La température de fusion des céramiques est généralement plus élevée que celle de la plupart des métaux en raison de la nature de leur liaison atomique et de leur structure. Les céramiques sont principalement composées de liaisons ioniques ou covalentes, qui sont beaucoup plus fortes que les liaisons métalliques que l'on trouve dans les métaux. Ces liaisons fortes nécessitent plus d'énergie pour être rompues, ce qui se traduit par des points de fusion plus élevés. En outre, les céramiques ont souvent des structures cristallines complexes avec des énergies de réseau élevées, ce qui contribue à leur stabilité thermique. Les métaux, quant à eux, ont des liaisons métalliques relativement plus faibles et plus délocalisées, ce qui leur permet de fondre à des températures plus basses. La combinaison de liaisons fortes et de structures cristallines stables rend les céramiques plus résistantes à la chaleur et explique leurs températures de fusion plus élevées.
Explication des points clés :
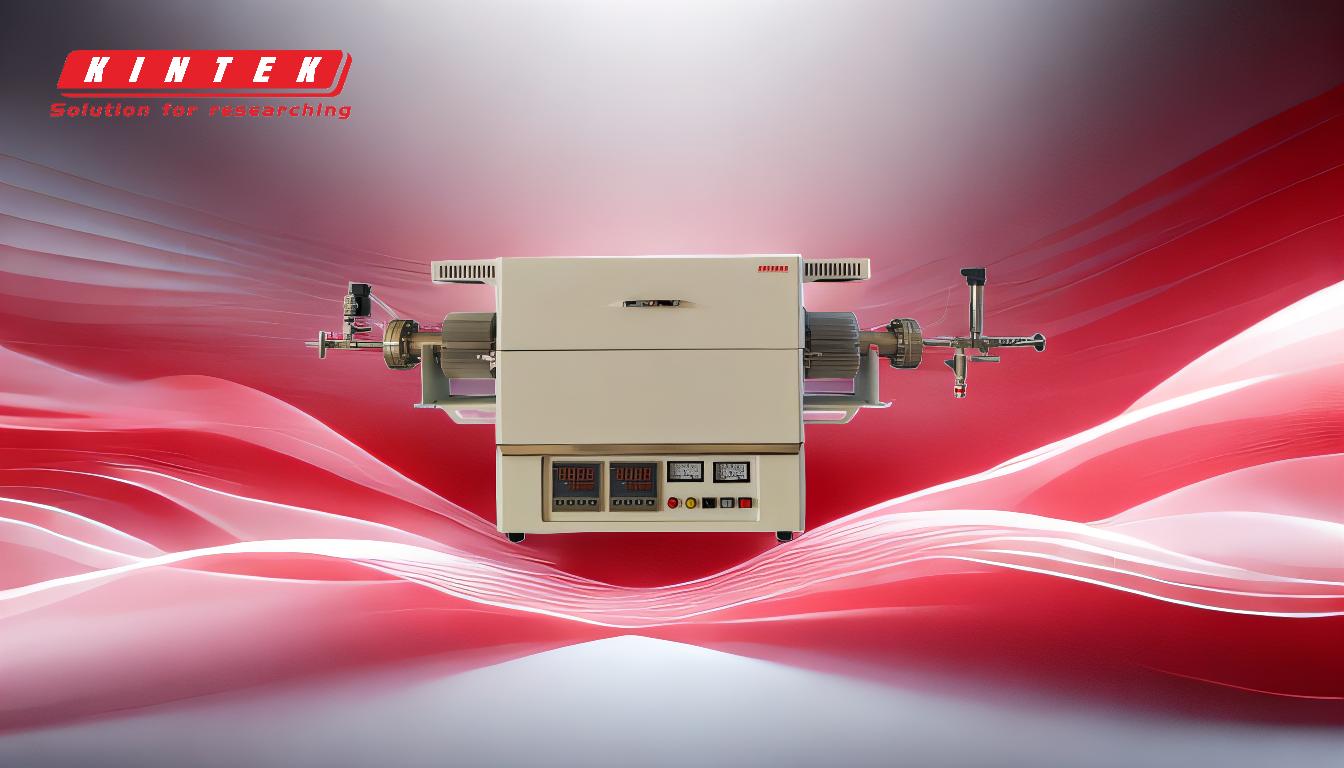
-
Types de liaisons atomiques:
- Céramique: Les céramiques sont principalement maintenues ensemble par des liaisons ioniques ou covalentes. Les liaisons ioniques impliquent l'attraction électrostatique entre des ions chargés positivement et négativement, tandis que les liaisons covalentes impliquent le partage d'électrons entre les atomes. Ces deux types de liaisons sont très solides et nécessitent une quantité importante d'énergie pour être rompues.
