Les techniques de dépôt physique en phase vapeur (PVD) sont largement utilisées dans diverses industries pour le revêtement et le dépôt de couches minces. Ces techniques offrent plusieurs avantages, tels que des revêtements de haute qualité, le respect de l'environnement et la possibilité de déposer une large gamme de matériaux. Cependant, ils présentent également des limites, notamment des coûts d'équipement élevés, une complexité de contrôle des processus et des limitations en termes d'épaisseur de revêtement. Comprendre ces avantages et limites est crucial pour sélectionner la technique PVD appropriée pour des applications spécifiques.
Points clés expliqués :
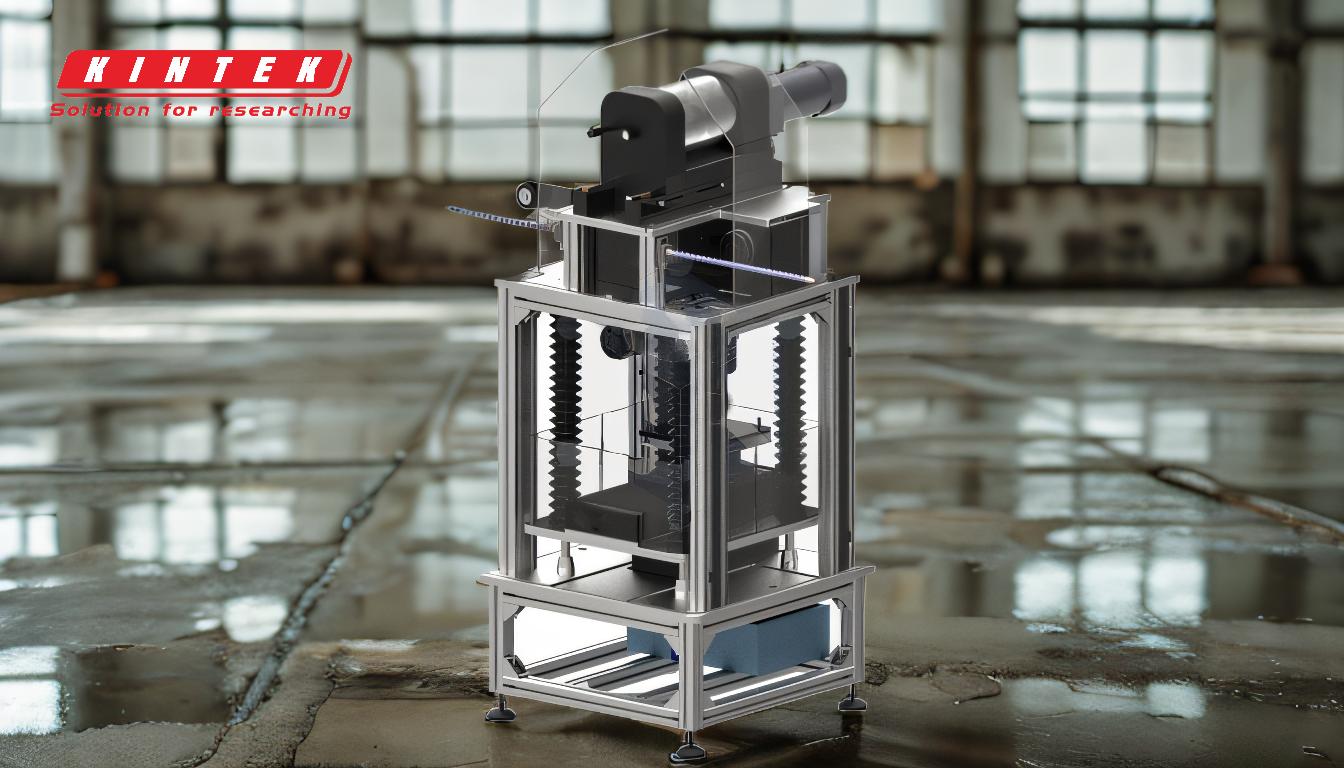
-
Avantages des techniques PVD :
- Revêtements de haute qualité : Les techniques PVD produisent des revêtements présentant une excellente adhérence, uniformité et pureté. Le processus permet un contrôle précis des propriétés du revêtement, telles que l'épaisseur, la composition et la microstructure, ce qui donne lieu à des revêtements hautes performances.
- Respect de l'environnement : Le PVD est considéré comme un processus respectueux de l’environnement car il n’implique généralement pas de produits chimiques nocifs et ne produit pas de déchets dangereux. Cela en fait un choix privilégié dans les industries où les réglementations environnementales sont strictes.
