Le dépôt de matériaux de revêtement désigne le processus d'application d'une fine couche de matériau sur un substrat afin d'en améliorer les propriétés, telles que la résistance à la corrosion, la résistance à l'usure, la conductivité électrique ou l'attrait esthétique.Ce procédé est largement utilisé dans des secteurs tels que l'automobile, l'aérospatiale, l'électronique et la fabrication.Les techniques de dépôt varient en fonction des propriétés souhaitées, du matériau du substrat et des exigences de l'application.Les méthodes les plus courantes sont le dépôt physique en phase vapeur (PVD), le dépôt chimique en phase vapeur (CVD), la galvanoplastie et la pulvérisation thermique.Chaque méthode présente ses propres avantages et limites, ce qui la rend adaptée à des applications spécifiques.Il est essentiel de comprendre le processus de dépôt pour choisir la bonne technique afin d'obtenir les propriétés de revêtement souhaitées.
Explication des points clés :
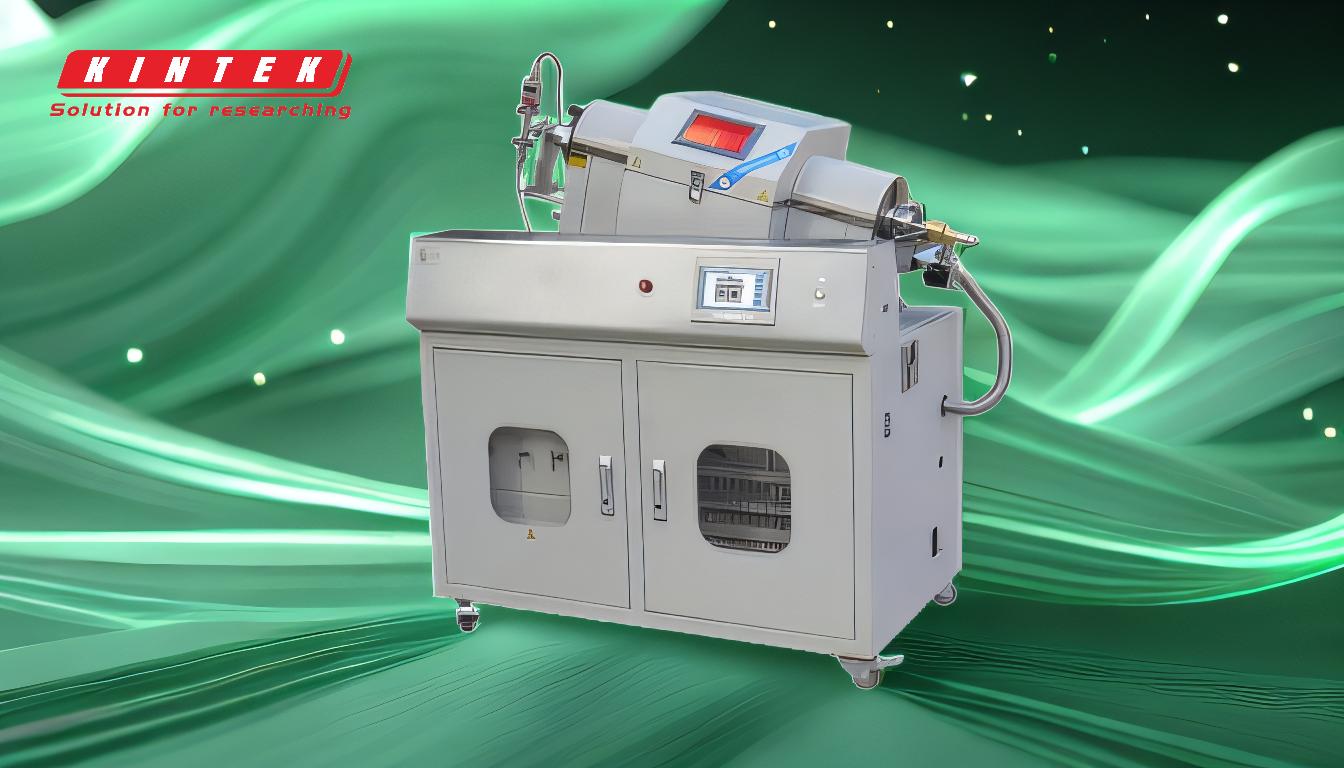
-
Définition du dépôt de revêtement:
- Le dépôt de revêtement est le processus d'application d'une fine couche de matériau sur un substrat.Cette couche peut être métallique, céramique, polymère ou composite, en fonction de l'application.
- L'objectif principal est d'améliorer les performances du substrat en renforçant des propriétés telles que la dureté, la résistance à la corrosion, l'isolation thermique ou la conductivité électrique.
