CVD (Chemical Vapor Deposition) et PVD (Physical Vapor Deposition) sont deux technologies de revêtement largement utilisées, chacune avec des processus, des avantages et des applications distincts. Le CVD implique des réactions chimiques entre les précurseurs gazeux et le substrat à haute température, entraînant un dépôt multidirectionnel et la capacité de recouvrir des géométries complexes. Le PVD, quant à lui, repose sur la vaporisation physique de matériaux solides, en les déposant en visibilité directe à des températures plus basses. Le choix entre CVD et PVD dépend de facteurs tels que le matériau du substrat, les propriétés de revêtement souhaitées et les exigences de l'application.
Points clés expliqués :
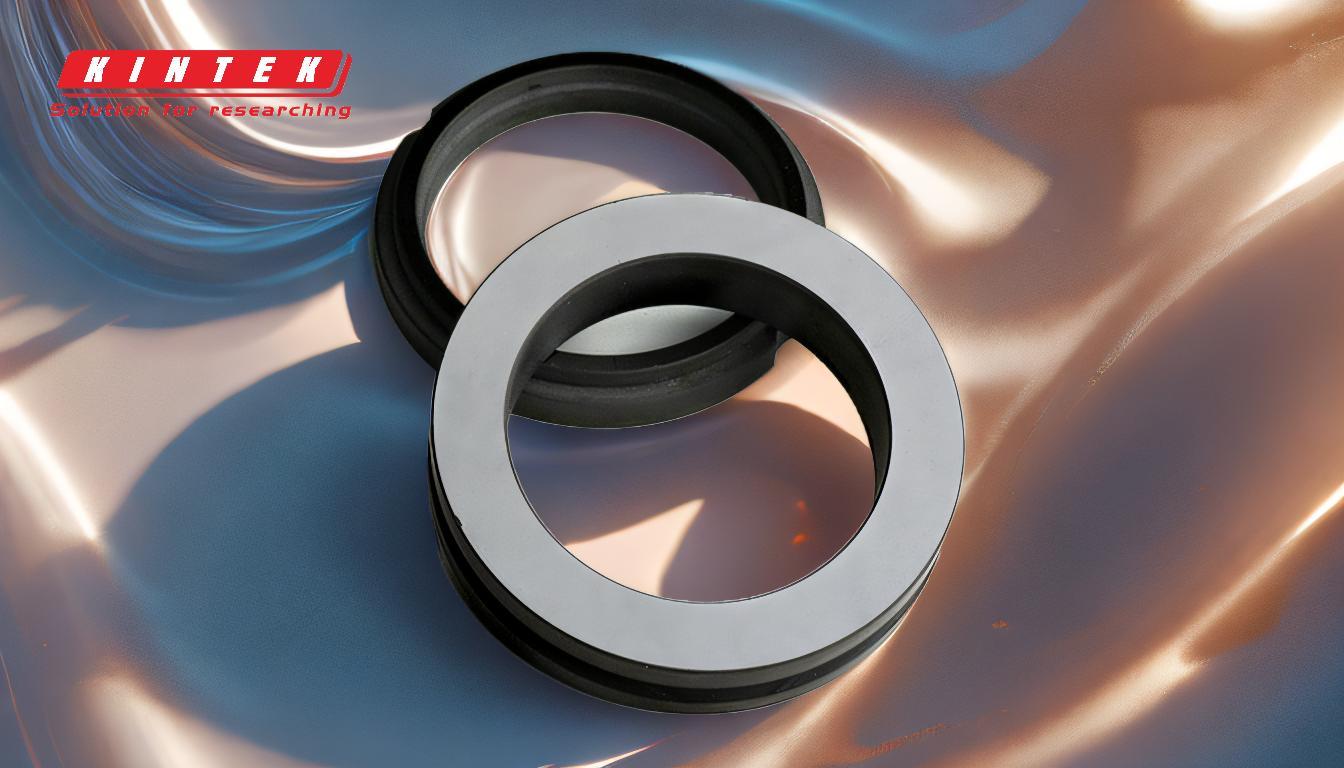
-
Mécanisme de dépôt:
- MCV: Implique des réactions chimiques entre les précurseurs gazeux et le substrat. Le processus est multidirectionnel, permettant un revêtement uniforme de formes complexes, de trous et de creux profonds.