- Polyvalence dans le dépôt de matériaux : Les techniques PVD peuvent déposer une large gamme de matériaux, notamment des métaux, des alliages, des céramiques et des composites. Cette polyvalence permet la création de revêtements aux propriétés adaptées à des applications spécifiques.
- Traitement à basse température : De nombreux processus PVD peuvent être réalisés à des températures relativement basses, ce qui est bénéfique pour le revêtement de substrats sensibles à la température sans provoquer de dommages thermiques.
-
Limites des techniques PVD :
- Coûts d’équipement élevés : L'investissement initial pour l'équipement PVD peut être substantiel. Le besoin d’environnements sous vide poussé, de systèmes de contrôle sophistiqués et de matériaux cibles spécialisés contribue au coût global.
- Complexité du contrôle des processus : Les processus PVD nécessitent un contrôle précis de divers paramètres, tels que la pression, la température et la puissance. Cette complexité peut rendre difficile l’obtention de résultats cohérents, en particulier dans le cadre d’une production à grande échelle.
- Limites de l’épaisseur du revêtement : Les techniques PVD sont généralement plus adaptées aux applications en couches minces. L'obtention de revêtements épais peut être difficile et nécessiter plusieurs cycles de dépôt, ce qui augmente le temps et le coût du processus.
- Limites de la ligne de vue : De nombreuses techniques PVD sont des processus en visibilité directe, ce qui signifie que seules les surfaces directement exposées au flux de vapeur seront recouvertes. Cela peut entraîner des revêtements inégaux sur des géométries complexes ou des surfaces internes.
-
Comparaison avec la distillation sous vide à court trajet :
- Bien que les techniques PVD soient principalement utilisées pour les applications de revêtement, distillation sous vide à court trajet est une technique utilisée pour séparer et purifier les composés, notamment ceux qui sont sensibles à la chaleur. Les deux techniques fonctionnent sous vide, ce qui réduit les points d’ébullition des substances et permet un traitement à des températures plus basses. Cependant, les applications et les objectifs de ces techniques sont très différents, le PVD se concentrant sur le dépôt de matériaux et la distillation sous vide à court trajet pour la séparation des composés.
-
Applications industrielles :
- PVD dans la fabrication : Les revêtements PVD sont largement utilisés dans la fabrication d'outils de coupe, de dispositifs médicaux et de composants optiques. La capacité de produire des revêtements durs et résistants à l’usure fait du PVD un procédé précieux dans les industries où la durabilité et les performances sont essentielles.
- Distillation sous vide à court trajet dans le traitement chimique : La distillation sous vide à court trajet est couramment utilisée dans les industries pharmaceutique, alimentaire et chimique pour la purification des huiles essentielles, des cannabinoïdes et d'autres composés sensibles. La capacité de cette technique à fonctionner à basse température et à produire des produits de haute pureté la rend idéale pour ces applications.
-
Tendances futures :
- Avancées de la technologie PVD : Les recherches en cours se concentrent sur l’amélioration de l’efficacité et de l’évolutivité des techniques PVD. Les innovations dans les matériaux cibles, les systèmes de vide et le contrôle des processus devraient réduire les coûts et élargir la gamme d'applications.
- Intégration avec d'autres technologies : La combinaison du PVD avec d’autres techniques de dépôt ou de traitement de surface, telles que le dépôt chimique en phase vapeur (CVD) ou le traitement par plasma, pourrait conduire au développement de procédés hybrides aux capacités améliorées.
En conclusion, les techniques PVD offrent des avantages significatifs en termes de qualité du revêtement, d’impact environnemental et de polyvalence des matériaux. Cependant, ils présentent également des défis liés au coût, à la complexité du processus et à l’épaisseur du revêtement. Comprendre ces facteurs est essentiel pour prendre des décisions éclairées lors de la sélection et de l’application des techniques PVD dans divers contextes industriels.
Tableau récapitulatif :
Aspect | Avantages | Limites |
---|---|---|
Qualité du revêtement | Haute adhérence, uniformité et pureté | Limité aux applications en couches minces |
Impact environnemental | Pas de produits chimiques nocifs ni de déchets dangereux | Coûts d’équipement et d’exploitation élevés |
Polyvalence des matériaux | Peut déposer des métaux, des alliages, des céramiques et des composites | Le processus de visibilité directe limite le revêtement sur des géométries complexes |
Sensibilité à la température | Traitement à basse température adapté aux supports sensibles | Contrôle de processus complexe requis pour des résultats cohérents |
Besoin d'aide pour sélectionner la bonne technique PVD pour votre application ? Contactez nos experts dès aujourd'hui !