Le dépôt physique en phase vapeur (PVD) et le dépôt chimique en phase vapeur (CVD) sont deux techniques de dépôt de couches minces utilisées dans diverses industries, chacune ayant des caractéristiques, des avantages et des limites distincts.Le dépôt en phase vapeur par procédé physique repose sur des processus physiques, tels que l'évaporation ou la pulvérisation, pour déposer des couches minces sous vide, généralement à des températures plus basses (250°C~500°C).Il produit des revêtements minces et ultra-durs (3~5μm) avec une contrainte de compression, ce qui le rend idéal pour des applications telles que la coupe interrompue (par exemple, le fraisage).Le dépôt en phase vapeur (CVD), quant à lui, implique des réactions chimiques à des températures élevées (800~1000°C) pour déposer des revêtements plus épais (10~20μm) avec une uniformité et une densité excellentes, ce qui le rend adapté aux processus de coupe continue (par exemple, le tournage).Le dépôt en phase vapeur (PVD) permet de déposer une plus large gamme de matériaux, notamment des métaux, des alliages et des céramiques, alors que le dépôt en phase vapeur (CVD) se limite généralement aux céramiques et aux polymères.Les revêtements PVD sont plus rapides à appliquer mais moins denses et moins uniformes, tandis que les revêtements CVD sont plus denses et plus uniformes mais nécessitent des temps de traitement plus longs.
Explication des points clés :
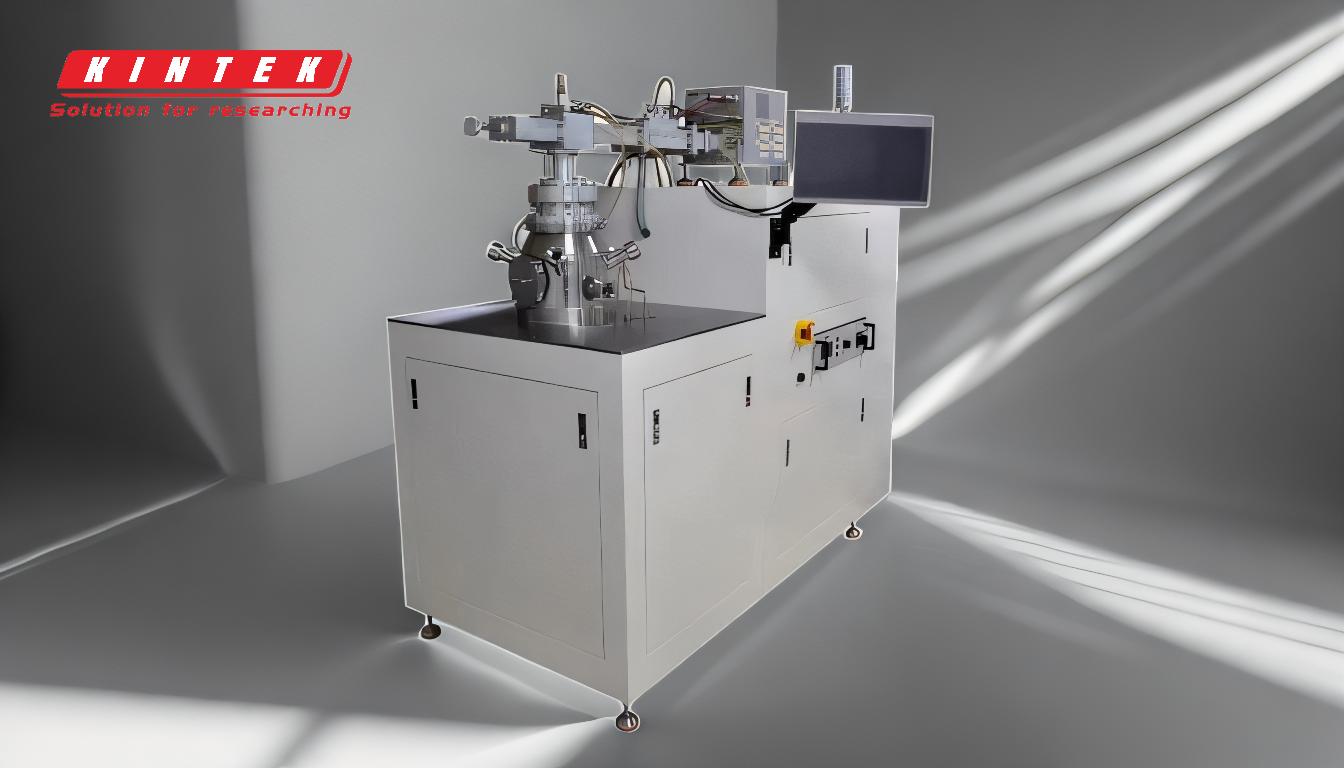
-
Processus de dépôt:
- PVD:Utilise des processus physiques tels que l'évaporation ou la pulvérisation dans un environnement sous vide.Le matériau est vaporisé à partir d'une cible solide et se condense sur le substrat.
- CVD:Il repose sur des réactions chimiques impliquant des précurseurs gazeux.Les gaz précurseurs réagissent à la surface du substrat pour former le revêtement.
