Les revêtements PVD (Physical Vapor Deposition) sont connus pour leur finesse, allant généralement de 0,02 à 5 microns, les applications courantes se situant souvent dans la plage de 3 à 5 microns. Cette finesse constitue un avantage clé, car elle préserve le tranchant des outils de coupe, réduit les forces de coupe et la génération de chaleur, et minimise le risque de dommages thermiques au substrat. Le processus fonctionne à des températures relativement basses (environ 500 °C), ce qui évite en outre la déformation de la plupart des matériaux. Les revêtements PVD sont appliqués sous vide, garantissant un dépôt précis et uniforme, et forment une contrainte de compression pendant le refroidissement, ce qui aide à prévenir la formation et l'expansion de fissures. Ces caractéristiques rendent les revêtements PVD idéaux pour les applications hautes performances, telles que les outils de coupe, les revêtements optiques et les composants de précision.
Points clés expliqués :
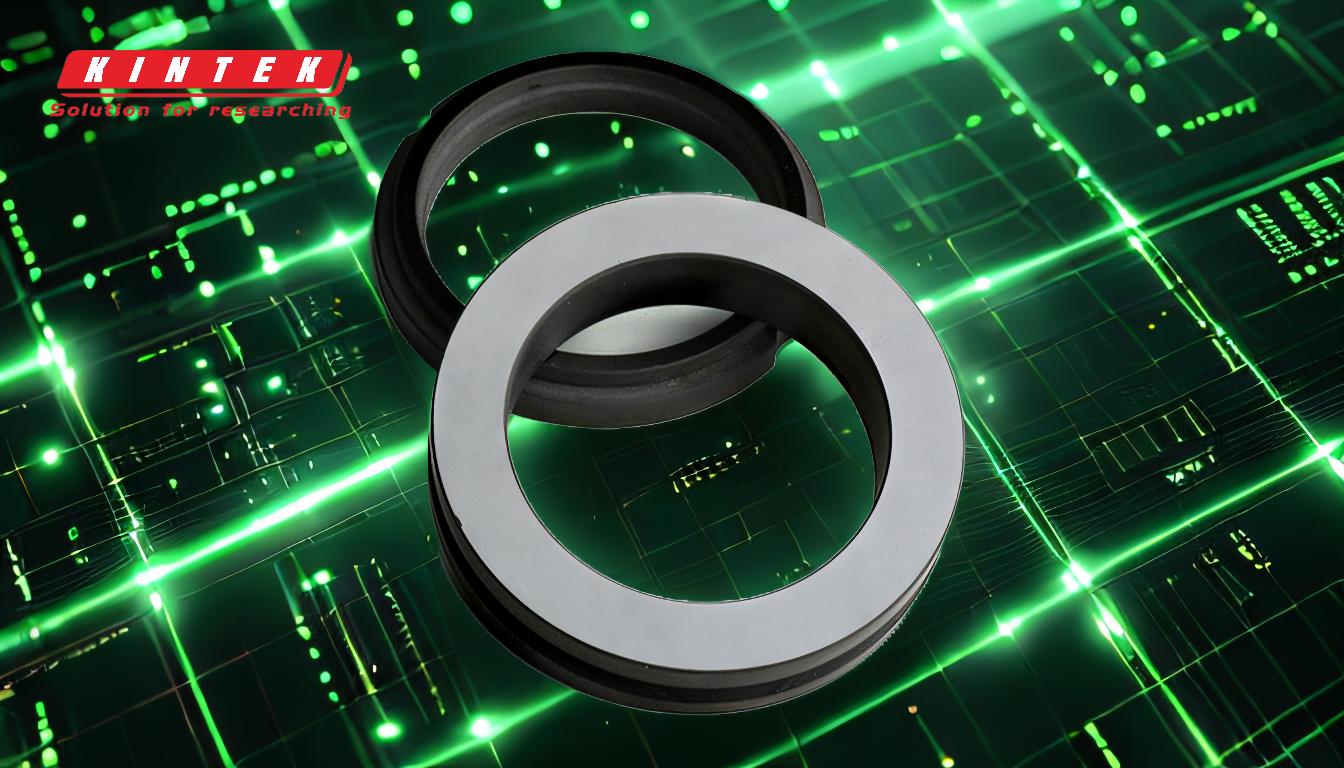
-
Gamme d'épaisseur des revêtements PVD:
- Les revêtements PVD sont extrêmement fins, allant généralement de 0,02 à 5 microns . Cette finesse constitue un avantage significatif dans les applications où le maintien de l’affûtage et de la précision des outils est essentiel.
