Le dépôt chimique en phase vapeur (CVD) et le dépôt physique en phase vapeur (PVD) sont deux techniques largement utilisées pour appliquer des revêtements d'outils, chacune présentant des processus, des avantages et des limites distincts. Le CVD implique des réactions chimiques à des températures relativement plus basses, produisant des revêtements denses et uniformes adaptés aux géométries complexes. Le PVD, quant à lui, fonctionne sous vide à haute température, en utilisant des processus physiques pour déposer une gamme plus large de matériaux, notamment des métaux, des alliages et des céramiques. Alors que les revêtements PVD sont moins denses et plus rapides à appliquer, les revêtements CVD sont plus denses, plus uniformes et mieux adaptés aux formes complexes. Les deux méthodes nécessitent un équipement sophistiqué et des salles blanches, mais leurs applications diffèrent en fonction des propriétés de revêtement souhaitées et des exigences en matière d'outils.
Points clés expliqués :
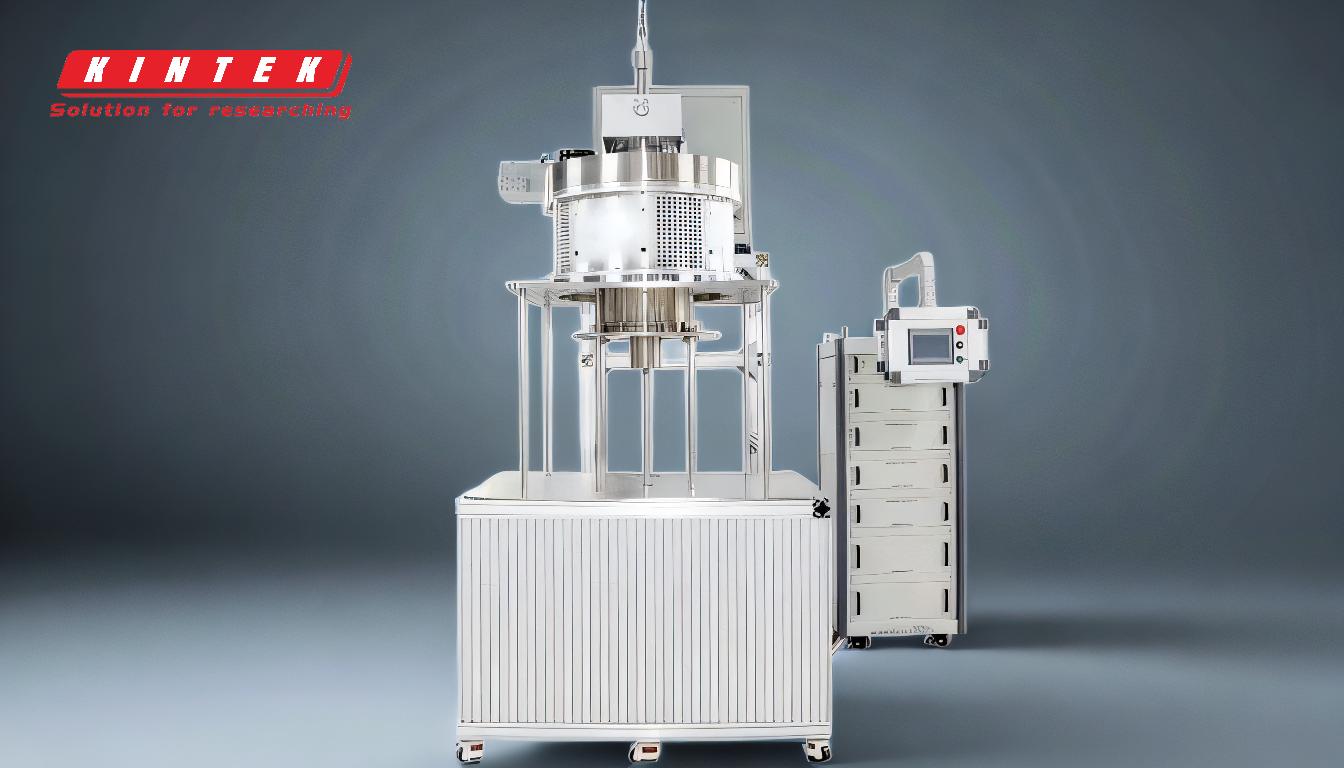
-
Gamme de matériaux et applicabilité:
- PVD: Peut déposer une grande variété de matériaux, notamment des métaux, des alliages et des céramiques. Cette polyvalence le rend adapté aux applications nécessitant diverses propriétés de matériaux.
