La technique des pastilles pressées pour la fluorescence X (XRF) est une méthode de préparation des échantillons utilisée pour créer des disques uniformes et plats à partir d'échantillons en poudre.Cette technique est essentielle pour une analyse élémentaire précise, car elle garantit une présentation uniforme de l'échantillon à l'instrument XRF.Le processus consiste à broyer l'échantillon en une fine poudre, à le mélanger à un liant et à le comprimer sous haute pression pour former une pastille solide.Cette méthode est largement utilisée dans des secteurs tels que l'exploitation minière, la géologie et la métallurgie, car elle permet d'obtenir des résultats fiables et reproductibles pour les analyses chimiques.Nous présentons ci-dessous les principaux aspects de cette technique et son importance.
Les points clés expliqués :
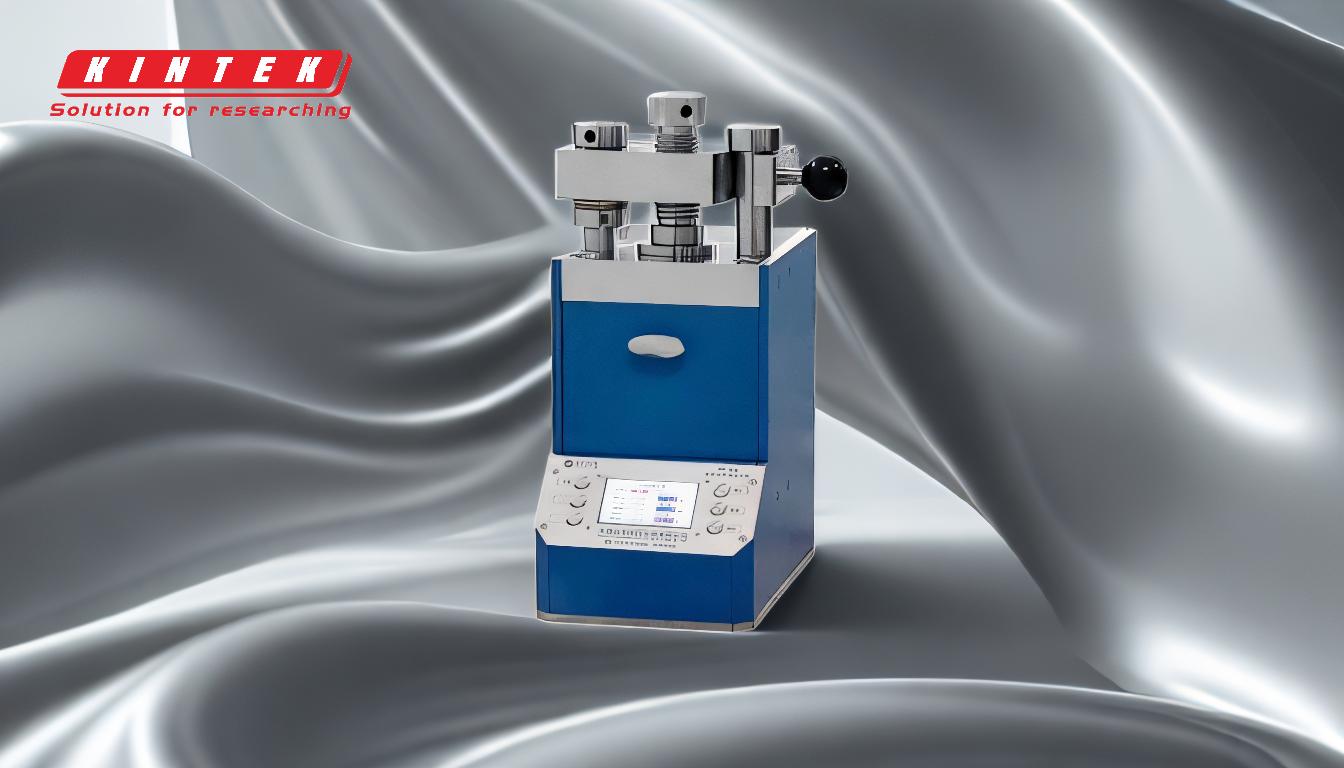
-
Objectif de la technique des pastilles pressées
- L'objectif principal de la technique des pastilles pressées est de préparer les échantillons pour l'analyse XRF sous une forme qui assure une densité uniforme et une consistance de surface.
- Cette uniformité est essentielle pour une identification et une quantification précises des éléments, car l'analyse par fluorescence X repose sur l'interaction des rayons X avec la surface de l'échantillon.
- Si l'échantillon n'est pas correctement préparé, les résultats peuvent être incohérents ou inexacts, ce qui peut entraîner des erreurs d'analyse.