- Pour les outils de coupe, l'épaisseur tombe souvent dans la Plage de 3 à 5 microns , ce qui est suffisant pour améliorer la dureté et la résistance à l'usure sans compromettre la netteté des bords de l'outil.
-
Avantages des revêtements PVD fins:
- Préservation de la netteté: La finesse des revêtements PVD garantit le maintien du tranchant des outils de coupe, tels que les lames, ce qui entraîne de meilleures performances et une durée de vie plus longue.
- Force de coupe et chaleur réduites: Les revêtements minces réduisent la force de coupe requise lors de l'usinage, ce qui minimise la génération de chaleur et le risque de dommages thermiques au substrat.
- Formation de contraintes de compression: Pendant la phase de refroidissement, les revêtements PVD forment une contrainte de compression, ce qui aide à prévenir la formation de fissures et leur expansion, ce qui les rend adaptés aux applications exigeantes telles que les processus de coupe interrompus (par exemple, le fraisage).
-
Dépôt à basse température:
- Les revêtements PVD sont appliqués à des températures relativement basses, généralement autour de 500 °C , ce qui est nettement inférieur à d'autres méthodes de revêtement comme le CVD (Chemical Vapor Deposition). Ce processus à basse température réduit le risque de distorsion thermique dans le substrat, ce qui le rend adapté à une large gamme de matériaux, y compris ceux sensibles à la chaleur.
-
Processus de dépôt sous vide:
- Le processus PVD est mené sous conditions de vide , ce qui garantit que le dépôt du matériau de revêtement est précis et uniforme. L'environnement sous vide empêche également la conduction et la convection, permettant le transport thermique uniquement par rayonnement, ce qui contribue à la haute qualité et à la cohérence des revêtements.
-
Applications des revêtements PVD minces:
- Outils de coupe: Les revêtements PVD sont largement utilisés sur les outils de coupe en acier rapide (HSS) et en carbure en raison de leur capacité à améliorer la dureté et la résistance à l'usure sans compromettre la géométrie de l'outil.
- Composants de précision: La nature fine et uniforme des revêtements PVD les rend idéaux pour les pièces aux tolérances serrées, telles que les composants de moulage par injection plastique et les outils de découpage fin.
- Revêtements optiques: Le dépôt précis de films minces en PVD le rend adapté aux applications optiques, où l'uniformité et la finesse sont essentielles.
-
Avantages environnementaux:
- Le revêtement PVD est un respectueux de l'environnement processus. Il ne produit aucun déchet ni gaz nocif et ne modifie pas la valeur recyclable des matériaux comme l’acier inoxydable. Cela en fait un choix durable pour les industries cherchant à réduire leur impact environnemental.
-
Étapes et caractéristiques du processus:
- Le processus PVD comprend trois étapes principales : (1) vaporisation du matériau de revêtement, (2) migration d'atomes, de molécules ou d'ions, et (3) déposition de ces particules sur le substrat. Ce processus donne lieu à des revêtements purs et de haute qualité qui améliorent la qualité de la surface en réduisant la rugosité.
-
Polyvalence dans la fabrication:
- Les machines de revêtement PVD sont contrôlé par ordinateur , permettant une haute précision et la capacité de gérer à la fois une fabrication en grand volume et à grande échelle et une production en petits lots. Cette polyvalence rend le revêtement PVD adapté à un large éventail d’industries, de l’automobile à l’aérospatiale.
En résumé, la finesse des revêtements PVD, combinée à leur dépôt à basse température, leur précision sous vide et leurs avantages environnementaux, en fait une solution très efficace pour améliorer les performances et la durabilité des outils et composants dans diverses industries.
Tableau récapitulatif :
Aspect | Détails |
---|---|
Plage d'épaisseur | 0,02 à 5 microns (commun : 3-5 microns pour les outils de coupe) |
Avantages | Préserve le tranchant, réduit la force de coupe, prévient les dommages thermiques |
Température de dépôt | ~500 °C (processus à basse température) |
Processus | À base de vide, assurant un dépôt précis et uniforme |
Applications | Outils de coupe, composants de précision, revêtements optiques |
Impact environnemental | Respectueux de l'environnement, pas de déchets ni de gaz nocifs |
Améliorez vos outils avec des revêtements PVD ultra-fins : contactez-nous aujourd'hui pour en savoir plus !