Le dépôt chimique en phase vapeur (CVD) est une technique de dépôt de couches minces très répandue qui présente de nombreux avantages, tels qu'une grande pureté, l'uniformité, l'évolutivité et la polyvalence, ce qui la rend adaptée à des applications telles que les circuits électriques et les revêtements de surface complexes.Cependant, elle présente également des limites, notamment le coût élevé des équipements et des gaz précurseurs, les températures de fonctionnement élevées et les difficultés à revêtir des matériaux complexes ou de grande taille.Nous examinons ci-dessous en détail les avantages et les inconvénients du dépôt en phase vapeur (CVD).
Explication des principaux points :
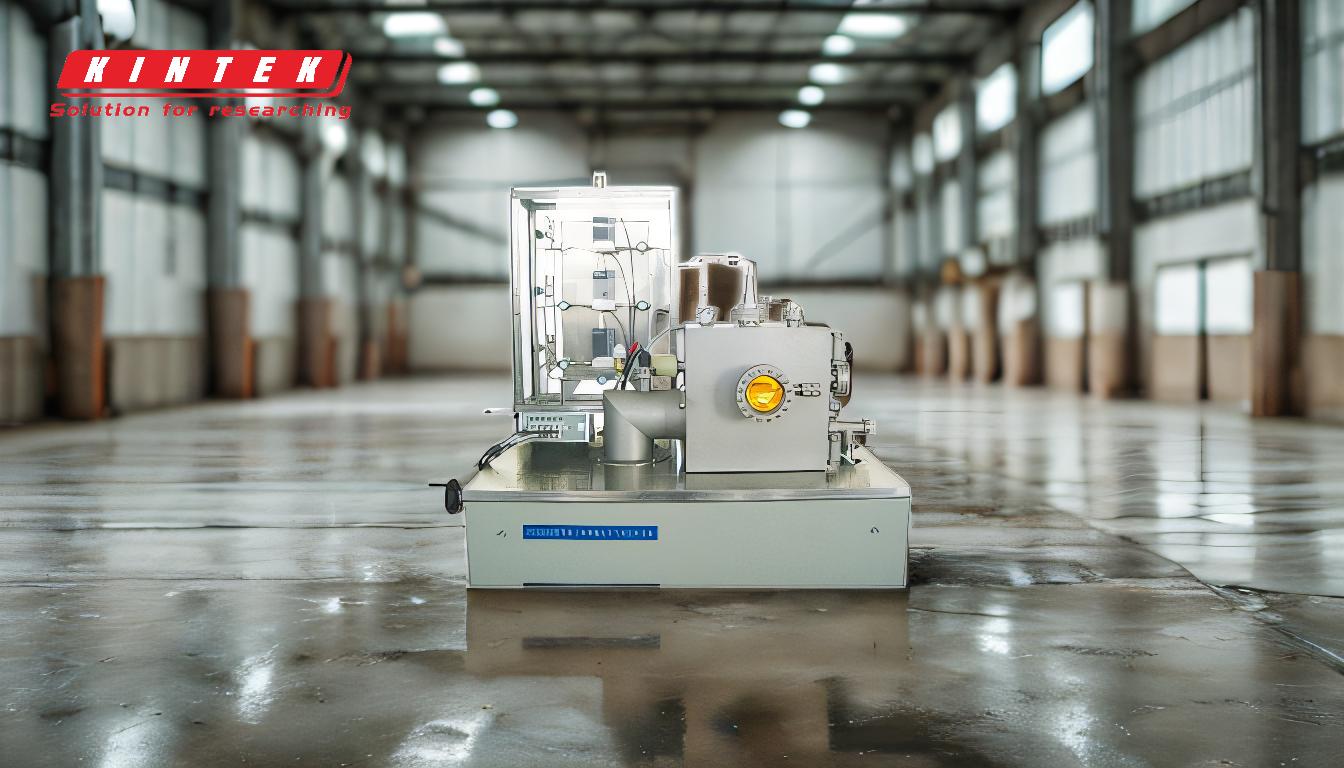
Avantages du dépôt chimique en phase vapeur (CVD) :
-
Pureté et densité élevées des films :
- Le dépôt en phase vapeur produit des films minces d'une pureté et d'une densité extrêmement élevées, ce qui est essentiel pour les applications exigeant des propriétés matérielles précises, telles que les semi-conducteurs et les revêtements optiques.
- Le procédé repose sur des réactions chimiques, ce qui garantit une contamination minimale et des résultats de haute qualité.
-
Uniformité et contrôle :
- Le dépôt en phase vapeur permet un contrôle précis de l'épaisseur, de la composition et de la microstructure des films déposés, ce qui permet d'obtenir des propriétés sur mesure pour des applications spécifiques.
- Les films sont uniformes à la fois à l'intérieur de la couche et sur la surface du substrat, ce qui en fait un procédé idéal pour les revêtements de grande surface.
-
Polyvalence des matériaux et des substrats :
- Le dépôt en phase vapeur peut déposer une large gamme de matériaux, notamment des métaux, des semi-conducteurs, des céramiques et des polymères.
- Elle est compatible avec divers substrats, tels que les métaux, le verre et les plastiques, ce qui la rend très adaptable à différents secteurs d'activité.