-
Plage de température:
- PVD:Fonctionne à des températures relativement basses (250°C~500°C), ce qui le rend adapté aux substrats sensibles à la température.
- CVD:Nécessite des températures élevées (800~1000°C), ce qui limite son utilisation avec des matériaux qui ne peuvent pas supporter une telle chaleur.
-
Épaisseur du revêtement:
- PVD:Produit des revêtements plus fins (3~5μm) avec une contrainte de compression, idéal pour les applications de précision.
- CVD:Dépose des revêtements plus épais (10~20μm) avec une meilleure uniformité, adapté aux applications nécessitant des couches robustes et résistantes à l'usure.
-
Compatibilité des matériaux:
- PVD:Peut déposer une large gamme de matériaux, y compris des métaux, des alliages et des céramiques.
- CVD:Principalement limité aux céramiques et aux polymères en raison de la nature chimique du processus.
-
Propriétés du revêtement:
- PVD:Les revêtements sont moins denses et moins uniformes, mais plus rapides à appliquer.Ils sont très durables et peuvent résister à des températures plus élevées.
- CVD:Les revêtements sont plus denses, plus uniformes et présentent une excellente adhérence.Toutefois, ils sont plus longs à appliquer et conviennent moins bien aux processus de coupe interrompue.
-
Les applications:
- PVD:Convient le mieux aux processus de coupe interrompue (par exemple, le fraisage) et aux applications nécessitant des revêtements minces et durs.
- CVD:Idéal pour les processus de coupe continue (par exemple, le tournage) et les applications nécessitant des revêtements épais et résistants à l'usure.
-
Contrainte et adhérence:
- PVD:Forme une contrainte de compression pendant le refroidissement, ce qui améliore l'adhérence et la durabilité du revêtement.
- CVD:Il en résulte généralement une contrainte de traction qui peut affecter l'adhérence, mais qui est atténuée par le processus à haute température.
-
Vitesse de traitement:
- PVD:Des taux de dépôt plus rapides, ce qui le rend plus efficace pour la production en grande quantité.
- CVD:Les vitesses de dépôt sont plus lentes en raison du processus de réaction chimique, mais elles permettent d'obtenir une qualité de revêtement supérieure.
-
Considérations environnementales:
- PVD:Fonctionne sous vide, ce qui réduit la contamination de l'environnement et le rend plus propre.
- CVD:Implique des réactions chimiques et nécessite souvent la manipulation de précurseurs volatils, ce qui peut poser des problèmes d'environnement et de sécurité.
-
Coût et complexité:
- PVD:Généralement moins coûteux et plus simple à mettre en œuvre en raison des exigences de température moins élevées et des temps de traitement plus rapides.
- CVD:Plus coûteux et plus complexe en raison de l'équipement à haute température, des temps de traitement plus longs et de la nécessité d'un contrôle précis des réactions chimiques.
En comprenant ces différences clés, les acheteurs d'équipements et de consommables peuvent prendre des décisions éclairées quant à la technique de revêtement la mieux adaptée aux exigences de leurs applications spécifiques.Le dépôt en phase vapeur (PVD) est idéal pour la précision, la durabilité et les applications sensibles à la température, tandis que le dépôt en phase vapeur (CVD) permet d'obtenir des revêtements épais, uniformes et résistants à l'usure pour les processus à haute température.
Tableau récapitulatif :
Aspect | PVD | CVD |
---|---|---|
Processus de dépôt | Processus physiques (évaporation/sprayage) dans un environnement sous vide. | Réactions chimiques avec des précurseurs gazeux sur le substrat. |
Plage de température | 250°C~500°C, convient aux matériaux sensibles à la température. | 800~1000°C, limité aux matériaux résistants à la chaleur. |
Épaisseur du revêtement | Revêtements minces (3~5μm) avec contrainte de compression. | Revêtements épais (10~20μm) avec une excellente uniformité. |
Compatibilité des matériaux | Métaux, alliages, céramiques. | Principalement les céramiques et les polymères. |
Propriétés du revêtement | Moins dense, moins uniforme, mais plus rapide à appliquer. | Plus dense, plus uniforme, mais plus lent à appliquer. |
Applications | Coupe interrompue (par exemple, fraisage), applications de précision. | Coupe continue (par exemple, tournage), applications résistantes à l'usure. |
Contrainte et adhérence | La contrainte de compression améliore l'adhérence et la durabilité. | Les contraintes de traction sont atténuées par le processus à haute température. |
Vitesse de traitement | Vitesses de dépôt plus rapides, idéales pour la production en grande quantité. | Des taux de dépôt plus lents mais une qualité de revêtement supérieure. |
Impact sur l'environnement | Processus plus propre grâce au fonctionnement sous vide. | Implique des précurseurs volatils, ce qui pose des problèmes d'environnement et de sécurité. |
Coût et complexité | Moins coûteux, plus simple à mettre en œuvre. | Plus coûteux et plus complexe en raison de l'équipement et des procédés à haute température. |
Vous avez besoin d'aide pour choisir entre le PVD et le CVD pour votre application ? Contactez nos experts dès aujourd'hui pour des conseils sur mesure !