Le dépôt chimique en phase vapeur (CVD) est une technique largement utilisée pour déposer des films et des revêtements minces, mais elle présente plusieurs inconvénients importants. Ceux-ci incluent les défis liés à la synthèse de matériaux multi-composants en raison des variations de la pression de vapeur, de la nucléation et des taux de croissance, conduisant à des compositions de particules hétérogènes. Le processus nécessite souvent des températures élevées, ce qui peut provoquer une instabilité thermique des substrats et limiter les types de matériaux pouvant être utilisés. De plus, les précurseurs chimiques nécessaires aux maladies cardiovasculaires peuvent être très toxiques, volatils et dangereux, et les sous-produits sont souvent toxiques et corrosifs, ce qui rend la neutralisation coûteuse et problématique. Le processus est également limité par la taille de la chambre à vide, ce qui rend difficile le revêtement de surfaces plus grandes, et il ne peut pas être réalisé sur site, ce qui nécessite le transport des pièces vers un centre de revêtement. Ces facteurs font du CVD une méthode complexe et parfois peu pratique pour certaines applications.
Points clés expliqués :
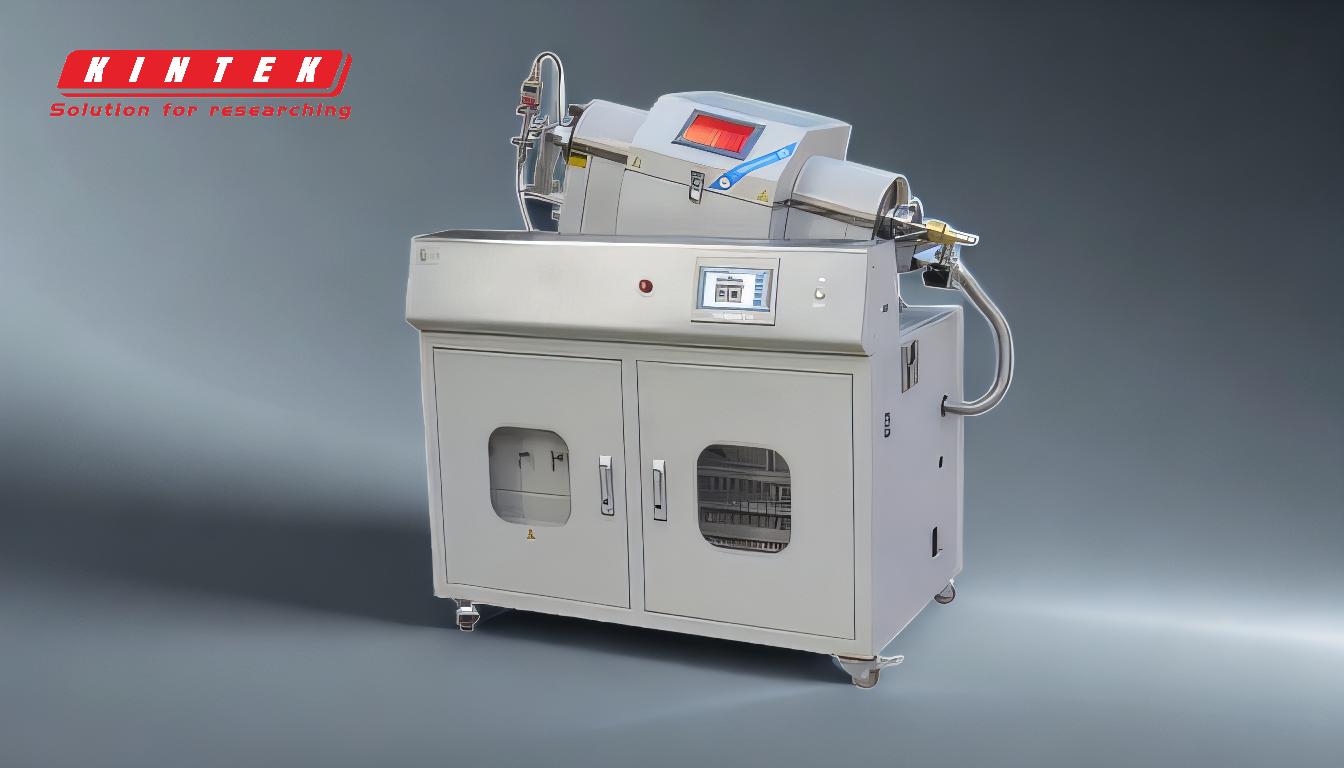
-
Difficulté à synthétiser des matériaux multi-composants:
- Le CVD est confronté à des défis dans la création de matériaux multi-composants en raison des variations de pression de vapeur, de nucléation et de taux de croissance au cours de la conversion gaz-particule. Ces variations aboutissent à une composition hétérogène de particules, ce qui rend difficile l’obtention de propriétés matérielles uniformes. Cela est particulièrement problématique lorsqu’on tente de créer des matériaux dotés de caractéristiques spécifiques et bien définies, car le processus peut conduire à des incohérences dans le produit final.