- Métaux: Les métaux sont maintenus ensemble par des liaisons métalliques, caractérisées par une "mer" d'électrons délocalisés qui se déplacent librement entre les ions métalliques chargés positivement. Ces liaisons sont généralement plus faibles que les liaisons ioniques ou covalentes, ce qui rend les métaux plus faciles à fondre.
-
Force d'adhérence et température de fusion:
- La force des liaisons dans un matériau influence directement sa température de fusion. Des liaisons plus fortes nécessitent plus d'énergie thermique pour être rompues, ce qui conduit à des points de fusion plus élevés.
- Les céramiques, avec leurs fortes liaisons ioniques ou covalentes, ont des températures de fusion beaucoup plus élevées que les métaux, dont les liaisons métalliques sont relativement plus faibles.
-
Structure cristalline et énergie de réseau:
- Céramique: Les céramiques présentent souvent des structures cristallines complexes avec des énergies de réseau élevées. L'énergie de réseau est l'énergie nécessaire pour séparer une mole d'un solide ionique en ses ions gazeux. L'énergie de réseau élevée des céramiques contribue à leurs températures de fusion élevées.
- Métaux: Les métaux présentent généralement des structures cristallines plus simples, telles que les structures cubiques à faces centrées (FCC), cubiques à corps centré (BCC) ou hexagonales rapprochées (HCP). Ces structures ont des énergies de réseau plus faibles que celles des céramiques, ce qui se traduit par des points de fusion plus bas.
-
Stabilité thermique:
- Les céramiques sont connues pour leur stabilité thermique, c'est-à-dire qu'elles peuvent supporter des températures élevées sans se décomposer ni fondre. Cette stabilité est due aux liaisons solides et aux énergies de réseau élevées mentionnées plus haut.
- Les métaux, bien qu'ils soient également thermiquement stables dans une certaine mesure, ont généralement une stabilité thermique inférieure à celle des céramiques. C'est pourquoi les métaux ont tendance à fondre à des températures plus basses.
-
Exemples et comparaisons:
- Céramique: L'alumine (Al₂O₃), qui fond à environ 2072°C, et le carbure de silicium (SiC), qui fond à environ 2730°C, sont des exemples de céramiques ayant un point de fusion élevé.
- Métaux: En revanche, les métaux courants comme l'aluminium (Al) fondent à environ 660°C, et le fer (Fe) à environ 1538°C. Ces points de fusion sont nettement inférieurs à ceux des céramiques.
-
Implications pratiques:
- Les températures de fusion élevées des céramiques en font des matériaux idéaux pour les applications nécessitant une résistance à la chaleur extrême, comme les revêtements de fours, les composants aérospatiaux et les outils de coupe.
- Les métaux, dont le point de fusion est plus bas, conviennent mieux aux applications où la malléabilité et la ductilité sont importantes, comme dans la construction, les pièces automobiles et l'électronique.
En résumé, la température de fusion plus élevée des céramiques par rapport aux métaux est principalement due aux liaisons ioniques ou covalentes plus fortes et aux énergies de réseau plus élevées dans les céramiques. Ces facteurs rendent les céramiques plus résistantes à la chaleur et adaptées aux applications à haute température, tandis que les métaux, avec leurs liaisons métalliques plus faibles, fondent à des températures plus basses et conviennent mieux aux applications nécessitant flexibilité et conductivité.
Tableau récapitulatif :
Aspect | Céramique | Métaux |
---|---|---|
Type de collage | Liaisons ioniques ou covalentes (plus fortes) | Liaisons métalliques (plus faibles et délocalisées) |
Force d'adhérence | Élevée, nécessitant plus d'énergie pour la briser | Plus faible, nécessitant moins d'énergie pour se briser |
Structure cristalline | Complexe, énergie de réseau élevée | Plus simple (FCC, BCC, HCP), énergie de réseau plus faible |
Température de fusion | Élevée (par exemple, Al₂O₃ : 2072°C, SiC : 2730°C) | Plus bas (par exemple, Al : 660°C, Fe : 1538°C) |
Stabilité thermique | Excellente résistance à la chaleur extrême | Modéré, fond à des températures plus basses |
Applications | Revêtements de four, aérospatiale, outils de coupe | Construction, automobile, électronique |
Vous souhaitez en savoir plus sur les céramiques et leurs applications à haute température ? Contactez nos experts dès aujourd'hui pour des solutions sur mesure !