Le moulage par injection est un procédé de fabrication largement utilisé pour produire des pièces en plastique, et le choix de la conception du moule joue un rôle essentiel dans la détermination de l'efficacité, de la qualité et de la complexité du produit final.Un moule à trois plaques offre plusieurs avantages par rapport à un moule à deux plaques, principalement en raison de la présence d'une plaque de coulée supplémentaire.Cette conception permet des géométries de pièces plus complexes, un meilleur contrôle de l'emplacement des portes et la possibilité de séparer automatiquement les canaux et les pièces.Ces caractéristiques font des moules à trois plaques des outils idéaux pour la production en grande série, les configurations multi-empreintes et les conceptions de pièces complexes où la précision et l'efficacité sont primordiales.
Explication des points clés :
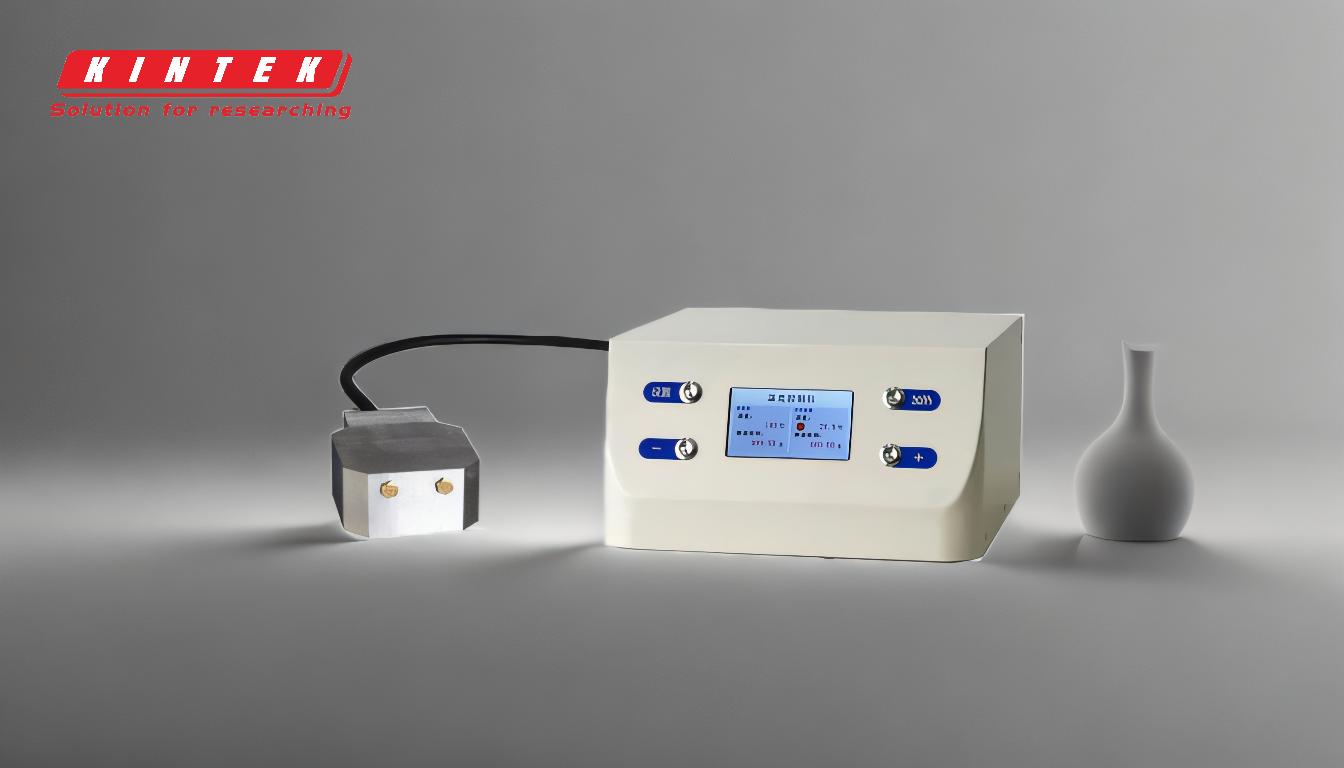
-
Une plaque de coulée supplémentaire pour plus de flexibilité
- Un moule à trois plaques comprend une plaque supplémentaire (plaque de coulée) par rapport à un moule à deux plaques.
- Cette plaque permet de séparer le système d'écoulement (les canaux par lesquels s'écoule le plastique fondu) des pièces moulées.
- La séparation s'effectue automatiquement pendant le processus d'ouverture du moule, ce qui réduit les interventions manuelles et améliore l'efficacité.
-
Meilleur contrôle de l'emplacement des portes
- La conception à trois plaques permet de placer les portillons (les points d'entrée du plastique fondu dans la cavité de la pièce) à n'importe quel endroit de la pièce, et pas seulement sur le plan de joint.
- Cette flexibilité est particulièrement utile pour les pièces à géométrie complexe ou pour celles qui nécessitent des points d'entrée à des endroits spécifiques afin de minimiser les marques ou les défauts visibles.