-
Importance du dépôt de revêtement:
- Protection:Les revêtements protègent les substrats des facteurs environnementaux tels que la corrosion, l'oxydation et l'usure.
- Fonctionnalité:Ils peuvent ajouter des propriétés fonctionnelles, telles que la conductivité électrique ou l'isolation thermique.
- Esthétique:Les revêtements sont souvent utilisés pour améliorer l'apparence des produits, comme les finitions décoratives sur les biens de consommation.
-
Techniques de dépôt courantes:
-
Dépôt physique en phase vapeur (PVD):
- Le dépôt en phase vapeur (PVD) consiste à vaporiser le matériau de revêtement sous vide et à le déposer sur le substrat.Les techniques utilisées sont la pulvérisation cathodique et l'évaporation.
- Elle est utilisée pour les revêtements durs et résistants à l'usure, tels que le nitrure de titane (TiN) sur les outils de coupe.
-
Dépôt chimique en phase vapeur (CVD):
- Le dépôt en phase vapeur (CVD) utilise des réactions chimiques pour déposer un revêtement sur le substrat à partir d'une phase gazeuse.Il est idéal pour les applications à haute température et produit des revêtements uniformes et de haute qualité.
- Les applications comprennent la fabrication de semi-conducteurs et les revêtements de protection sur les pales de turbines.
-
Galvanisation:
- La galvanoplastie utilise un courant électrique pour déposer un revêtement métallique sur un substrat conducteur.Elle est couramment utilisée pour les finitions décoratives, la protection contre la corrosion et l'amélioration de la conductivité électrique.
-
Pulvérisation thermique:
- Cette technique consiste à faire fondre le matériau de revêtement et à le pulvériser sur le substrat.Elle est utilisée pour les revêtements épais et les grandes surfaces, comme dans les industries aérospatiale et automobile.
-
Dépôt physique en phase vapeur (PVD):
-
Facteurs influençant le dépôt:
- Matériau du substrat:Le choix de la méthode de dépôt dépend des propriétés du substrat, telles que la stabilité thermique et la rugosité de la surface.
- Matériau de revêtement:Les différents matériaux nécessitent des techniques de dépôt spécifiques pour obtenir les propriétés souhaitées.
- Exigences en matière d'application:L'utilisation prévue du produit revêtu détermine l'épaisseur du revêtement, la force d'adhérence et d'autres critères de performance.
-
Avantages et limites:
-
Avantages:
- Amélioration de la durabilité et des performances des substrats.
- Possibilité d'adapter les revêtements à des applications spécifiques.
- Amélioration de la durée de vie des produits et réduction des coûts d'entretien.
-
Limites:
- Coûts d'équipement et d'exploitation élevés pour certaines techniques.
- Complexité de l'obtention de revêtements uniformes sur des géométries complexes.
- Préoccupations en matière d'environnement et de sécurité, en particulier avec les méthodes à base de produits chimiques.
-
Avantages:
-
Applications du dépôt de revêtement:
- Automobile:Les revêtements sont utilisés sur les composants des moteurs, les systèmes de freinage et les garnitures décoratives pour améliorer les performances et l'esthétique.
- L'aérospatiale:Des revêtements protecteurs sont appliqués aux pales des turbines, au fuselage et à d'autres composants critiques pour résister à des conditions extrêmes.
- L'électronique:Des couches minces sont déposées sur les semi-conducteurs, les circuits et les écrans pour améliorer les propriétés électriques.
- Fabrication:Les outils de coupe, les moules et les matrices sont revêtus pour améliorer la résistance à l'usure et prolonger la durée de vie.
En comprenant le processus de dépôt et ses différentes techniques, les fabricants peuvent sélectionner la méthode la plus appropriée pour obtenir les propriétés de revêtement souhaitées pour leurs applications spécifiques.Cela garantit des performances optimales, la durabilité et la rentabilité des produits revêtus.
Tableau récapitulatif :
Aspect | Détails |
---|---|
Définition | Application d'une fine couche de matériau pour améliorer les propriétés du substrat. |
Principaux avantages | Résistance à la corrosion, résistance à l'usure, conductivité électrique, esthétique. |
Techniques courantes | PVD, CVD, galvanoplastie, pulvérisation thermique. |
Applications | Automobile, aérospatiale, électronique, fabrication. |
Avantages | Durabilité accrue, revêtements sur mesure, rentabilité. |
Limites | Coûts élevés, géométries complexes, préoccupations environnementales. |
Découvrez la meilleure solution de dépôt de revêtement pour vos besoins. contactez nos experts dès aujourd'hui !