Le revêtement PVD (Physical Vapor Deposition) est un processus sophistiqué utilisé pour appliquer des revêtements fins, durables et hautes performances sur divers substrats. Les revêtements sont réalisés en vaporisant un matériau cible dans un environnement sous vide et en le déposant sur un substrat, souvent en combinaison avec des gaz réactifs pour former des composés spécifiques. Les matériaux couramment utilisés dans les revêtements PVD comprennent le nitrure de titane (TiN), le nitrure de zirconium (ZrN), le nitrure de chrome (CrN) et le carbone de type diamant (DLC). Ces matériaux offrent des propriétés améliorées telles que la dureté, la résistance à l'usure, la résistance à la corrosion et l'attrait esthétique. Le processus implique plusieurs étapes, notamment le nettoyage du substrat, la vaporisation, la réaction et le dépôt, garantissant un revêtement homogène et de haute qualité.
Points clés expliqués :
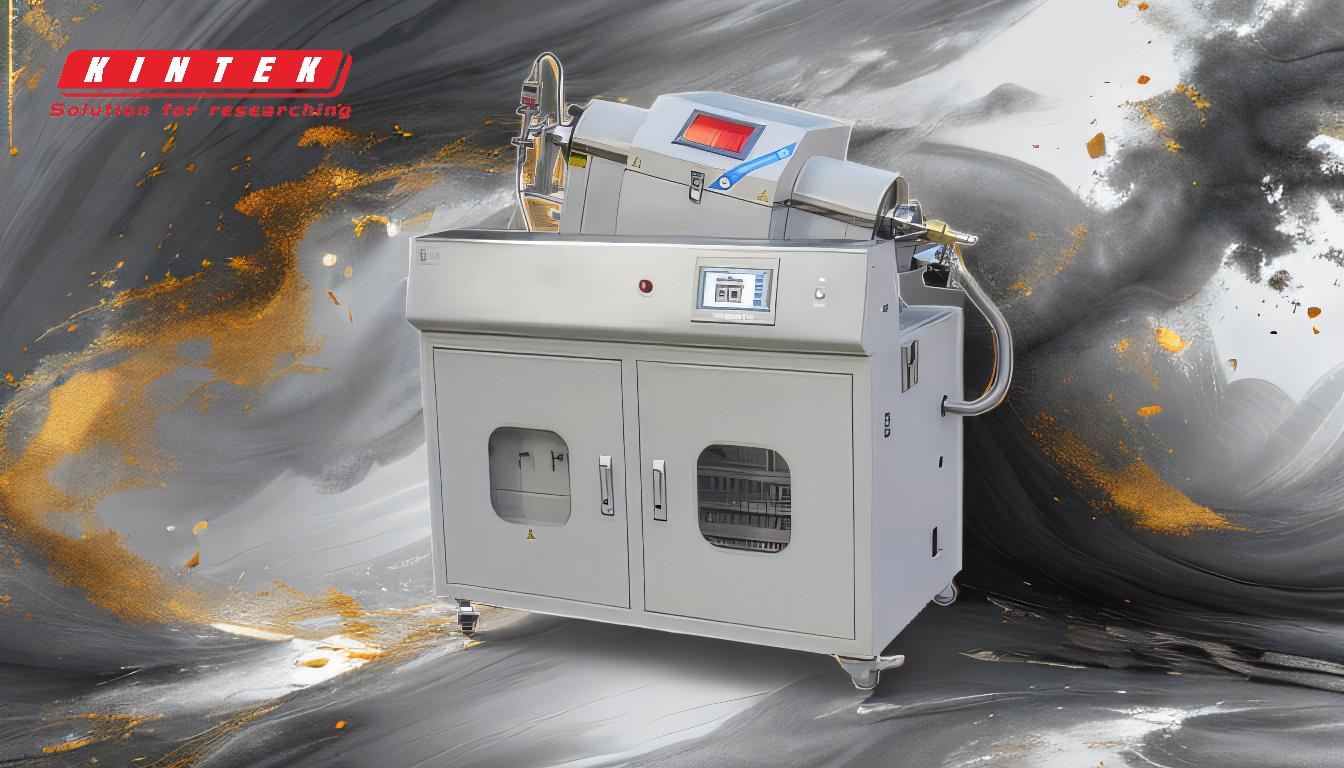
-
Matériaux utilisés dans les revêtements PVD:
- Nitrure de titane (TiN): Connu pour son aspect doré, le TiN est largement utilisé pour sa dureté et sa résistance à l’usure. Il est couramment appliqué aux outils de coupe, aux instruments médicaux et aux finitions décoratives.
