Les systèmes de gaz inerte sont largement utilisés dans les industries pour prévenir la combustion en réduisant la concentration d'oxygène dans un espace confiné. S'ils offrent des avantages considérables en termes de sécurité, ils présentent également plusieurs inconvénients. Il s'agit notamment des coûts initiaux et opérationnels élevés, de la complexité de la maintenance, des risques potentiels liés à une mauvaise utilisation et des limitations dans certains environnements. Il est essentiel de comprendre ces inconvénients pour que les acheteurs d'équipements et de consommables puissent prendre des décisions éclairées et garantir des opérations sûres et efficaces.
Explication des points clés :
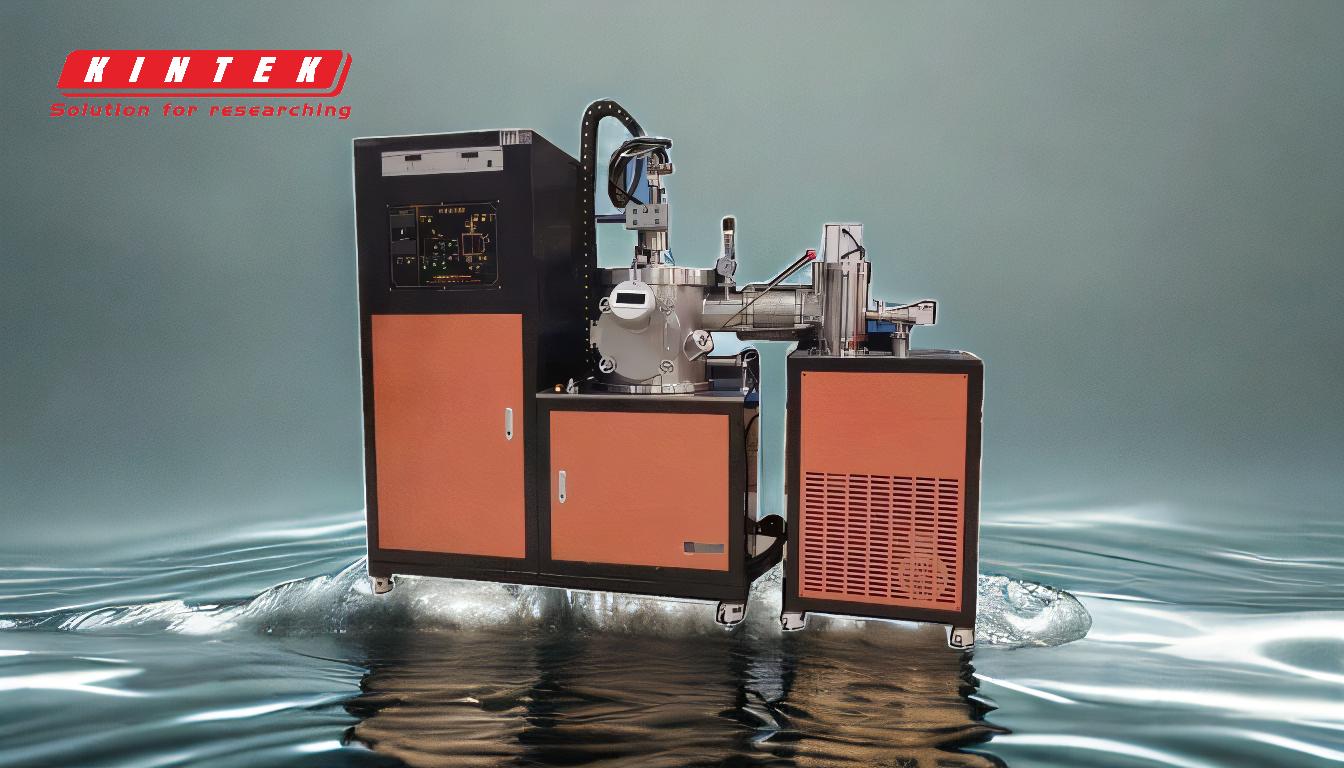
-
Coûts initiaux et opérationnels élevés:
- Investissement initial: Les systèmes à gaz inerte nécessitent des coûts initiaux importants pour l'équipement, l'installation et la mise en place. Cela comprend l'achat de générateurs de gaz, de réservoirs de stockage et de systèmes de distribution.
- Dépenses opérationnelles: Les coûts permanents d'entretien et d'exploitation de ces systèmes peuvent être importants. Ils comprennent le coût des gaz inertes (azote, argon, etc.), la consommation d'énergie pour la production de gaz et l'entretien régulier.
- Impact économique: Pour les petites entreprises ou les industries à budget serré, ces coûts peuvent être prohibitifs, ce qui rend l'investissement difficile à justifier.
