Le dépôt chimique en phase vapeur (CVD) et le revêtement par pulvérisation cathodique (un type de dépôt physique en phase vapeur, PVD) sont deux techniques de dépôt de couches minces très répandues, mais elles diffèrent considérablement dans leurs principes, leurs processus et leurs applications.Le dépôt en phase vapeur implique des réactions chimiques entre des précurseurs gazeux pour former un film mince sur un substrat, tandis que le revêtement par pulvérisation cathodique repose sur des processus physiques tels que les collisions atomiques pour déposer un matériau sur une surface.Le dépôt en phase vapeur est un procédé sans visibilité directe, ce qui permet de revêtir des géométries complexes, et il fonctionne généralement à des températures plus élevées, ce qui permet d'obtenir une meilleure adhérence et des revêtements plus denses.Le revêtement par pulvérisation cathodique, quant à lui, est un procédé à visibilité directe, ce qui limite sa capacité à revêtir des zones cachées, mais il peut déposer une gamme plus large de matériaux et fonctionne à des températures plus basses.Il est essentiel de comprendre ces différences pour choisir la méthode appropriée en fonction des exigences de l'application.
Explication des points clés :
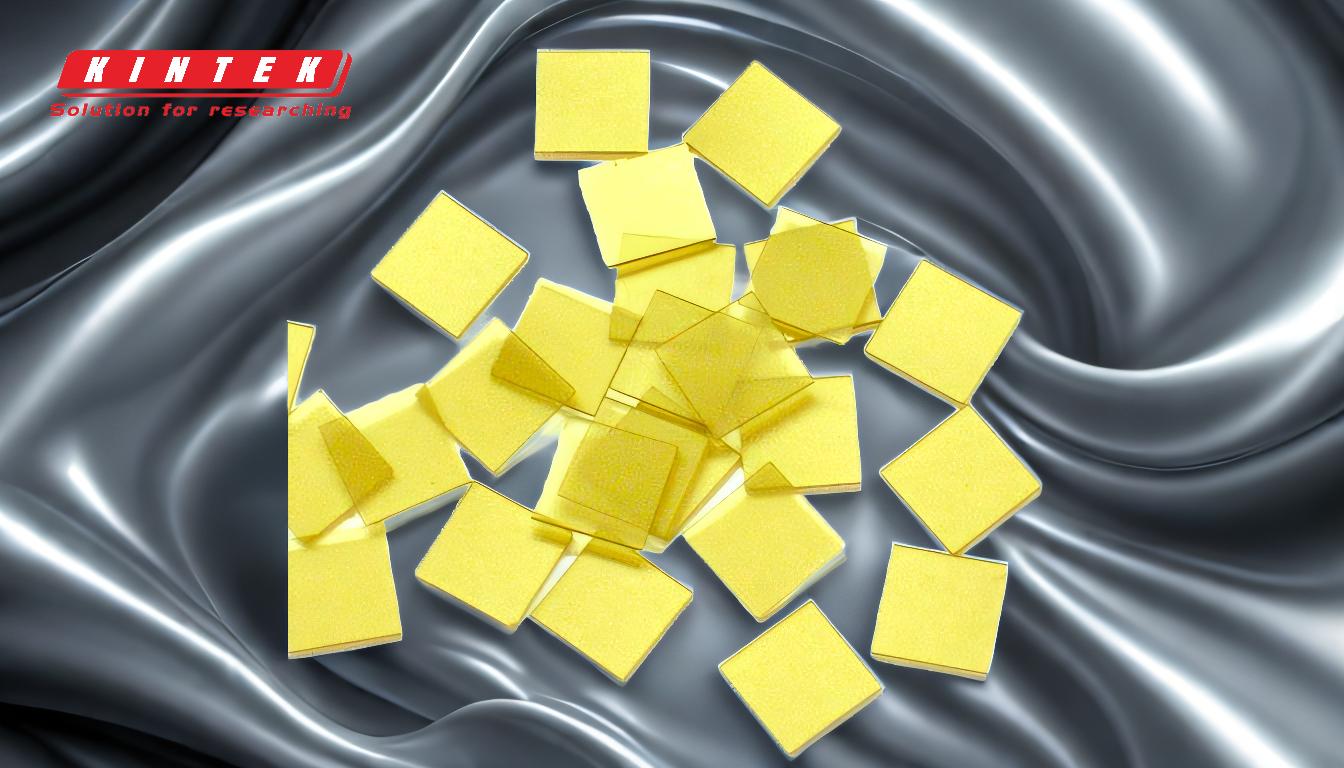
-
Principe de fonctionnement:
-
MCV:Il s'agit de réactions chimiques entre des précurseurs gazeux pour former un film mince sur le substrat.Le processus est alimenté par des températures élevées et se déroule souvent sous vide.
