La galvanoplastie et le dépôt physique en phase vapeur (PVD) sont deux techniques distinctes de revêtement de surface utilisées pour améliorer les propriétés des matériaux, telles que la résistance à la corrosion, la dureté et l'attrait esthétique.La galvanoplastie implique le dépôt électrochimique d'une couche métallique sur un substrat à l'aide d'une solution électrolytique, tandis que le dépôt physique en phase vapeur utilise des procédés physiques tels que l'évaporation ou la pulvérisation pour déposer des couches minces dans un environnement sous vide.Le dépôt en phase vapeur présente des avantages tels qu'une plus grande résistance à la corrosion, une meilleure adhérence et une sécurité environnementale, car il ne fait pas appel à des produits chimiques toxiques.La galvanoplastie, en revanche, est souvent plus rentable et convient à des revêtements plus épais, mais elle peut faire appel à des produits chimiques dangereux et produire des finitions moins durables.
Explication des principaux points :
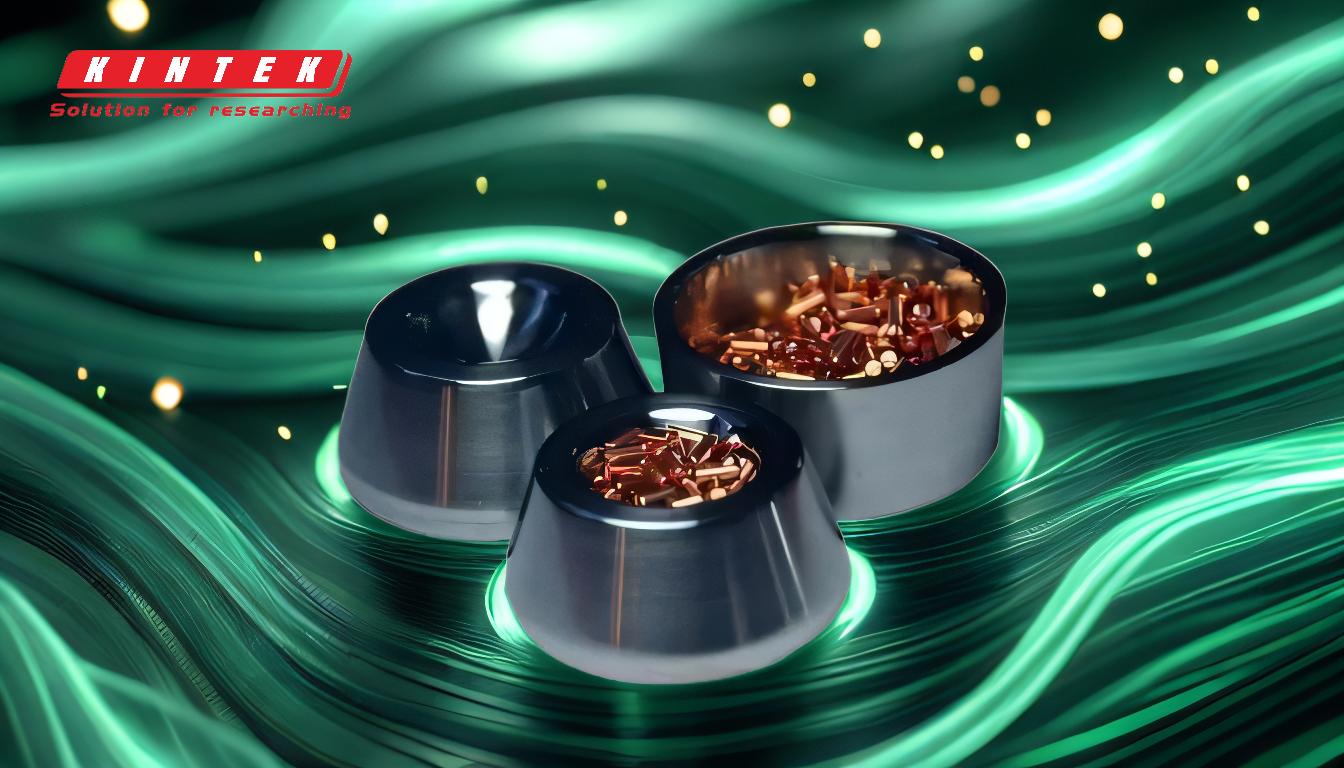
-
Mécanisme du processus:
- Galvanisation:Il s'agit d'un processus électrochimique dans lequel une solution d'ions métalliques (électrolyte) est utilisée pour déposer une couche métallique sur un substrat.Un courant électrique réduit les ions métalliques dans l'électrolyte, ce qui les lie au substrat.
- PVD:Le dépôt en phase vapeur est un procédé physique qui consiste à vaporiser un matériau solide (cible) dans une chambre à vide.Les atomes ou molécules vaporisés se condensent ensuite sur le substrat pour former un revêtement mince et uniforme.Des techniques telles que la pulvérisation cathodique et l'évaporation sont couramment utilisées.
