Les revêtements de carbone de type diamant (DLC) sont une classe de matériaux connus pour leur combinaison unique de propriétés, notamment une grande dureté, un faible frottement et une excellente résistance à l'usure et aux produits chimiques.Ces revêtements sont principalement composés de carbone, mais leur composition chimique spécifique peut varier en fonction de la méthode de dépôt et de la présence d'hydrogène.La clé de la compréhension des revêtements DLC réside dans leur structure de liaison, qui comprend un mélange de liaisons carbone sp3 (de type diamant) et sp2 (de type graphite).La proportion de ces liaisons, ainsi que la présence d'hydrogène, influencent considérablement les propriétés mécaniques et tribologiques du revêtement.
Explication des points clés :
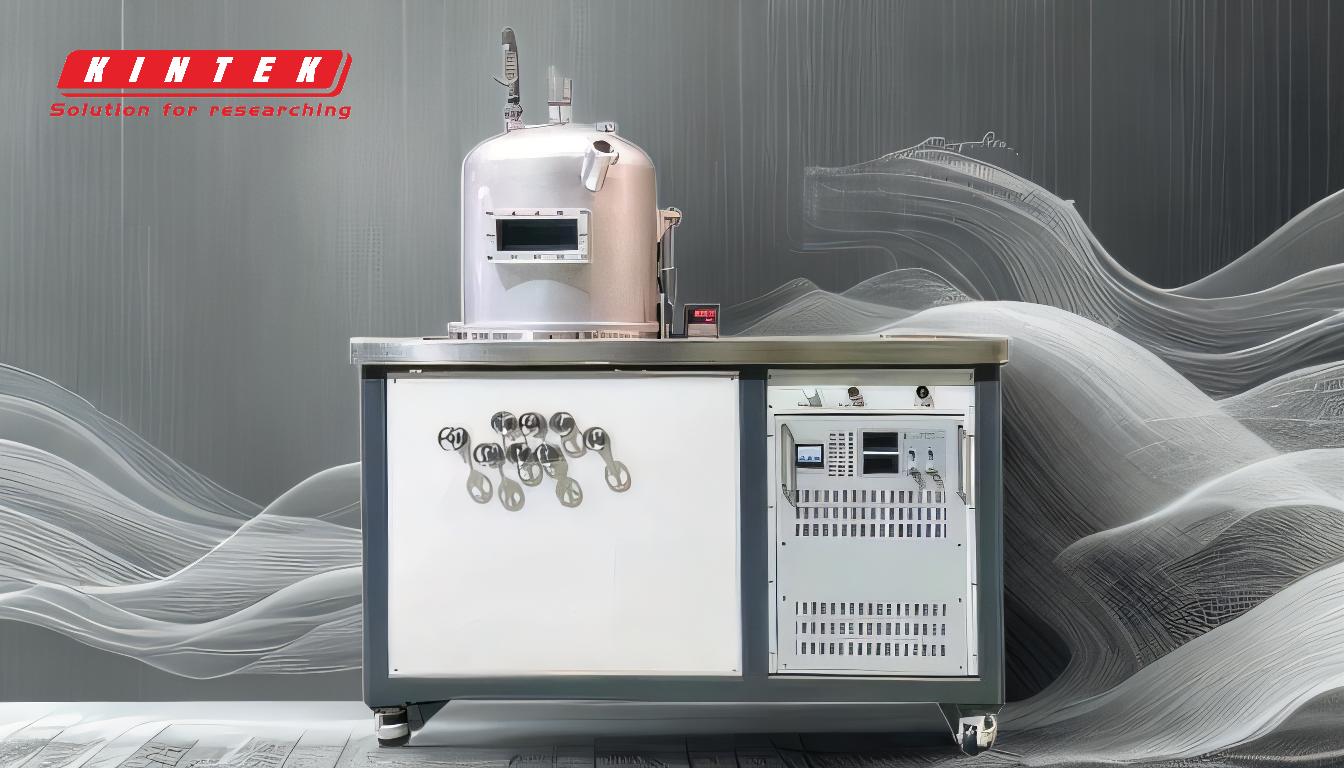
-
Composition primaire :Carbone
- Les revêtements DLC sont principalement composés d'atomes de carbone.Les atomes de carbone du DLC peuvent former différents types de liaisons, qui jouent un rôle crucial dans la détermination des propriétés du revêtement.
