Le dépôt physique en phase vapeur (PVD) est en effet une technique polyvalente capable de déposer des films minces allant du nanomètre au micromètre d'épaisseur. Cette méthode consiste à vaporiser un matériau solide dans un environnement sous vide, puis à le condenser sur un substrat pour former un film mince. Le PVD est largement utilisé dans diverses industries, notamment l’optique, l’électronique et les revêtements, en raison de sa capacité à produire des films très durables, résistants à la corrosion et tolérants à la température. Le processus est hautement contrôlable, permettant des épaisseurs et une uniformité précises, ce qui le rend adapté aux applications nécessitant une précision à l’échelle nanométrique ainsi que des revêtements d’épaisseur micrométrique.
Points clés expliqués :
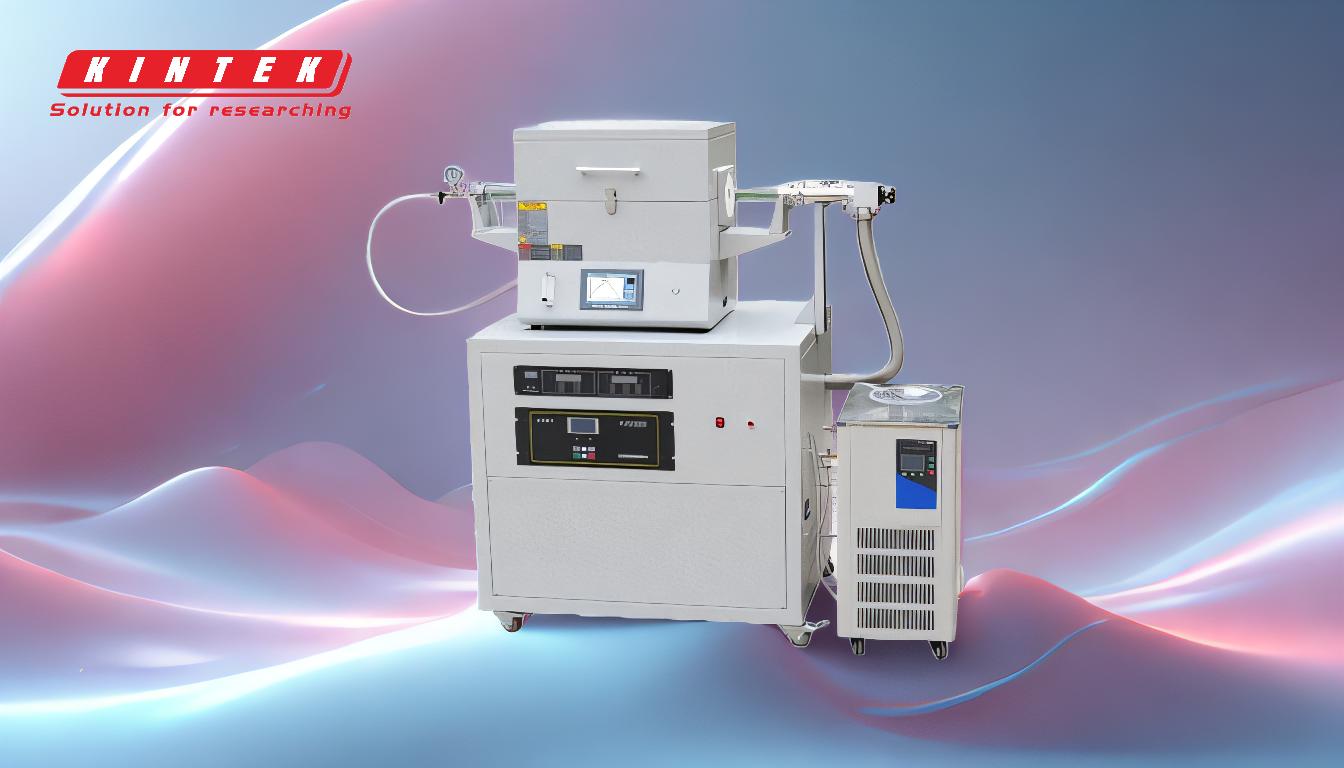
-
Présentation du processus PVD:
- Le PVD implique la vaporisation d'un matériau solide dans une chambre basse pression, suivie de son dépôt sur un substrat.
- Le processus est mené sous vide pour garantir un environnement propre et contrôlé, ce qui est crucial pour obtenir des films minces de haute qualité.
-
Plage d'épaisseur:
- Le PVD permet de déposer des films allant de quelques nanomètres à plusieurs micromètres d'épaisseur.
- L'épaisseur peut être contrôlée avec précision en ajustant des paramètres tels que le temps de dépôt, la puissance et la température du substrat.
-
Applications en optique:
- En optique, le PVD est utilisé pour créer des miroirs très sophistiqués et des verres à revêtement spécial.
- Des couches protectrices, réfléchissantes ou absorbantes peuvent être déposées sur des feuilles de verre, des lentilles ou des prismes, essentiels pour l'optique de haute technologie moderne telle que les composants laser et les instruments optiques.
-
Avantages du PVD:
- Durabilité: Les revêtements PVD sont très durables et résistants à l'usure, à la corrosion et aux températures élevées.
- Précision: Le processus permet un contrôle précis de l’épaisseur et de l’uniformité du film, ce qui le rend adapté aux applications nécessitant une précision à l’échelle nanométrique.
- Versatilité: Le PVD peut être utilisé pour déposer une large gamme de matériaux, notamment les métaux, les céramiques et les composites.
-
Comparaison avec CVD:
- Alors que le PVD est un processus physique impliquant la vaporisation et la condensation, le dépôt chimique en phase vapeur (CVD) implique des réactions chimiques entre précurseurs pour former un film mince.
- Le CVD nécessite généralement des températures plus élevées que le PVD, bien que des techniques avancées telles que dépôt chimique en phase vapeur par plasma micro-ondes peut permettre un dépôt à des températures plus basses.
-
Pertinence industrielle:
- Le PVD est largement utilisé dans les industries nécessitant des revêtements hautes performances, telles que l'aérospatiale, l'automobile et l'électronique.
- La capacité de déposer des films minces avec des épaisseurs précises et une excellente adhérence fait du PVD un choix privilégié pour de nombreuses applications de haute technologie.
En résumé, le PVD est une technique très efficace et polyvalente pour déposer des films minces d’épaisseurs allant du nanomètre au micromètre. Sa capacité à produire des revêtements durables et de haute qualité avec un contrôle précis de l’épaisseur et de l’uniformité le rend adapté à un large éventail d’applications, en particulier dans les industries nécessitant des matériaux et des revêtements avancés.
Tableau récapitulatif :
Aspect | Détails |
---|---|
Aperçu du processus | Vaporisation d'un matériau solide sous vide, se condensant sur un substrat. |
Plage d'épaisseur | Échelle nanométrique à micrométrique, avec contrôle précis de l'épaisseur. |
Applications | Optique, électronique, aérospatiale, automobile et revêtements. |
Avantages | Durable, résistant à la corrosion, tolérant à la température et très précis. |
Comparaison avec CVD | Le PVD est un processus physique ; Les MCV impliquent des réactions chimiques à des températures plus élevées. |
Intéressé par le PVD pour vos applications ? Contactez-nous aujourd'hui pour en savoir plus !