Le nombre de plaques utilisées dans un moule d'injection dépend de la conception et de la complexité du moule.En général, les moules sont conçus comme des moules à deux plaques ou à trois plaques.Les moules à deux plaques sont plus simples et se composent de deux plaques principales : l'une pour le noyau et l'autre pour la cavité.Ces moules sont généralement utilisés pour des pièces simples et nécessitent moins de temps de préparation.Les moules à trois plaques, en revanche, comportent une plaque supplémentaire, ce qui permet de concevoir des pièces plus complexes et d'automatiser l'éjection des pièces.Le choix entre les moules à deux ou trois plaques dépend de la géométrie de la pièce, des exigences de production et des considérations de coût.
Explication des points clés :
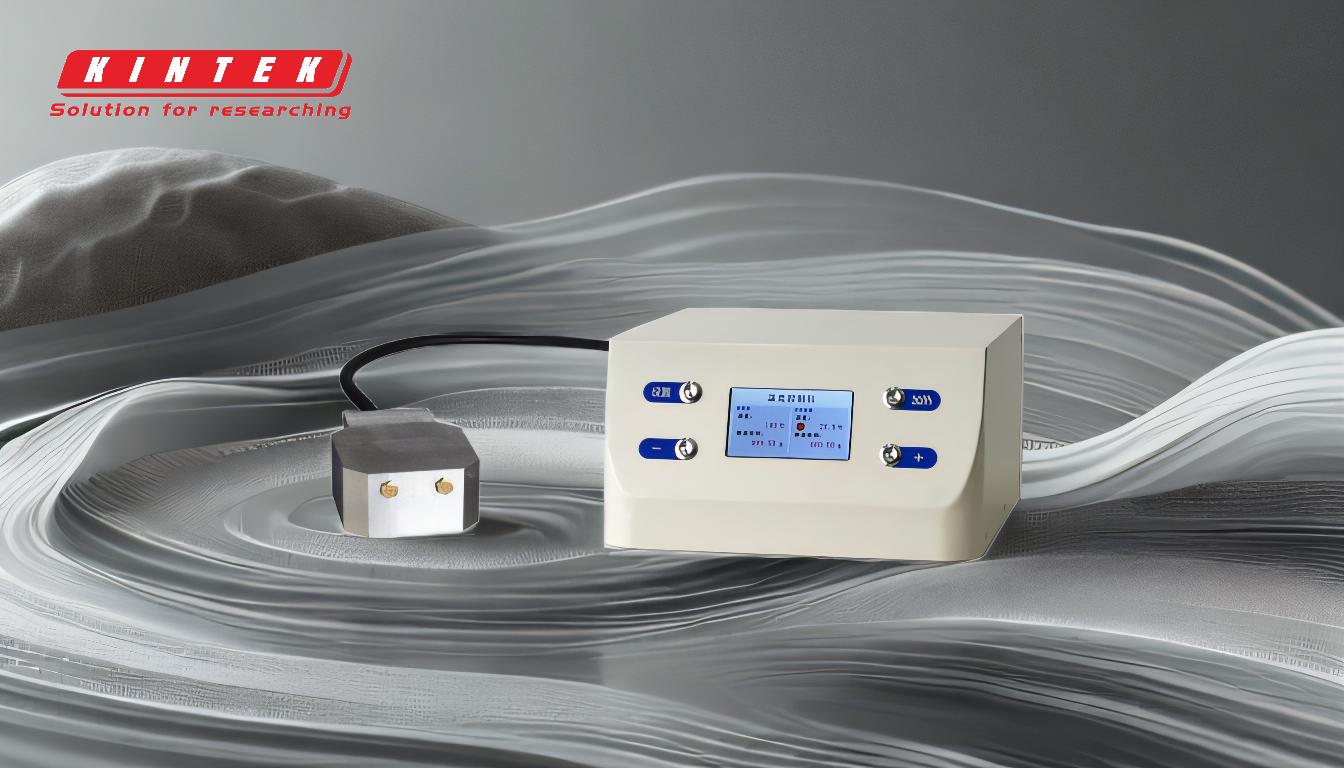
-
Moules à deux plaques:
- Structure:Se compose de deux plaques principales : l'une pour le noyau et l'autre pour la cavité.
- L'utilisation:Idéal pour les pièces plus simples avec des géométries directes.
-
Avantages:
- Plus facile à concevoir et à fabriquer.
- Réduction des coûts grâce à la diminution du nombre de composants.
- Installation plus rapide et cycles de production plus courts.
- Inconvénients:Flexibilité limitée pour les conceptions de pièces complexes ou les systèmes d'éjection automatisés.
-
Moules à trois plaques:
- Structure:Comprend une plaque supplémentaire, ce qui en fait un système à trois plaques.
- Utilisation:Convient pour les pièces plus complexes qui nécessitent plusieurs portes ou une éjection automatisée.
-
Avantages:
- Plus grande flexibilité dans la conception des pièces.
- Permet des points d'injection multiples, ce qui améliore la qualité des pièces.
- Permet l'éjection automatisée des pièces, ce qui réduit le travail manuel.
-
Inconvénients:
- Conception et processus de fabrication plus complexes.
- Coût plus élevé en raison des composants supplémentaires.
- Temps d'installation et cycles de production plus longs.
-
Facteurs influençant le choix:
- Complexité des pièces:Les pièces complexes avec des géométries compliquées ou des caractéristiques multiples peuvent nécessiter un moule à trois plaques.
- Volume de production:Les gros volumes de production peuvent bénéficier de l'efficacité des moules à deux plaques, tandis que les petits volumes ou les pièces personnalisées peuvent nécessiter la flexibilité des moules à trois plaques.
- Considérations relatives aux coûts:Les moules à deux plaques sont généralement plus rentables, mais la fonctionnalité supplémentaire des moules à trois plaques peut justifier le coût plus élevé pour certaines applications.
- Temps de cycle:Les moules à deux plaques ont généralement des temps de cycle plus courts, ce qui les rend plus adaptés à la production à grande vitesse.
-
Considérations pratiques:
- Outillage et maintenance:Les moules à trois plaques nécessitent un outillage et une maintenance plus sophistiqués, ce qui peut avoir un impact sur les coûts d'exploitation à long terme.
- Flux de matériaux:La conception des plaques du moule affecte l'écoulement du plastique fondu, ce qui influe sur la qualité et l'uniformité des pièces.
- Mécanisme d'éjection:Les moules à trois plaques comprennent souvent des systèmes d'éjection automatisés, qui peuvent améliorer l'efficacité de la production mais ajoutent à la complexité du moule.
En comprenant ces points clés, un acheteur peut décider en connaissance de cause d'opter pour un moule à deux ou trois plaques en fonction des exigences spécifiques de son projet.
Tableau récapitulatif :
Caractéristiques | Moules à deux plaques | Moules à trois plaques |
---|---|---|
Structure | Deux plaques principales (noyau et cavité) | Trois plaques (plaque supplémentaire incluse) |
Utilisation | Pièces simples avec des conceptions directes | Pièces complexes avec plusieurs portes |
Avantages | Conception plus facile, coût plus faible, mise en place plus rapide | Plus grande flexibilité, éjection automatisée |
Inconvénients | Flexibilité limitée pour les conceptions complexes | Coût plus élevé, temps de préparation plus long |
Idéal pour | Géométries simples et de grand volume | Faible volume, géométries complexes |
Vous ne savez toujours pas quel moule convient le mieux à votre projet ? Contactez nos experts dès aujourd'hui pour des conseils personnalisés !