Le dépôt chimique en phase vapeur (CVD) et le dépôt physique en phase vapeur (PVD) sont deux technologies de revêtement largement utilisées, chacune ayant des processus, des propriétés et des applications distincts.Le dépôt chimique en phase vapeur fait appel à des réactions chimiques à des températures élevées (800-1000°C) pour déposer des revêtements plus épais (10-20μm), tandis que le dépôt physique en phase vapeur fait appel à des processus physiques tels que l'évaporation ou la pulvérisation à des températures plus basses (250-500°C) pour créer des films plus fins et ultra-durs (3-5μm).Les revêtements CVD sont plus denses et plus uniformes, mais leur application prend plus de temps, tandis que les revêtements PVD sont plus rapides à déposer, moins denses et moins uniformes.Le choix entre le dépôt en phase vapeur et le dépôt en phase vapeur dépend de facteurs tels que la compatibilité des matériaux, l'épaisseur du revêtement, la sensibilité à la température et les exigences de l'application.
Explication des points clés :
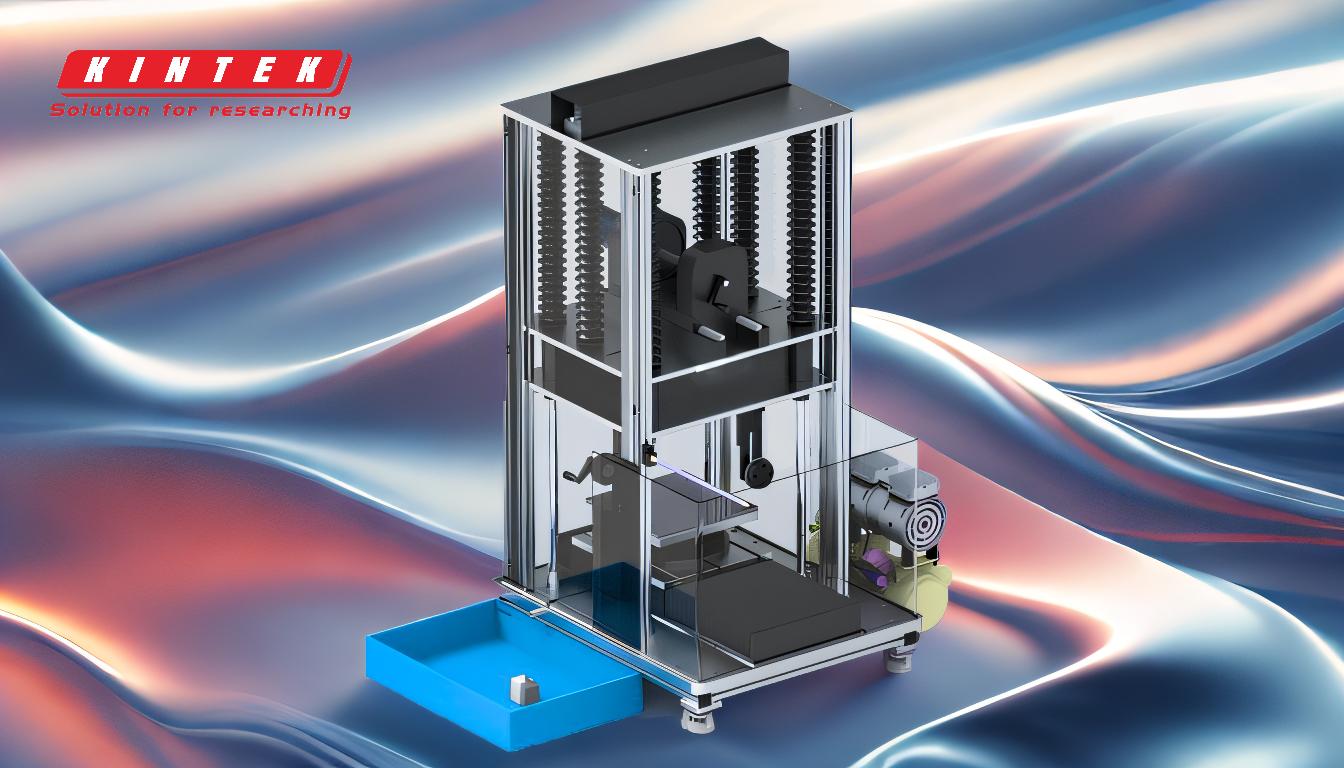
-
Mécanisme du processus:
- MCV:Le dépôt en phase vapeur (CVD) repose sur des réactions chimiques entre des précurseurs gazeux et la surface du substrat.Le processus se déroule à des températures élevées (800-1000°C), où les gaz se décomposent ou réagissent pour former un revêtement solide.Il en résulte un dépôt multidirectionnel qui assure une couverture uniforme, même sur des géométries complexes.
