Le CVD (Chemical Vapor Deposition) et le PVD (Physical Vapor Deposition) sont deux techniques largement utilisées pour déposer des films ou des revêtements minces sur des substrats, mais elles diffèrent considérablement par leurs processus, leurs matériaux et leurs applications. La CVD implique des réactions chimiques entre les précurseurs gazeux et le substrat, ce qui donne lieu à des revêtements plus épais et plus rugueux pouvant être appliqués sur une large gamme de matériaux. Le PVD, quant à lui, utilise la vaporisation physique de matériaux solides, produisant des revêtements plus fins, plus lisses et plus durables. Le choix entre CVD et PVD dépend de facteurs tels que l'épaisseur du revêtement, la tolérance à la température et les exigences spécifiques de l'application.
Points clés expliqués :
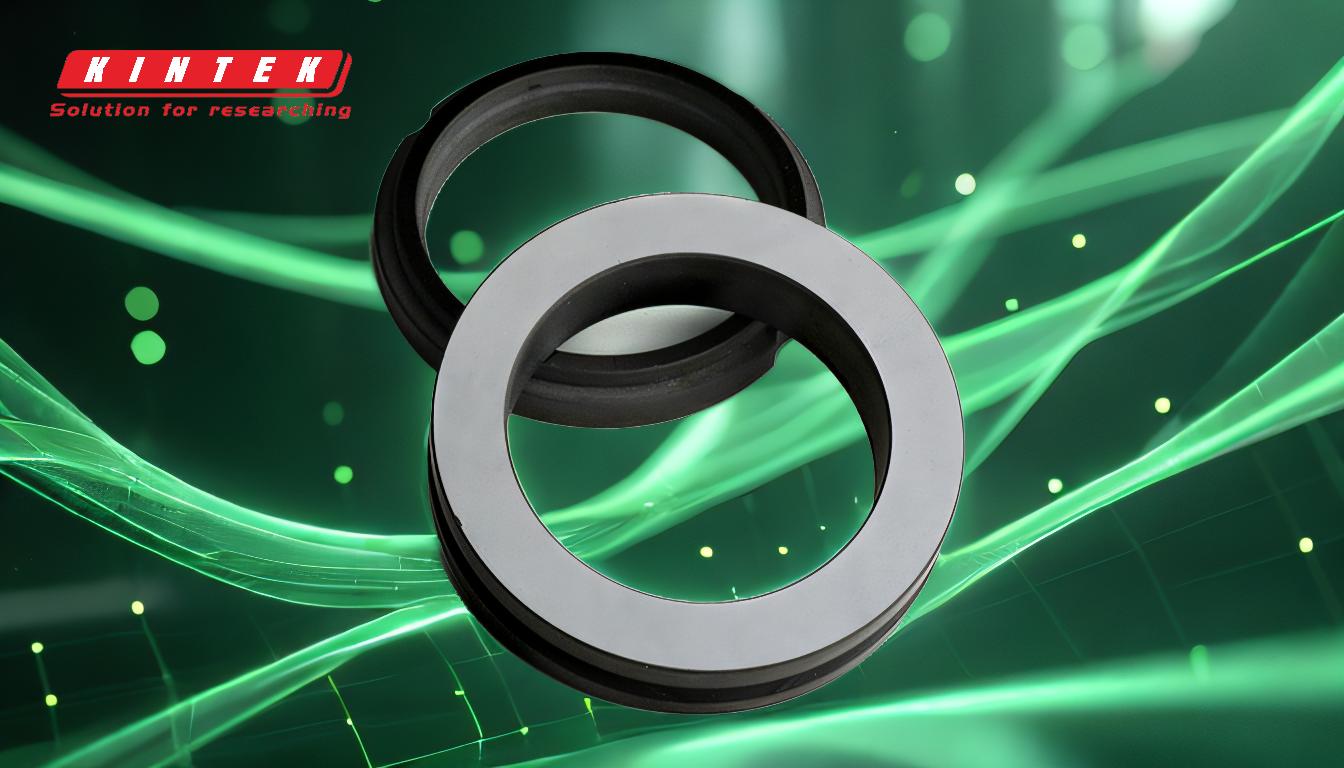
-
Processus de dépôt:
- MCV: La CVD repose sur des réactions chimiques entre des précurseurs gazeux et le substrat. Les gaz réagissent à des températures élevées (450°C à 1 050°C) pour former un revêtement solide sur le substrat. Ce processus est multidirectionnel, ce qui signifie que le revêtement peut être appliqué uniformément sur des géométries complexes.
