La principale différence entre l'évaporation par faisceau d'électrons et l'évaporation thermique réside dans la méthode utilisée pour vaporiser le matériau.L'évaporation par faisceau d'électrons utilise un faisceau d'électrons à haute énergie pour chauffer et vaporiser directement le matériau cible, ce qui la rend adaptée aux matériaux à point de fusion élevé tels que les oxydes.En revanche, l'évaporation thermique utilise une résistance électrique pour chauffer un creuset, qui fait ensuite fondre et s'évaporer le matériau source, ce qui la rend idéale pour les matériaux dont la température de fusion est plus basse.L'évaporation par faisceau d'électrons offre des avantages tels que des revêtements en couches minces plus denses, des taux de dépôt plus élevés et des risques d'impuretés plus faibles par rapport à l'évaporation thermique.
Explication des points clés :
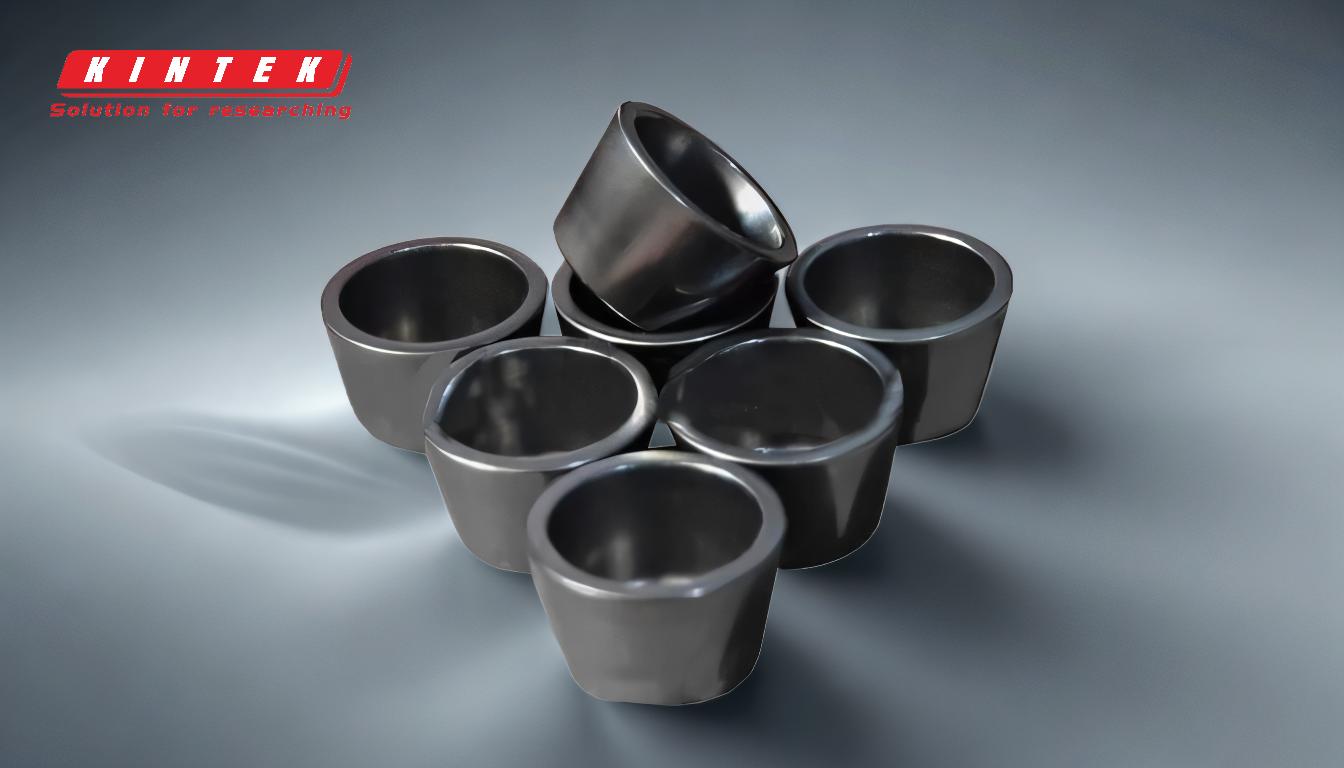
-
Méthode de vaporisation:
- Evaporation par faisceau d'électrons:Utilise un faisceau d'électrons à haute énergie pour chauffer et vaporiser directement le matériau cible.Cette méthode transfère de l'énergie cinétique au matériau, ce qui provoque son évaporation.