- Nitrure de Zirconium (ZrN): Offre une excellente résistance à la corrosion et une couleur dorée brillante. Il est souvent utilisé dans des applications nécessitant à la fois durabilité et esthétique.
- Nitrure de chrome (CrN): Offre une résistance supérieure à la corrosion et est souvent utilisé dans des environnements difficiles, comme dans les industries aérospatiale et automobile.
- Carbone de type diamant (DLC): Connu pour sa dureté exceptionnelle et son faible frottement, le DLC est utilisé dans des applications nécessitant une résistance élevée à l'usure, telles que les composants de moteurs et les outils de coupe.
-
Le processus de revêtement PVD:
- Nettoyage du substrat: Le support est soigneusement nettoyé pour éliminer tous contaminants qui pourraient nuire à l'adhérence et à la qualité du revêtement.
- Vaporisation: Le matériau cible est vaporisé dans une chambre à vide en utilisant des méthodes telles que des arcs électriques, des faisceaux d'électrons ou une pulvérisation cathodique.
- Réaction: Le matériau vaporisé réagit avec les gaz (par exemple, l'azote ou l'oxygène) pour former un composé ayant les propriétés souhaitées, telles que la dureté ou la couleur.
- Déposition: Le matériau vaporisé et réagi est déposé sur le substrat, formant un revêtement mince et uniforme.
- Contrôle de qualité: Chaque lot de composants revêtus est testé pour la cohérence, l'épaisseur et la couleur à l'aide de techniques telles que la fluorescence des rayons X (XRF) et la spectrophotométrie.
-
Facteurs clés du revêtement PVD:
- Transfert en ligne de mire: Le PVD est un processus en visibilité directe, ce qui signifie que le revêtement est appliqué directement sur les surfaces visibles par la source de vapeur. Cela nécessite un positionnement minutieux du substrat.
- Prétraitement des surfaces: Une bonne préparation de la surface, y compris le nettoyage et le prétraitement, est cruciale pour garantir une bonne adhérence et une bonne qualité de revêtement.
- Environnement sous vide: Le processus se déroule dans un environnement sous vide poussé pour éviter la contamination et garantir un dépôt pur.
- Évitement de l'air emprisonné: Les trous taraudés hermétiquement fermés doivent être évités pour éviter que l'air emprisonné n'affecte la qualité du revêtement.
-
Applications des revêtements PVD:
- Outils industriels: Les revêtements PVD sont largement utilisés sur les outils de coupe, les moules et les matrices pour améliorer leur durabilité et leurs performances.
- Instruments médicaux: La biocompatibilité et la résistance à la corrosion des revêtements PVD les rendent idéaux pour les outils chirurgicaux et les implants.
- Finitions décoratives: Les revêtements PVD sont utilisés dans l'industrie de la bijouterie et de l'horlogerie pour leur esthétique et leur durabilité.
- Automobile et aérospatiale: Les composants de ces industries bénéficient de la résistance à l'usure et à la corrosion offerte par les revêtements PVD.
-
Avantages des revêtements PVD:
- Durabilité: Les revêtements PVD sont très durables et résistants à l'usure, à la corrosion et aux températures élevées.
- Versatilité: Le procédé est compatible avec une large gamme de matériaux, notamment les métaux, les plastiques et la céramique.
- Appel esthétique: Les revêtements PVD peuvent être adaptés pour obtenir différentes couleurs et finitions, améliorant ainsi l'attrait visuel des produits revêtus.
- Respect de l'environnement: Le processus PVD est respectueux de l'environnement, car il n'implique pas de produits chimiques nocifs et ne produit pas de déchets dangereux.
En résumé, les revêtements PVD sont fabriqués à partir d'une variété de matériaux, chacun offrant des avantages uniques, et sont appliqués selon un processus précis et contrôlé pour améliorer les performances et l'apparence de divers produits.
Tableau récapitulatif :
Matériel | Propriétés | Applications courantes |
---|---|---|
Nitrure de titane (TiN) | Dureté, résistance à l'usure, aspect doré | Outils de coupe, instruments médicaux, finitions décoratives |
Nitrure de Zirconium (ZrN) | Résistance à la corrosion, couleur dorée brillante | Applications nécessitant durabilité et esthétique |
Nitrure de chrome (CrN) | Résistance supérieure à la corrosion | Applications aérospatiales, automobiles et environnements difficiles |
Carbone de type diamant (DLC) | Dureté exceptionnelle, faible frottement | Composants de moteur, outils de coupe, applications à haute résistance à l'usure |
Vous souhaitez améliorer vos produits avec des revêtements PVD ? Contactez-nous aujourd'hui pour en savoir plus !