- Exemple :Un gaz comme le méthane (CH₄) se décompose à haute température pour déposer du carbone sur un substrat.
-
Revêtement par pulvérisation:Le procédé repose sur des processus physiques, où un matériau cible est bombardé par des ions à haute énergie, ce qui provoque l'éjection d'atomes qui se déposent sur le substrat.
- Exemple :Les ions argon entrent en collision avec une cible métallique, pulvérisant des atomes métalliques sur un substrat.
-
MCV:Il s'agit de réactions chimiques entre des précurseurs gazeux pour former un film mince sur le substrat.Le processus est alimenté par des températures élevées et se déroule souvent sous vide.
-
Exigences en matière de température:
- MCV:Fonctionne généralement à des températures élevées (800-1000 °C), ce qui peut limiter les types de matériaux de base qui peuvent être revêtus en raison de la dégradation thermique ou des problèmes de réactivité.
- Revêtement par pulvérisation cathodique:Fonctionne à des températures plus basses (environ 500 °C), ce qui le rend adapté aux matériaux sensibles à la chaleur.
-
Ligne de mire et non ligne de mire:
- MCV:Processus sans visibilité directe, ce qui signifie que le gaz de revêtement peut atteindre et revêtir toutes les zones d'une pièce, y compris les géométries complexes telles que les filetages, les trous borgnes et les surfaces intérieures.
- Revêtement par pulvérisation cathodique:Processus à visibilité directe, ce qui limite sa capacité à revêtir uniformément les zones cachées ou encastrées.
-
Adhésion et densité du revêtement:
- MCV:Produit des revêtements avec une adhérence supérieure en raison de la liaison chimique pendant la réaction.Les revêtements sont également plus denses et plus uniformes.
- Revêtement par pulvérisation:L'adhérence est généralement plus faible que celle du CVD, et les revêtements sont moins denses et moins uniformes.
-
Compatibilité des matériaux:
- MCV:Principalement utilisé pour les céramiques et les polymères.Limité par la nécessité de précurseurs chimiques compatibles et de températures élevées.
- Revêtement par pulvérisation:Peut déposer une plus large gamme de matériaux, y compris les métaux, les alliages et les céramiques, en raison de sa nature physique.
-
Temps de traitement:
- MCV:Généralement plus lent en raison du processus de réaction chimique et des exigences en matière de haute température.
- Revêtement par pulvérisation cathodique:Des taux de dépôt plus rapides, ce qui le rend plus efficace pour certaines applications.
-
Applications:
- MCV:Largement utilisé dans les industries nécessitant des revêtements de haute performance, telles que la fabrication de semi-conducteurs, les revêtements d'outils et les couches de protection sur les métaux.
- Revêtement par pulvérisation cathodique:Couramment utilisé pour les revêtements optiques, les finitions décoratives et les couches minces électroniques.
-
Épaisseur du revêtement:
- MCV:Produit généralement des revêtements plus épais (10-20 μm) mais est limité par la contrainte du revêtement.
- Revêtement par pulvérisation cathodique:Produit des revêtements plus fins (3-5 μm), qui conviennent aux applications nécessitant un contrôle précis de l'épaisseur.
En comprenant ces différences clés, les acheteurs d'équipements et de consommables peuvent prendre des décisions éclairées quant à la méthode de revêtement la mieux adaptée à leurs besoins spécifiques, qu'il s'agisse de résistance aux hautes températures, de géométries complexes ou de polyvalence des matériaux.
Tableau récapitulatif :
Aspect | CVD | Revêtement par pulvérisation cathodique |
---|---|---|
Principe | Réactions chimiques entre des précurseurs gazeux. | Processus physique impliquant des collisions atomiques. |
Température | Haute (800-1000 °C). | Plus bas (environ 500 °C). |
Procédé d'enduction | Sans visibilité directe, idéal pour les géométries complexes. | En visibilité directe, limité aux surfaces exposées. |
Adhésion et densité | Adhésion supérieure et revêtements plus denses. | Adhésion plus faible, revêtements moins denses. |
Compatibilité des matériaux | Principalement céramiques et polymères. | Large éventail, y compris les métaux, les alliages et les céramiques. |
Temps de traitement | Plus lent en raison des réactions chimiques. | Taux de dépôt plus rapide. |
Applications | Fabrication de semi-conducteurs, revêtements d'outils, couches protectrices. | Revêtements optiques, finitions décoratives, électronique en couches minces. |
Épaisseur du revêtement | Revêtements plus épais (10-20 μm). | Revêtements plus fins (3-5 μm). |
Vous avez besoin d'aide pour sélectionner la bonne méthode de dépôt en couche mince ? Contactez nos experts dès aujourd'hui pour discuter de vos besoins spécifiques !