Les revêtements de type diamant (DLC) sont appliqués à l'aide de techniques de dépôt avancées, principalement le dépôt physique en phase vapeur (PVD) et le dépôt chimique en phase vapeur (CVD).Ces méthodes consistent à créer une couche mince et durable de carbone semblable au diamant (DLC) sur la surface des outils ou des composants.Le dépôt en phase vapeur (PVD) consiste à évaporer un matériau source et à le laisser se condenser sur l'outil, formant ainsi une monocouche de DLC d'une épaisseur typique de 0,5 à 2,5 microns.Le dépôt en phase vapeur (CVD), quant à lui, utilise des gaz d'hydrogène et de méthane dans une chambre, où des fils de tungstène chauffés à plus de 2 300 °C décomposent les gaz, permettant aux atomes de carbone de se recombiner et de former un film de diamant pur sur la surface de l'outil.Les deux méthodes nécessitent un contrôle précis de la température, de la pression et de la composition des gaz pour obtenir des résultats optimaux.
Explication des points clés :
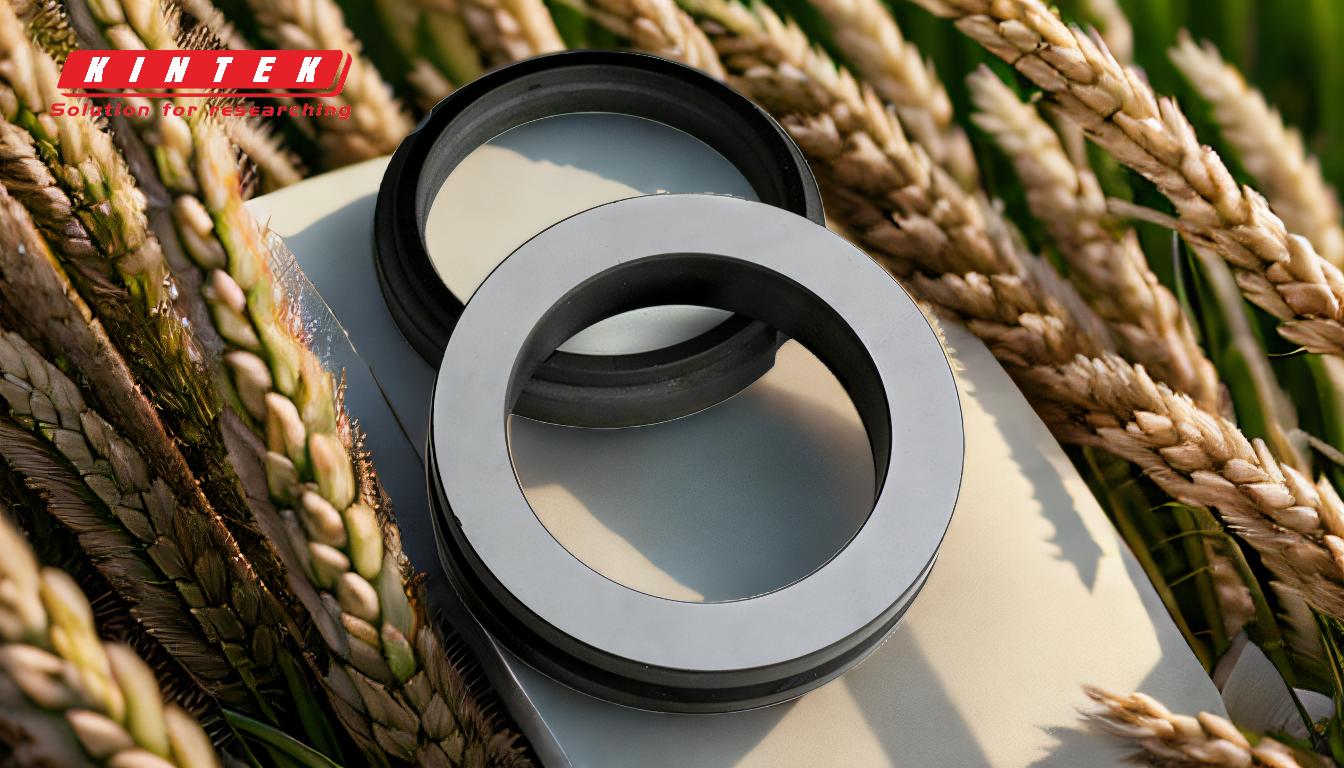
-
Vue d'ensemble des revêtements de type diamant (DLC) :
- Les revêtements DLC sont des couches minces, dures et résistantes à l'usure, appliquées sur des outils ou des composants afin d'améliorer leurs performances et leur longévité.
- Ces revêtements sont amorphes, c'est-à-dire qu'ils n'ont pas de structure cristalline, mais ils présentent des propriétés similaires à celles du diamant, telles qu'une grande dureté et une faible friction.
-
Méthodes de revêtement primaires :
-
Dépôt physique en phase vapeur (PVD) :
- Le dépôt physique en phase vapeur est une méthode largement utilisée pour appliquer des revêtements DLC.
- Le processus consiste à évaporer un matériau source (souvent à base de carbone) dans une chambre à vide.
- Le matériau évaporé se condense ensuite sur la surface de l'outil, formant une fine couche uniforme de DLC.
- L'épaisseur du revêtement est généralement comprise entre 0,5 et 2,5 microns.
