La principale différence entre les revêtements CVD (Chemical Vapor Deposition) et PCD (Physical Vapor Deposition) réside dans leurs processus de dépôt, les propriétés qui en résultent et leurs applications. Le dépôt en phase vapeur par procédé chimique implique des réactions chimiques à des températures élevées (800-1000°C) pour déposer des revêtements plus épais, plus denses et plus uniformes, ce qui le rend adapté aux processus de coupe continue tels que le tournage. En revanche, le dépôt en phase vapeur (PVD) fait appel à des procédés physiques à des températures plus basses (environ 500 °C) pour créer des revêtements plus fins, moins denses et soumis à des contraintes de compression, ce qui est idéal pour les procédés de coupe interrompus tels que le fraisage. Les revêtements CVD adhèrent fortement au substrat et sont plus résistants à l'abrasion, tandis que les revêtements PVD offrent une application plus rapide et une polyvalence dans le dépôt de matériaux.
Explication des points clés :
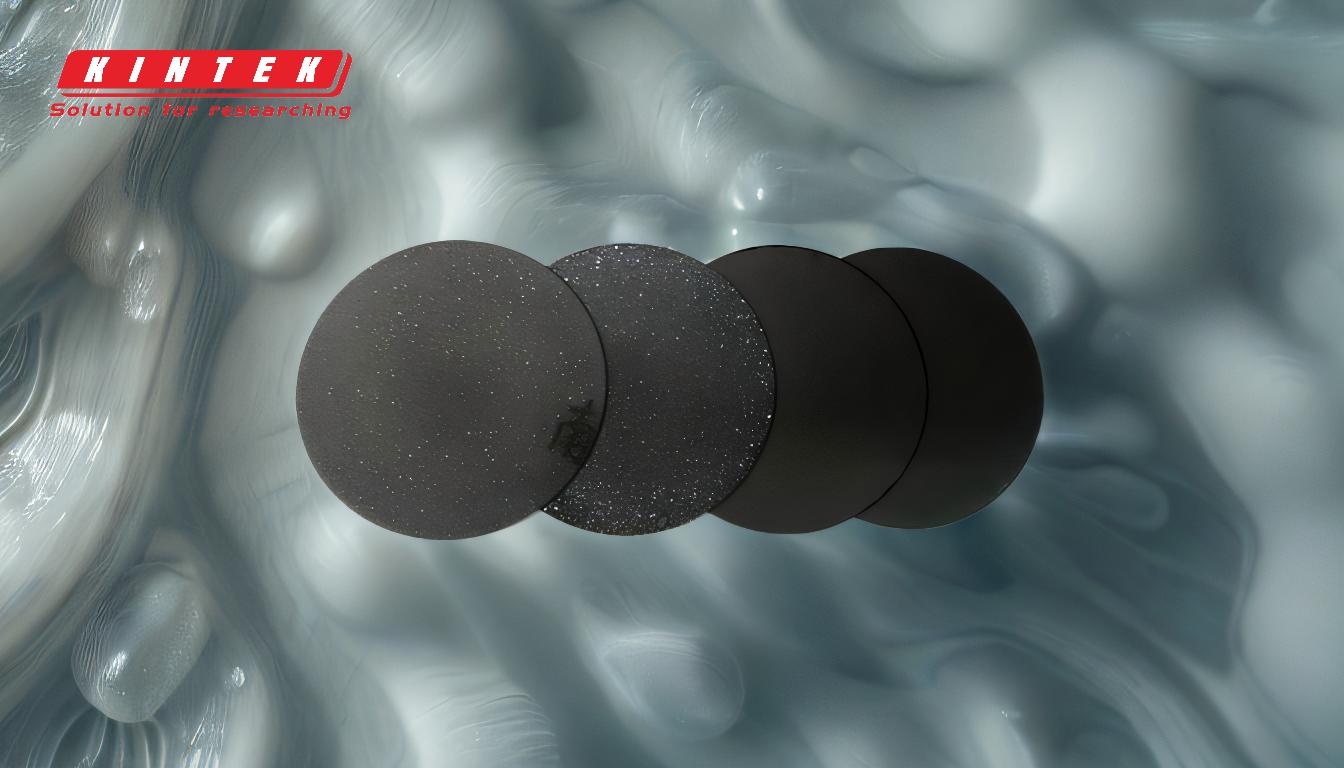
-
Processus de dépôt:
- MCV: Implique des réactions chimiques dans un environnement contrôlé utilisant des gaz réactifs à des températures élevées (800-1000°C). Le procédé dépose un revêtement plus épais (10-20μm) et forme une liaison de type diffusion avec le substrat, ce qui se traduit par une adhésion plus forte.