- MCV: Principalement limité aux céramiques et aux polymères. Sa nature chimique restreint la gamme de matériaux mais permet des films de haute pureté et une synthèse de matériaux complexes.
-
Conditions de processus:
- PVD: Réalisé sous vide à haute température, impliquant des processus physiques comme l'évaporation ou la pulvérisation cathodique. Cela nécessite un équipement spécialisé, des conditions de vide et des opérateurs qualifiés.
- MCV: Fonctionne à des températures plus basses que le PVD, en s'appuyant sur des réactions chimiques pour déposer les revêtements. Il ne nécessite pas de conditions d’ultra-vide, ce qui le rend plus économique dans certains cas.
-
Propriétés du revêtement:
- PVD: Produit des revêtements moins denses et moins uniformes mais est plus rapide à appliquer. Le processus d’impaction en ligne de mire limite sa capacité à recouvrir uniformément des géométries complexes.
- MCV: Crée des revêtements plus denses et plus uniformes avec un excellent pouvoir de projection, lui permettant de recouvrir efficacement les trous, les creux profonds et les formes complexes.
-
Taux de dépôt et épaisseur:
- PVD: A généralement des taux de dépôt plus faibles, mais des techniques telles que le PVD par faisceau d'électrons (EBPVD) peuvent atteindre des taux élevés (0,1 à 100 μm/min) avec une efficacité d'utilisation élevée des matériaux.
- MCV: Offre des taux de dépôt plus élevés et peut produire des revêtements plus épais, allant de nanomètres à moins de 20 microns, par rapport aux méthodes conventionnelles.
-
Considérations relatives à la température et à l'environnement:
- PVD: Nécessite des températures et des conditions de vide élevées, ce qui peut limiter son utilisation pour les substrats sensibles à la chaleur. Cela nécessite également des systèmes de refroidissement pour dissiper la chaleur.
- MCV: Fonctionne à des températures plus basses (500°–1 100°C) et ne produit pas de sous-produits corrosifs, ce qui le rend plus respectueux de l'environnement et adapté à une plus large gamme de substrats.
-
Adéquation des applications:
- PVD: Idéal pour les applications nécessitant des processus de revêtement rapides et une large gamme de matériaux, tels que des revêtements résistants à l'usure et anticorrosion.
- MCV: Mieux adapté aux applications nécessitant des revêtements uniformes de haute pureté sur des formes complexes, telles que les dispositifs semi-conducteurs et les outils avancés.
-
Facteurs économiques et opérationnels:
- PVD: Nécessite un investissement important dans les systèmes de vide et une main-d'œuvre qualifiée, mais son temps d'application plus rapide peut compenser les coûts d'une production en grand volume.
- MCV: Souvent plus économique en raison de taux de dépôt plus élevés et de la capacité de revêtir des géométries complexes sans exigences d'ultra-vide.
En résumé, le choix entre CVD et PVD pour le revêtement d'outils dépend des exigences spécifiques de l'application, notamment des propriétés du matériau, de l'uniformité du revêtement, des taux de dépôt et de la complexité géométrique. Les deux méthodes ont leurs avantages et leurs limites uniques, ce qui en fait des technologies complémentaires plutôt que concurrentes dans le domaine de l’ingénierie des surfaces.
Tableau récapitulatif :
Aspect | MCV | PVD |
---|---|---|
Gamme de matériaux | Principalement des céramiques et des polymères | Métaux, alliages et céramiques |
Conditions de processus | Températures plus basses, réactions chimiques, aucun ultra-vide requis | Températures élevées, vide, processus physiques comme l'évaporation/pulvérisation |
Propriétés du revêtement | Plus dense, plus uniforme, excellent pour les formes complexes | Application moins dense et plus rapide, limitée par l'impactement de la ligne de vue |
Taux de dépôt | Taux plus élevés, revêtements plus épais (nanomètres à <20 microns) | Des débits inférieurs, mais l'EBPVD peut atteindre des débits élevés (0,1 à 100 μm/min) |
Température et environnement | Températures plus basses (500°–1 100°C), respectueux de l'environnement | Températures élevées, vide, nécessite des systèmes de refroidissement |
Adéquation des applications | Revêtements uniformes de haute pureté pour les formes complexes (par exemple, semi-conducteurs) | Revêtement rapide, matériaux divers (par exemple, résistant à l'usure, anticorrosion) |
Facteurs économiques | Économique pour les géométries complexes, taux de dépôt plus élevés | Un investissement initial élevé, mais une application plus rapide compense les coûts |
Besoin d'aide pour choisir entre CVD et PVD pour vos besoins de revêtement d'outils ? Contactez nos experts dès aujourd'hui pour des solutions sur mesure !