Le dépôt chimique en phase vapeur (CVD) est une technique largement utilisée pour déposer des films et des revêtements minces, mais elle présente plusieurs inconvénients. Ceux-ci incluent des températures de fonctionnement élevées qui peuvent limiter la compatibilité des substrats, le besoin de précurseurs chimiques toxiques et volatils et la génération de sous-produits dangereux. De plus, les processus CVD sont gourmands en énergie, coûteux et nécessitent un contrôle précis de plusieurs paramètres. La méthode est également limitée en termes de taille de substrat et de types de matériaux pouvant être synthétisés, en particulier pour les systèmes multi-composants. Malgré ses avantages, tels qu'une pureté et une uniformité élevées, ces inconvénients rendent le CVD moins adapté à certaines applications et plus difficile à mettre en œuvre par rapport à d'autres techniques de dépôt.
Points clés expliqués :
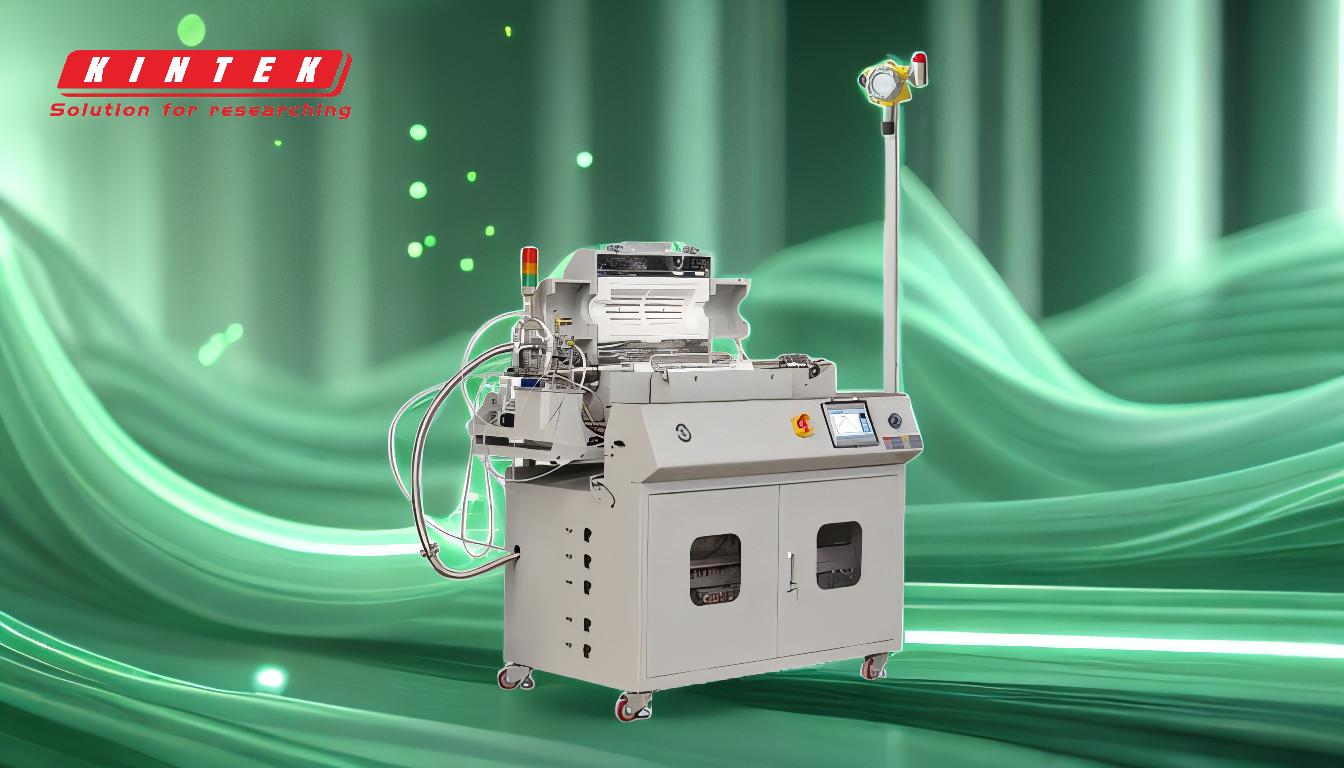
-
Températures de fonctionnement élevées:
- Le CVD nécessite généralement des températures supérieures à 600°C, ce qui peut provoquer une instabilité thermique sur de nombreux substrats. Cela limite les types de matériaux pouvant être utilisés, car certains peuvent se dégrader ou se déformer à des températures aussi élevées.