- PVD: Le PVD implique la vaporisation physique de matériaux solides, qui sont ensuite déposés sur le substrat. Ce processus s'effectue en visibilité directe, ce qui signifie que le matériau est déposé directement sur le substrat sans interaction chimique. Le PVD fonctionne à des températures plus basses (250°C à 450°C).
-
Matériaux de revêtement:
- MCV: Le CVD utilise des matières gazeuses comme précurseurs. Ces gaz réagissent chimiquement pour former le revêtement, qui peut être plus épais (10 ~ 20 μm) et plus rugueux par rapport aux revêtements PVD.
- PVD: Le PVD utilise des matériaux solides qui sont vaporisés puis condensés sur le substrat. Les revêtements résultants sont plus fins (3 ~ 5 μm), plus lisses et plus durables.
-
Exigences de température:
- MCV: Le CVD nécessite des températures élevées (450°C à 1050°C) pour faciliter les réactions chimiques nécessaires au dépôt. Ce processus à haute température peut entraîner des contraintes de traction et de fines fissures dans le revêtement.
- PVD: Le PVD fonctionne à des températures plus basses (250°C à 450°C), ce qui minimise le risque de dommages thermiques au substrat. La température plus basse entraîne également des contraintes de compression pendant le refroidissement, améliorant ainsi la durabilité du revêtement.
-
Propriétés du revêtement:
- MCV: Les revêtements CVD sont généralement plus épais et plus rugueux, ce qui les rend adaptés aux applications où une surface robuste et résistante à l'usure est nécessaire. Cependant, la température de traitement élevée peut limiter les types de substrats pouvant être recouverts.
- PVD: Les revêtements PVD sont plus fins, plus lisses et plus uniformes, ce qui les rend idéaux pour les applications nécessitant précision et durabilité. La température de traitement plus basse permet d'utiliser une plus large gamme de matériaux de substrat.
-
Applications:
- MCV: Le CVD est couramment utilisé dans les applications nécessitant des revêtements épais et résistants à l'usure, comme dans l'industrie des semi-conducteurs, les outils de coupe et les composants résistants à l'usure.
- PVD: Le PVD est souvent utilisé dans des applications nécessitant des revêtements fins, durables et lisses, comme dans l'industrie aérospatiale, les dispositifs médicaux et les finitions décoratives.
-
Formation de contraintes et de fissures:
- MCV: Les températures élevées en CVD peuvent entraîner des contraintes de traction et de fines fissures dans le revêtement, ce qui peut affecter ses performances dans certaines applications.
- PVD: Les revêtements PVD subissent généralement des contraintes de compression, ce qui améliore leur durabilité et leur résistance à la fissuration.
En résumé, le choix entre CVD et PVD dépend des exigences spécifiques de l'application, notamment de l'épaisseur de revêtement souhaitée, de la tolérance à la température et des types de matériaux impliqués. Les deux techniques ont leurs avantages et leurs limites uniques, ce qui les rend adaptées à différentes applications industrielles.
Tableau récapitulatif :
Aspect | MCV | PVD |
---|---|---|
Processus de dépôt | Réactions chimiques entre les gaz et le substrat à haute température. | Vaporisation physique de matériaux solides à des températures plus basses. |
Matériaux de revêtement | Précurseurs gazeux ; revêtements plus épais (10 ~ 20 μm), plus rugueux. | Matériaux solides ; revêtements plus fins (3 ~ 5 μm), plus lisses et plus durables. |
Température | Élevé (450 °C à 1 050 °C) ; peut provoquer des contraintes de traction et des fissures. | Inférieur (250°C à 450°C) ; minimise les dommages thermiques et améliore la durabilité. |
Propriétés du revêtement | Plus épais, plus rugueux, résistant à l'usure ; limité par la tolérance aux températures élevées. | Plus fin, plus lisse, uniforme ; adapté à la précision et à la durabilité. |
Applications | Semi-conducteurs, outils de coupe, composants résistants à l'usure. | Aéronautique, dispositifs médicaux, finitions décoratives. |
Formation de contraintes | Contrainte de traction ; de fines fissures peuvent apparaître. | Contrainte de compression ; améliore la durabilité et la résistance aux fissures. |
Vous ne savez toujours pas quelle technique de revêtement convient à votre application ? Contactez nos experts dès aujourd'hui pour des conseils personnalisés !