-
Évolutivité et taux de dépôt élevés :
- Le dépôt chimique en phase vapeur est modulable et convient aussi bien à la recherche à petite échelle qu'à la production industrielle à grande échelle.
- Elle offre des taux de dépôt élevés, ce qui la rend efficace pour produire rapidement des couches minces de grande surface.
-
Propriétés enveloppantes pour les surfaces complexes :
- Le dépôt en phase vapeur peut revêtir uniformément des surfaces irrégulières ou de forme complexe en raison de sa nature non linéaire, ce qui le rend idéal pour les composants de précision et les conceptions complexes.
-
Revêtements durables et performants :
- Les revêtements produits par dépôt en phase vapeur sont durables et peuvent résister à des environnements soumis à de fortes contraintes, à des températures extrêmes et à des variations de température.
- Les gaz utilisés dans le procédé CVD peuvent être optimisés pour obtenir des propriétés spécifiques, telles que la résistance à la corrosion ou à l'abrasion.
-
Un équipement simple et facile à utiliser :
- L'équipement CVD est relativement simple à utiliser et à entretenir, ce qui réduit la complexité opérationnelle et les temps d'arrêt.
Inconvénients du dépôt chimique en phase vapeur (CVD) :
-
Coût élevé de l'équipement et des gaz précurseurs :
- L'investissement initial dans l'équipement CVD est élevé et les gaz précurseurs utilisés dans le processus peuvent être coûteux, ce qui augmente les coûts globaux.
-
Températures de fonctionnement élevées :
- Le dépôt chimique en phase vapeur nécessite généralement des températures élevées, ce qui peut limiter son utilisation avec des matériaux et des substrats sensibles à la température.
- Les températures élevées peuvent également entraîner des contraintes résiduelles dans le revêtement et le substrat, ce qui nécessite un contrôle minutieux des paramètres de dépôt.
-
Application limitée sur site :
- Le dépôt en phase vapeur est généralement réalisé dans des centres de revêtement spécialisés plutôt que sur site, ce qui peut s'avérer peu pratique pour certaines applications.
- Toutes les pièces doivent être démontées en composants individuels pour le revêtement, ce qui ajoute à la complexité du processus.
-
Contraintes de taille dues aux chambres à vide :
- La taille de la chambre à vide limite la possibilité de revêtir des surfaces plus grandes, ce qui restreint son utilisation pour des applications à grande échelle.
-
Processus de revêtement "tout ou rien" :
- Le dépôt en phase vapeur est un procédé "tout ou rien", ce qui signifie qu'il est difficile de revêtir partiellement des matériaux ou d'obtenir une couverture sélective.
-
Dangers potentiels des gaz précurseurs :
- Certains gaz précurseurs utilisés dans le dépôt chimique en phase vapeur peuvent être dangereux et nécessitent des mesures de sécurité et des protocoles de manipulation stricts.
-
Difficultés à obtenir une couverture complète :
- Bien que le dépôt en phase vapeur puisse revêtir des surfaces complexes, l'obtention d'une couverture complète et uniforme peut s'avérer difficile, en particulier pour les géométries complexes.
Conclusion :
Le dépôt chimique en phase vapeur est une méthode très polyvalente et efficace pour le dépôt de couches minces, qui offre des avantages tels qu'une grande pureté, une grande uniformité et une grande évolutivité.Sa capacité à recouvrir des surfaces complexes et à produire des films durables et performants la rend indispensable dans des secteurs tels que l'électronique, l'optique et l'aérospatiale.Cependant, ses coûts élevés, ses températures de fonctionnement élevées et ses limites dans le revêtement de matériaux de grande taille ou sensibles à la température constituent des inconvénients notables.Il est essentiel de comprendre ces avantages et ces inconvénients pour choisir la technique de dépôt chimique en phase vapeur (CVD) comme technique de dépôt appropriée pour des applications spécifiques.
Tableau récapitulatif :
Aspect | Avantages | Inconvénients |
---|---|---|
Pureté et densité | Pureté et densité élevées des films, idéales pour les semi-conducteurs et les revêtements optiques. | Coûts élevés des équipements et des gaz précurseurs. |
Uniformité et contrôle | Contrôle précis de l'épaisseur, de la composition et de la microstructure. | Températures de fonctionnement élevées, limitant l'utilisation de matériaux sensibles à la température. |
Polyvalence | Dépose une large gamme de matériaux et est compatible avec divers substrats. | Application limitée sur site ; nécessite des centres de revêtement spécialisés. |
Évolutivité | Évolutif pour la recherche à petite échelle et la production à grande échelle. | Les contraintes de taille dues aux chambres à vide limitent les applications à grande échelle. |
Surfaces complexes | Recouvre uniformément les surfaces irrégulières ou de forme complexe. | Processus de revêtement tout ou rien ; difficile d'obtenir une couverture sélective. |
Durabilité | Produit des revêtements durables et très performants pour les environnements extrêmes. | Risques potentiels liés aux gaz précurseurs, nécessitant des mesures de sécurité strictes. |
Facilité d'utilisation | Équipement simple et facile à utiliser. | Difficultés à obtenir une couverture complète pour les géométries complexes. |
Vous êtes prêt à découvrir comment le dépôt en phase vapeur peut améliorer vos applications ? Contactez nous dès aujourd'hui pour obtenir des conseils d'experts !