La distance entre la cible et le substrat dans la pulvérisation est un paramètre critique qui influence directement la qualité, l'uniformité et l'épaisseur du film mince déposé.Cette distance doit être soigneusement contrôlée pour garantir des conditions de dépôt optimales, car elle affecte l'énergie cinétique des particules pulvérisées, leur direction et la vitesse de dépôt globale.La distance idéale entre la cible et le substrat varie en fonction de facteurs tels que la méthode de pulvérisation, le matériau de la cible, le matériau du substrat, la pression de la chambre et la puissance de pulvérisation.En général, une distance de 5 à 15 cm est couramment utilisée, mais des applications spécifiques peuvent nécessiter des ajustements pour obtenir les propriétés de film souhaitées.Un espacement correct garantit une couverture uniforme, minimise les défauts et améliore la qualité générale du revêtement.
Explication des points clés :
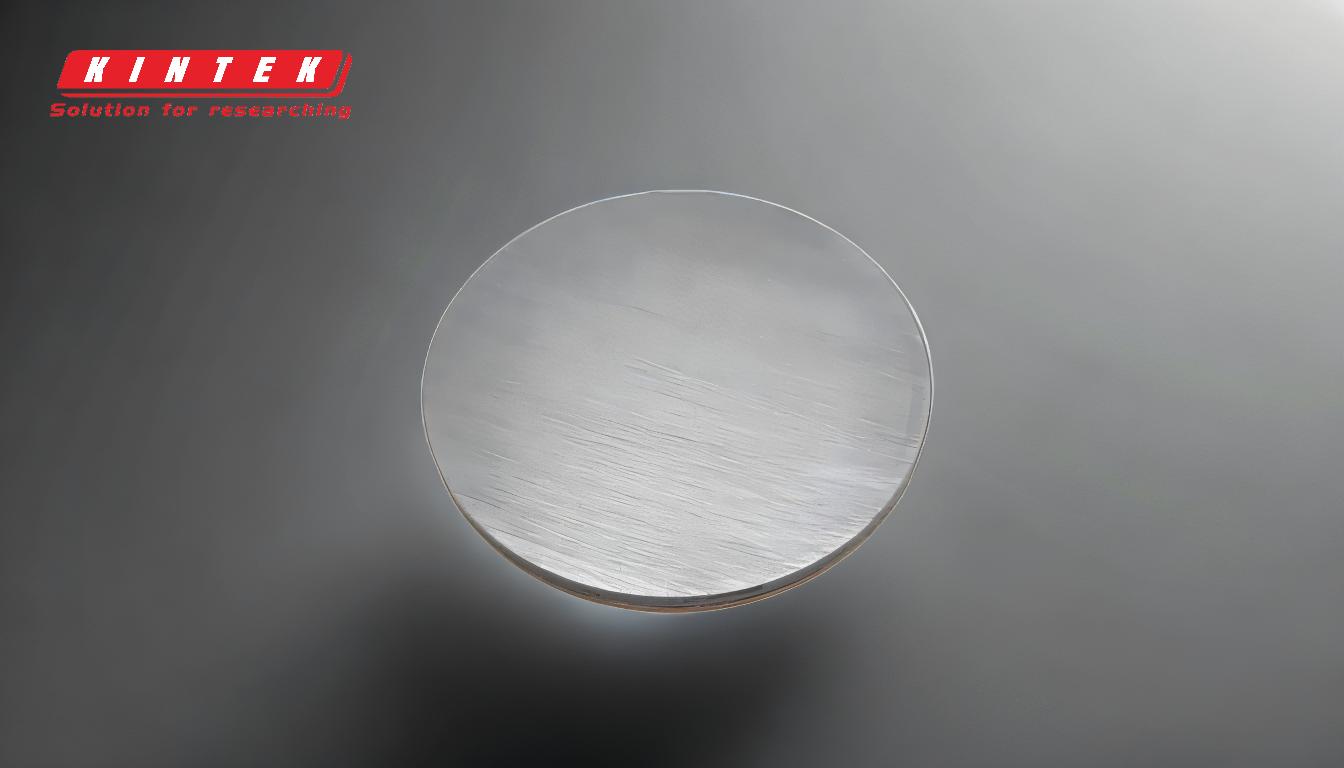
-
Importance de la distance du substrat cible:
- La distance entre la cible et le substrat est cruciale pour obtenir un dépôt uniforme de couches minces.
- Elle influe sur l'énergie cinétique et la direction des particules pulvérisées, qui à leur tour influencent l'épaisseur, l'uniformité et la qualité du film.
- Un espacement correct garantit des taux de dépôt constants et minimise les défauts tels qu'un revêtement inégal ou des vides.