-
Étapes de la technique des pastilles pressées
- Préparation de l'échantillon:L'échantillon est d'abord broyé en une fine poudre afin d'en garantir l'homogénéité.Cette étape est cruciale car les particules les plus grosses peuvent donner des résultats irréguliers.
- Mélange avec un liant:Un agent liant est souvent ajouté à l'échantillon en poudre pour l'aider à se maintenir pendant la compression.Les liants les plus courants sont les cires, la cellulose ou d'autres composés organiques.
- Compression:Le mélange est placé dans une matrice et soumis à une pression élevée (généralement de 10 à 40 tonnes) à l'aide d'une presse hydraulique.La poudre est ainsi comprimée en un disque solide et plat.
- Pellet final:La pastille obtenue est un disque uniforme et durable qui peut être directement analysé par XRF.
-
Avantages de la technique des pastilles pressées
- Consistance:La technique permet d'obtenir des pastilles dont la densité et les propriétés de surface sont uniformes, ce qui est essentiel pour une analyse XRF fiable.
- La polyvalence:Il peut être utilisé pour un large éventail de types d'échantillons, y compris les minerais, les métaux, les céramiques et les matériaux géologiques.
- Rapport coût-efficacité:Par rapport à d'autres méthodes de préparation des échantillons, telles que la fusion, les pastilles pressées sont relativement peu coûteuses et nécessitent moins d'équipement spécialisé.
- Perte minimale d'échantillon:Le processus conserve la composition originale de l'échantillon, garantissant une représentation précise de sa teneur en éléments.
-
Applications dans des secteurs clés
- Exploitation minière et géologie:Utilisé pour analyser des échantillons de minerais afin d'y déceler des éléments précieux et des impuretés.
- Métallurgie:Aide au contrôle de la qualité en identifiant la composition des métaux et des alliages.
- Science de l'environnement:Utilisé pour tester les échantillons de sol et de sédiments afin d'y déceler des contaminants.
- Produits pharmaceutiques et alimentaires:Garantit la conformité aux normes de sécurité en analysant les éléments traces.
-
Défis et considérations
- Taille des particules:Si l'échantillon n'est pas broyé assez finement, il peut en résulter une compression inégale et des résultats incohérents.
- Sélection du liant:Le choix du liant peut affecter la durabilité du granulé et la précision de l'analyse.
- Contrôle de la pression:L'application d'une pression trop forte ou trop faible peut entraîner des granulés trop fragiles ou pas assez denses.
- Contamination:Il faut veiller à ne pas introduire de matières étrangères pendant le processus de broyage ou de pressage.
-
Comparaison avec d'autres méthodes de préparation des échantillons
- Boulettes pressées vs. fusion:La fusion consiste à faire fondre l'échantillon avec un fondant pour créer un disque de verre.Bien que la fusion offre une excellente homogénéité, elle est plus complexe et plus coûteuse que les granulés pressés.
- Granulés pressés et poudre libre:L'analyse des poudres libres est plus simple mais moins précise en raison des variations de la taille et de la distribution des particules.
- Boulettes pressées et échantillons solides:Les échantillons solides peuvent ne pas nécessiter de préparation, mais ils manquent souvent de l'uniformité nécessaire pour une analyse XRF précise.
-
Équipement nécessaire
- Presse hydraulique:Utilisé pour appliquer la pression nécessaire à la formation des granulés.
- Broyeur:Assure que l'échantillon est finement broyé avant d'être pressé.
- Jeu de matrices:Maintient l'échantillon pendant la compression et lui donne la forme d'une pastille.
- Liant:Facultatif, en fonction du type d'échantillon et des exigences de l'analyse.
En résumé, la technique des pastilles pressées est une méthode fondamentale de préparation des échantillons pour l'analyse XRF.Sa capacité à produire des pastilles uniformes et durables la rend indispensable pour les industries nécessitant une analyse élémentaire précise.Bien que le processus exige une attention particulière aux détails, ses avantages en termes de cohérence, de polyvalence et de rentabilité en font un choix privilégié pour de nombreuses applications.
Tableau récapitulatif :
Aspect | Détails |
---|---|
Objectif | Assurer une densité uniforme et une consistance de surface pour une analyse XRF précise. |
Etapes | 1.Réduire l'échantillon en poudre fine.2.Mélanger avec le liant.3.Compression en granulés. |
Avantages | Cohérence, polyvalence, rentabilité, perte minimale d'échantillons. |
Applications | Exploitation minière, géologie, métallurgie, sciences de l'environnement, produits pharmaceutiques. |
Défis | Taille des particules, sélection du liant, contrôle de la pression, contamination. |
Comparaison | Plus rentable que la fusion ; plus précis que l'analyse des poudres en vrac. |
Équipement | Presse hydraulique, broyeur, filière, liant. |
Découvrez comment la technique des pastilles pressées peut optimiser votre analyse XRF. contactez nos experts dès aujourd'hui !