Les moules à deux plaques sont largement utilisés dans le moulage par injection en raison de leur simplicité et de leur rentabilité.Cependant, ils présentent certains inconvénients, en particulier dans les conceptions à cavités multiples.L'une des principales difficultés consiste à équilibrer le flux de plastique fondu dans les multiples cavités, ce qui peut entraîner un remplissage inégal et des défauts dans le produit final.En outre, l'alignement du plan de joint avec la porte dans un moule à deux plaques peut compliquer le processus de conception et de fabrication.Ces limitations peuvent avoir un impact sur l'efficacité, la qualité et le coût de la production, et il est donc essentiel d'évaluer soigneusement leur adéquation à des applications spécifiques.
Explication des points clés :
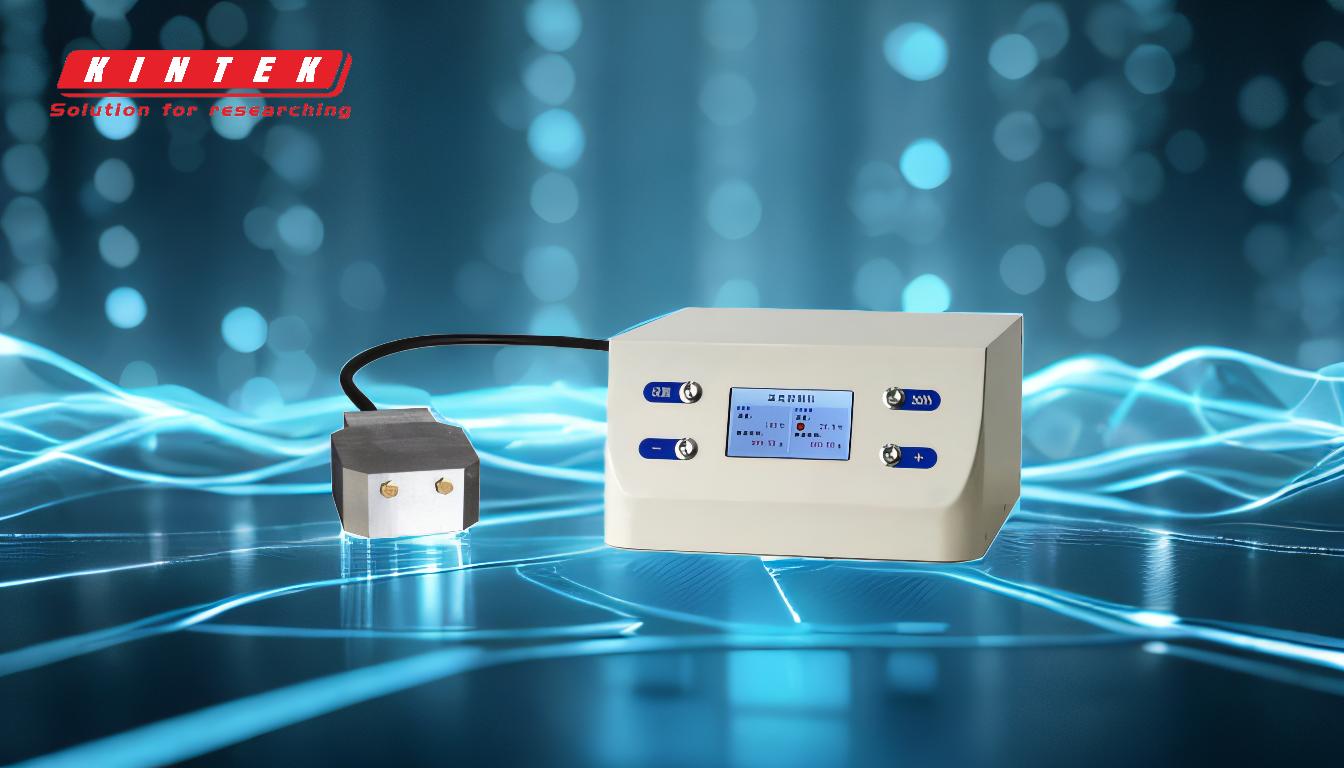
-
Défis liés à l'équilibrage des flux de plastique fondu:
- Dans les moules multi-empreintes à deux plaques, il est difficile d'assurer une distribution uniforme du plastique fondu dans chaque empreinte.
