Le dépôt chimique en phase vapeur (CVD) et le dépôt physique en phase vapeur (PVD) sont deux techniques de revêtement largement utilisées pour les inserts, chacune ayant des processus, des propriétés et des applications distincts.Le dépôt chimique en phase vapeur fait appel à des réactions chimiques à des températures élevées (800-1000 °C) pour déposer des revêtements plus épais (10-20 μm), tandis que le dépôt physique en phase vapeur fait appel à la vaporisation physique à des températures plus basses (250-500 °C) pour créer des films plus fins et ultra-durs (3-5 μm).Les revêtements CVD sont plus denses et plus uniformes, mais peuvent introduire des contraintes de traction et de fines fissures en raison des températures de traitement élevées.Les revêtements PVD, en revanche, forment des contraintes de compression et sont idéaux pour les applications de précision nécessitant des surfaces lisses et durables.Le choix entre CVD et PVD dépend de facteurs tels que l'épaisseur du revêtement, la température de fonctionnement et les exigences spécifiques de l'application.
Explication des points clés :
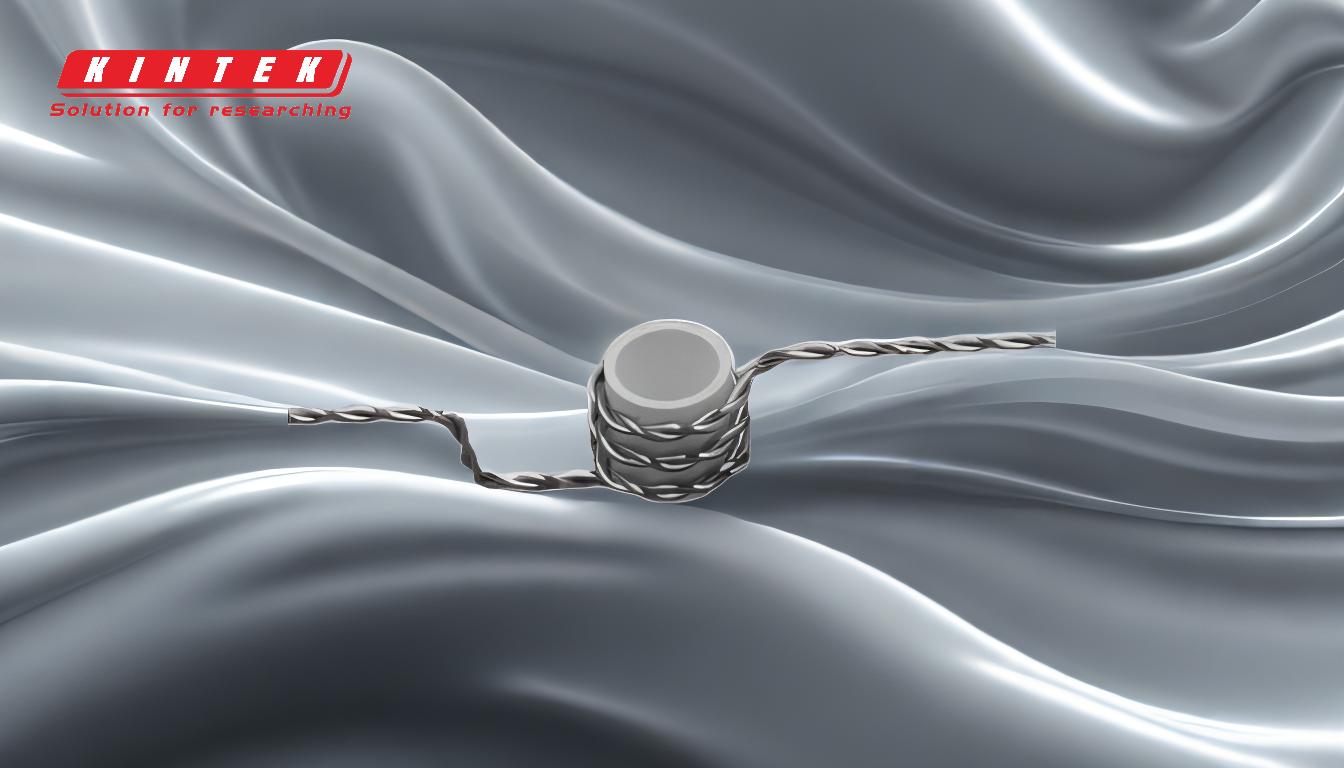
-
Mécanisme de dépôt:
- MCV:Il s'agit de réactions chimiques entre des précurseurs gazeux et le substrat à des températures élevées (800-1000 °C).Il en résulte un dépôt multidirectionnel, où le revêtement se forme uniformément sur toutes les surfaces, y compris les géométries complexes.