- La consommation d'énergie élevée associée à ces températures augmente également les coûts d'exploitation.
-
Précurseurs chimiques toxiques et volatils:
- Le CVD repose sur des précurseurs chimiques à haute pression de vapeur, tels que les halogénures et les composés métal-carbonyle, qui sont souvent toxiques, pyrophoriques ou dangereux. Cela pose des risques importants pour la santé et la sécurité lors de la manipulation et du traitement.
- La rareté des précurseurs non toxiques et non pyrophoriques complique encore le processus.
-
Sous-produits dangereux:
- Le procédé CVD génère des sous-produits souvent toxiques et corrosifs, comme le chlorure d'hydrogène ou d'autres composés volatils. La neutralisation de ces sous-produits nécessite des équipements et des processus supplémentaires, ce qui augmente à la fois la complexité et les coûts.
-
Coût élevé et consommation d’énergie:
- L'équipement CVD est coûteux et le processus est gourmand en énergie en raison des températures élevées et du contrôle précis requis. Cela rend le CVD moins viable économiquement pour certaines applications par rapport aux méthodes alternatives telles que le dépôt physique en phase vapeur (PVD).
-
Taille du substrat et compatibilité limitées:
- La taille des substrats pouvant être traités est limitée par les dimensions de la chambre CVD. Cela limite l'évolutivité du processus pour des applications plus volumineuses.
- De plus, les températures élevées et la réactivité chimique des précurseurs peuvent limiter les types de substrats compatibles avec le CVD.
-
Exigences de complexité et de précision:
- Le CVD nécessite un contrôle précis sur plusieurs paramètres, notamment les débits de gaz, la température du substrat et le temps de traitement. Cela rend le processus plus complexe et moins indulgent par rapport aux autres techniques de dépôt.
-
Limites de la synthèse des matériaux:
- La synthèse de matériaux multi-composants est un défi en raison des variations de pression de vapeur, de nucléation et de taux de croissance au cours de la conversion gaz-particule. Cela aboutit souvent à des compositions hétérogènes et à des propriétés de matériaux incohérentes.
-
Épaisseur et limites structurelles:
- Le CVD est principalement adapté au dépôt de films minces allant de quelques nanomètres à quelques micromètres. Il n’est pas bien adapté à la création de films plus épais ou de structures tridimensionnelles, ce qui limite son applicabilité dans certains domaines.
-
Préoccupations environnementales et de sécurité:
- L'utilisation de gaz et de produits chimiques dangereux dans les processus CVD soulève des préoccupations en matière d'environnement et de sécurité. Une manipulation, un stockage et une élimination appropriés de ces matériaux sont nécessaires, ce qui ajoute à la complexité et au coût global.
Bien que le CVD offre des avantages tels qu'une pureté et une uniformité élevées, ces inconvénients mettent en évidence les défis associés à la technique. Pour les applications nécessitant des températures plus basses, des processus plus simples ou une production à plus grande échelle, des méthodes de dépôt alternatives peuvent être plus adaptées.
Tableau récapitulatif :
Inconvénient | Description |
---|---|
Températures de fonctionnement élevées | Nécessite >600°C, ce qui limite la compatibilité du substrat et augmente les coûts énergétiques. |
Précurseurs chimiques toxiques | Utilise des précurseurs dangereux et volatils, posant des risques pour la santé et la sécurité. |
Sous-produits dangereux | Génère des sous-produits toxiques et corrosifs, nécessitant une neutralisation supplémentaire. |
Coût élevé et consommation d’énergie | Des équipements coûteux et des processus énergivores réduisent la viabilité économique. |
Taille du substrat limitée | Limité par les dimensions de la chambre, limitant l'évolutivité pour des applications plus importantes. |
Complexité et précision | Nécessite un contrôle précis sur plusieurs paramètres, ce qui augmente la complexité du processus. |
Limites de la synthèse des matériaux | Défis liés à la synthèse de matériaux multi-composants aux propriétés cohérentes. |
Épaisseur et limites structurelles | Convient uniquement aux films minces, pas aux structures plus épaisses ou 3D. |
Préoccupations environnementales et de sécurité | La manipulation et l'élimination des matières dangereuses ajoutent de la complexité et des coûts. |
Vous recherchez une meilleure solution de dépôt ? Contactez-nous aujourd'hui pour explorer des alternatives adaptées à vos besoins !