Le dépôt physique en phase vapeur (PVD) et le dépôt chimique en phase vapeur (CVD) sont deux techniques de dépôt de couches minces largement utilisées, chacune ayant des processus, des applications et des caractéristiques distincts.Le dépôt physique en phase vapeur consiste à vaporiser un matériau solide et à le condenser sur un substrat, en s'appuyant uniquement sur des processus physiques sans réactions chimiques.En revanche, le dépôt en phase vapeur (CVD) implique des réactions chimiques entre des précurseurs gazeux et le substrat pour former un film mince solide.Le dépôt en phase vapeur est respectueux de l'environnement, fonctionne à des températures plus basses et produit des revêtements durables et lisses, tandis que le dépôt en phase vapeur peut traiter une plus large gamme de matériaux, fonctionne à des températures plus élevées et produit souvent des revêtements plus épais et plus rugueux.L'équipement CVD est plus complexe et produit des sous-produits toxiques, alors que le PVD a un impact minimal sur l'environnement.
Explication des points clés :
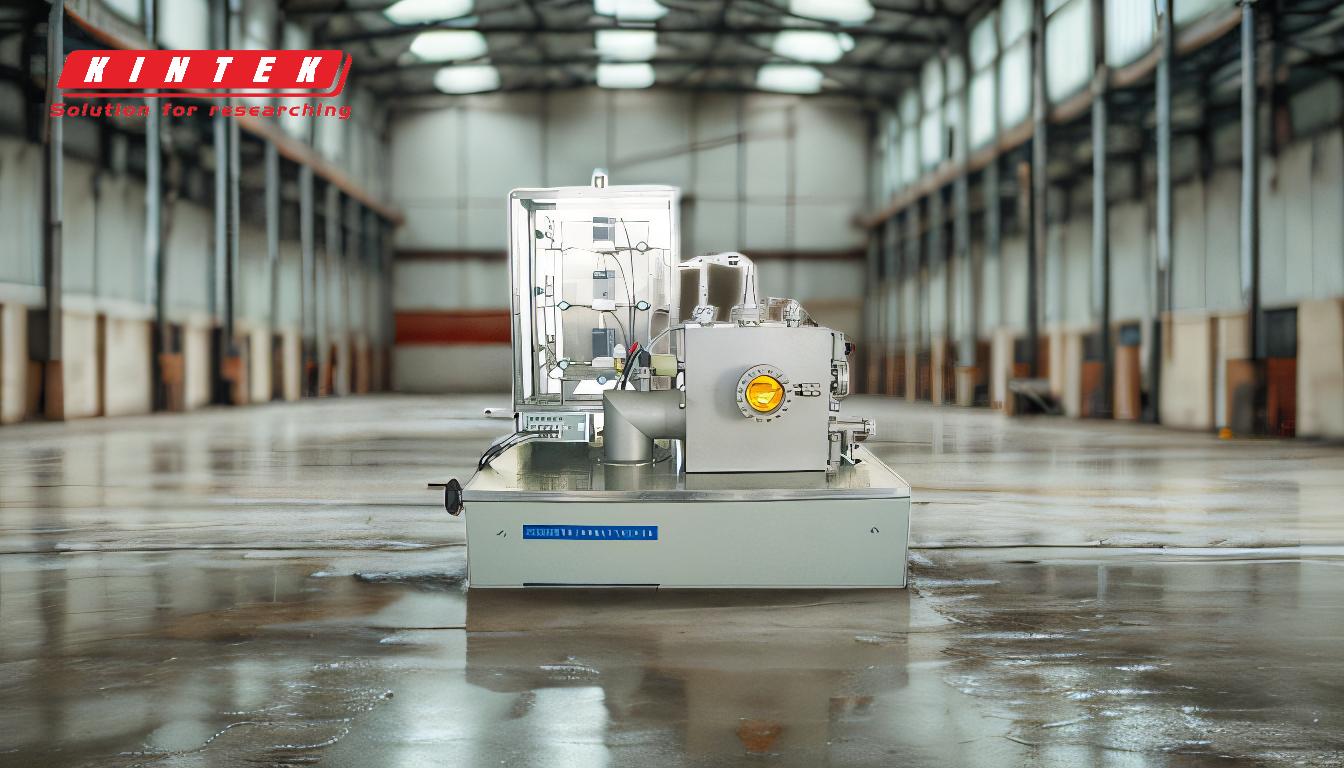
-
Mécanisme du processus:
- PVD:Ce procédé fait appel à des processus physiques tels que l'évaporation, la pulvérisation ou le placage ionique pour vaporiser un matériau solide, qui se condense ensuite sur le substrat.Aucune réaction chimique ne se produit pendant le dépôt en phase vapeur.