- Évaporation thermique:La résistance électrique sert à chauffer un creuset qui fait fondre et s'évaporer le matériau d'origine.La chaleur est appliquée indirectement à travers le creuset.
-
Compatibilité des matériaux:
- Evaporation par faisceau d'électrons:Convient aux matériaux à point de fusion élevé, tels que les oxydes, qui ne se subliment pas facilement lors de l'évaporation thermique.
- Évaporation thermique:Convient mieux aux matériaux à faible température de fusion, car il ne peut pas vaporiser efficacement les matériaux à point de fusion élevé.
-
Qualité du revêtement:
- Evaporation par faisceau d'électrons:Produit des couches minces plus denses grâce au processus à haute énergie, ce qui permet d'obtenir une meilleure adhérence et une plus grande uniformité.
- Évaporation thermique:Tend à produire des revêtements moins denses, qui peuvent nécessiter des étapes supplémentaires pour obtenir une qualité comparable.
-
Taux de dépôt:
- Evaporation par faisceau d'électrons:Offre une vitesse de dépôt plus élevée, ce qui la rend plus efficace pour les applications à grande échelle ou à haut débit.
- Évaporation thermique:La vitesse de dépôt est plus lente, ce qui peut limiter son utilisation dans les processus sensibles au temps.
-
Risques d'impureté:
- Evaporation par faisceau d'électrons:Le risque d'impuretés est moindre car le faisceau d'électrons cible directement le matériau, ce qui minimise la contamination par le creuset.
- Évaporation thermique:Risque plus élevé d'impuretés en raison des réactions potentielles entre le matériau et le creuset pendant le chauffage.
-
Aptitude à l'application:
- Evaporation par faisceau d'électrons:Idéal pour les applications avancées nécessitant des matériaux de haute pureté et à point de fusion élevé, telles que la fabrication de semi-conducteurs ou les revêtements optiques.
- Évaporation thermique:Plus adapté aux applications plus simples impliquant des matériaux à faible point de fusion, comme le dépôt de couches minces de base ou les revêtements décoratifs.
En comprenant ces différences essentielles, les acheteurs d'équipements et de consommables peuvent prendre des décisions éclairées en fonction des exigences spécifiques de leurs applications, telles que le type de matériau, la qualité de revêtement souhaitée et l'efficacité de la production.
Tableau récapitulatif :
Aspect | Évaporation par faisceau d'électrons | Évaporation thermique |
---|---|---|
Méthode de vaporisation | Un faisceau d'électrons à haute énergie chauffe et vaporise directement le matériau. | La résistance électrique chauffe un creuset qui fait fondre et évapore le matériau. |
Compatibilité des matériaux | Convient aux matériaux à point de fusion élevé comme les oxydes. | Meilleur pour les matériaux dont la température de fusion est plus basse. |
Qualité du revêtement | Produit des revêtements plus denses et plus uniformes avec une meilleure adhérence. | Revêtements moins denses ; peuvent nécessiter des étapes supplémentaires pour la qualité. |
Vitesse de dépôt | Vitesse de dépôt plus élevée, idéale pour les applications à grande échelle ou à haut débit. | Vitesse de dépôt plus lente, moins efficace pour les processus sensibles au temps. |
Risques d'impuretés | Risque d'impuretés plus faible en raison du ciblage direct des matériaux. | Risque plus élevé d'impuretés dues aux réactions en creuset. |
Aptitude à l'application | Applications avancées telles que les semi-conducteurs et les revêtements optiques. | Applications plus simples comme le dépôt de couches minces de base ou les revêtements décoratifs. |
Vous avez besoin d'aide pour choisir la méthode d'évaporation adaptée à votre application ? Contactez nos experts dès aujourd'hui !