- Un écoulement irrégulier peut entraîner des défauts tels que des coups courts, des déformations ou des dimensions de pièces incohérentes.
- Ce problème est exacerbé dans les conceptions complexes où les cavités sont situées à des distances variables de l'opercule.
-
Alignement du plan de joint avec la porte:
- Le plan de joint d'un moule à deux plaques doit être aligné avec la porte, ce qui limite la flexibilité de la conception.
- Cet alignement peut compliquer la conception du moule, en particulier pour les pièces complexes ou les configurations à plusieurs empreintes.
- Il peut également augmenter le risque de formation de bavures ou d'autres défauts au niveau du plan de joint.
-
Flexibilité de conception limitée:
- Les moules à deux plaques sont moins polyvalents que les moules à trois plaques ou les systèmes à canaux chauds.
- Ils ne sont pas idéaux pour les pièces qui nécessitent un cadrage complexe ou qui ont des exigences esthétiques spécifiques.
- La simplicité des moules à deux plaques s'accompagne souvent d'une réduction des possibilités de personnalisation.
-
Risque accru de défauts:
- En raison des difficultés liées à l'équilibrage des flux et à l'alignement des portes, les moules à deux plaques sont plus susceptibles de présenter des défauts.
- Les problèmes les plus courants sont les lignes de soudure, les pièges à air et la qualité irrégulière des pièces.
- Ces défauts peuvent augmenter les taux de rebut et les coûts de production.
-
Temps de cycle plus longs:
- Les limites des moules à deux plaques peuvent entraîner des temps de refroidissement et de cycle plus longs.
- Cela est particulièrement vrai pour les moules multi-empreintes où un refroidissement inégal peut se produire.
- Des temps de cycle plus longs réduisent l'efficacité globale de la production et augmentent les coûts d'exploitation.
-
Exigences de maintenance plus élevées:
- La complexité de l'équilibrage du débit et de l'alignement des vannes peut entraîner une usure accrue du moule.
- Une maintenance régulière est nécessaire pour garantir des performances constantes, ce qui augmente le coût total de possession.
-
Ne convient pas à toutes les applications:
- Les moules à deux plaques conviennent le mieux pour les pièces simples dont les exigences en matière d'injection sont simples.
- Pour les pièces complexes ou les applications de haute précision, d'autres conceptions de moules (par exemple, les moules à trois plaques ou les systèmes à canaux chauds) peuvent être plus appropriées.
En comprenant ces inconvénients, les fabricants peuvent décider en connaissance de cause si un moule à deux plaques est le bon choix pour leurs besoins de production spécifiques.Bien qu'ils soient simples et économiques, leurs limites doivent être soigneusement évaluées en fonction des exigences du projet.
Tableau récapitulatif :
Désavantage | Impact |
---|---|
Défis liés à l'équilibrage des flux | Remplissage inégal, défauts tels que coups courts, gauchissement ou dimensions incohérentes. |
Alignement du plan de joint | Flexibilité de conception limitée, risque accru de formation de bavures. |
Flexibilité de conception limitée | Moins de souplesse pour les pièces complexes ou les exigences esthétiques spécifiques. |
Risque accru de défauts | Les lignes de soudure, les pièges à air et la qualité irrégulière des pièces augmentent les taux de rebut. |
Temps de cycle plus longs | Un refroidissement inégal réduit l'efficacité de la production. |
Besoins d'entretien plus importants | Usure et détérioration accrues, nécessitant un entretien régulier. |
Ne convient pas à toutes les applications | Il convient mieux aux pièces simples ; les conceptions complexes peuvent nécessiter d'autres moules. |
Vous avez besoin d'aide pour choisir le bon moule pour votre projet ? Contactez nos experts dès aujourd'hui pour des solutions sur mesure !