-
Épaisseur et uniformité du revêtement:
- Galvanisation:produit généralement des revêtements plus épais, qui peuvent aller de quelques micromètres à plusieurs millimètres.Toutefois, il peut être difficile d'obtenir une épaisseur uniforme, en particulier sur des géométries complexes.
- LE DÉPÔT EN PHASE VAPEUR (PVD):Il permet de créer des revêtements beaucoup plus fins, souvent de l'ordre du nanomètre ou du micromètre.Les revêtements PVD sont très uniformes et peuvent épouser des formes complexes grâce au processus de dépôt en ligne droite.
-
Adhésion et durabilité:
- Galvanisation:L'adhérence des revêtements électrodéposés dépend de la préparation de la surface et des conditions électrochimiques.Bien que durables, ces revêtements peuvent avoir tendance à s'écailler ou à se décoller sous l'effet d'une contrainte.
- PVD:Ils offrent une adhérence supérieure grâce à la liaison au niveau atomique entre le revêtement et le substrat.Les revêtements PVD sont très durables et résistants à l'usure, à la corrosion et à l'oxydation.
-
Considérations relatives à l'environnement et à la sécurité:
- Galvanisation:Il implique souvent l'utilisation de produits chimiques dangereux, tels que les cyanures et les acides, qui doivent être manipulés et éliminés avec précaution.Le processus peut générer des déchets toxiques et présenter des risques pour l'environnement.
- PVD:Généralement considérée comme plus sûre et plus respectueuse de l'environnement, car elle ne fait pas appel à des produits chimiques toxiques.Le processus se déroule sous vide, ce qui minimise l'exposition aux substances dangereuses.
-
Les applications:
- Galvanisation:Il est couramment utilisé dans les industries nécessitant des revêtements épais, décoratifs ou fonctionnels, telles que l'automobile (chromage), l'électronique (dorure) et la bijouterie.
- PVD:Préférence pour les applications nécessitant des revêtements de haute performance, telles que les outils de coupe, les appareils médicaux et les composants aérospatiaux, où la durabilité, la résistance à la corrosion et la précision sont essentielles.
-
Coût et évolutivité:
- Galvanisation:Généralement plus rentable pour la production à grande échelle et les revêtements plus épais.Il est largement utilisé dans la production de masse en raison de son coût relativement faible et de son rendement élevé.
- PVD:Plus coûteux en raison de la nécessité d'un équipement sous vide et de procédés spécialisés.Cependant, il est très évolutif pour les applications de précision et offre des avantages financiers à long terme en raison de la durabilité des revêtements.
-
Compatibilité des matériaux:
- Galvanisation:Limité aux métaux qui peuvent être déposés par voie électrochimique.Les substrats non conducteurs nécessitent un prétraitement conducteur.
- PVD:Peut déposer une large gamme de matériaux, y compris les métaux, les céramiques et les composites, sur des substrats conducteurs et non conducteurs.
-
Finition de surface et esthétique:
- Galvanisation:Il offre une finition brillante et réfléchissante, idéale pour les applications décoratives.Cependant, la finition peut se dégrader avec le temps en raison de l'exposition à l'environnement.
- PVD:Offre une finition mate ou satinée, qui peut être adaptée à des exigences esthétiques spécifiques.Les revêtements PVD sont plus résistants à la décoloration et au ternissement.
En comprenant ces différences essentielles, les acheteurs peuvent prendre des décisions éclairées en fonction des exigences spécifiques de leur application, telles que la durabilité, l'impact sur l'environnement et les considérations de coût.
Tableau récapitulatif :
Aspect | Placage électrolytique | PVD |
---|---|---|
Mécanisme du procédé | Dépôt électrochimique à l'aide d'une solution électrolytique. | Vaporisation physique dans un environnement sous vide. |
Épaisseur du revêtement | Revêtements plus épais (micromètres à millimètres). | Revêtements plus minces (nanomètres à micromètres). |
Adhésion et durabilité | Durable mais peut se décoller ou s'écailler sous la contrainte. | Adhésion supérieure, très durable et résistant à l'usure et à la corrosion. |
Impact sur l'environnement | Utilise des produits chimiques dangereux ; génère des déchets toxiques. | Respectueux de l'environnement ; aucun produit chimique toxique n'est utilisé. |
Applications | Automobile, électronique, bijouterie (revêtements épais et décoratifs). | Outils de coupe, appareils médicaux, aérospatiale (revêtements haute performance). |
Coût | Rentable pour la production à grande échelle. | Coût initial plus élevé mais avantages en termes de durabilité à long terme. |
Compatibilité des matériaux | Limitée aux métaux ; les substrats non conducteurs nécessitent un prétraitement. | Compatible avec les métaux, les céramiques et les composites. |
Finition de la surface | Finition brillante et réfléchissante ; peut se dégrader avec le temps. | Finition mate ou satinée, résistante à la décoloration et au ternissement. |
Vous ne savez toujours pas quelle technique de revêtement convient à votre projet ? Contactez nos experts dès aujourd'hui pour des conseils personnalisés !