- PVD:Il s'agit d'un procédé physique, tel que la pulvérisation ou l'évaporation, qui permet de déposer un matériau directement sur le substrat en ligne de mire.Cela limite la couverture des surfaces exposées mais permet un contrôle précis des propriétés du film.
-
Température de fonctionnement:
- MCV:Nécessite des températures élevées (800-1000 °C), qui peuvent affecter les propriétés mécaniques du substrat et entraîner des contraintes de traction ou de fines fissures dans le revêtement.
- PVD:Fonctionne à des températures plus basses (250-500 °C), ce qui le rend adapté aux matériaux sensibles à la chaleur et réduit le risque de déformation du substrat.
-
Épaisseur et uniformité du revêtement:
- MCV:Produit des revêtements plus épais (10-20 μm) avec une excellente uniformité, ce qui le rend idéal pour les applications nécessitant une résistance à l'usure et une durabilité élevées.
- PVD:Forme des revêtements plus fins (3-5 μm) avec une douceur et une précision supérieures, adaptés aux applications exigeant des finitions de surface fines et des changements dimensionnels minimes.
-
Contrainte et adhérence:
- MCV:Les températures de traitement élevées peuvent entraîner des tensions dans le revêtement, ce qui peut provoquer des microfissures et une réduction de l'adhérence dans certains cas.
- PVD:Génère une contrainte de compression pendant le refroidissement, améliorant l'adhérence et la durabilité du revêtement, en particulier dans les applications de haute précision.
-
Compatibilité des matériaux:
- MCV:Principalement utilisé pour les céramiques et les polymères, il offre une excellente résistance chimique et une grande stabilité thermique.
- PVD:Peut déposer une plus large gamme de matériaux, y compris des métaux, des alliages et des céramiques, offrant ainsi une plus grande polyvalence pour diverses applications.
-
Applications:
- MCV:Couramment utilisé dans les industries nécessitant des revêtements épais et résistants à l'usure, comme les outils de coupe, les composants aérospatiaux et la fabrication de semi-conducteurs.
- PVD:Préféré pour les applications nécessitant des revêtements fins, lisses et précis, comme les appareils médicaux, les composants optiques et les finitions décoratives.
-
Coût et temps de traitement:
- MCV:Généralement plus coûteux et plus long en raison des températures élevées et des processus chimiques complexes impliqués.
- PVD:Offre des temps de traitement plus rapides et des coûts plus faibles, ce qui le rend plus économique pour la production en grande quantité.
En résumé, le choix entre les inserts de revêtement CVD et PVD dépend des exigences spécifiques de l'application, notamment de l'épaisseur du revêtement, de la température de fonctionnement, de la compatibilité des matériaux et des propriétés de surface souhaitées.Le procédé CVD est idéal pour les revêtements épais et uniformes dans des environnements à haute température, tandis que le procédé PVD excelle dans les applications de précision nécessitant des surfaces lisses et durables à des températures plus basses.
Tableau récapitulatif :
Aspect | CVD | PVD |
---|---|---|
Mécanisme de dépôt | Réactions chimiques à haute température (800-1000 °C), multidirectionnelles | Vaporisation physique à des températures plus basses (250-500 °C), en ligne de mire |
Épaisseur du revêtement | Plus épais (10-20 μm), uniforme | Plus mince (3-5 μm), ultra-dur et lisse |
Température de fonctionnement | Élevée (800-1000 °C), peut provoquer des contraintes de traction | Faible (250-500 °C), réduit la déformation du substrat |
Contrainte et adhésion | Contrainte de traction, microfissures potentielles | Contrainte de compression, amélioration de l'adhérence |
Compatibilité des matériaux | Céramiques, polymères, haute résistance chimique | Métaux, alliages, céramiques, polyvalents |
Applications | Outils de coupe, aérospatiale, semi-conducteurs | Dispositifs médicaux, optique, finitions décoratives |
Coût et traitement | Coûteux, long à mettre en œuvre | Rentable, traitement plus rapide |
Vous avez besoin d'aide pour choisir entre CVD et PVD pour votre application ? Contactez nos experts dès aujourd'hui pour des conseils sur mesure !