- PVD: Utilise des procédés physiques, tels que la décharge d'arc, pour évaporer une cible métallique sous vide à des températures plus basses (environ 500°C). Cela crée un revêtement plus fin (3-5μm) avec une contrainte de compression pendant le refroidissement.
-
Propriétés du revêtement:
- MCV: Produit des revêtements plus denses et plus uniformes avec une résistance élevée à l'abrasion et à l'usure. Cependant, la température élevée du traitement peut introduire des contraintes de traction résiduelles, ce qui rend l'équipement revêtu plus fragile.
- PVD: Il en résulte des revêtements moins denses et moins uniformes, mais les temps d'application sont plus courts. La contrainte de compression dans les revêtements PVD améliore leur aptitude aux processus de coupe interrompue.
-
Polyvalence des matériaux:
- MCV: Généralement limité aux céramiques et aux polymères en raison de la nature chimique du processus.
- PVD: Peut déposer une plus large gamme de matériaux, y compris des métaux, des alliages et des céramiques, ce qui offre une plus grande flexibilité dans les applications.
-
Applications:
- MCV: Convient parfaitement aux processus de coupe continue (par exemple, le tournage) et aux applications de formage des métaux soumises à de fortes contraintes, où le frottement de glissement et le grippage sont des problèmes. Sa capacité à revêtir des surfaces de forme irrégulière le rend également polyvalent.
- PVD: Idéal pour les processus de coupe interrompus (par exemple, le fraisage) en raison de sa contrainte de compression et des températures de traitement plus basses. Il est également préféré pour les applications nécessitant une plus large gamme de matériaux.
-
Résistance de l'adhérence et structure de la couche:
- MCV: Forme une liaison de type diffusion avec le substrat, ce qui renforce l'adhérence et améliore la structure de la couche et l'homogénéité de l'épaisseur.
- PVD: Crée une liaison mécanique, qui est généralement plus faible que la liaison de type diffusion de la CVD, mais suffisante pour de nombreuses applications.
-
Sensibilité à la température:
- MCV: Les températures de traitement élevées limitent son utilisation avec des substrats qui ne supportent pas une chaleur extrême.
- PVD: Les températures de traitement plus basses permettent d'utiliser des matériaux et des substrats sensibles à la température.
-
Uniformité et densité du revêtement:
- MCV: Permet d'obtenir des revêtements plus denses et plus uniformes, améliorant la durabilité et la résistance à l'usure.
- PVD: Les revêtements sont moins denses et moins uniformes mais peuvent être appliqués plus rapidement, ce qui les rend rentables pour certaines applications.
-
Contrainte résiduelle:
- MCV: Les tensions résiduelles peuvent fragiliser l'équipement revêtu, malgré sa résistance à l'abrasion.
- PVD: La contrainte de compression améliore la performance du revêtement dans les processus de coupe interrompue et réduit le risque de fissuration.
En comprenant ces différences clés, les acheteurs d'équipements et de consommables peuvent prendre des décisions éclairées en fonction des exigences spécifiques de leurs applications, telles que les processus de coupe, la compatibilité des matériaux et les propriétés de revêtement souhaitées.
Tableau récapitulatif :
Aspect | CVD (dépôt chimique en phase vapeur) | PVD (dépôt physique en phase vapeur) |
---|---|---|
Processus de dépôt | Réactions chimiques à haute température (800-1000°C) | Processus physiques à des températures plus basses (environ 500°C) |
Épaisseur du revêtement | Plus épais (10-20μm) | Plus fin (3-5μm) |
Densité du revêtement | Plus dense et plus uniforme | Moins dense et moins uniforme |
Force d'adhérence | Liaison de type diffusion, adhésion plus forte | Liaison mécanique, plus faible mais suffisante |
Polyvalence des matériaux | Limité aux céramiques et aux polymères | Gamme plus large (métaux, alliages, céramiques) |
Applications | Coupe continue (par exemple, tournage), formage de métaux sous forte contrainte | Coupe interrompue (par exemple, fraisage), matériaux sensibles à la température |
Contrainte résiduelle | Contrainte de traction, peut fragiliser l'équipement | Contrainte de compression, améliore les performances de la coupe interrompue |
Délai de traitement | Plus lent | Plus rapide |
Besoin d'aide pour choisir le bon revêtement pour votre application ? Contactez nos experts dès aujourd'hui pour un accompagnement personnalisé !