-
Complexité de la maintenance:
- Exigences en matière d'entretien régulier: Les systèmes à gaz inerte nécessitent des inspections, des étalonnages et des entretiens fréquents pour garantir leur bon fonctionnement. Ces opérations peuvent prendre du temps et requièrent du personnel qualifié.
- Expertise technique: Une maintenance correcte nécessite souvent des connaissances et une formation spécialisées, qui ne sont pas toujours disponibles dans toutes les organisations.
- Temps d'arrêt: Les activités de maintenance peuvent entraîner des arrêts d'exploitation, ce qui affecte la productivité et peut entraîner des pertes financières.
-
Risques potentiels liés à une utilisation incorrecte:
- Risque d'asphyxie: Les gaz inertes peuvent déplacer l'oxygène de l'air, créant un risque d'asphyxie pour les travailleurs si le système n'est pas correctement géré ou si des fuites se produisent.
- Erreur humaine: Une utilisation incorrecte ou le non-respect des protocoles de sécurité peut entraîner des situations dangereuses, y compris la raréfaction de l'oxygène dans les espaces confinés.
- Fuites de gaz: Des fuites dans le système peuvent passer inaperçues, entraînant une accumulation progressive de gaz inerte et posant un risque sérieux pour la santé du personnel.
-
Limites dans certains environnements:
- Contraintes spatiales: Les systèmes à gaz inerte nécessitent un espace d'installation adéquat, qui peut ne pas être disponible dans toutes les installations, en particulier dans les usines plus anciennes ou plus petites.
- Questions de compatibilité: Certains matériaux ou procédés peuvent ne pas être compatibles avec les gaz inertes, ce qui limite leur applicabilité dans certaines industries.
- Conditions environnementales: Les températures extrêmes ou les conditions humides peuvent affecter les performances des systèmes à gaz inerte, nécessitant des mesures supplémentaires pour garantir la fiabilité.
-
Défis en matière de réglementation et de conformité:
- Des réglementations strictes: L'utilisation de systèmes de gaz inertes est souvent soumise à des exigences réglementaires strictes, qui peuvent varier selon les régions et les secteurs d'activité. Le respect de ces réglementations peut s'avérer complexe et coûteux.
- Documentation et rapports: Les organisations doivent tenir des registres détaillés des performances du système, de la maintenance et des contrôles de sécurité, ce qui alourdit la charge administrative.
- Inspection et audits: Les inspections et les audits réguliers effectués par les organismes de réglementation peuvent prendre beaucoup de temps et nécessiter des ressources supplémentaires pour résoudre les problèmes identifiés.
-
Impact sur la qualité des produits:
- Risques de contamination: Dans certains cas, l'introduction de gaz inertes peut entraîner une contamination des produits, en particulier dans des industries telles que l'industrie alimentaire ou pharmaceutique, où la pureté est essentielle.
- Interférence avec le processus: La présence de gaz inertes peut interférer avec certains processus de fabrication, affectant potentiellement la qualité ou le rendement du produit.
- Coût du contrôle de la qualité: Des mesures supplémentaires peuvent être nécessaires pour surveiller et contrôler l'impact des gaz inertes sur la qualité des produits, ce qui augmente les coûts opérationnels.
En conclusion, si les systèmes à gaz inerte offrent des avantages significatifs en matière de sécurité, ils présentent une série d'inconvénients qu'il convient d'examiner attentivement. Les coûts élevés, la complexité de la maintenance, les risques potentiels, les limitations environnementales, les défis réglementaires et les impacts sur la qualité des produits sont autant de facteurs que les acheteurs d'équipements et de consommables doivent prendre en compte lorsqu'ils décident de mettre en œuvre ces systèmes. Une planification, une formation et une gestion continue appropriées sont essentielles pour atténuer ces inconvénients et garantir une utilisation sûre et efficace des systèmes à gaz inerte.
Tableau récapitulatif :
Inconvénient | Détails clés |
---|---|
Coûts initiaux et opérationnels élevés | Coûts initiaux importants pour l'équipement, l'installation et la maintenance. |
Complexité de la maintenance | Nécessite des inspections fréquentes, du personnel qualifié et peut entraîner des arrêts d'exploitation. |
Dangers potentiels | Risque d'asphyxie, d'erreur humaine et de fuites de gaz en cas de mauvaise gestion. |
Limites dans certains environnements | Contraintes d'espace, problèmes de compatibilité et défis environnementaux. |
Défis en matière de réglementation et de conformité | Réglementation stricte, documentation et contrôles fréquents. |
Impact sur la qualité des produits | Risques de contamination, interférences dans les processus et coûts supplémentaires liés au contrôle de la qualité. |
Vous avez besoin d'aide pour décider si un système de gaz inerte est adapté à votre activité ? Contactez nos experts dès aujourd'hui pour des conseils personnalisés !