- Le dépôt en phase vapeur est connu pour sa capacité à produire des revêtements de haute qualité, adhérents et présentant une excellente résistance à l'usure.
-
Dépôt chimique en phase vapeur (CVD) :
- Le dépôt chimique en phase vapeur est une autre méthode courante d'application de revêtements DLC.
- Dans ce procédé, l'outil est placé dans une chambre remplie de gaz d'hydrogène et de méthane.
- Des fils de tungstène chauffés à plus de 2 300 °C fournissent l'énergie nécessaire pour briser les molécules de gaz.
- Les atomes de carbone activés se recombinent ensuite à la surface de l'outil, formant un film de diamant pur.
- Le dépôt en phase vapeur est particulièrement efficace pour créer des revêtements plus épais et plus durables.
-
Dépôt physique en phase vapeur (PVD) :
-
Étapes du processus d'application des revêtements DLC :
-
Préparation :
- L'outil ou le composant à revêtir doit être soigneusement nettoyé et préparé pour garantir une bonne adhérence du revêtement.
- Cela implique souvent l'élimination de tous les contaminants de surface, tels que les huiles ou les oxydes, par des moyens chimiques ou mécaniques.
-
Chargement dans la chambre :
- Les outils préparés sont chargés dans la chambre de dépôt.
- Dans le cas du dépôt en phase vapeur (PVD), la chambre est mise sous vide, tandis que dans le cas du dépôt en phase vapeur (CVD), la chambre est remplie des gaz appropriés.
-
Dépôt :
- Dans le cas du dépôt en phase vapeur (PVD), le matériau source est évaporé et la vapeur se condense sur la surface de l'outil.
- Dans le cas de la CVD, les gaz sont activés et les atomes de carbone se déposent sur l'outil.
-
Refroidissement et finition :
- Après le dépôt, les outils revêtus sont refroidis lentement pour éviter les contraintes thermiques.
- Le revêtement final est contrôlé en termes de qualité, d'épaisseur et d'adhérence.
-
Préparation :
-
Paramètres clés et considérations :
-
Température :
- Les procédés PVD et CVD requièrent des températures élevées, allant généralement de 750°C à plus de 2 300°C, selon la méthode.
- Un contrôle adéquat de la température est essentiel pour garantir la qualité et l'adhérence du revêtement.
-
Composition du gaz :
- Dans le procédé CVD, la composition des gaz d'hydrogène et de méthane doit être soigneusement contrôlée pour obtenir le dépôt de carbone souhaité.
-
Épaisseur du revêtement :
- L'épaisseur du revêtement DLC est un facteur essentiel pour déterminer ses performances.
- Les revêtements plus épais peuvent offrir une meilleure résistance à l'usure, mais ils peuvent aussi être plus susceptibles de se fissurer ou de se décoller.
-
Adhésion :
- Garantir une forte adhérence entre le revêtement et le substrat est essentiel pour la durabilité du revêtement.
- Cela implique souvent un prétraitement du substrat ou l'utilisation de couches intermédiaires.
-
Température :
-
Applications des revêtements DLC :
- Les revêtements DLC sont utilisés dans un large éventail d'industries, notamment l'automobile, l'aérospatiale, les appareils médicaux et les outils de coupe.
- Ils sont particulièrement appréciés pour leur capacité à réduire le frottement, à résister à l'usure et à prolonger la durée de vie des composants soumis à des conditions difficiles.
-
Avantages et limites :
-
Avantages :
- Dureté élevée et résistance à l'usure.
- Faible coefficient de frottement, réduisant la consommation d'énergie et améliorant l'efficacité.
- Excellente résistance à la corrosion.
- Capacité à revêtir des géométries complexes.
-
Limites :
- Coût élevé de l'équipement et du processus.
- Épaisseur limitée en raison du risque de contrainte interne et de fissuration.
- Nécessite un contrôle précis des paramètres du processus.
-
Avantages :
-
Tendances futures :
- Les recherches en cours se concentrent sur l'amélioration de l'adhérence, de l'épaisseur et de l'uniformité des revêtements DLC.
- Les progrès des nanotechnologies et des méthodes de revêtement hybrides devraient permettre d'améliorer encore les performances et l'applicabilité des revêtements DLC dans diverses industries.
En comprenant ces points clés, les acheteurs d'équipements et de consommables peuvent prendre des décisions éclairées sur l'application de revêtements de type diamant, en s'assurant qu'ils choisissent la méthode et les paramètres les plus appropriés pour leurs besoins spécifiques.
Tableau récapitulatif :
Aspect | Détails |
---|---|
Méthodes primaires | PVD (dépôt physique en phase vapeur), CVD (dépôt chimique en phase vapeur) |
Épaisseur du revêtement | 0,5 à 2,5 microns (PVD), plus épais pour le CVD |
Paramètres clés | Température (750°C à 2 300°C), composition du gaz, adhérence, épaisseur du revêtement |
Applications | Automobile, aérospatiale, dispositifs médicaux, outils de coupe |
Avantages | Dureté élevée, faible frottement, résistance à la corrosion, géométries complexes |
Limites | Coût élevé, épaisseur limitée, nécessité d'un contrôle précis des paramètres |
Optimisez vos outils avec les revêtements DLC avancés. contactez nos experts dès aujourd'hui pour des solutions sur mesure !