-
Températures de fonctionnement élevées:
- Le CVD fonctionne généralement à des températures élevées, ce qui peut provoquer une instabilité thermique dans de nombreux substrats. Cela limite les types de matériaux pouvant être utilisés, car certains substrats peuvent se dégrader ou être endommagés dans ces conditions. Les températures élevées augmentent également la consommation d’énergie et peuvent rendre le processus plus coûteux et moins respectueux de l’environnement.
-
Précurseurs toxiques et dangereux:
- Les précurseurs chimiques nécessaires aux maladies cardiovasculaires ont souvent des pressions de vapeur élevées et peuvent être très toxiques, volatils et dangereux. La manipulation de ces produits chimiques nécessite des mesures de sécurité strictes et leur utilisation peut présenter des risques importants pour la santé et l'environnement. De plus, le manque de précurseurs extrêmement volatils, non toxiques et non pyrophoriques complique encore davantage le processus, le rendant moins accessible pour certaines applications.
-
Sous-produits toxiques et corrosifs:
- Les sous-produits des maladies cardiovasculaires sont souvent toxiques et corrosifs et nécessitent une neutralisation et une élimination soigneuses. Cela ajoute au coût global et à la complexité du processus, car des équipements et des procédures spécialisés sont nécessaires pour manipuler ces sous-produits en toute sécurité. L'impact environnemental de ces sous-produits est également une préoccupation, en particulier dans les industries où la durabilité est une priorité.
-
Limites du revêtement de grandes surfaces:
- La taille de la chambre à vide utilisée en CVD limite la taille des surfaces pouvant être recouvertes. Cela rend difficile l’application de revêtements CVD sur des structures grandes ou complexes, limitant ainsi son utilisation dans certaines industries. De plus, le processus est souvent « tout ou rien », ce qui signifie qu'il est difficile de recouvrir partiellement un matériau ou d'obtenir une couverture complète dans certains cas.
-
Incapacité d'effectuer sur place:
- Le CVD ne peut généralement pas être réalisé sur site et nécessite le transport des pièces vers un centre de revêtement. Cela ajoute à la complexité logistique et au coût du processus, en particulier pour les composants volumineux ou lourds. La nécessité de décomposer les pièces en composants individuels pour le revêtement complique encore davantage le processus, le rendant moins efficace pour certaines applications.
-
Défis liés à la production de graphène de haute qualité:
- La production de graphène monocouche par CVD est un défi en raison de la multiplicité des conditions de croissance requises. La réalisation de films de graphène de haute qualité nécessite un contrôle précis du mécanisme de croissance et des conditions optimales, qui peuvent être difficiles à maintenir de manière cohérente. Cela limite l’évolutivité et la reproductibilité de la production de graphène par CVD.
-
Formation d'agrégats durs:
- L'agglomération en phase gazeuse lors du CVD peut conduire à la formation d'agrégats durs, rendant difficile la synthèse de matériaux en vrac de haute qualité. Ce problème est particulièrement problématique lorsqu’on tente de créer des matériaux dotés de propriétés mécaniques ou structurelles spécifiques, car la présence d’agrégats peut compromettre l’intégrité du produit final.
En résumé, alors que dépôt chimique en phase vapeur est une technique puissante pour déposer des films et des revêtements minces, mais elle présente plusieurs inconvénients importants qui peuvent limiter son applicabilité dans certains scénarios. Ceux-ci incluent les défis liés à la synthèse des matériaux, les températures de fonctionnement élevées, l'utilisation de précurseurs toxiques et les limites du revêtement de grandes surfaces. Comprendre ces inconvénients est crucial pour sélectionner la méthode de dépôt appropriée pour une application donnée.
Tableau récapitulatif :
Inconvénient | Description |
---|---|
Difficulté dans la synthèse multi-composants | Les variations de pression de vapeur et de taux de croissance conduisent à des propriétés matérielles incohérentes. |
Températures de fonctionnement élevées | Instabilité thermique des substrats et augmentation de la consommation d'énergie. |
Précurseurs toxiques et dangereux | Nécessite des mesures de sécurité strictes et présente des risques pour la santé et l’environnement. |
Sous-produits toxiques et corrosifs | Processus coûteux de neutralisation et d’élimination. |
Limites du revêtement de grandes surfaces | Limité par la taille de la chambre à vide et les défis liés au revêtement partiel. |
Incapacité d'effectuer sur place | Nécessite un transport vers les centres de revêtement, ce qui augmente la complexité logistique. |
Défis liés à la production de graphène de haute qualité | Difficulté à obtenir des conditions de croissance constantes pour le graphène monocouche. |
Formation d'agrégats durs | L'agglomération en phase gazeuse compromet l'intégrité du matériau. |
Besoin d’aide pour choisir la bonne méthode de dépôt ? Contactez nos experts dès aujourd'hui pour des conseils personnalisés !