Le dépôt chimique en phase vapeur (CVD) est une technique largement utilisée pour déposer des films minces sur des substrats. Elle peut être classée en CVD à paroi chaude et CVD à paroi froide en fonction de la façon dont le substrat et les parois du réacteur sont chauffés. Le CVD à parois chaudes consiste à chauffer à la fois le substrat et les parois du réacteur à des températures similaires, ce qui simplifie le processus et est rentable, mais peut conduire à des dépôts indésirables sur les parois du réacteur. Le CVD à paroi froide, en revanche, ne chauffe que le substrat, minimisant ainsi les dépôts sur les parois du réacteur mais introduisant des problèmes tels que les gradients de température et les problèmes de débit de gaz. Comprendre les différences entre ces méthodes est crucial pour sélectionner la bonne approche pour des applications spécifiques.
Points clés expliqués :
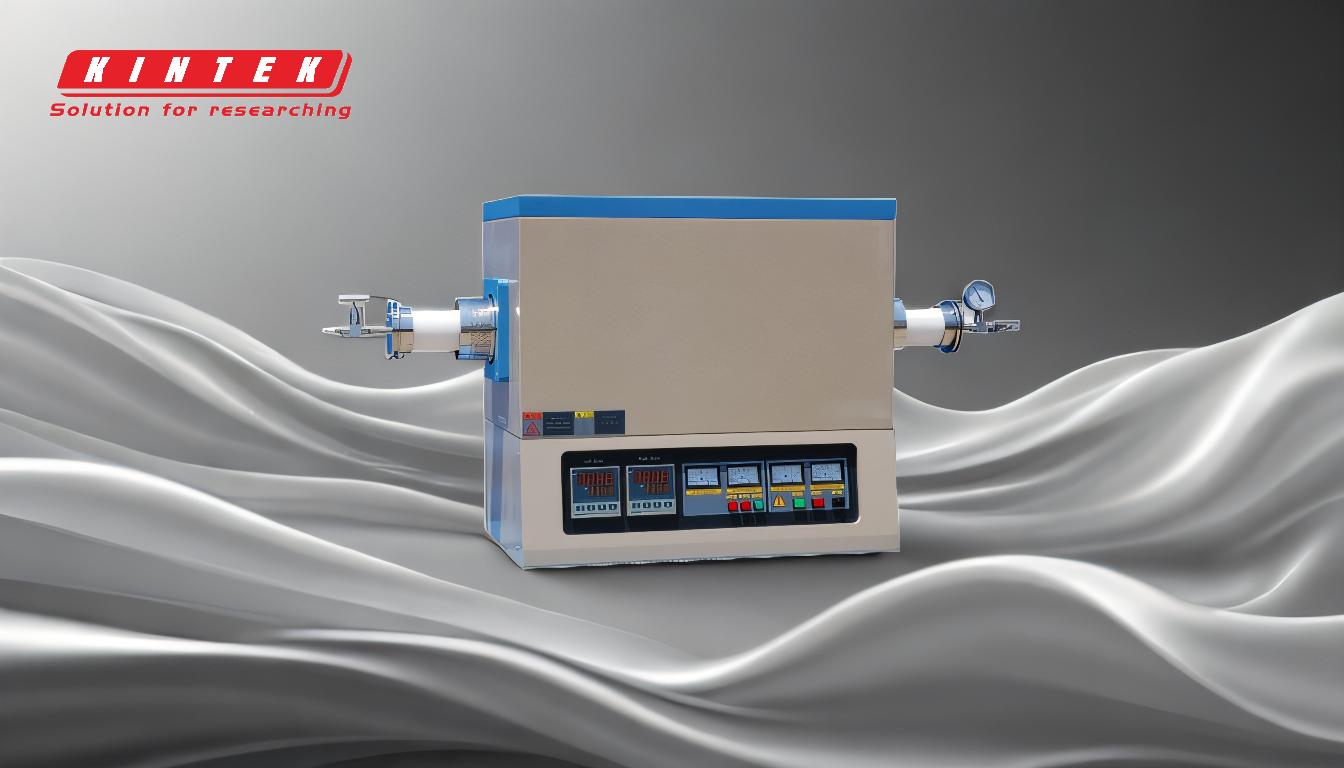
-
Mécanisme de chauffage:
- CVD à paroi chaude: Le substrat et les parois du réacteur sont chauffés à des températures comparables. Ceci garantit un chauffage uniforme mais peut conduire à un dépôt sur les parois du réacteur, susceptible de provoquer une contamination ou une non-uniformité du film déposé.
