Les revêtements PVD (Physical Vapor Deposition) sont des revêtements avancés en couche mince connus pour leur dureté exceptionnelle, leur résistance à l'usure, leur résistance à la corrosion et leurs propriétés de faible friction.Ils sont largement utilisés dans des secteurs tels que l'automobile, l'aérospatiale, la médecine et la fabrication de semi-conducteurs en raison de leur durabilité et de leurs avantages environnementaux par rapport aux méthodes de revêtement traditionnelles telles que le chromage.Les revêtements PVD sont appliqués à des températures relativement basses, sont très uniformes et adhèrent bien aux substrats, ce qui les rend appropriés pour une variété d'applications, y compris l'allongement de la durée de vie des outils, des pièces automobiles et des dispositifs médicaux.Les revêtements PVD les plus courants comprennent des matériaux tels que le nitrure de titane (TiN), le nitrure de chrome (CrN) et le carbone semblable à un diamant (DLC), chacun offrant des propriétés uniques adaptées à des cas d'utilisation spécifiques.
Les points clés expliqués :
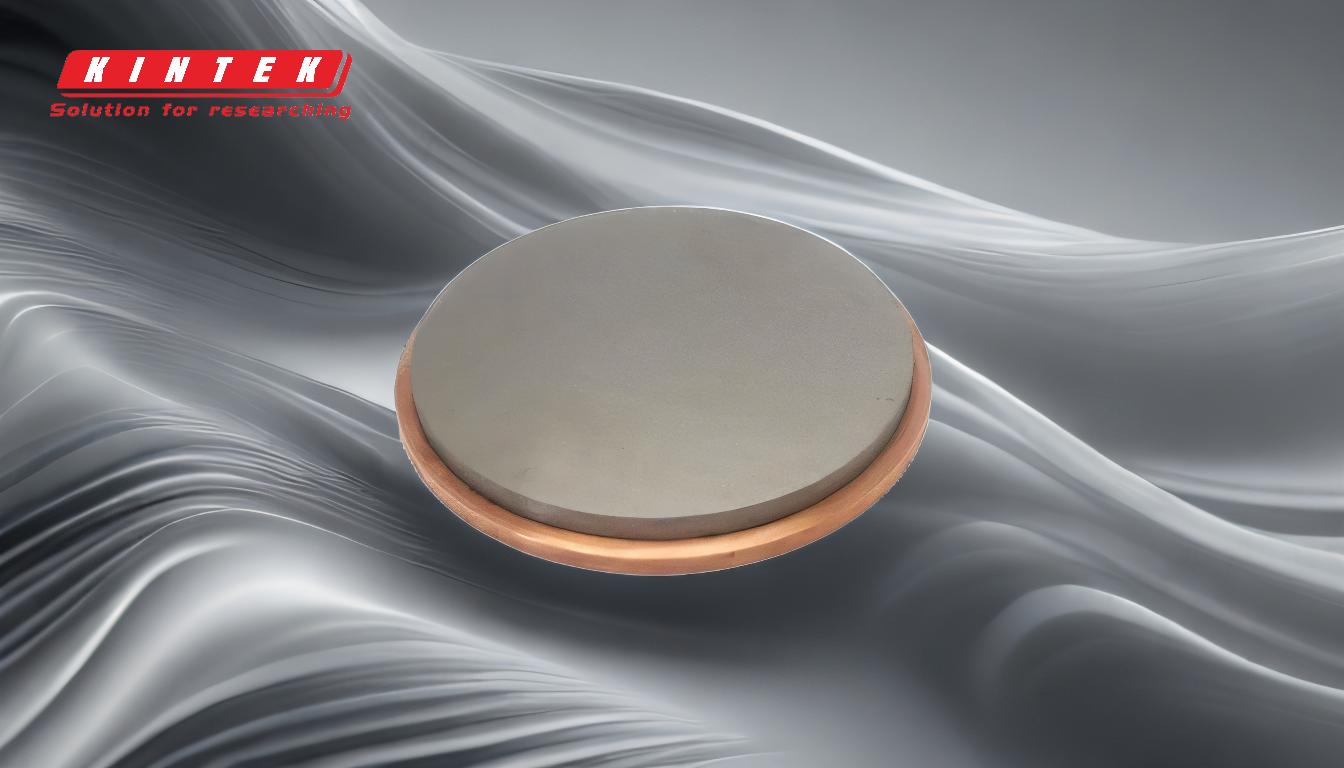
-
Qu'est-ce que le revêtement PVD ?
- Le revêtement PVD est un procédé de dépôt en couche mince dans lequel un matériau solide est vaporisé sous vide, puis déposé sur un substrat.Ce procédé permet d'obtenir un revêtement très durable, uniforme et adhérent.
- Les revêtements sont généralement très fins, de l'ordre de 0,5 à 5 microns, mais ils apportent des améliorations significatives en termes de dureté, de résistance à l'usure et de résistance à la corrosion.
