Les revêtements en couches minces sont des couches spécialisées appliquées sur des surfaces afin d'en améliorer les propriétés ou d'y ajouter de nouvelles fonctionnalités.Ces revêtements sont généralement minces, d'une épaisseur allant de quelques nanomètres à quelques micromètres, et sont utilisés dans diverses industries à des fins de protection, de décoration et d'amélioration des performances.Ils peuvent améliorer la dureté de la surface, la résistance à la corrosion, la conductivité électrique, les propriétés optiques, etc.Les revêtements en couches minces sont polyvalents et peuvent être adaptés à des besoins spécifiques, ce qui les rend essentiels dans des applications allant des outils industriels à l'électronique de pointe et aux finitions décoratives.
Explication des points clés :
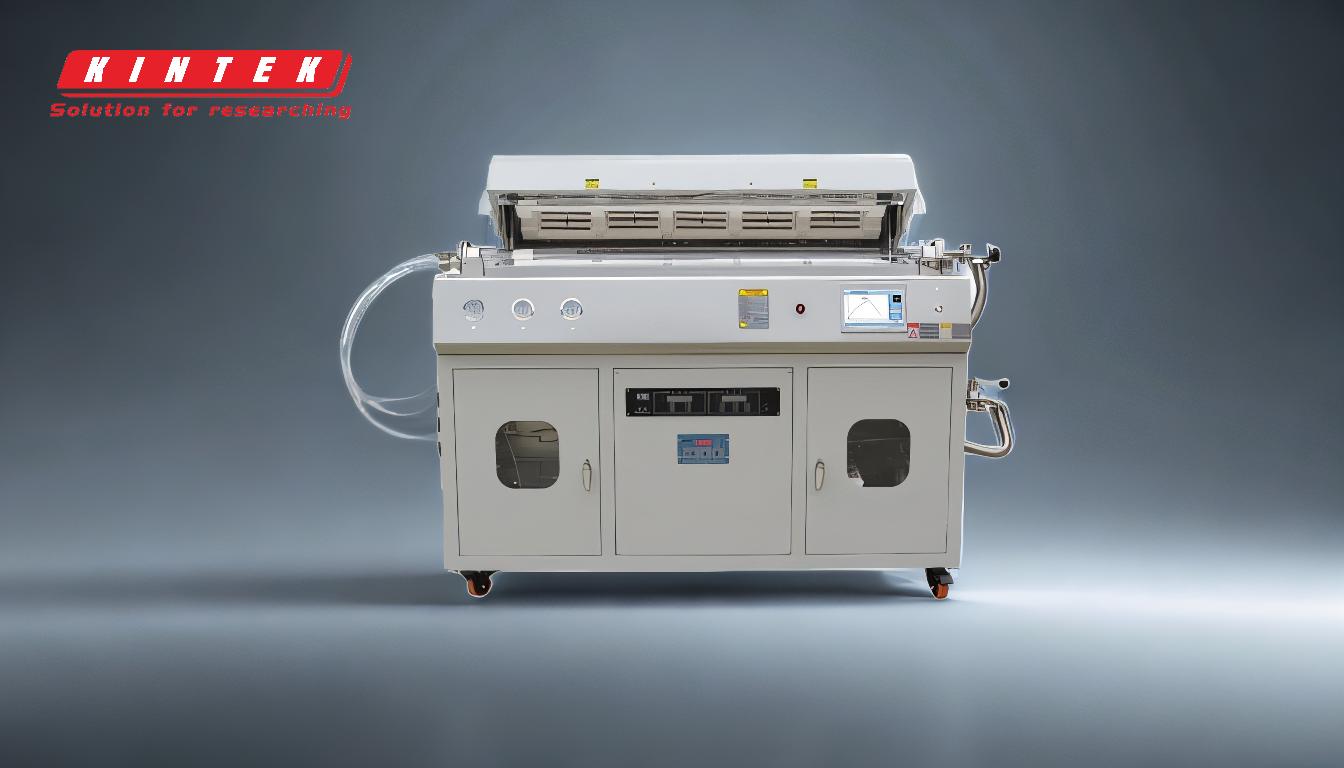
-
Définition et objectif des revêtements à couche mince:
- Les revêtements en couches minces sont des couches ultrafines appliquées sur des surfaces afin de modifier leurs propriétés ou d'ajouter de nouvelles fonctionnalités.
- Ils ont de multiples fonctions, notamment la protection (contre l'usure, les rayures, la corrosion), la décoration (modification de la couleur ou de la brillance) et l'amélioration des performances (amélioration de la conductivité ou de la dureté).
-
Caractéristiques des revêtements en couches minces:
- Transparence:Certains revêtements sont conçus pour être transparents, ce qui les rend adaptés aux applications optiques telles que les lentilles ou les écrans.