- CVD à paroi froide: Seul le substrat est chauffé, généralement à l'aide d'un suscepteur en graphite, tandis que les parois du réacteur restent plus froides. Cela minimise les dépôts sur les parois mais peut créer d'importants gradients de température à proximité du substrat, affectant le flux de gaz et l'uniformité du dépôt.
-
Uniformité du dépôt:
- CVD à paroi chaude: Le chauffage uniforme du substrat et des parois du réacteur peut conduire à un dépôt plus cohérent sur le substrat. Cependant, le dépôt sur les parois du réacteur peut entraîner la chute de poudres ou de paillettes sur le substrat, potentiellement à l'origine de défauts.
- CVD à paroi froide: En chauffant uniquement le substrat, les réacteurs à parois froides réduisent les risques de dépôt sur les parois du réacteur. Cependant, les gradients de température à proximité du substrat peuvent conduire à un dépôt non uniforme, notamment dans les applications à grande échelle.
-
Complexité et coût du processus:
- CVD à paroi chaude: Cette méthode est généralement plus simple à mettre en œuvre et plus rentable, ce qui la rend adaptée au traitement par lots. La technologie mature et les coûts d'équipement réduits sont des avantages significatifs.
- CVD à paroi froide: Bien que plus complexe en raison de la nécessité d'un contrôle précis du chauffage et du refroidissement du substrat, le CVD sur paroi froide offre une plus grande flexibilité dans le contrôle des conditions de dépôt, ce qui peut être crucial pour certaines applications de haute précision.
-
Applications:
- CVD à paroi chaude: Couramment utilisé dans les applications où le coût et la simplicité sont plus critiques que l'obtention des plus hauts niveaux d'uniformité de dépôt. Il est bien adapté au traitement par lots et aux applications où une contamination mineure due au dépôt des parois du réacteur est acceptable.
- CVD à paroi froide: Préféré pour les applications nécessitant une haute précision et une contamination minimale, comme dans l'industrie des semi-conducteurs. La capacité de contrôler les vitesses de refroidissement et de minimiser les dépôts sur les parois du réacteur le rend idéal pour les matériaux hautes performances.
-
Comparaison avec d'autres techniques:
- CVD contre PVD: Alors que le CVD repose sur des réactions chimiques pour déposer des matériaux, le dépôt physique en phase vapeur (PVD) implique la vaporisation physique des matériaux. Le CVD est généralement utilisé pour les céramiques et les polymères, tandis que le PVD peut déposer une gamme plus large de matériaux, notamment les métaux et les alliages. Les revêtements CVD sont plus denses et plus uniformes mais prennent plus de temps à appliquer que les revêtements PVD.
- Distillation sous vide à court trajet: Cette technique, souvent utilisée en distillation moléculaire, consiste à réduire la pression pour garantir que le libre parcours moyen des molécules soit plus long que la distance entre l'évaporateur et le condenseur, éliminant ainsi la contre-pression. Ceci est différent du CVD mais partage l’objectif d’un dépôt ou d’une séparation précise des matériaux. Pour plus de détails, voir distillation sous vide à court trajet .
En résumé, le choix entre le CVD à paroi chaude et le CVD à paroi froide dépend des exigences spécifiques de l'application, notamment du besoin d'uniformité du dépôt, de contrôle de la contamination et de complexité du processus. Le CVD à paroi chaude offre simplicité et rentabilité, tandis que le CVD à paroi froide offre une plus grande précision et un meilleur contrôle, ce qui le rend adapté aux applications hautes performances.
Tableau récapitulatif :
Aspect | CVD à paroi chaude | CVD à paroi froide |
---|---|---|
Mécanisme de chauffage | Chauffe uniformément le substrat et les parois du réacteur | Chauffe uniquement le substrat, gardant les parois du réacteur plus froides |
Uniformité du dépôt | Dépôt uniforme mais risque de contamination par le dépôt sur les parois du réacteur | Minimise les dépôts sur les parois du réacteur mais peut être confronté à des problèmes de gradient de température |
Complexité du processus | Plus simple et économique, idéal pour le traitement par lots | Plus complexe, nécessite un contrôle précis du chauffage et du refroidissement |
Applications | Convient aux applications sensibles aux coûts et présentant des risques de contamination mineurs | Préféré pour les applications de haute précision telles que la fabrication de semi-conducteurs |
Besoin d'aide pour choisir la bonne méthode CVD pour votre application ? Contactez nos experts dès aujourd'hui pour un accompagnement personnalisé !