- PVD:Le PVD implique la vaporisation physique de matériaux solides (cibles) par des procédés tels que la pulvérisation ou l'évaporation.Les atomes vaporisés se condensent ensuite sur le substrat en ligne de mire, ce qui signifie que seules les surfaces directement exposées au flux de vapeur sont revêtues.
-
Exigences en matière de température:
- MCV:Fonctionne à des températures élevées (800-1000°C), ce qui peut limiter son utilisation sur des matériaux sensibles à la température.Les températures élevées entraînent également des tensions dans le revêtement, ce qui peut provoquer de fines fissures.
- PVD:Fonctionne à des températures nettement plus basses (250-500°C), ce qui le rend adapté aux substrats sensibles à la température.Les températures plus basses entraînent une contrainte de compression qui améliore l'adhérence et la durabilité du revêtement.
-
Épaisseur et uniformité du revêtement:
- MCV:Produit des revêtements plus épais (10-20μm) avec une uniformité et une densité excellentes.Le dépôt multidirectionnel assure une couverture uniforme sur les formes complexes et les surfaces internes.
- PVD:Crée des revêtements plus fins (3-5μm) avec moins d'uniformité en raison du dépôt en ligne de mire.Cependant, les revêtements PVD sont plus rapides à appliquer et permettent d'obtenir des surfaces ultra-dures.
-
Compatibilité des matériaux:
- MCV:Généralement limité aux céramiques et aux polymères en raison de la nature chimique du procédé.Il est idéal pour les applications nécessitant une résistance à l'usure et une stabilité à haute température.
- PVD:Peut déposer une plus large gamme de matériaux, y compris les métaux, les alliages et les céramiques.Grâce à cette polyvalence, le dépôt en phase vapeur convient aux applications nécessitant des finitions décoratives, une résistance à la corrosion ou des propriétés mécaniques améliorées.
-
Contrainte et adhérence:
- MCV:Les températures de traitement élevées entraînent souvent des contraintes de traction dans le revêtement, ce qui peut provoquer de fines fissures ou un décollement au fil du temps.
- PVD:Les températures plus basses et la contrainte de compression pendant le refroidissement améliorent l'adhérence du revêtement et réduisent le risque de fissuration, ce qui rend les revêtements PVD plus durables dans certaines applications.
-
Vitesse d'application:
- MCV:L'application est plus longue en raison du processus de réaction chimique et des températures élevées requises.
- PVD:L'application est plus rapide car elle repose sur la vaporisation et la condensation physiques, ce qui la rend plus efficace pour les applications à haut débit.
-
Applications:
- MCV:Les revêtements sont couramment utilisés dans les industries exigeant des performances élevées, telles que la fabrication de semi-conducteurs, les outils de coupe et les composants aérospatiaux.
- PVD:Largement utilisé pour les revêtements décoratifs, les surfaces résistantes à l'usure et les composants de précision dans des secteurs tels que l'automobile, les appareils médicaux et l'optique.
En résumé, le choix entre CVD et PVD dépend des exigences spécifiques de l'application, notamment de la compatibilité des matériaux, de l'épaisseur du revêtement, de la sensibilité à la température et des propriétés souhaitées.Les deux technologies offrent des avantages uniques qui les rendent indispensables à la fabrication moderne et à l'ingénierie des surfaces.
Tableau récapitulatif :
Aspect | CVD | PVD |
---|---|---|
Mécanisme du procédé | Réactions chimiques à haute température (800-1000°C) | Vaporisation physique à basse température (250-500°C) |
Température | Haute (800-1000°C), limite l'utilisation sur les matériaux sensibles à la température | Faible (250-500°C), convient aux substrats sensibles à la température |
Épaisseur du revêtement | Plus épais (10-20μm), dense et uniforme | Plus mince (3-5μm), moins uniforme, ultra-dur |
Compatibilité des matériaux | Limitée aux céramiques et aux polymères | Large éventail, y compris les métaux, les alliages et les céramiques |
Contrainte et adhérence | Contrainte de traction, risque de fissures fines | Contrainte de compression, amélioration de l'adhérence et de la durabilité |
Vitesse d'application | Plus lente en raison des réactions chimiques et des températures élevées | Plus rapide, idéal pour les applications à haut débit |
Applications | Fabrication de semi-conducteurs, outils de coupe, composants aérospatiaux | Revêtements décoratifs, surfaces résistantes à l'usure, composants de précision |
Vous avez besoin d'aide pour choisir entre les revêtements CVD et PVD ? Contactez nos experts dès aujourd'hui pour trouver la meilleure solution pour votre application !