- Le carbone dans le DLC peut exister dans des configurations de liaison sp3 (tétraédrique, semblable au diamant) et sp2 (trigonale, semblable au graphite).Les liaisons sp3 contribuent à la dureté et à la résistance à l'usure, tandis que les liaisons sp2 apportent un certain degré de flexibilité et réduisent la friction.
-
Structure de liaison : liaisons sp3 et sp2
- Les liaisons sp3 sont caractéristiques du diamant et confèrent au DLC sa grande dureté et sa résistance à l'usure.
- Les liaisons sp2 sont similaires à celles que l'on trouve dans le graphite, contribuant à la faible friction et à un certain degré de conductivité électrique.
- Le rapport entre les liaisons sp3 et sp2 peut varier considérablement en fonction de la technique et des conditions de dépôt, ce qui permet d'obtenir différents types de revêtements DLC aux propriétés variées.
-
Teneur en hydrogène
- De nombreux revêtements DLC sont hydrogénés, ce qui signifie qu'ils contiennent une quantité importante d'hydrogène.La teneur en hydrogène peut varier de quelques pour cent à plus de 50 %, en fonction de la méthode de dépôt.
- L'hydrogène dans les revêtements DLC aide à stabiliser la structure amorphe et peut influencer les propriétés mécaniques, telles que la dureté et le coefficient de frottement.
-
Structure amorphe
- Les revêtements DLC sont généralement amorphes, ce qui signifie qu'ils n'ont pas d'ordre cristallin à longue portée.Cette nature amorphe contribue à leurs propriétés isotropes et à leurs performances uniformes dans différentes directions.
- La structure amorphe permet également une large gamme de compositions et de propriétés possibles, ce qui rend les revêtements DLC très polyvalents.
-
Types de revêtements DLC
- ta-C (carbone amorphe tétraédrique) : Ce type de DLC se caractérise par une forte proportion de liaisons sp3, ce qui le rend très dur et semblable à un diamant.
- a-C (carbone amorphe) : Ce type de carbone a une fraction plus faible de liaisons sp3 et peut contenir plus de liaisons sp2, ce qui le rend moins dur mais très résistant à l'usure.
- DLC à terminaison H : Ces revêtements contiennent de l'hydrogène, ce qui peut contribuer à réduire le frottement et à améliorer la résistance chimique.
-
Propriétés influencées par la composition
- Dureté : La dureté des revêtements DLC peut varier de 1500 à 3000 HV (dureté Vickers), en fonction du rapport sp3/sp2 et de la teneur en hydrogène.
- Coefficient de frottement : Les revêtements DLC sont connus pour leurs faibles coefficients de frottement, qui peuvent descendre jusqu'à 0,05, ce qui les rend idéaux pour les applications de glissement.
- Résistance à l'usure et aux produits chimiques : La combinaison d'une grande dureté et d'une faible friction rend les revêtements DLC très résistants à l'usure et à la corrosion, ce qui les rend adaptés aux environnements difficiles.
-
Applications
- Les revêtements DLC sont largement utilisés dans les secteurs de l'automobile et des machines, en particulier dans des composants tels que les groupes motopropulseurs, les roulements et les arbres à cames, où leur faible frottement et leur résistance à l'usure peuvent entraîner des économies d'énergie significatives et prolonger la durée de vie des composants.
En résumé, la composition chimique des revêtements DLC est principalement constituée de carbone, avec un mélange de liaisons sp3 et sp2 et souvent une quantité importante d'hydrogène.La composition spécifique et la structure des liaisons déterminent les propriétés mécaniques et tribologiques du revêtement, ce qui rend les revêtements DLC très polyvalents et adaptés à un large éventail d'applications.
Tableau récapitulatif :
Aspect clé | Détails |
---|---|
Composition primaire | Principalement des atomes de carbone avec des liaisons sp3 (de type diamant) et sp2 (de type graphite) |
Teneur en hydrogène | varie de quelques pour cent à plus de 50 %, ce qui stabilise la structure amorphe. |
Structure de liaison | Mélange de liaisons sp3 (dureté) et sp2 (faible friction) |
Structure amorphe | Absence d'ordre cristallin à longue portée, ce qui permet d'obtenir des propriétés polyvalentes. |
Types de revêtements DLC | ta-C (sp3 élevé), a-C (sp3 inférieur), terminaison H (hydrogénée) |
Propriétés | Dureté élevée (1500-3000 HV), faible frottement (jusqu'à 0,05), résistance à l'usure |
Applications | Automobile, machines (roulements, arbres à cames, groupes motopropulseurs) |
Découvrez comment les revêtements DLC peuvent améliorer vos applications. contactez nos experts dès aujourd'hui !