- PVD: Repose sur la vaporisation physique de matériaux solides, qui sont ensuite déposés sur le substrat en visibilité directe. Cela limite sa capacité à recouvrir uniformément des géométries complexes.
-
Exigences de température:
- MCV: Fonctionne à des températures élevées, généralement entre 450°C et 1050°C. Cet environnement à haute température facilite les réactions chimiques mais peut également entraîner des contraintes thermiques et de fines fissures dans le revêtement.
- PVD: Fonctionne à des températures plus basses, généralement entre 250°C et 450°C. Cela le rend adapté aux substrats sensibles à la température et réduit le risque de dommages thermiques.
-
Matériau et épaisseur du revêtement:
- MCV: Utilise des précurseurs gazeux, qui réagissent pour former un revêtement solide. Le CVD peut produire des revêtements plus épais (10 ~ 20 μm) et est souvent utilisé pour des applications nécessitant une résistance élevée à l'usure.
- PVD: Utilise des matériaux solides qui sont vaporisés et déposés sur le substrat. Les revêtements PVD sont généralement plus fins (3 à 5 μm) mais offrent une excellente dureté et adhérence.
-
Propriétés du revêtement:
- MCV: Produit des revêtements avec un pouvoir de projection élevé, ce qui le rend idéal pour revêtir des formes complexes et des retraits profonds. Cependant, les températures élevées peuvent entraîner des contraintes de traction et de fines fissures.
- PVD: Forme une contrainte de compression lors du refroidissement, ce qui donne des revêtements d'une dureté élevée et d'une excellente adhérence. Les revêtements PVD sont également plus lisses et plus uniformes que les revêtements CVD.
-
Applications:
- MCV: Couramment utilisé dans les applications nécessitant des revêtements épais et résistants à l'usure, telles que les outils de coupe, les dispositifs semi-conducteurs et les composants résistants à l'usure.
- PVD: Préféré pour les applications nécessitant des revêtements fins et durs de haute précision, tels que les revêtements décoratifs, les revêtements optiques et les outils de précision.
-
Considérations économiques et opérationnelles:
- MCV: Souvent plus économique en raison des taux de dépôt élevés et de la capacité à produire des revêtements épais. Il ne nécessite pas d’ultra-vide, ce qui peut réduire les coûts opérationnels.
- PVD: Bien que les taux de dépôt soient généralement plus faibles, le PVD offre une efficacité d'utilisation élevée des matériaux et peut être réalisé à des températures plus basses, réduisant ainsi la consommation d'énergie.
En résumé, le choix entre CVD et PVD dépend des exigences spécifiques de l'application, notamment du matériau du substrat, des propriétés de revêtement souhaitées et des contraintes opérationnelles. Le CVD est idéal pour les géométries complexes et les revêtements épais, tandis que le PVD excelle dans la production de revêtements fins et durs avec une excellente adhérence et une excellente finition de surface.
Tableau récapitulatif :
Aspect | MCV | PVD |
---|---|---|
Mécanisme de dépôt | Réactions chimiques avec des précurseurs gazeux ; dépôt multidirectionnel | Vaporisation physique de matières solides ; dépôt en ligne de mire |
Température | Élevé (450 °C à 1 050 °C) | Faible (250 °C à 450 °C) |
Épaisseur du revêtement | Plus épais (10 ~ 20 μm) | Plus fin (3~5μm) |
Propriétés du revêtement | Pouvoir de projection élevé, uniforme sur les formes complexes ; contrainte de traction | Haute dureté, excellente adhérence ; plus lisse et plus uniforme |
Applications | Outils de coupe, semi-conducteurs, composants résistants à l'usure | Revêtements décoratifs, revêtements optiques, outils de précision |
Considérations économiques | Taux de dépôt élevés, économiques pour les revêtements épais | Taux de dépôt inférieurs, efficacité matérielle élevée, efficacité énergétique |
Besoin d'aide pour choisir la bonne solution de revêtement ? Contactez nos experts dès aujourd'hui pour des conseils sur mesure !