-
Plage typique pour la distance du substrat cible:
- La distance entre la cible et le substrat est généralement comprise entre 5 à 15 cm .
- Cette plage convient à la plupart des applications de pulvérisation standard, offrant un équilibre entre la vitesse de dépôt et la qualité du film.
- Cependant, la distance exacte peut devoir être ajustée en fonction d'exigences expérimentales ou industrielles spécifiques.
-
Facteurs influençant la distance optimale:
- Méthode de pulvérisation:Les différentes techniques de pulvérisation (par exemple, DC, RF, magnétron) peuvent nécessiter des distances variables en raison des différences d'énergie ionique et de mécanismes de dépôt.
- Matériaux de la cible et du substrat:La masse et les propriétés des matériaux de la cible et du substrat influencent le rendement de la pulvérisation et le comportement des particules.
- Pression de la chambre:Des pressions plus élevées peuvent réduire le libre parcours moyen des particules, ce qui nécessite des distances plus courtes pour maintenir l'efficacité du dépôt.
- Puissance de pulvérisation:Des niveaux de puissance plus élevés peuvent augmenter l'énergie des particules pulvérisées, ce qui peut permettre d'augmenter la distance entre la cible et le substrat sans compromettre la qualité du film.
-
Impact sur la vitesse de dépôt et la qualité du film:
- Taux de dépôt:Une distance plus courte augmente généralement la vitesse de dépôt en raison de la réduction de la diffusion des particules et de l'augmentation du flux de particules sur le substrat.
- Qualité du film:Une distance plus longue peut améliorer l'uniformité du film en permettant aux particules de se répartir plus régulièrement sur le substrat, mais elle peut également réduire l'efficacité du dépôt.
-
Considérations pratiques pour l'installation de l'équipement:
- Uniformité:Il est essentiel de veiller à ce que le substrat soit positionné parallèlement à la surface cible pour obtenir une épaisseur de film uniforme.
- Ajustement:Les systèmes de pulvérisation doivent permettre un réglage précis de la distance entre la cible et le substrat afin de s'adapter aux différents matériaux et conditions de traitement.
- Le contrôle:Le contrôle en temps réel de l'épaisseur et de la qualité du film permet d'optimiser la distance pendant le processus de pulvérisation.
-
Réglages spécifiques à l'application:
- Revêtements de haute précision:Pour les applications nécessitant des revêtements extrêmement uniformes ou sans défaut, il peut être nécessaire de minimiser et de contrôler soigneusement la distance entre le substrat et la cible.
- Dépôt à grande échelle:En milieu industriel, des distances plus importantes peuvent être utilisées pour revêtir des substrats plus grands ou plusieurs substrats simultanément, bien que cela puisse nécessiter des ajustements à d'autres paramètres (par exemple, la puissance, la pression) pour maintenir la qualité.
-
Optimisation expérimentale:
- La distance optimale entre le substrat et la cible est souvent déterminée expérimentalement pour des applications spécifiques.
- Des facteurs tels que l'épaisseur de film souhaitée, la taille du substrat et les propriétés du matériau doivent guider le processus d'optimisation.
En résumé, la distance entre la cible et le substrat lors de la pulvérisation est un paramètre clé qui doit être soigneusement contrôlé pour obtenir un dépôt de couches minces de haute qualité.Bien qu'une fourchette générale de 5 à 15 cm soit couramment utilisée, la distance exacte doit être adaptée à la méthode de pulvérisation spécifique, aux matériaux et aux exigences de l'application.Un espacement correct garantit un dépôt uniforme, minimise les défauts et améliore les performances globales du substrat revêtu.
Tableau récapitulatif :
Facteur clé | Impact sur la distance du substrat cible |
---|---|
Gamme typique | 5 à 15 cm |
Méthode de pulvérisation | La pulvérisation DC, RF ou magnétron peut nécessiter des ajustements de distance pour obtenir une énergie ionique et un rendement optimaux. |
Matériaux de la cible/du substrat | La masse et les propriétés des matériaux affectent le rendement de la pulvérisation et le comportement des particules. |
Pression de la chambre | Une pression plus élevée peut nécessiter des distances plus courtes pour maintenir l'efficacité du dépôt. |
Puissance de pulvérisation | Une puissance plus élevée permet d'atteindre de plus grandes distances sans compromettre la qualité du film. |
Taux de dépôt | Les distances plus courtes augmentent le taux de dépôt ; les distances plus longues améliorent l'uniformité. |
Besoins spécifiques à l'application | Les revêtements de haute précision ou les dépôts à grande échelle peuvent nécessiter des distances adaptées. |
Vous avez besoin d'aide pour optimiser votre processus de pulvérisation ? Contactez nos experts dès aujourd'hui pour des solutions sur mesure !