- CVD:Ce procédé repose sur des réactions chimiques entre des précurseurs gazeux et la surface du substrat pour former un film mince solide.Ce processus implique des phases de polymérisation et de revêtement qui se produisent simultanément.
-
État du matériau:
- PVD:Utilise un matériau de revêtement solide qui est vaporisé puis déposé sur le substrat.
- CVD:Utilise des matériaux de revêtement gazeux qui réagissent chimiquement avec le substrat pour former le film mince.
-
Température de dépôt:
- PVD:Fonctionne à des températures relativement basses, généralement entre 250°C et 450°C.
- CVD:Nécessite des températures plus élevées, allant de 450°C à 1050°C, pour faciliter les réactions chimiques nécessaires au dépôt.
-
Caractéristiques du revêtement:
- PVD:Produit des revêtements minces, lisses et durables qui peuvent résister à des températures élevées.Les revêtements sont généralement plus uniformes et présentent une excellente adhérence.
- CVD:Il permet d'obtenir des revêtements plus épais et parfois plus rugueux.Le procédé peut être appliqué à une plus large gamme de matériaux, y compris ceux qui sont difficiles à revêtir par PVD.
-
Impact sur l'environnement:
- PVD:Respectueux de l'environnement, car il n'implique pas de réactions chimiques et ne produit pas de sous-produits nocifs.Le processus est propre et a un impact minimal sur l'environnement.
- CVD:Peut produire des sous-produits toxiques en raison des réactions chimiques impliquées.L'équipement est plus spécialisé et nécessite des mesures supplémentaires pour manipuler et éliminer ces sous-produits en toute sécurité.
-
Équipement et complexité:
- PVD:L'équipement est généralement plus simple et plus direct, et se concentre sur les processus physiques de vaporisation et de dépôt.
- CVD:L'équipement est plus complexe, conçu pour traiter les précurseurs gazeux et les réactions chimiques.Le processus nécessite un contrôle précis de la température, de la pression et des débits de gaz.
-
Les applications:
- PVD:Généralement utilisé pour les applications nécessitant une grande durabilité, telles que les outils de coupe, les revêtements décoratifs et les couches résistantes à l'usure.
- CVD:Convient aux applications nécessitant des revêtements plus épais ou impliquant des géométries complexes, telles que la fabrication de semi-conducteurs, les revêtements optiques et les couches de protection sur divers substrats.
En comprenant ces différences essentielles, les acheteurs d'équipements et de consommables peuvent prendre des décisions éclairées en fonction des exigences spécifiques de leurs applications, qu'elles privilégient les considérations environnementales, la durabilité des revêtements ou la compatibilité des matériaux.
Tableau récapitulatif :
Aspect | PVD | CVD |
---|---|---|
Mécanisme du procédé | Vaporisation physique d'un matériau solide (pas de réactions chimiques) | Réactions chimiques entre les précurseurs gazeux et le substrat |
État du matériau | Matériau de revêtement solide | Matériaux de revêtement gazeux |
Température de dépôt | 250°C - 450°C | 450°C - 1050°C |
Caractéristiques du revêtement | Revêtements minces, lisses, durables et uniformes | Revêtements plus épais, parfois plus rugueux ; compatibilité plus large avec les matériaux |
Impact sur l'environnement | Minime ; pas de sous-produits toxiques | Produit des sous-produits toxiques ; nécessite une manipulation spécialisée |
Complexité de l'équipement | Équipement plus simple | Équipements plus complexes |
Applications | Outils de coupe, revêtements décoratifs, couches résistantes à l'usure | Fabrication de semi-conducteurs, revêtements optiques, couches protectrices |
Vous avez besoin d'aide pour choisir entre PVD et CVD pour votre application ? Contactez nos experts dès aujourd'hui pour un accompagnement personnalisé !