-
Principales propriétés des revêtements PVD
- Dureté élevée : Les revêtements PVD sont nettement plus durs que les revêtements galvaniques traditionnels, ce qui les rend idéaux pour les applications nécessitant une résistance à l'usure.
- Résistance à la corrosion et à l'oxydation : Ces revêtements sont très résistants à la dégradation de l'environnement, ce qui les rend adaptés aux conditions difficiles.
- Faible friction : Les revêtements PVD réduisent le frottement, ce qui est bénéfique pour les pièces mobiles dans les applications automobiles et aérospatiales.
- Uniformité et adhérence : Les revêtements sont très uniformes et adhèrent bien au substrat, ce qui garantit des performances constantes.
- Respect de l'environnement : Contrairement au chromage, les revêtements PVD ne produisent pas de substances toxiques, ce qui en fait un choix plus durable.
-
Types courants de revêtements PVD
- Nitrure de titane (TiN) : Connu pour son aspect doré, le TiN est largement utilisé pour sa grande dureté, sa résistance à l'usure et sa capacité à augmenter la limite de fatigue des substrats.
- Nitrure de chrome (CrN) : Il offre une excellente résistance à la corrosion et est souvent utilisé dans des applications nécessitant une stabilité à haute température.
- Carbone semblable à un diamant (DLC) : Il offre une friction extrêmement faible et une grande résistance à l'usure, ce qui le rend idéal pour les applications automobiles et médicales.
- Nitrure d'aluminium et de titane (AlTiN) : Connu pour ses performances à haute température, il est couramment utilisé dans les outils de coupe.
-
Applications des revêtements PVD
- Industrie automobile : Utilisé pour le revêtement de pièces automobiles telles que les pistons, les roues et les composants du moteur afin d'améliorer la durabilité et de réduire les frottements.
- Industrie aérospatiale : Appliqué aux pales de turbines et à d'autres composants critiques pour améliorer la résistance à l'usure et à la corrosion.
- Dispositifs médicaux : Utilisés pour les outils chirurgicaux et les implants afin de garantir la biocompatibilité et la longévité.
- Semi-conducteurs et électronique : Employés dans les revêtements en couches minces pour l'énergie photovoltaïque, les dispositifs à semi-conducteurs et les revêtements antireflets.
- Outils et machines : Prolonge la durée de vie des forets, des outils de coupe et des moules en offrant une surface dure et résistante à l'usure.
-
Avantages par rapport aux méthodes de revêtement traditionnelles
- Durabilité : Les revêtements PVD peuvent multiplier par dix la durée de vie des produits, certains revêtements ayant une durée de vie supérieure à 25 ans.
- Avantages pour l'environnement : Le processus ne fait pas appel à des produits chimiques toxiques, ce qui en fait une alternative plus écologique au chromage.
- Polyvalence : Les revêtements PVD peuvent être appliqués à une large gamme de matériaux, y compris les métaux, les polymères et les céramiques.
-
Défis et limites
- Uniformité du revêtement : Bien que les revêtements PVD soient généralement uniformes, il peut être difficile d'obtenir une épaisseur constante sur des géométries complexes (par exemple, l'arrière et les côtés des outils) en raison de la faible pression de l'air pendant le dépôt.
- Le coût : Les exigences en matière d'équipement et de processus pour le revêtement PVD peuvent être plus coûteuses que les méthodes traditionnelles, bien que les avantages à long terme justifient souvent l'investissement.
-
Tendances futures des revêtements PVD
- Matériaux avancés : Des recherches sont en cours pour mettre au point de nouveaux revêtements PVD présentant des caractéristiques encore plus performantes, telles qu'une meilleure stabilité thermique et une biocompatibilité accrue.
- Durabilité : Les industries privilégiant des processus de fabrication plus écologiques, la demande de revêtements PVD devrait croître en raison de leurs avantages environnementaux.
En résumé, les revêtements PVD constituent un choix supérieur pour les applications nécessitant une grande durabilité, une résistance à l'usure et une durabilité environnementale.Leur polyvalence et leurs performances les rendent indispensables dans des secteurs allant de l'automobile aux appareils médicaux, et les progrès en cours continuent d'élargir leurs applications potentielles.
Tableau récapitulatif :
Aspect clé | Détails |
---|---|
Qu'est-ce que le revêtement PVD ? | Procédé de dépôt en couche mince permettant de créer des revêtements durables, uniformes et adhérents. |
Propriétés principales | Dureté élevée, résistance à la corrosion, faible frottement, uniformité, respect de l'environnement. |
Types courants | TiN (nitrure de titane), CrN (nitrure de chrome), DLC (carbone semblable au diamant). |
Applications | Industrie automobile, aérospatiale, dispositifs médicaux, outils et semi-conducteurs. |
Avantages | Durabilité, avantages environnementaux, polyvalence. |
Défis | Uniformité sur des géométries complexes, coût initial plus élevé. |
Tendances futures | Matériaux avancés, innovations axées sur le développement durable. |
Prêt à améliorer vos produits avec des revêtements PVD ? Contactez nous dès aujourd'hui pour en savoir plus !