- Durabilité:Les revêtements peuvent améliorer la durabilité des surfaces, les rendant résistantes à l'usure, aux rayures et aux facteurs environnementaux.
- Propriétés électriques et optiques:Les couches minces peuvent augmenter ou diminuer la conductivité électrique ou modifier la transmission des signaux et de la lumière, ce qui les rend utiles en électronique et en photonique.
- Résistance à la corrosion:De nombreux revêtements sont appliqués pour protéger les surfaces de la corrosion et prolonger la durée de vie des matériaux.
-
Types de revêtements à couche mince:
-
Revêtements fonctionnels:Ils sont conçus pour améliorer des propriétés spécifiques telles que la dureté, la résistance à l'usure ou la résistance thermique.En voici quelques exemples :
- Ti-Al-N:Augmente la dureté et réduit le frottement, couramment utilisé dans les outils de coupe.
- Al-Cr-N:Améliore la durée de vie de l'outil et la résistance thermique, idéal pour les applications à haute température.
- Le Cr-N et Ti-C-N:Améliore la résistance à la corrosion et les performances de coupe.
- Revêtements décoratifs:Ils sont appliqués à des fins esthétiques, comme les revêtements métalliques sur des substrats en plastique pour créer un aspect brillant ou texturé.
-
Revêtements fonctionnels:Ils sont conçus pour améliorer des propriétés spécifiques telles que la dureté, la résistance à l'usure ou la résistance thermique.En voici quelques exemples :
-
Applications des revêtements en couches minces:
- Outils industriels:Les revêtements tels que Ti-Al-N et Al-Cr-N sont utilisés pour améliorer les performances et la durée de vie des outils de coupe et des machines.
- L'électronique:Les couches minces sont utilisées dans les dispositifs de conversion de l'énergie lumineuse en énergie électrique (par exemple, les panneaux solaires) et dans les technologies avancées de stockage de mémoire.
- Optique:Les revêtements transparents sont appliqués aux lentilles, aux miroirs et aux écrans pour améliorer les performances optiques et la durabilité.
- Finitions décoratives:Les films minces sont utilisés pour créer des surfaces réfléchissantes, modifier les textures de surface et ajouter de la couleur aux produits.
-
Avantages des revêtements en couches minces:
- Performances accrues:Les revêtements peuvent améliorer de manière significative les performances des matériaux du substrat en ajoutant des propriétés telles que la dureté, la conductivité ou la résistance aux facteurs environnementaux.
- Polyvalence:Les revêtements en couches minces peuvent être adaptés pour répondre à des exigences spécifiques, ce qui leur permet de convenir à un large éventail d'applications.
- Protection de la surface:Ils protègent les surfaces de l'usure, des rayures, des empreintes digitales et de la corrosion, prolongeant ainsi la durée de vie des matériaux.
- Attrait esthétique:Les revêtements décoratifs peuvent améliorer l'attrait visuel des produits, les rendant plus attrayants pour les consommateurs.
-
Propriétés du revêtement et interaction avec le support:
- Les revêtements en couches minces sont extrêmement adhérents, c'est-à-dire qu'ils adhèrent fortement au substrat, garantissant ainsi des performances durables.
- L'interaction entre le revêtement et le substrat est essentielle, car elle détermine l'efficacité du revêtement à obtenir les propriétés souhaitées, telles que la dureté, la conductivité ou la transmission optique.
-
Exemples de revêtements importants:
- Ti-Al-N:Connu pour sa grande dureté et sa faible friction, il est largement utilisé dans les outils de coupe et les applications industrielles.
- Al-Cr-N:Il offre une excellente résistance thermique et une bonne durée de vie de l'outil, ce qui le rend adapté aux environnements à haute température.
- Le Cr-N et Ti-C-N:Ces revêtements sont appréciés pour leur résistance à la corrosion et leur capacité de coupe, et sont souvent utilisés dans des environnements difficiles.
En résumé, les revêtements en couches minces sont une technologie essentielle qui améliore la fonctionnalité, la durabilité et l'apparence des matériaux dans diverses industries.Leur capacité à être personnalisés pour des applications spécifiques les rend indispensables à la fabrication et à la technologie modernes.
Tableau récapitulatif :
Aspect clé | Détails |
---|---|
Objectif | Modifier les propriétés de la surface, ajouter une fonctionnalité, protéger, décorer, améliorer. |
Épaisseur | Nanomètres à micromètres. |
Caractéristiques principales | Transparence, durabilité, propriétés électriques/optiques, résistance à la corrosion. |
Types de revêtements | Revêtements fonctionnels (par exemple, Ti-Al-N, Al-Cr-N) et décoratifs. |
Applications | Outils industriels, électronique, optique, finitions décoratives. |
Avantages | Performances accrues, polyvalence, protection des surfaces, attrait esthétique. |
Découvrez comment les revêtements à couche mince peuvent transformer vos produits. contactez nos experts dès aujourd'hui !