-
Adaptation aux moules multi-empreintes
- Les moules à trois plaques sont idéaux pour les installations multi-empreintes, où plusieurs pièces sont produites en un seul cycle.
- Le système de canaux peut être conçu pour distribuer uniformément le plastique fondu dans toutes les cavités, ce qui garantit une qualité constante des pièces.
-
Séparation automatique des canaux et des pièces
- Dans un moule à trois plaques, le système de canaux et les pièces moulées sont éjectés séparément.
- Cette caractéristique élimine la nécessité d'une séparation manuelle, ce qui réduit les coûts de main-d'œuvre et minimise le risque d'endommagement des pièces.
-
Amélioration de la qualité et de l'esthétique des pièces
- La possibilité de placer les portillons à des endroits optimaux réduit la probabilité d'apparition de défauts tels que des lignes de soudure, des marques d'enfoncement ou des marques de portillon visibles.
- Il en résulte des pièces de meilleure qualité avec de meilleurs états de surface, ce qui est essentiel pour les applications exigeant un attrait esthétique.
-
Utilisation efficace des matériaux
- La conception du moule à trois plaques permet d'obtenir un système de glissières plus compact, ce qui réduit le gaspillage de matériaux.
- Cette efficacité est particulièrement bénéfique pour la production de gros volumes, où même de petites réductions dans l'utilisation des matériaux peuvent conduire à des économies significatives.
-
Polyvalence pour les conceptions de pièces complexes
- Les moules à trois plaques sont mieux adaptés à la production de pièces aux dessins complexes ou aux contre-dépouilles qu'il serait difficile de mouler avec un modèle à deux plaques.
- La plaque supplémentaire offre plus d'espace et de flexibilité pour les broches d'éjection, les glissières et les autres composants nécessaires aux géométries complexes des pièces.
-
Temps de cycle réduits
- La séparation automatique des canaux et des pièces dans un moule à trois plaques peut entraîner des temps de cycle plus courts que dans les moules à deux plaques, où une séparation manuelle peut être nécessaire.
- Des temps de cycle plus courts se traduisent par des taux de production plus élevés et des coûts de fabrication plus faibles.
-
Rentabilité dans la production en grande série
- Si les moules à trois plaques sont généralement plus coûteux à concevoir et à fabriquer que les moules à deux plaques, les avantages qu'ils présentent pour la production en grande série justifient souvent l'investissement initial.
- La réduction des coûts de main-d'œuvre, les économies de matériaux et l'efficacité accrue de la production en font un choix rentable pour la fabrication à grande échelle.
-
Applications dans la fabrication de pointe
- Les moules à trois plaques sont couramment utilisés dans les industries exigeant une grande précision et des conceptions de pièces complexes, telles que l'automobile, les appareils médicaux et l'électronique grand public.
- Leur capacité à produire des pièces de haute qualité avec un minimum de post-traitement les rend indispensables dans ces secteurs.
En résumé, le moule à trois plaques offre des avantages significatifs par rapport au moule à deux plaques, notamment en termes de flexibilité, d'efficacité et de qualité des pièces.Sa capacité à gérer des conceptions complexes, à réduire le gaspillage de matériaux et à automatiser la séparation des canaux et des pièces en fait un choix supérieur pour les processus de fabrication en grande quantité et axés sur la précision.Bien que le coût initial puisse être plus élevé, les avantages à long terme l'emportent souvent sur l'investissement, ce qui fait des moules à trois plaques une option privilégiée pour de nombreuses industries.
Tableau récapitulatif :
Avantage | Description |
---|---|
Plaque de coulée supplémentaire | Elle permet de séparer automatiquement les patins et les pièces, ce qui améliore l'efficacité. |
Meilleur contrôle de l'emplacement des portillons | Permet de placer les portillons à n'importe quel endroit de la pièce, ce qui réduit les défauts. |
Adaptation aux cavités multiples | Idéal pour produire plusieurs pièces en un seul cycle avec une qualité constante. |
Séparation automatique des canaux | Élimine la séparation manuelle, réduit les coûts de main-d'œuvre et les dommages aux pièces. |
Amélioration de la qualité des pièces | Minimise les défauts tels que les lignes de soudure et les marques d'enfoncement pour une meilleure esthétique. |
Utilisation efficace des matériaux | Le système de glissières compactes réduit les pertes de matériau, ce qui permet de réaliser des économies. |
Polyvalence pour les conceptions complexes | Prise en charge des géométries complexes et des contre-dépouilles avec une flexibilité accrue. |
Temps de cycle réduits | Des taux de production plus rapides grâce à des processus automatiques. |
Rentabilité | Les économies à long terme en termes de main-d'œuvre, de matériaux et d'efficacité justifient les coûts initiaux plus élevés. |
Applications de fabrication avancée | Largement utilisé dans les secteurs de l'automobile, de la médecine et de l'électronique. |
Prêt à améliorer votre processus de moulage par injection ? Contactez nous dès aujourd'hui pour savoir comment un moule à trois plaques peut être bénéfique pour votre production !