Les réacteurs à lit fluidisé (FBR) sont largement utilisés dans diverses industries en raison de leurs avantages, tels que le mélange uniforme des particules, les gradients de température et le fonctionnement continu. Cependant, ils présentent également plusieurs inconvénients notables. Ceux-ci incluent une taille accrue de la cuve du réacteur, des exigences de pompage et une chute de pression plus élevées, l'entraînement de particules, l'érosion des composants internes et des scénarios de perte de pression. De plus, les pyrolyseurs à lit fluidisé, un type spécifique de FBR, sont confrontés à des défis tels que le besoin de particules de petite taille, de grandes quantités de gaz inertes et des coûts d'exploitation élevés. Comprendre ces inconvénients est crucial pour prendre des décisions éclairées lors de l’examen des FBR pour des applications spécifiques.
Points clés expliqués :
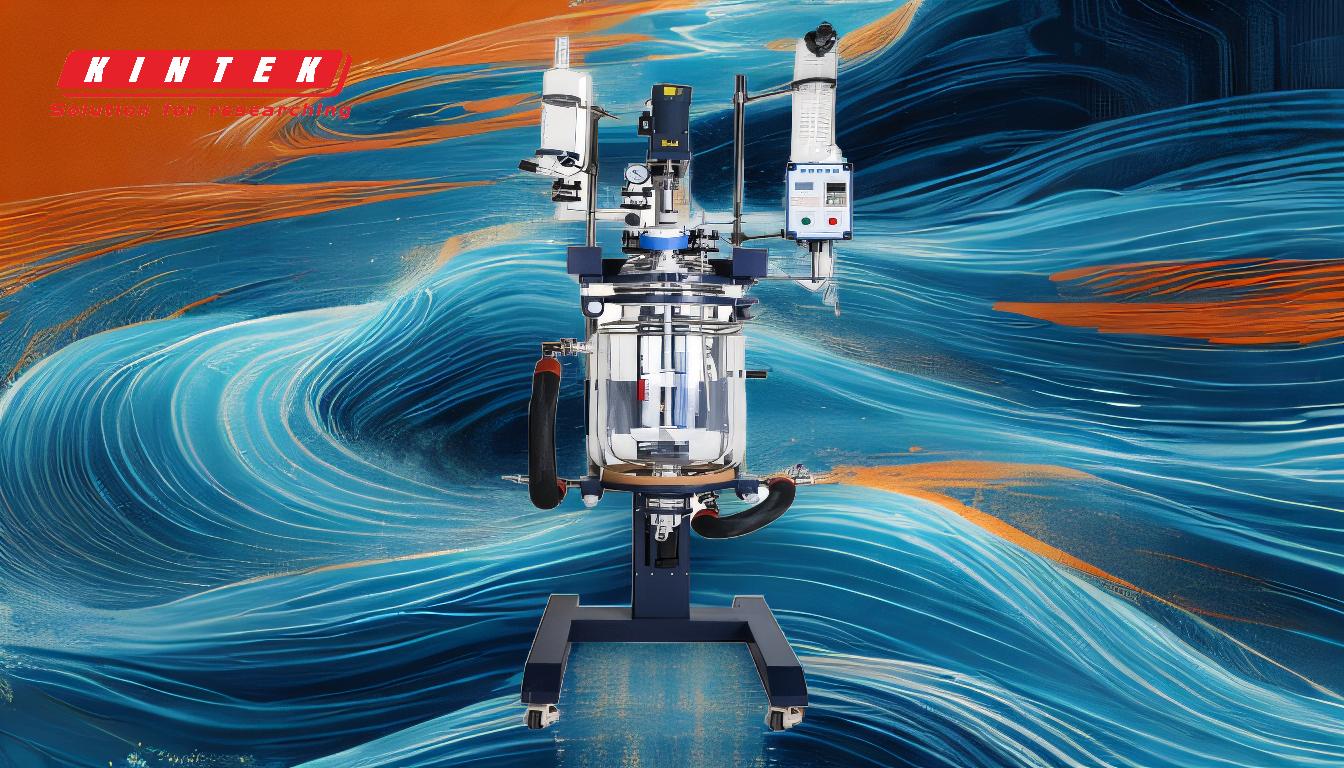
-
Augmentation de la taille de la cuve du réacteur:
- Les réacteurs à lit fluidisé nécessitent souvent des cuves de plus grande taille que les autres types de réacteurs. Cela est dû à la nécessité d’accueillir les particules fluidisées et de garantir des conditions de mélange et de réaction appropriées. Une taille plus grande peut entraîner des coûts d'investissement plus élevés et des besoins en espace plus importants, ce qui peut ne pas être réalisable pour toutes les applications.
