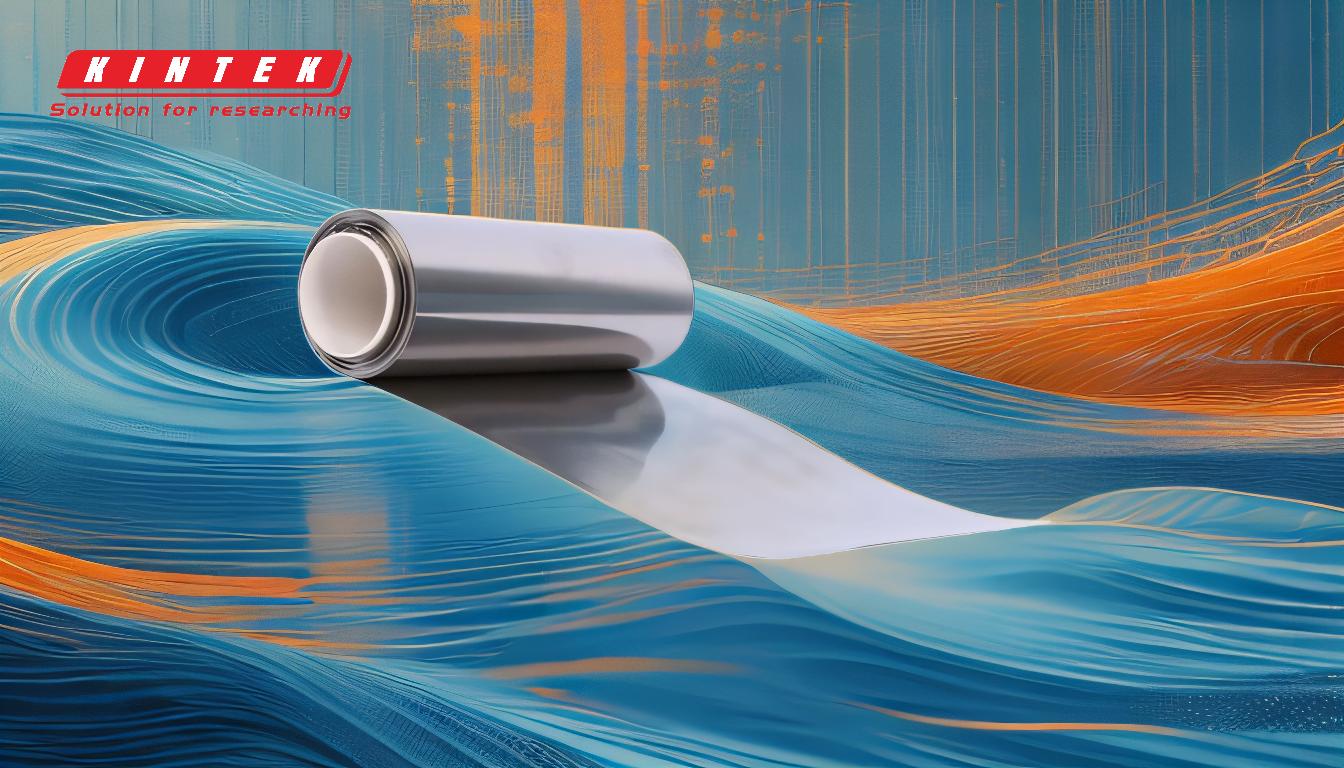
-
Revêtements PVD courants et leurs propriétés:
- Nitrure de titane (TiN):Il s'agit du revêtement PVD le plus utilisé, en particulier dans les dispositifs médicaux.Il a une épaisseur de 0,0001 à 0,0002 pouce, une dureté Vickers de 2 400 à 2 600 Hv et une couleur dorée distinctive.Le TiN est apprécié pour sa résistance à l'usure, sa résistance à la corrosion et sa biocompatibilité.
- Nitrure d'aluminium et de titane (AlTiN):Ce revêtement est connu pour sa grande dureté et sa stabilité thermique, ce qui le rend adapté aux applications à haute température.Il est souvent utilisé dans les outils de coupe et les composants industriels.
- Nitrure de chrome (CrN):CrN offre une excellente résistance à la corrosion et est couramment utilisé dans des applications où la durabilité et l'attrait esthétique sont importants, comme les garnitures décoratives et les pièces automobiles.
- Alpha Coatings:Il s'agit de revêtements spécialisés dotés de propriétés uniques adaptées à des applications spécifiques, souvent utilisés dans des industries exigeant une précision et des performances élevées.
-
Procédés de revêtement PVD:
- Pulvérisation:Ce procédé consiste à bombarder le matériau de revêtement (cible) avec une charge électrique à haute énergie pour libérer des atomes ou des molécules.Ces particules se déposent ensuite sur un substrat, formant un revêtement mince et uniforme.La pulvérisation est largement utilisée en raison de sa capacité à produire des revêtements de haute qualité avec une excellente adhérence.
- Évaporation thermique:Dans ce procédé, le matériau de revêtement est chauffé jusqu'à son point d'ébullition dans un vide poussé, créant une vapeur qui se condense sur le substrat.L'évaporation thermique est particulièrement efficace pour déposer des matériaux à faible point de fusion et est souvent utilisée dans les applications optiques et décoratives.
-
Applications des revêtements PVD:
- Dispositifs médicaux:Les revêtements PVD comme le TiN sont utilisés pour améliorer la durabilité et la biocompatibilité des instruments chirurgicaux, des implants et d'autres dispositifs médicaux.Les revêtements fins et durs réduisent l'usure et la corrosion, prolongeant ainsi la durée de vie de ces dispositifs.
- Industrie automobile:Les revêtements PVD sont appliqués aux composants du moteur, aux garnitures décoratives et aux roues pour améliorer la résistance à l'usure, la résistance à la corrosion et l'attrait esthétique.Ces revêtements aident les pièces automobiles à résister aux conditions difficiles tout en conservant leur apparence.
- Outils industriels:Les revêtements tels que l'AlTiN et le CrN sont utilisés sur les outils de coupe, les moules et d'autres composants industriels pour améliorer leur dureté, leur stabilité thermique et leur résistance à l'usure et à la corrosion.
-
Avantages des revêtements PVD:
- Mince et uniforme:Les revêtements PVD sont extrêmement fins, allant de couches atomiques (moins de 10 angströms) à plusieurs microns.Cela permet un contrôle précis de l'épaisseur et des propriétés du revêtement.
- Dureté et durabilité élevées:Les revêtements PVD sont connus pour leur grande dureté, ce qui les rend résistants à l'usure, à l'abrasion et aux chocs.
- Résistance à la corrosion:Ces revêtements offrent une excellente protection contre la corrosion, ce qui permet de les utiliser dans des environnements difficiles.
- Attrait esthétique:Les revêtements PVD peuvent être adaptés pour obtenir une variété de couleurs et de finitions, améliorant ainsi l'attrait visuel des produits revêtus.
En résumé, les revêtements PVD offrent une solution polyvalente et efficace pour améliorer les performances et l'aspect de divers matériaux.Avec une gamme de revêtements et de procédés disponibles, la technologie PVD peut être adaptée pour répondre aux besoins spécifiques de différentes industries, des dispositifs médicaux aux composants automobiles et aux outils industriels.
Tableau récapitulatif :
Type de revêtement | Propriétés principales | Applications courantes |
---|---|---|
Nitrure de titane (TiN) | Dureté (2 400-2 600 Hv), résistance à l'usure, résistance à la corrosion, biocompatibilité | Dispositifs médicaux, instruments chirurgicaux |
Nitrure d'aluminium et de titane (AlTiN) | Dureté élevée, stabilité thermique, résistance à l'usure | Outils de coupe, composants industriels |
Nitrure de chrome (CrN) | Excellente résistance à la corrosion, attrait esthétique | Garnitures décoratives, pièces automobiles |
Alpha Coatings | Propriétés spécialisées pour une précision et une performance élevées | Industries de précision, applications spécialisées |
Vous avez besoin d'un revêtement PVD adapté à votre application ? Contactez nos experts dès aujourd'hui pour des solutions sur mesure !