-
Exigences de pompage et chute de pression plus élevées:
- Les FBR nécessitent généralement une puissance de pompage plus élevée pour maintenir l’état fluidisé des particules. Cela entraîne une augmentation de la consommation d’énergie et des coûts opérationnels. De plus, la chute de pression à travers le lit peut être importante, nécessitant des systèmes de pompage robustes et coûteux pour maintenir les débits souhaités.
-
Entraînement des particules:
- L’un des défis des FBR est l’entraînement des fines particules dans le flux gazeux. Cela peut entraîner une perte de réactifs ou de produits précieux et nécessiter des équipements supplémentaires, tels que des cyclones ou des filtres, pour capturer et recycler les particules entraînées. Cela ajoute de la complexité et du coût au système.
-
Érosion des composants internes:
- Le mouvement continu des particules dans un lit fluidisé peut provoquer l'érosion des composants internes, tels que les parois du réacteur, les plaques distributrices et les échangeurs de chaleur. Cette érosion peut entraîner une maintenance et un remplacement fréquents des pièces, augmentant ainsi les coûts opérationnels globaux et les temps d'arrêt.
-
Scénarios de perte de pression:
- Les FBR sont sensibles à des scénarios de perte de pression, qui peuvent perturber le processus de fluidisation et affecter les performances globales du réacteur. La gestion et l'atténuation de ces pertes de pression nécessitent une conception et une surveillance minutieuses, ce qui ajoute à la complexité et au coût du système.
-
Exigence relative aux petites tailles de particules:
- Les pyrolyseurs à lit fluidisé, un type spécifique de FBR, nécessitent de petites tailles de particules pour obtenir des performances optimales. Cela nécessite des étapes de traitement supplémentaires pour réduire la taille des particules, ce qui peut augmenter le coût global et la complexité du système.
-
Grande quantité de gaz inertes:
- Le fonctionnement des pyrolyseurs à lit fluidisé nécessite souvent une grande quantité de gaz inertes pour maintenir les conditions de réaction souhaitées. Cela peut entraîner des coûts opérationnels plus élevés et la nécessité d’infrastructures supplémentaires de manutention et de stockage du gaz.
-
Coûts d'exploitation élevés:
- La combinaison d'exigences de pompage plus élevées, d'entraînement de particules, d'érosion des composants internes et du besoin de particules de petite taille et de gaz inertes contribue aux coûts d'exploitation élevés associés aux FBR. Ces coûts peuvent constituer un inconvénient majeur, en particulier pour les applications où la rentabilité est un facteur critique.
En résumé, si les réacteurs à lit fluidisé offrent plusieurs avantages, tels qu’un mélange uniforme et des gradients de température, ils présentent également des inconvénients notables qui doivent être soigneusement pris en compte. Ceux-ci incluent une taille accrue du réacteur, des exigences de pompage plus élevées, l'entraînement de particules, l'érosion des composants internes, des scénarios de perte de pression et des coûts d'exploitation élevés. Comprendre ces inconvénients est essentiel pour prendre des décisions éclairées lors de la sélection et de la conception de FBR pour des applications spécifiques.
Tableau récapitulatif :
Inconvénient | Description |
---|---|
Augmentation de la taille de la cuve du réacteur | Les navires plus grands augmentent les coûts d’investissement et les besoins en espace. |
Exigences de pompage plus élevées | Nécessite plus d’énergie et des systèmes robustes pour maintenir la fluidisation. |
Entraînement des particules | Des particules fines peuvent s'échapper, nécessitant un équipement supplémentaire pour la récupération. |
Érosion des composants internes | Le mouvement continu des particules provoque une usure, conduisant à un entretien fréquent. |
Scénarios de perte de pression | Les chutes de pression peuvent perturber la fluidisation, nécessitant une conception et une surveillance minutieuses. |
Exigence relative aux petites tailles de particules | Un traitement supplémentaire est nécessaire pour réduire la taille des particules, ce qui augmente les coûts. |
Grande quantité de gaz inertes | Coûts d'exploitation élevés en raison du besoin de gaz inertes. |
Coûts d'exploitation élevés | La combinaison de ces facteurs entraîne des dépenses opérationnelles importantes. |
Besoin d'aide pour décider si les réacteurs à lit fluidisé conviennent à votre application ? Contactez nos experts dès aujourd'hui !